- お役立ち記事
- Casting Technology and Its Applications in Manufacturing
Casting Technology and Its Applications in Manufacturing
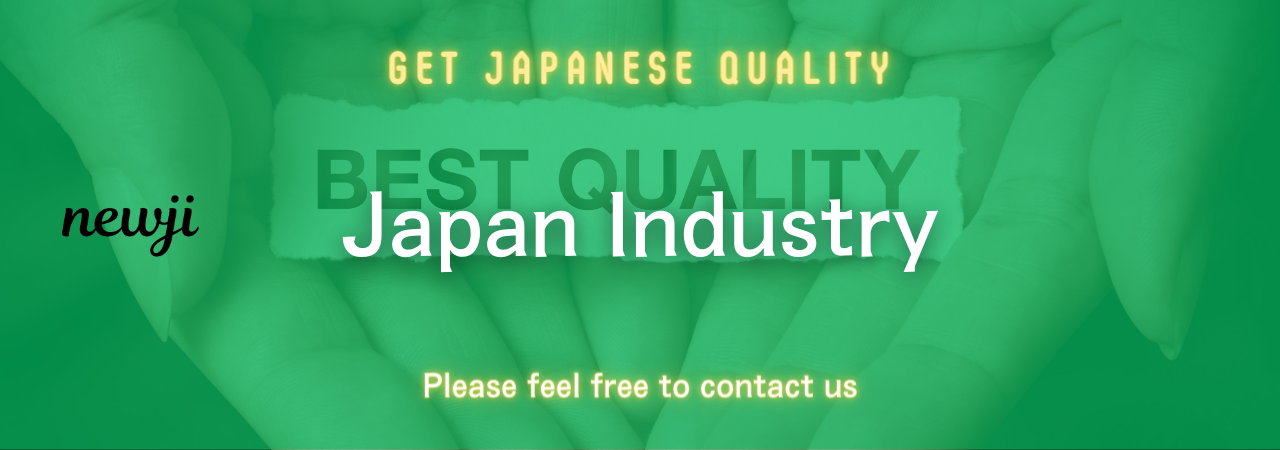
Casting technology has a long and fascinating history and is an essential part of modern manufacturing processes.
At its core, casting involves pouring liquid material, often metal or plastic, into a mold that contains a hollow cavity with the desired shape.
The material then solidifies, taking the shape of the mold.
Once cooled and hardened, the object is removed, creating a cast part.
Different types of casting methods include sand casting, die casting, and investment casting, among others.
Each has unique benefits and is suited to particular applications.
This article will delve into the specifics of casting technology and its various applications in the manufacturing industry.
目次
Types of Casting Methods
Sand Casting
One of the oldest and most widely used casting methods is sand casting.
This process uses a mold made from a mixture of sand and a binding agent like clay.
A pattern that resembles the final product is placed in the sand to create a cavity.
Molten metal is then poured into the cavity to form the desired shape.
Sand casting is relatively cost-effective, making it suitable for producing large parts or small production runs.
It is primarily used for manufacturing heavy machinery, automotive parts, and complex shapes.
Die Casting
Die casting involves forcing molten metal under high pressure into a mold cavity.
Usually made from steel, these molds are called dies.
This process is quick, efficient, and ideal for producing high volumes of small to medium-sized parts with excellent surface finish and dimensional accuracy.
Industries like consumer electronics, automotive, and aerospace often use die casting for components that require a strong, durable, and lightweight material.
Common products made through die casting include engine blocks, cylinder heads, and gearbox housings.
Investment Casting
Investment casting, also known as lost-wax casting, is a more intricate process used for producing detailed and complex shapes.
A wax pattern is created and coated with a ceramic material to form a mold.
Once hardened, the wax is melted away, leaving a shell mold.
Molten metal is then poured into the shell to create the final product.
This method allows for high precision and is often used to manufacture intricate components for industries such as aerospace, medical, and jewelry.
Examples include turbine blades, medical implants, and intricate jewelry designs.
Advantages of Casting Technology
Complex Shapes
One of the most significant advantages of casting technology is its ability to create complex shapes that are difficult or impossible to achieve through other manufacturing methods.
The mold can be designed to include elaborate geometries and features, reducing the need for assembly and secondary processing.
Material Versatility
Casting is versatile in terms of the materials that can be used.
It is possible to cast metals, plastics, ceramics, and even certain composites.
This flexibility allows manufacturers to choose the best material for the specific requirements of the product, whether it is strength, durability, heat resistance, or lightweight properties.
Cost-Effectiveness
For medium to large production runs, casting technology proves to be cost-effective.
The initial investment in creating molds and patterns can be high, but the per-unit cost decreases significantly with larger quantities.
Additionally, casting processes often require minimal secondary machining, further reducing production costs.
Applications in Various Industries
Automotive Industry
The automotive industry heavily relies on casting technology to produce various components.
Engine blocks, cylinder heads, and transmission cases are prime examples.
Casting allows for high precision and durability, ensuring the reliability and performance of automotive parts.
Aluminum and iron are common materials used in automotive casting due to their strength and lightweight properties.
Aerospace Industry
In the aerospace industry, casting technology is indispensable for creating complex and high-performance components.
The precision and reliability of investment casting make it ideal for producing turbine blades, engine components, and aerospace structures.
Materials like titanium and nickel alloys are commonly used due to their strength-to-weight ratios and excellent temperature resistance.
Medical Field
The medical field benefits greatly from casting technology, particularly for producing surgical instruments and implants.
Investment casting ensures the intricate designs required for medical devices are met with high precision.
Biocompatible materials like titanium and surgical-grade stainless steel are often used to create durable and safe medical components.
Future Trends in Casting Technology
3D Printing and Rapid Prototyping
3D printing is making significant inroads in casting technology.
By creating a 3D-printed pattern, manufacturers can produce molds more quickly and accurately.
This innovation in rapid prototyping allows for faster development cycles and lower costs, making it easier to bring new products to market.
Automation and AI
Automation and artificial intelligence are gradually transforming casting processes.
Automated systems can manage the entire casting process, from mold creation to material pouring and finishing.
AI algorithms can optimize material usage, predict defects, and adjust parameters in real time, leading to higher quality and efficiency.
Sustainability and Eco-Friendly Practices
As sustainability becomes a focal point, the casting industry is adopting eco-friendly practices.
Recycling materials, improving energy efficiency, and reducing waste are major trends shaping the future of casting technology.
Advancements in materials science are also leading to more sustainable and recyclable casting materials.
Summing up, casting technology has been a cornerstone of manufacturing for centuries, providing a versatile and efficient method for producing complex parts and components.
With continuous advancements and innovations, casting technology remains a vital part of modern industry, promising even greater precision, efficiency, and sustainability in the future.
資料ダウンロード
QCD調達購買管理クラウド「newji」は、調達購買部門で必要なQCD管理全てを備えた、現場特化型兼クラウド型の今世紀最高の購買管理システムとなります。
ユーザー登録
調達購買業務の効率化だけでなく、システムを導入することで、コスト削減や製品・資材のステータス可視化のほか、属人化していた購買情報の共有化による内部不正防止や統制にも役立ちます。
NEWJI DX
製造業に特化したデジタルトランスフォーメーション(DX)の実現を目指す請負開発型のコンサルティングサービスです。AI、iPaaS、および先端の技術を駆使して、製造プロセスの効率化、業務効率化、チームワーク強化、コスト削減、品質向上を実現します。このサービスは、製造業の課題を深く理解し、それに対する最適なデジタルソリューションを提供することで、企業が持続的な成長とイノベーションを達成できるようサポートします。
オンライン講座
製造業、主に購買・調達部門にお勤めの方々に向けた情報を配信しております。
新任の方やベテランの方、管理職を対象とした幅広いコンテンツをご用意しております。
お問い合わせ
コストダウンが利益に直結する術だと理解していても、なかなか前に進めることができない状況。そんな時は、newjiのコストダウン自動化機能で大きく利益貢献しよう!
(Β版非公開)