- お役立ち記事
- Catalog Comparison and Selection Points for Standard Equipment
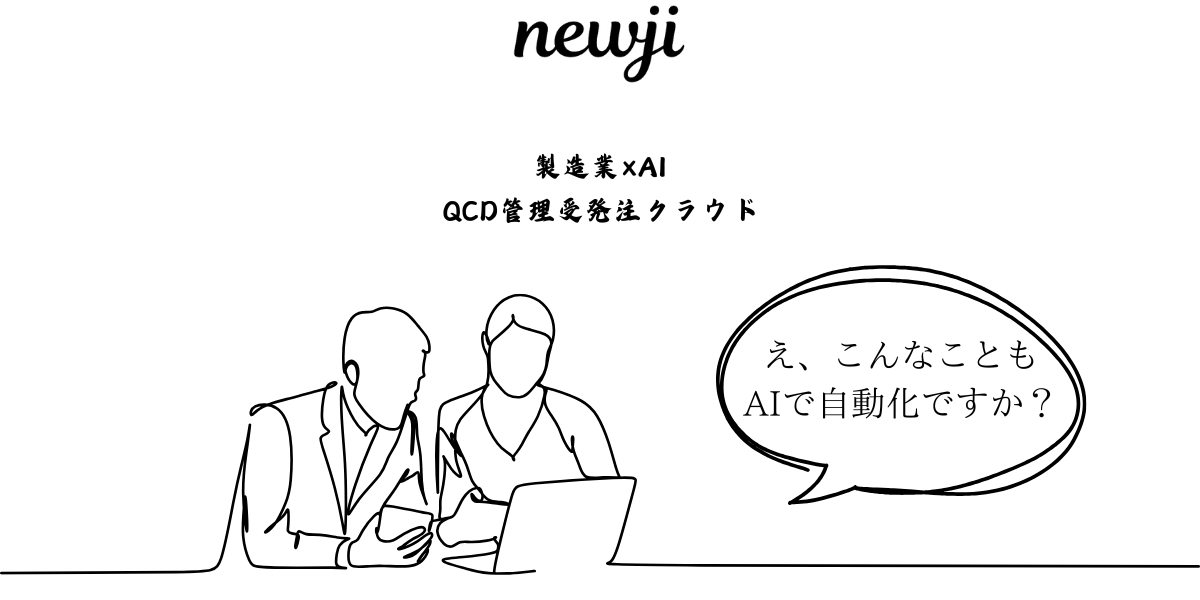
Catalog Comparison and Selection Points for Standard Equipment
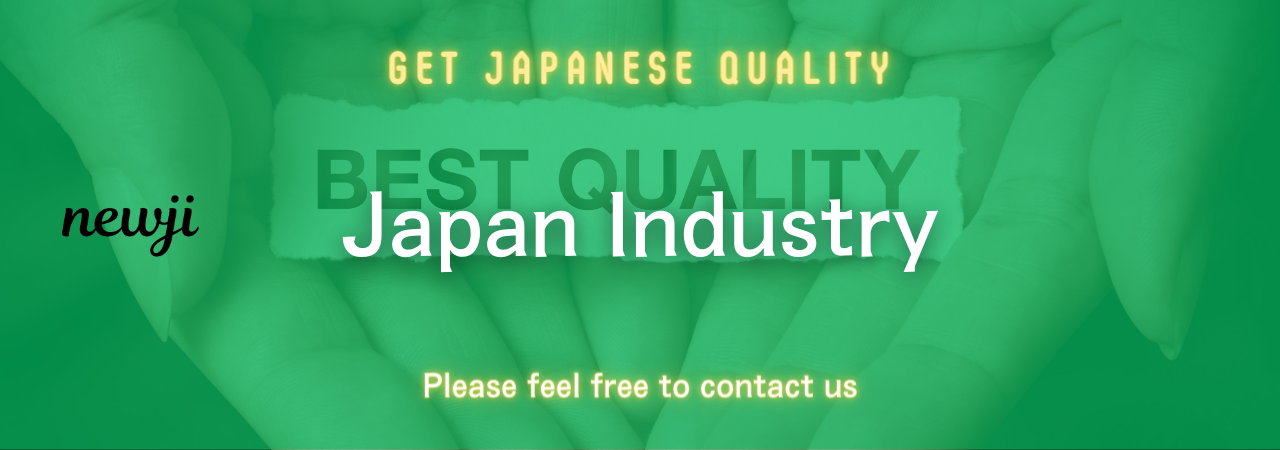
When selecting standard equipment for a project or an industrial setup, a thorough catalog comparison becomes essential.
Choosing the right standard equipment can lead to increased efficiency, reduced costs, and a more streamlined workflow.
By comparing catalogs from different suppliers, you can ensure that you pick the best options for your needs.
目次
Understanding Standard Equipment
Standard equipment refers to the basic machinery, tools, and facilities used in various industries and projects.
They are often prefabricated and come with fixed specifications.
These equipment types are utilized across multiple applications and industries due to their versatility and reliability.
Standard equipment ranges from hand tools to complex machinery like pumps, valves, and conveyor systems.
They are designed to meet general requirements, eliminating the need for custom manufacturing.
This makes them more cost-effective and faster to implement compared to bespoke equipment.
Why Catalog Comparison Matters
Cost Efficiency
Comparing multiple catalogs allows you to gauge the price differences across various suppliers.
This can help identify cost-saving opportunities without compromising quality.
By understanding market pricing trends, you can negotiate better deals and reduce expenses.
Quality Assurance
Different suppliers offer varying levels of quality.
Catalog comparison provides insight into the materials, build quality, and durability of the equipment.
It helps to identify the most reliable suppliers and avoid substandard products, ensuring longevity and performance.
Feature Analysis
Not all standard equipment is built the same way, even if they serve identical functions.
A detailed comparison highlights the unique features and specifications of each product.
This information helps in selecting equipment that best fits your specific requirements and adds value to your process.
Supplier Reliability
Through catalog comparison, you can evaluate the reputation and reliability of different suppliers.
Customer reviews, industry ratings, and the history of the suppliers offer valuable insights.
Choosing a trustworthy supplier ensures consistent product quality and excellent after-sales service.
Key Factors to Consider in Catalog Comparison
Specifications and Performance
Review the technical specifications and performance details of the equipment listed in the catalogs.
Consider parameters like size, power output, efficiency, materials, and compatibility with existing systems.
High-performance equipment can significantly enhance productivity.
Price and Payment Terms
Analyze the price points and payment terms offered by different suppliers.
Compare the initial costs with the long-term value provided by the equipment.
Look for flexible payment options like installment plans or leasing, which can ease financial pressure.
Warranty and After-Sales Support
Evaluate the warranty terms and after-sales services offered by the suppliers.
Good warranty coverage provides peace of mind and financial protection against defects.
Efficient after-sales support ensures timely maintenance and repair services, reducing downtime.
Compliance and Certifications
Ensure that the equipment complies with industry regulations and standards.
Look for certifications like ISO, CE, or other relevant marks that testify to the equipment’s safety and quality.
Compliance with standards minimizes risks and ensures smooth operational workflows.
Supplier Credentials
Research the background and credentials of the suppliers listed in the catalogs.
Consider their experience, market presence, and customer feedback.
A reputable supplier with positive reviews is more likely to provide reliable and high-quality equipment.
Practical Steps for Catalog Comparison
Identify Your Requirements
Start by defining the specific requirements of your project or operation.
List down the features, specifications, and performance criteria that are vital for your needs.
Having a clear understanding of your requirements helps filter the options efficiently.
Gather Multiple Catalogs
Collect catalogs from various reputable suppliers in your industry.
Digital catalogs are often available on supplier websites, making it easy to gather information.
Ensure that you have a diverse selection to compare different aspects thoroughly.
Use a Comparison Chart
Create a comparison chart to systematically review the features, prices, and specifications of the equipment.
A well-organized chart allows for a side-by-side comparison, making it easier to identify the best options.
Include columns for critical features, pros, cons, and additional comments.
Consult Industry Experts
Seek advice from industry experts or colleagues who have experience with the equipment you are considering.
Their insights and recommendations can provide valuable perspectives and help avoid potential pitfalls.
Expert advice can guide you toward the most suitable and reliable equipment.
Making the Final Decision
After a thorough comparison, narrow down the options to the best few that meet your criteria.
Consider doing a cost-benefit analysis to evaluate the long-term value of each option.
Make sure to factor in the warranty, maintenance costs, and supplier reliability.
Conduct a final review, ensuring that the chosen equipment aligns with your operational goals and budget.
Once confident, proceed with the purchase from the selected supplier, ensuring all terms and conditions are clear.
In conclusion, catalog comparison is a crucial step in selecting standard equipment.
By evaluating various factors such as cost, quality, performance, and supplier reliability, you can make a well-informed decision.
Understanding your needs and conducting a structured comparison ensures that you choose the best equipment for your operations, leading to optimal efficiency and success.
資料ダウンロード
QCD調達購買管理クラウド「newji」は、調達購買部門で必要なQCD管理全てを備えた、現場特化型兼クラウド型の今世紀最高の購買管理システムとなります。
ユーザー登録
調達購買業務の効率化だけでなく、システムを導入することで、コスト削減や製品・資材のステータス可視化のほか、属人化していた購買情報の共有化による内部不正防止や統制にも役立ちます。
NEWJI DX
製造業に特化したデジタルトランスフォーメーション(DX)の実現を目指す請負開発型のコンサルティングサービスです。AI、iPaaS、および先端の技術を駆使して、製造プロセスの効率化、業務効率化、チームワーク強化、コスト削減、品質向上を実現します。このサービスは、製造業の課題を深く理解し、それに対する最適なデジタルソリューションを提供することで、企業が持続的な成長とイノベーションを達成できるようサポートします。
オンライン講座
製造業、主に購買・調達部門にお勤めの方々に向けた情報を配信しております。
新任の方やベテランの方、管理職を対象とした幅広いコンテンツをご用意しております。
お問い合わせ
コストダウンが利益に直結する術だと理解していても、なかなか前に進めることができない状況。そんな時は、newjiのコストダウン自動化機能で大きく利益貢献しよう!
(Β版非公開)