- お役立ち記事
- Causes and Countermeasures for Die Swell Phenomenon in Extrusion Molding
Causes and Countermeasures for Die Swell Phenomenon in Extrusion Molding
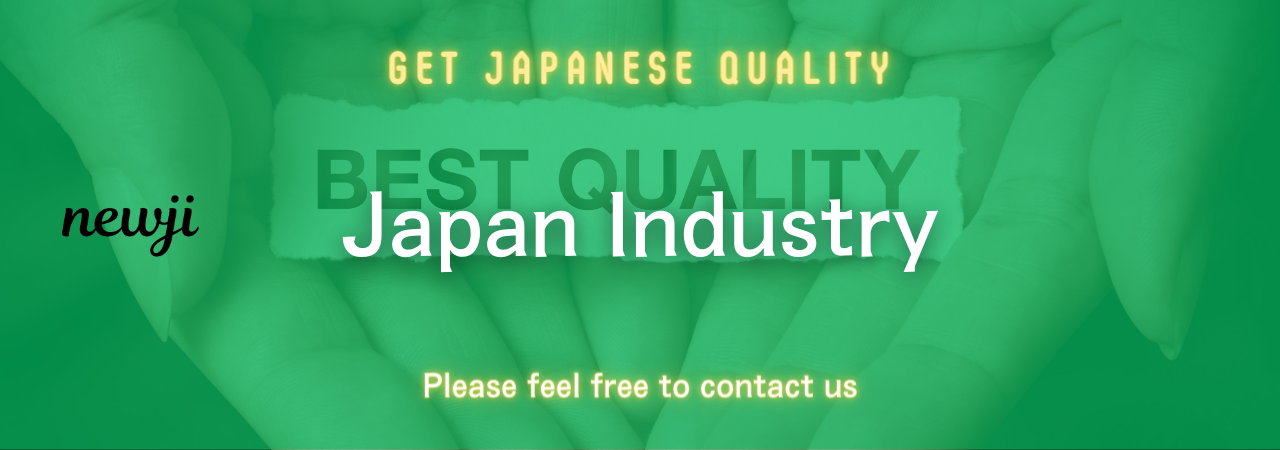
Extrusion molding is a widely used manufacturing process that shapes materials, usually thermoplastics, by pushing them through a die to produce continuous profiles like pipes, sheets, and films.
One significant issue that can occur during this process is die swell, where the extrudate expands upon exiting the die, jeopardizing the precision of the final product.
Understanding the causes and countermeasures for die swell is critical for improving product quality and efficiency in extrusion molding.
目次
What is Die Swell?
Die swell, also known as Barus effect, is the phenomenon where the diameter or thickness of an extrudate increases upon exiting the die.
The material tends to expand as it moves from the high-pressure environment of the die to the relatively lower pressure of the ambient air.
This can result in products that don’t meet the desired specifications, leading to wastage and additional costs.
Causes of Die Swell
Elastic Recovery
One of the primary causes of die swell is elastic recovery or memory effect.
As the polymer melt is pushed through the die, it gets compressed.
When it exits, it attempts to return to its original shape and size, causing the extrudate to swell.
Shear Rate and Shear Stress
High shear rates and shear stress levels inside the die significantly contribute to die swell.
These conditions cause the polymer chains to align and stretch.
Upon exit, the chains relax and retract, leading to expansion.
Viscoelastic Properties
Polymer melts often exhibit both viscous and elastic properties.
The balance between these properties influences the degree of die swell.
Materials with higher elasticity will generally show greater swelling.
Temperature and Viscosity
Temperature plays a vital role in extrusion molding.
Higher temperatures typically lower the viscosity of the polymer melt, making it flow more easily.
However, this can also lead to increased die swell because the material exits the die more rapidly.
Conversely, lower temperatures can cause higher viscosity and reduced flow, resulting in less die swell.
Die Geometry
The design and condition of the die also impact die swell.
A well-designed die with appropriate land length (the straight section at the exit) helps in reducing the swell.
However, worn-out or poorly maintained dies can exacerbate the problem.
Countermeasures for Die Swell
Optimize Temperature
Maintaining the right melt temperature is essential.
By carefully monitoring and adjusting the temperature, you can control the viscosity of the polymer melt, thereby reducing the die swell.
Using cooling devices can help in managing the temperature more efficiently.
Adjust Shear Rate
Controlling the shear rate inside the die is another effective way to mitigate die swell.
This can be achieved by optimizing the screw speed and maintaining a consistent feed rate.
Lowering the shear rate can minimize the alignment and stretching of polymer chains, thus reducing die swell.
Modify Die Geometry
Die design plays a critical role in minimizing die swell.
Extending the land length and ensuring it is smooth can help in this regard.
Additionally, regular maintenance of the die to ensure it is free from wear and tear is crucial.
Choose the Right Material
Selecting materials with lower elastic properties can help in reducing die swell.
Consulting with material experts to choose the best polymer for your specific application can make a significant difference.
Use of Additives
Certain additives can be mixed with the polymer melt to reduce die swell.
These additives can alter the viscoelastic properties of the material, making it less prone to swelling upon extrusion.
Controlled Cooling
Implementing a controlled cooling system can aid in reducing die swell.
By gradually cooling the extrudate, you allow the polymer chains to relax in a more controlled manner, thereby minimizing expansion.
Testing and Monitoring
Regular Testing
Consistent testing and monitoring of the extrusion process are essential for identifying and addressing die swell issues promptly.
Using quality control measures such as regular sampling and dimensional checks can provide real-time data, helping you make necessary adjustments quickly.
Advanced Monitoring Systems
Employing advanced monitoring systems can significantly enhance the control of die swell.
Modern extrusion lines are equipped with sensors and automated control systems that can provide detailed insights into parameters like temperature, pressure, and shear rate.
Case Studies and Examples
Case Study: Reducing Die Swell in Pipe Extrusion
A company producing PVC pipes faced significant issues with die swell, resulting in inconsistent pipe diameters.
By implementing a combination of optimizing the extrusion temperature, adjusting the shear rate, and extending the land length of the die, they managed to reduce the die swell by 30%.
This led to considerable improvements in product consistency and reduced material wastage.
Example: Film Extrusion
In the film extrusion industry, a manufacturer was struggling with die swell that affected the thickness uniformity of their films.
After a detailed analysis, they decided to use a different polymer with lower elastic properties and incorporated a cooling system.
These measures successfully minimized the swell and improved the quality of their film products.
Conclusion
Understanding the causes of die swell in extrusion molding and implementing effective countermeasures is crucial for ensuring product quality and operational efficiency.
By optimizing temperature, controlling shear rate, modifying die geometry, and using appropriate materials and additives, manufacturers can significantly reduce the impact of die swell.
Regular testing and advanced monitoring further aid in maintaining consistency and precision in the extrusion process.
Employing these strategies will lead to higher product quality, reduced waste, and ultimately, a more profitable and efficient manufacturing operation.
資料ダウンロード
QCD調達購買管理クラウド「newji」は、調達購買部門で必要なQCD管理全てを備えた、現場特化型兼クラウド型の今世紀最高の購買管理システムとなります。
ユーザー登録
調達購買業務の効率化だけでなく、システムを導入することで、コスト削減や製品・資材のステータス可視化のほか、属人化していた購買情報の共有化による内部不正防止や統制にも役立ちます。
NEWJI DX
製造業に特化したデジタルトランスフォーメーション(DX)の実現を目指す請負開発型のコンサルティングサービスです。AI、iPaaS、および先端の技術を駆使して、製造プロセスの効率化、業務効率化、チームワーク強化、コスト削減、品質向上を実現します。このサービスは、製造業の課題を深く理解し、それに対する最適なデジタルソリューションを提供することで、企業が持続的な成長とイノベーションを達成できるようサポートします。
オンライン講座
製造業、主に購買・調達部門にお勤めの方々に向けた情報を配信しております。
新任の方やベテランの方、管理職を対象とした幅広いコンテンツをご用意しております。
お問い合わせ
コストダウンが利益に直結する術だと理解していても、なかなか前に進めることができない状況。そんな時は、newjiのコストダウン自動化機能で大きく利益貢献しよう!
(Β版非公開)