- お役立ち記事
- Causes and countermeasures for delivery delay problems faced by purchasing managers
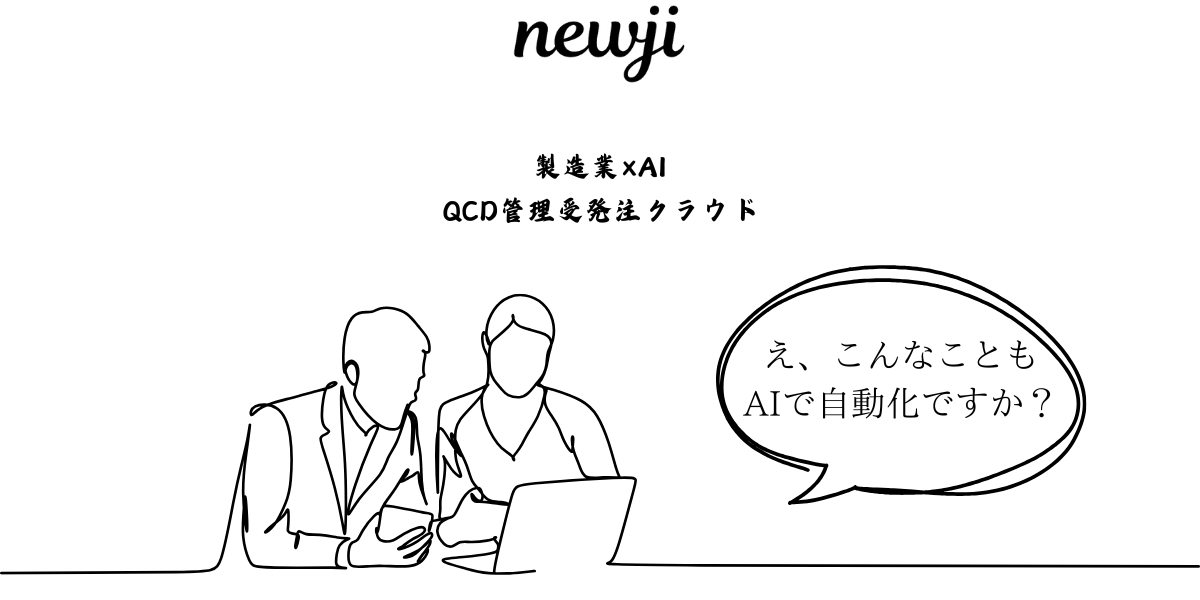
Causes and countermeasures for delivery delay problems faced by purchasing managers
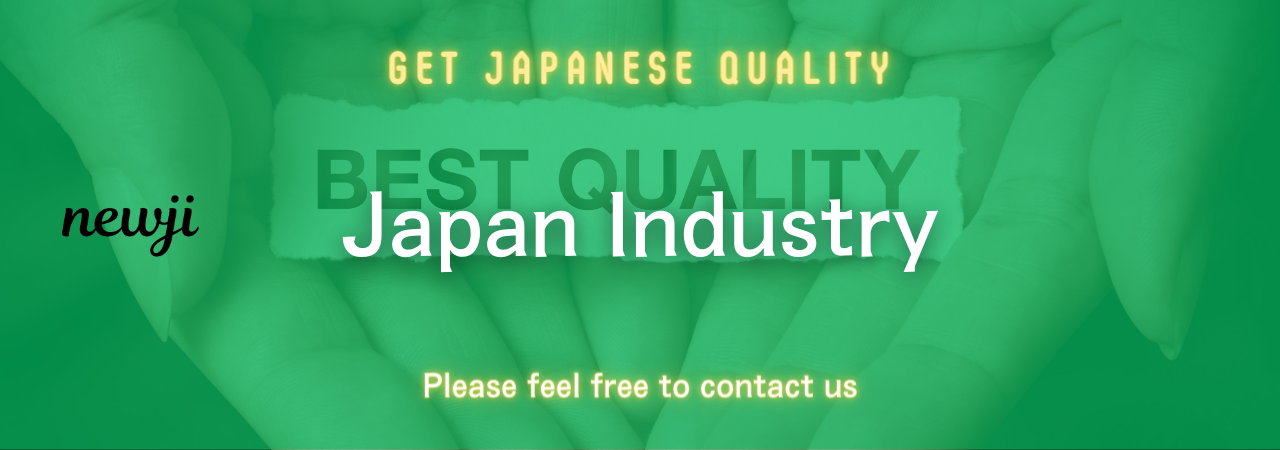
目次
Understanding Delivery Delays
Delivery delays are a common issue faced by purchasing managers.
When products or materials don’t arrive on time, it can disrupt production schedules and potentially lead to customer dissatisfaction.
Understanding the causes of these delays is the first step in managing and mitigating their impact.
Supply Chain Disruptions
One of the primary causes of delivery delays is interruptions within the supply chain.
These disruptions can result from various factors, such as natural disasters, strikes, or geopolitical tensions.
For example, a hurricane might damage roads or facilities, preventing trucks from reaching their destinations.
Similarly, labor strikes at ports can cause goods to sit idle, waiting for workers to process them.
Purchasing managers should establish good communication channels with suppliers to stay informed about potential or existing disruptions.
Building a collaborative relationship can result in suppliers considering your company a priority when operations resume.
Forecasting Errors
Inaccurate demand forecasting can lead to delivery delays.
If a company underestimates the demand for its product, it may not order enough materials or components in advance.
Once the error is realized, the rush to meet unexpected demand can strain suppliers, leading to delays.
To avoid these issues, purchasing managers should regularly review and refine their forecasting techniques.
Using historical data and market analysis can improve accuracy.
Additionally, implementing advanced technologies like AI and machine learning can provide more precise forecasts by analyzing broader datasets.
Production Bottlenecks
Manufacturers sometimes experience bottlenecks in their production processes, causing delays in order fulfillment.
These bottlenecks can occur due to equipment malfunctions, inadequate staffing, or inefficient practices.
Purchasing managers can help mitigate these issues by maintaining open lines of communication with manufacturers.
By understanding their production processes, managers can identify potential bottlenecks and work collaboratively to address them.
Regularly visiting production facilities and engaging in process improvement discussions can also be beneficial.
Transportation Challenges
Transportation is a critical component of the delivery process.
Delays can happen when there are issues with the carriers, such as vehicle breakdowns, accidents, or route disruptions.
Weather conditions, like heavy snowfall or thunderstorms, can also delay shipments.
To counter transportation issues, purchasing managers should diversify their carrier options, ensuring they’re not dependent on a single provider.
Investing in a transportation management system can help identify the fastest and most reliable routes.
Additionally, having contingency plans for various scenarios, like alternative routes or carriers, can keep deliveries on track during adverse conditions.
Supplier Performance
Suppliers can sometimes fail to meet their delivery commitments due to various internal issues.
These might include staffing shortages, financial troubles, or inadequate management systems.
Purchasing managers should regularly evaluate supplier performance to ensure reliability.
This evaluation can include setting key performance indicators (KPIs) to measure factors like on-time delivery rates.
Building a strong relationship and maintaining open dialogue can also foster improvement.
If a supplier continually fails to meet expectations, managers might need to consider alternative suppliers.
Handling Delivery Delays
Despite best attempts to prevent them, delivery delays may still occur.
Having strategies in place to deal with such situations can mitigate negative impacts.
Proactive Communication
When a delay is unavoidable, immediate and transparent communication with all stakeholders is crucial.
This includes informing production teams, sales departments, and even end customers, if applicable.
Providing clear updates on new expected delivery dates and reasons for the delay can help manage expectations and maintain trust.
Building Buffer Stock
Another effective tactic is maintaining a buffer or safety stock for essential materials.
This can help to mitigate the impact of delays.
While this strategy may increase holding costs, it often proves beneficial by ensuring production continuity.
Implementing Technology Solutions
Investing in modern technology solutions, such as supply chain management software, can improve visibility and control over the entire delivery process.
These systems enable real-time tracking of shipments, alerting purchasing managers of any potential delays.
Data analytics can also help identify patterns leading to delays, allowing for preemptive action.
Developing Supplier Relationships
Long-term relationships with key suppliers can foster better service and more reliable delivery schedules.
Suppliers are more likely to prioritize buyers they have a strong, positive relationship with.
Collaborating on process improvements or efficiency projects can also result in mutually beneficial outcomes.
Conclusion
Delivery delays pose significant challenges for purchasing managers.
Understanding the causes can significantly improve a company’s ability to manage and mitigate these disruptions.
By addressing supply chain disruptions, improving forecasting accuracy, managing production bottlenecks, overcoming transportation challenges, and ensuring supplier reliability, purchasing managers can reduce the occurrence and impact of delivery delays.
Employing proactive communication, maintaining buffer stocks, and leveraging technology solutions further enhances an organization’s resilience against potential delays.
Ultimately, developing strong supplier relationships can facilitate smoother operations and more consistent delivery schedules.
資料ダウンロード
QCD調達購買管理クラウド「newji」は、調達購買部門で必要なQCD管理全てを備えた、現場特化型兼クラウド型の今世紀最高の購買管理システムとなります。
ユーザー登録
調達購買業務の効率化だけでなく、システムを導入することで、コスト削減や製品・資材のステータス可視化のほか、属人化していた購買情報の共有化による内部不正防止や統制にも役立ちます。
NEWJI DX
製造業に特化したデジタルトランスフォーメーション(DX)の実現を目指す請負開発型のコンサルティングサービスです。AI、iPaaS、および先端の技術を駆使して、製造プロセスの効率化、業務効率化、チームワーク強化、コスト削減、品質向上を実現します。このサービスは、製造業の課題を深く理解し、それに対する最適なデジタルソリューションを提供することで、企業が持続的な成長とイノベーションを達成できるようサポートします。
オンライン講座
製造業、主に購買・調達部門にお勤めの方々に向けた情報を配信しております。
新任の方やベテランの方、管理職を対象とした幅広いコンテンツをご用意しております。
お問い合わせ
コストダウンが利益に直結する術だと理解していても、なかなか前に進めることができない状況。そんな時は、newjiのコストダウン自動化機能で大きく利益貢献しよう!
(Β版非公開)