- お役立ち記事
- Causes and Countermeasures for Die Swell in Extrusion Molding
月間76,176名の
製造業ご担当者様が閲覧しています*
*2025年3月31日現在のGoogle Analyticsのデータより
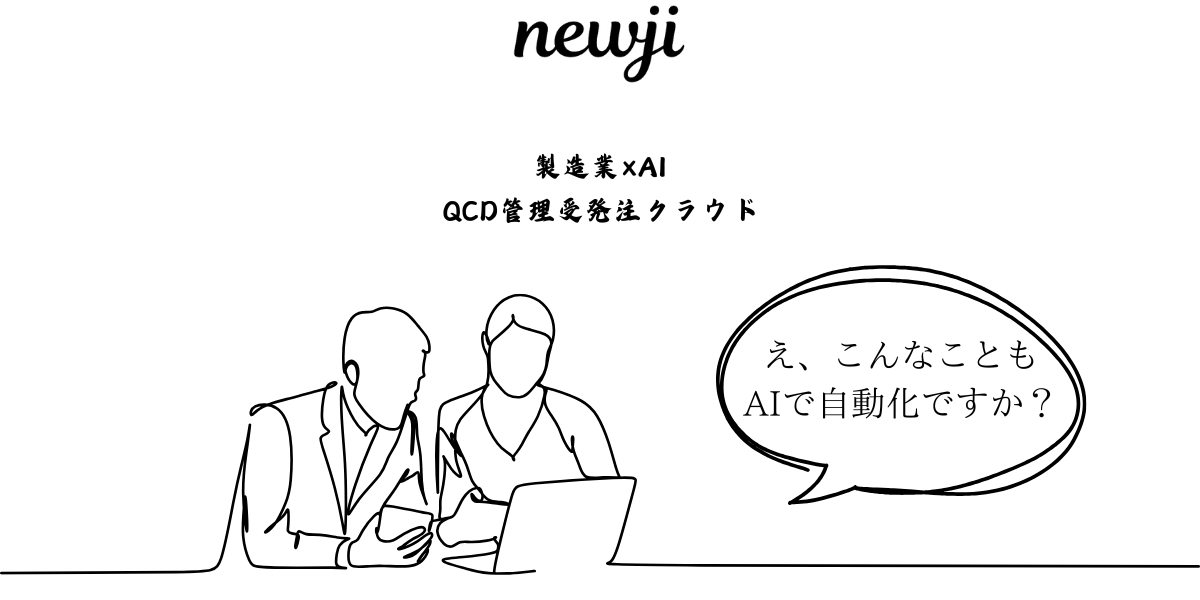
Causes and Countermeasures for Die Swell in Extrusion Molding
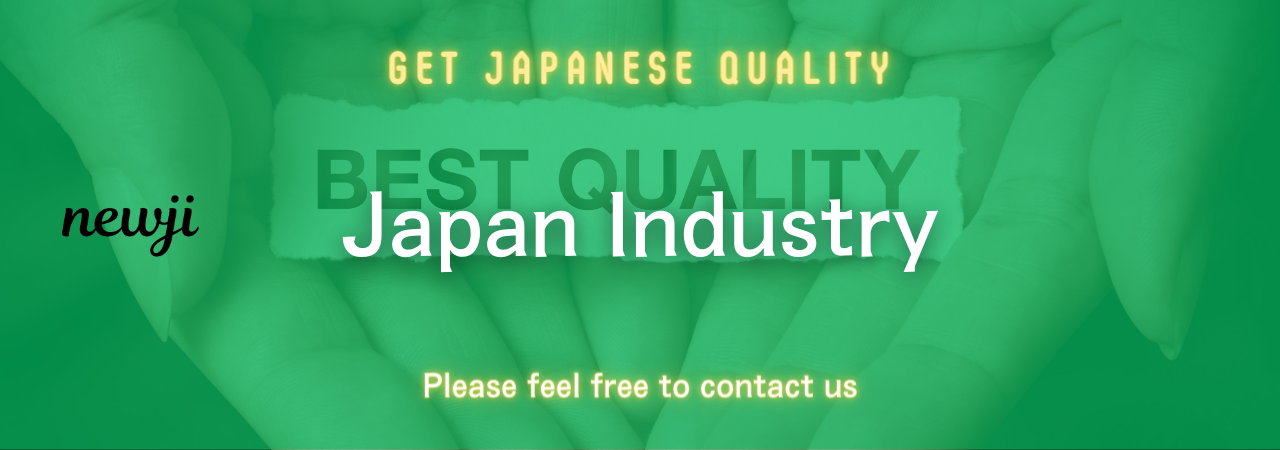
Extrusion molding is a vital process in manufacturing, used to produce products such as pipes, sheets, and films.
However, one common problem encountered in this process is die swell.
Die swell occurs when the extruded material expands upon exiting the die, resulting in a final product that is larger than intended.
This phenomenon can compromise product quality and lead to material wastage.
Understanding the causes of die swell and implementing countermeasures can help optimize the extrusion process.
目次
What is Die Swell?
Die swell, also known as extrudate swell, is the increase in diameter or cross-sectional area of an extruded material as it exits the die.
This expansion occurs because the material, initially compressed and shaped within the die, tries to return to its original form once it is no longer confined.
Impact of Die Swell
Die swell can have several negative impacts on the extrusion process:
– **Dimensional accuracy:** Products may have inconsistent dimensions, making them unsuitable for specific applications.
– **Surface quality:** Uneven expansion can result in a rough or wavy surface finish.
– **Material wastage:** Excessive swell can lead to more scrap material, increasing production costs.
Causes of Die Swell
To effectively counteract die swell, it is essential to understand its root causes.
The primary factors contributing to die swell include:
Polymer Rheology
The flow behavior of polymers, termed rheology, plays a significant role in die swell.
Polymers with high melt viscosity tend to exhibit greater die swell.
Viscosity is influenced by the molecular weight of the polymer and its distribution.
Polymers with higher molecular weights and broad molecular weight distributions typically show higher viscosity, leading to increased die swell.
Elastic Recovery
When the polymer melt exits the die, it undergoes elastic recovery.
This recovery occurs because the material attempts to resume its original shape, causing it to expand.
Materials with high elastic properties tend to exhibit more die swell compared to those with lower elasticity.
Die Design
The geometry of the die can significantly influence the extent of die swell.
Dies with sharp corners or abrupt changes in cross-sectional area can cause higher stress concentrations in the polymer melt.
This stress leads to increased elastic recovery and thus greater die swell.
Conversely, well-designed dies with smooth transitions and optimized geometries can reduce die swell.
Processing Conditions
Several processing conditions impact die swell, including:
– **Temperature:** Higher melt temperatures can reduce viscosity, leading to less die swell.
– **Pressure:** Increased extrusion pressure can enhance the elastic recovery, causing more die swell.
– **Screw speed:** Faster screw speeds can result in higher shear rates, affecting melt viscosity and ultimately die swell.
Countermeasures to Reduce Die Swell
To minimize die swell, manufacturers can implement several strategies involving material selection, die design, and processing conditions.
Material Selection
Selecting the appropriate polymer with favorable rheological properties can significantly reduce die swell.
Materials with lower viscosity and elastic recovery are preferable.
Additives, such as lubricants or plasticizers, can be incorporated to modify the polymer’s properties, reducing viscosity and enhancing processing performance.
Optimizing Die Design
A well-designed die can mitigate die swell. Consider the following design aspects:
– **Die geometry:** Smooth transitions and rounded corners can help distribute stress more evenly, reducing elastic recovery.
– **Die land length:** Increasing the land length of the die can help stabilize the flow of the polymer melt, reducing die swell.
– **Tapered dies:** Tapered dies can slowly reduce the cross-sectional area, minimizing abrupt changes that contribute to die swell.
Adjusting Processing Conditions
Fine-tuning the extrusion process can also help control die swell. Key adjustments include:
– **Temperature control:** Maintaining optimal melt temperatures can reduce the polymer’s viscosity and its tendency to swell.
– **Pressure regulation:** Fine-tuning the extrusion pressure can help manage the extent of elastic recovery.
– **Screw speed adjustment:** Adjusting screw speed can control the shear rate, influencing the polymer’s flow behavior and die swell.
Advanced Techniques for Controlling Die Swell
Beyond basic countermeasures, advanced techniques can further help manage die swell.
Use of Backpressure Devices
Backpressure devices, such as screens and breaker plates, can be employed to stabilize the melt flow.
These devices create a more uniform flow profile, reducing stress concentrations and subsequently minimizing die swell.
Flow Simulation and Modeling
Computational fluid dynamics (CFD) and other simulation tools can predict flow behavior and die swell before manufacturing.
These tools enable engineers to optimize die design and processing conditions based on simulated outcomes, ensuring reduced die swell.
Post-Processing Techniques
In cases where die swell cannot be fully eliminated, post-processing techniques can be employed to rectify the issue.
Processes such as annealing or stretching can help attain the desired product dimensions and properties.
Conclusion
Die swell is a common challenge in extrusion molding that can impact product quality and production efficiency.
Understanding the causes of die swell, including polymer rheology, elastic recovery, die design, and processing conditions, is crucial for effective management.
By selecting appropriate materials, optimizing die design, adjusting processing conditions, and implementing advanced techniques, manufacturers can significantly reduce die swell and enhance the quality of their extruded products.
Consistent monitoring and fine-tuning of these factors will ultimately lead to a more efficient and reliable extrusion process.
資料ダウンロード
QCD管理受発注クラウド「newji」は、受発注部門で必要なQCD管理全てを備えた、現場特化型兼クラウド型の今世紀最高の受発注管理システムとなります。
ユーザー登録
受発注業務の効率化だけでなく、システムを導入することで、コスト削減や製品・資材のステータス可視化のほか、属人化していた受発注情報の共有化による内部不正防止や統制にも役立ちます。
NEWJI DX
製造業に特化したデジタルトランスフォーメーション(DX)の実現を目指す請負開発型のコンサルティングサービスです。AI、iPaaS、および先端の技術を駆使して、製造プロセスの効率化、業務効率化、チームワーク強化、コスト削減、品質向上を実現します。このサービスは、製造業の課題を深く理解し、それに対する最適なデジタルソリューションを提供することで、企業が持続的な成長とイノベーションを達成できるようサポートします。
製造業ニュース解説
製造業、主に購買・調達部門にお勤めの方々に向けた情報を配信しております。
新任の方やベテランの方、管理職を対象とした幅広いコンテンツをご用意しております。
お問い合わせ
コストダウンが利益に直結する術だと理解していても、なかなか前に進めることができない状況。そんな時は、newjiのコストダウン自動化機能で大きく利益貢献しよう!
(β版非公開)