- お役立ち記事
- Causes and countermeasures for damage to equipment and equipment: Fundamentals of metal fatigue, damage analysis, and measures to improve fatigue strength
Causes and countermeasures for damage to equipment and equipment: Fundamentals of metal fatigue, damage analysis, and measures to improve fatigue strength
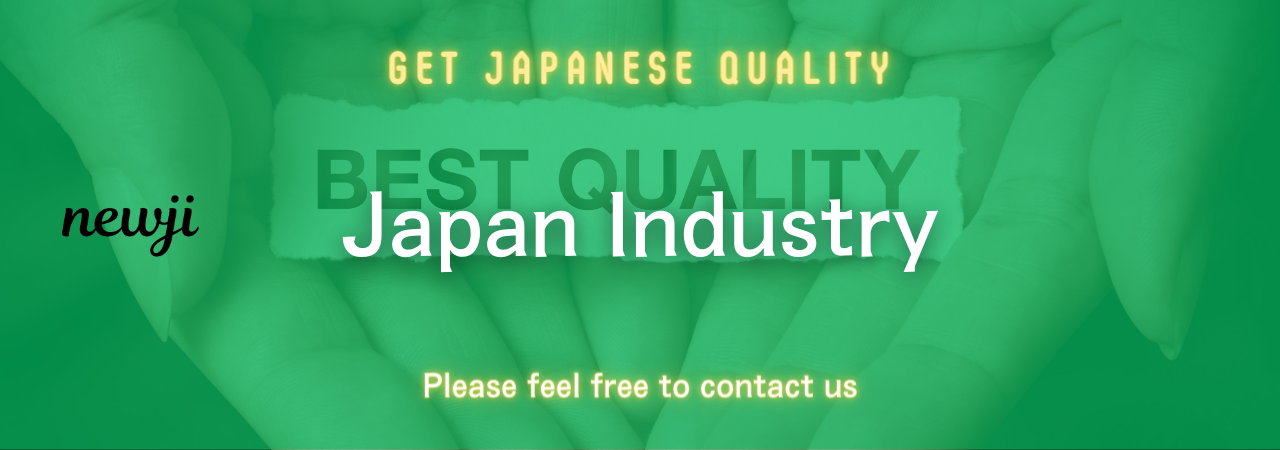
目次
Understanding Metal Fatigue
Metal fatigue is a common phenomenon that can lead to the deterioration and failure of metal parts and equipment over time.
This gradual process is caused by repeated cycles of stress, which lead to microscopic cracks forming in the metal.
Eventually, these cracks can grow large enough to cause structural failure.
Understanding metal fatigue and its fundamental causes is crucial for anyone involved in the maintenance and design of equipment to prevent costly damages and ensure safety.
Fatigue occurs in three stages: crack initiation, crack propagation, and final fracture.
During the crack initiation stage, microscopic cracks begin to form on the surface of the metal.
This is often due to imperfections on the metal surface or stress concentrations caused by features like holes or notches.
As the metal continues to undergo cyclic loading, these cracks propagate, growing both in depth and length until they are large enough to reduce the metal’s overall strength significantly.
Finally, the metal can no longer withstand the load and fractures.
Causes of Metal Fatigue
Several factors contribute to metal fatigue, making it critical to recognize them during the design and maintenance phases.
The primary cause is cyclic loading, which refers to repeated application and release of stress on the metal.
This is common in machinery parts like engine components, turbines, and bridges that experience fluctuating loads throughout their life cycle.
Material properties play a significant role in determining how susceptible a metal is to fatigue.
For example, metals like aluminum and copper tend to be more susceptible to fatigue than steel.
Surface finish is another critical factor.
Rough surfaces with scratches or gouges can act as stress risers, making it easier for cracks to initiate.
Similarly, sharp corners or edges can concentrate stress in small areas, accelerating fatigue failure.
Environmental conditions, such as exposure to corrosive environments or elevated temperatures, also hasten fatigue.
These conditions can weaken the metal, making it more susceptible to crack initiation and propagation.
Analyzing Metal Fatigue
Fatigue analysis is an essential step in identifying potential weaknesses in a metal part before it fails.
There are three primary methodologies used: experimental, analytical, and computational.
Experimental approaches involve subjecting the metal or component to controlled cyclic loading in a lab setting to observe when and how fatigue occurs.
This process, though informative, can be costly and time-consuming.
Analytical methods use mathematical models to predict the fatigue life of a material.
These models generally consider factors such as material properties, loading conditions, and environmental influences.
One common approach is the S-N curve, which represents the relationship between the cyclical load (stress) and the number of cycles to failure.
Computational methods, such as finite element analysis (FEA), offer a sophisticated way to simulate and analyze fatigue without physical testing.
This approach allows engineers to model complex components and predict fatigue life by considering interactions between different parts of the assembly.
Measures to Improve Fatigue Strength
To mitigate fatigue and enhance the longevity of metal components, various measures can be employed during design and manufacturing.
Material selection is fundamental to improving fatigue strength.
Metals with higher fatigue limits, such as certain grades of steel and titanium, offer better resistance to repetitive stresses.
Additionally, employing advanced materials like composites can provide improved fatigue properties for specific applications.
Design optimization is another critical measure.
Reducing stress concentrations by incorporating gradual curves rather than sharp corners can prolong the fatigue life of components.
Similarly, minimizing abrupt changes in cross-sectional areas helps to distribute stress more evenly.
Surface treatment techniques, such as shot peening or surface hardening, enhance the fatigue strength by inducing beneficial residual compressive stresses on the metal surface.
These methods improve the surface finish and make it more difficult for cracks to initiate.
Regular maintenance and inspection are crucial in identifying early signs of fatigue.
Scheduled inspections can detect cracks before they reach a critical size, allowing for timely interventions.
Practices such as non-destructive testing (NDT) can be integrated into regular maintenance routines to assess the integrity of components without causing additional stress.
Practical Applications
Understanding and preventing metal fatigue is vital across various industries.
In the automotive sector, parts such as axles, suspension systems, and engines are frequently subjected to cyclical stresses.
Applying principles of fatigue analysis and employing robust materials can prevent failures that could lead to accidents.
In aerospace, where safety is paramount, understanding metal fatigue is critical.
Aircraft components experience varying loads during takeoffs, flights, and landings.
Designing components with fatigue resistance in mind ensures longer service life and reduces maintenance costs.
Conclusion
The fundamentals of metal fatigue include understanding how this process initiates, propagates, and eventually results in failure.
Comprehending its causes and effectively analyzing fatigue are fundamental for enhancing the durability and safety of machinery and structures.
By implementing strategic measures to improve fatigue strength, such as selecting appropriate materials, optimizing designs, and conducting regular inspections, industries can significantly mitigate the risks associated with metal fatigue.
This ensures the longevity and reliability of vital equipment and infrastructure.
資料ダウンロード
QCD調達購買管理クラウド「newji」は、調達購買部門で必要なQCD管理全てを備えた、現場特化型兼クラウド型の今世紀最高の購買管理システムとなります。
ユーザー登録
調達購買業務の効率化だけでなく、システムを導入することで、コスト削減や製品・資材のステータス可視化のほか、属人化していた購買情報の共有化による内部不正防止や統制にも役立ちます。
NEWJI DX
製造業に特化したデジタルトランスフォーメーション(DX)の実現を目指す請負開発型のコンサルティングサービスです。AI、iPaaS、および先端の技術を駆使して、製造プロセスの効率化、業務効率化、チームワーク強化、コスト削減、品質向上を実現します。このサービスは、製造業の課題を深く理解し、それに対する最適なデジタルソリューションを提供することで、企業が持続的な成長とイノベーションを達成できるようサポートします。
オンライン講座
製造業、主に購買・調達部門にお勤めの方々に向けた情報を配信しております。
新任の方やベテランの方、管理職を対象とした幅広いコンテンツをご用意しております。
お問い合わせ
コストダウンが利益に直結する術だと理解していても、なかなか前に進めることができない状況。そんな時は、newjiのコストダウン自動化機能で大きく利益貢献しよう!
(Β版非公開)