- お役立ち記事
- Causes of injection molding defects, measures to prevent them, and their key points
月間76,176名の
製造業ご担当者様が閲覧しています*
*2025年3月31日現在のGoogle Analyticsのデータより
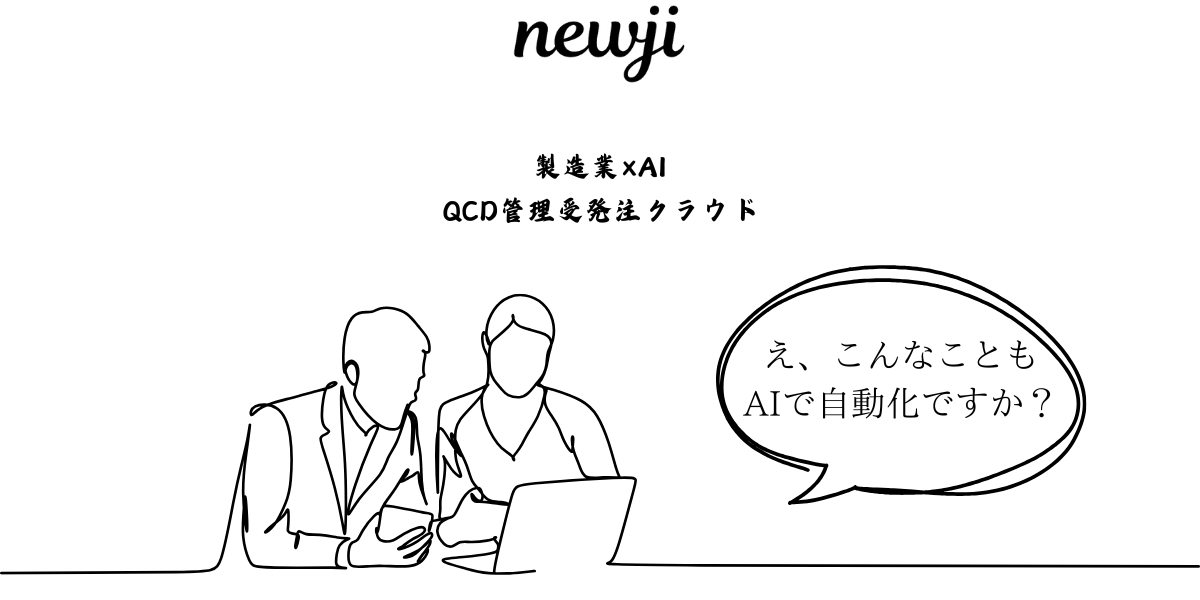
Causes of injection molding defects, measures to prevent them, and their key points
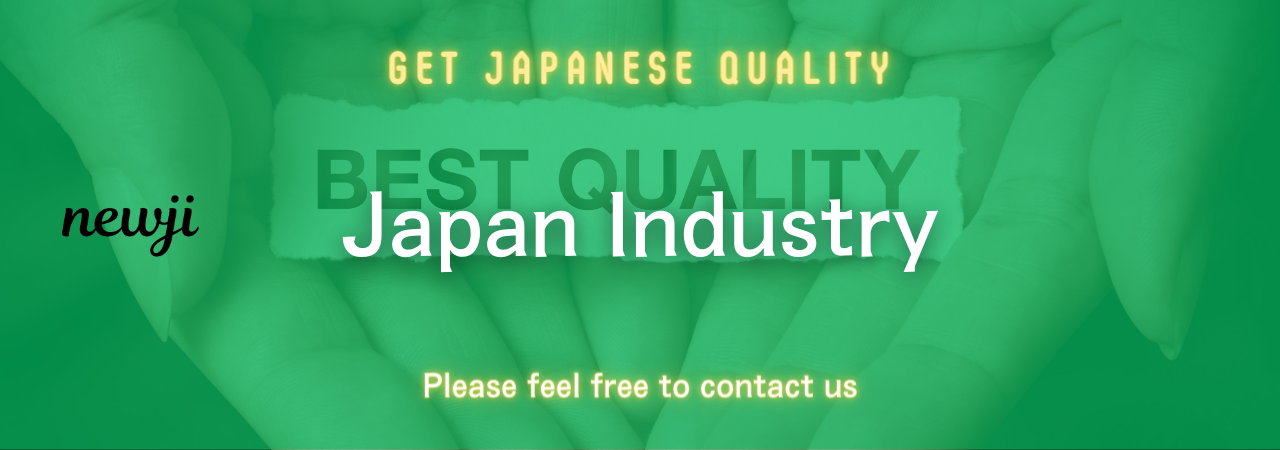
目次
Understanding Injection Molding Defects
Injection molding is a manufacturing process used to produce parts by injecting molten material into a mold.
Despite its precision and efficiency, the process often encounters defects that can compromise the quality of the final product.
Understanding the causes of these defects is crucial in implementing effective measures to prevent them.
Injection molding defects can arise from various sources, including material issues, machine problems, and improper processing parameters.
Some of the most common defects encountered in injection molding production are warping, short shots, sink marks, and weld lines.
Common Causes of Injection Molding Defects
One primary cause of defects in injection molding is improper material selection.
Choosing materials that are incompatible with the desired part application or mold design can lead to issues such as warping and surface blemishes.
Additionally, using contaminated or recycled materials can result in inconsistent parts and compromised structural integrity.
Machine malfunction is another significant factor leading to mold defects.
Problems such as inadequate clamping force, uneven mold temperature, or faulty screws can result in issues like flash or short shots.
Furthermore, machines that are poorly maintained or improperly calibrated can produce parts that fail to meet desired specifications.
Processing parameters, such as injection speed, pressure, and temperature, play a critical role in ensuring defect-free parts.
Incorrect adjustments in these parameters can lead to defects such as sink marks, voids, and burn marks.
Preventive Measures for Injection Molding Defects
To mitigate the occurrence of defects in injection molding, it is essential to focus on three major areas: material management, machine maintenance, and process optimization.
When it comes to material management, selecting the right material for the specific application is critical.
Understanding the properties and the suitability of the materials with respect to the mold design will go a long way in preventing defects.
Keeping materials clean and stored under appropriate conditions will reduce the chance of contamination.
Regular machine maintenance is crucial for preventing technical glitches that can cause defects.
Regularly inspecting and recalibrating machines will ensure optimal performance and consistent product quality.
Maintaining the mold itself through regular cleaning and checking for wear and tear is equally important.
Process optimization involves fine-tuning the injection speed, pressure, and temperature to suit the material and mold design.
Using technology like computer-aided engineering (CAE) tools can help simulate the process and identify the ideal parameters needed to produce defect-free parts.
Key Points for Successful Injection Molding
Ensuring success in injection molding requires a comprehensive approach that combines material knowledge, proper machine operation, and optimal processing conditions.
Key Considerations in Material Selection
When selecting materials, always consider the end application and environment the part will be subjected to.
Materials should be sorted and cleaned to avoid contamination and ensure a consistent melt.
Proper drying of materials before processing is also vital to prevent moisture-induced defects.
The Importance of Machine Calibration
An adequately calibrated machine ensures components are produced within the tolerances specified in the design.
It’s vital to monitor and adjust clamping force, temperature settings, and injection speeds to match the desired production parameters.
Staff training on machine operation is equally crucial to prevent human errors during the production process.
Optimizing Processing Conditions
Having defined processing conditions is key in reducing the variability and defects in the production process.
Careful monitoring and control of cycle time, cooling rate, and ejection speed, for example, play an important role in maintaining product consistency.
Utilizing smart manufacturing tools can aid in monitoring real-time data and making necessary adjustments quickly.
Conclusion
Injection molding is a highly efficient process capable of producing complex parts from a variety of polymers.
However, this efficiency can be undermined by defects, which are often preventable through proper material selection, regular machine maintenance, and optimized processing conditions.
Understanding the underlying causes of defects allows manufacturers to implement targeted measures that improve overall product quality and consistency.
By focusing on these key aspects, businesses can enhance their injection molding operations and deliver high-quality products.
資料ダウンロード
QCD管理受発注クラウド「newji」は、受発注部門で必要なQCD管理全てを備えた、現場特化型兼クラウド型の今世紀最高の受発注管理システムとなります。
ユーザー登録
受発注業務の効率化だけでなく、システムを導入することで、コスト削減や製品・資材のステータス可視化のほか、属人化していた受発注情報の共有化による内部不正防止や統制にも役立ちます。
NEWJI DX
製造業に特化したデジタルトランスフォーメーション(DX)の実現を目指す請負開発型のコンサルティングサービスです。AI、iPaaS、および先端の技術を駆使して、製造プロセスの効率化、業務効率化、チームワーク強化、コスト削減、品質向上を実現します。このサービスは、製造業の課題を深く理解し、それに対する最適なデジタルソリューションを提供することで、企業が持続的な成長とイノベーションを達成できるようサポートします。
製造業ニュース解説
製造業、主に購買・調達部門にお勤めの方々に向けた情報を配信しております。
新任の方やベテランの方、管理職を対象とした幅広いコンテンツをご用意しております。
お問い合わせ
コストダウンが利益に直結する術だと理解していても、なかなか前に進めることができない状況。そんな時は、newjiのコストダウン自動化機能で大きく利益貢献しよう!
(β版非公開)