- お役立ち記事
- Causes of human error at manufacturing sites and points to countermeasures
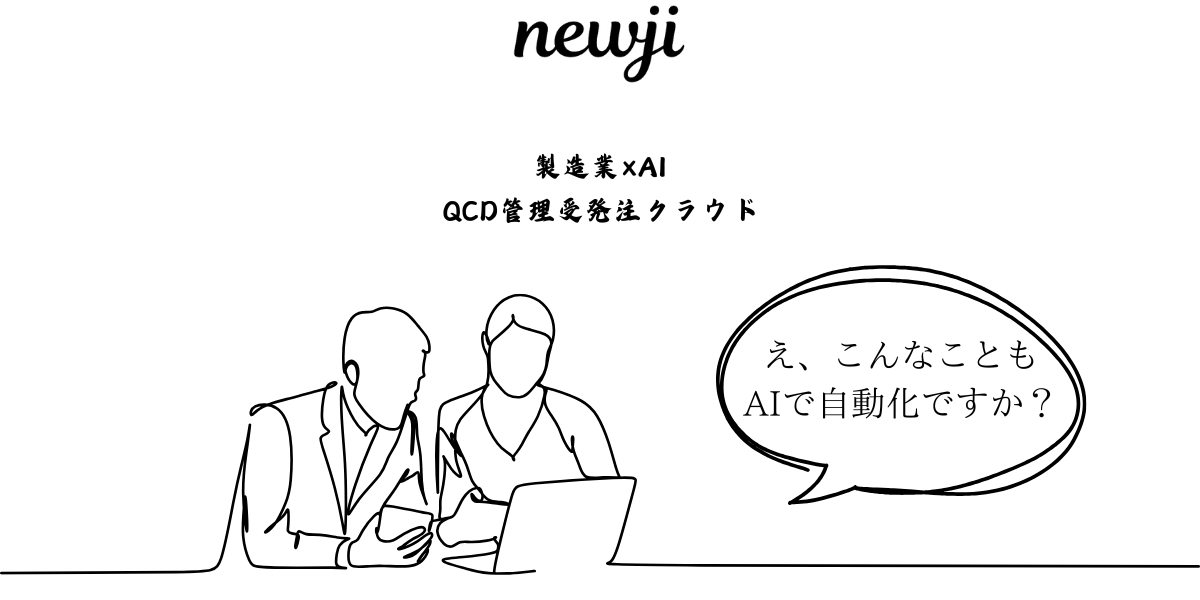
Causes of human error at manufacturing sites and points to countermeasures
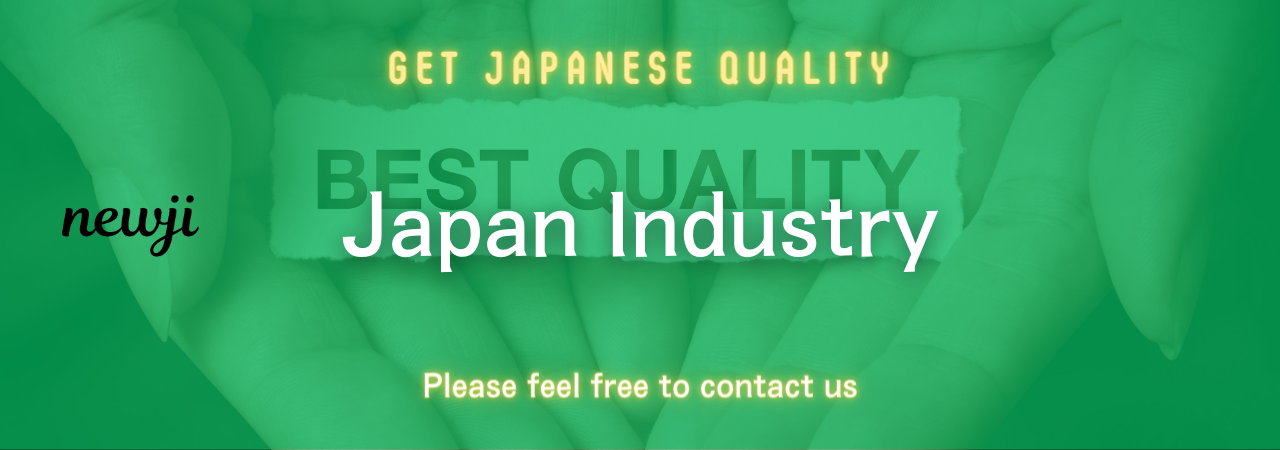
目次
Understanding Human Error in Manufacturing
When we think about manufacturing, precision and efficiency come to mind.
However, human error is an inevitable part of any operation involving people.
Manufacturing sites are no exception.
Understanding the causes of human error in these settings is crucial for improving productivity and safety.
What is Human Error?
Human error refers to mistakes made by people.
These mistakes can occur due to various reasons, ranging from lack of knowledge to mere oversight.
In manufacturing, human error can lead to defective products, equipment damage, or even accidents resulting in injury.
Common Causes of Human Error in Manufacturing
Poor Training and Skill Levels
One of the primary reasons for human error in manufacturing settings is inadequate training.
When workers are not well-trained, they may not understand their tasks fully or know how to properly operate machinery.
Lack of skills increases the likelihood of mistakes.
Fatigue and Overwork
Another significant cause is fatigue.
Workers who are tired or overworked are more prone to errors.
Long shifts without adequate breaks can lead to decreased concentration and increased risk of mistakes.
Complexity of Tasks
The complexity of a task can also contribute to human error.
When tasks are too complicated, workers may have difficulty keeping track of every detail, leading to errors.
Simplifying processes where possible can help reduce this risk.
Poor Communication
Miscommunication or lack of communication can also lead to errors.
If instructions are unclear or not conveyed properly, workers might misunderstand what is expected, resulting in mistakes.
Effective communication is key in preventing such errors.
Inadequate Supervision and Support
In some cases, the absence of proper supervision can lead to errors.
Without guidance or feedback, workers might continue making mistakes without realizing it.
Adequate supervision ensures that workers adhere to protocols and correct errors promptly.
Strategies for Minimizing Human Error
Enhancing Training Programs
To reduce human error, enhancing training programs is essential.
Regular training sessions and skill-upgrading workshops can help workers understand their roles better and stay informed about the latest best practices.
Implementing Rest and Break Schedules
Establishing proper rest and break schedules can help combat fatigue.
Allowing workers time to rest can greatly improve their performance and reduce the chance of mistakes.
Simplifying Tasks
Whenever feasible, simplifying tasks can decrease the potential for errors.
Streamlining processes and reducing unnecessary steps make it easier for workers to perform tasks accurately.
Improving Communication
Increasing the effectiveness of communication within a manufacturing site is crucial.
This includes ensuring that instructions are clear and relaying important information promptly.
Adopting visual aids and reminders can also improve communication.
Enhancing Supervision and Support
Implementing robust supervision systems helps minimize errors.
By providing immediate feedback and support, supervisors can assist workers in making fewer mistakes and improving their performance.
The Role of Technology in Reducing Human Error
Apart from the strategies mentioned, technology can also play a significant role in reducing human error at manufacturing sites.
Automated Systems
Automating repetitive or complex tasks can significantly reduce the potential for human error.
Automated systems can perform tasks with precision and consistency that is difficult for humans to achieve.
Use of Sensors and Monitoring Tools
Utilizing sensors and monitoring tools can aid in tracking operations and alerting operators to potential issues before they become significant problems.
These technologies can prevent errors by offering real-time feedback.
Data Analytics
Data analytics can be used to identify patterns and predict potential errors.
By analyzing historical data, manufacturers can pinpoint areas of concern and adjust processes proactively to mitigate risks.
The Importance of a Safety Culture
In addition to the measures discussed, fostering a culture of safety is crucial in minimizing human error.
Encouraging workers to prioritize safety over speed can lead to fewer mistakes.
Encouraging Reporting of Errors
Creating an environment where workers feel comfortable reporting mistakes without fear of retribution is vital.
This openness allows for learning from errors and preventing their recurrence.
Promoting Teamwork
Promoting teamwork and collaboration can decrease errors.
When workers collaborate and support each other, they are more likely to catch each other’s mistakes and correct them.
By understanding the root causes of human error and implementing these strategies, manufacturing sites can improve efficiency, reduce waste, and enhance overall safety.
資料ダウンロード
QCD調達購買管理クラウド「newji」は、調達購買部門で必要なQCD管理全てを備えた、現場特化型兼クラウド型の今世紀最高の購買管理システムとなります。
ユーザー登録
調達購買業務の効率化だけでなく、システムを導入することで、コスト削減や製品・資材のステータス可視化のほか、属人化していた購買情報の共有化による内部不正防止や統制にも役立ちます。
NEWJI DX
製造業に特化したデジタルトランスフォーメーション(DX)の実現を目指す請負開発型のコンサルティングサービスです。AI、iPaaS、および先端の技術を駆使して、製造プロセスの効率化、業務効率化、チームワーク強化、コスト削減、品質向上を実現します。このサービスは、製造業の課題を深く理解し、それに対する最適なデジタルソリューションを提供することで、企業が持続的な成長とイノベーションを達成できるようサポートします。
オンライン講座
製造業、主に購買・調達部門にお勤めの方々に向けた情報を配信しております。
新任の方やベテランの方、管理職を対象とした幅広いコンテンツをご用意しております。
お問い合わせ
コストダウンが利益に直結する術だと理解していても、なかなか前に進めることができない状況。そんな時は、newjiのコストダウン自動化機能で大きく利益貢献しよう!
(Β版非公開)