- お役立ち記事
- Causes of molding defects and check points for occurrence
月間73,982名の
製造業ご担当者様が閲覧しています*
*2025年1月31日現在のGoogle Analyticsのデータより
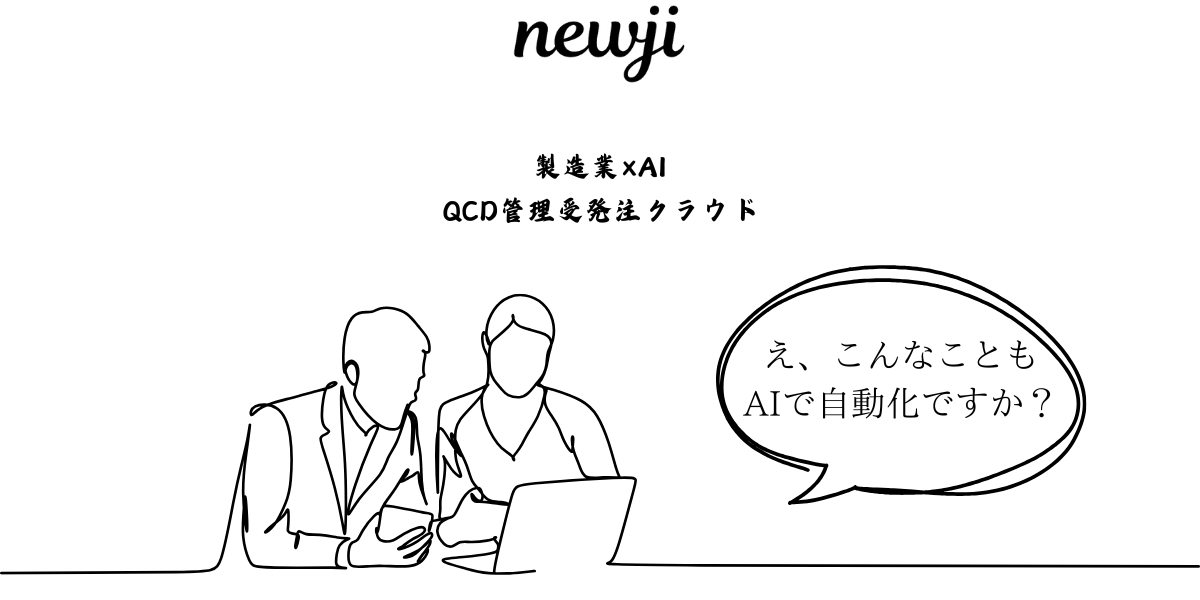
Causes of molding defects and check points for occurrence
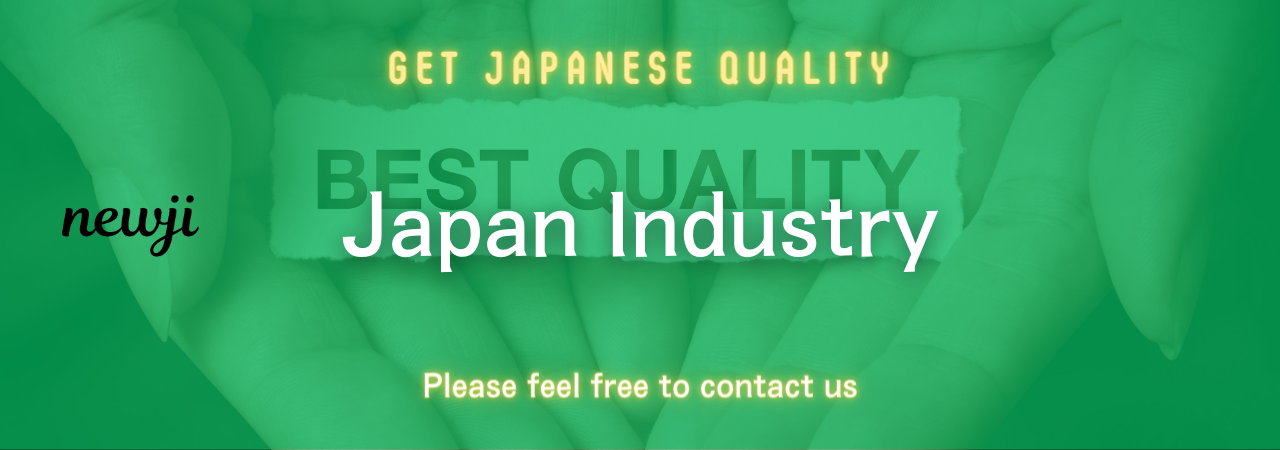
目次
Understanding Molding Defects
Molding defects can be a significant pain in the manufacturing process, leading to wasted time, increased costs, and compromised product quality.
Understanding the causes of these defects and knowing how to identify them early can save manufacturers from these headaches.
Molding defects occur for various reasons, and recognizing them is the first step in rectifying the problem.
Common Types of Molding Defects
There are numerous types of molding defects, each with its causes and solutions.
Some of the most common types include short shots, sink marks, warping, and jetting.
**Short Shots**: Short shots occur when the molded part is incomplete because the material didn’t fill the mold cavity entirely.
This defect often results from inadequate material, low injection pressure, or improper venting.
**Sink Marks**: Sink marks are small depressions on the surface of the molded part.
They often occur due to cooling issues, thick wall sections that cause shrinkage, or inadequate packing pressure.
**Warping**: Warping is a distortion that results in a deformed part.
It typically happens due to uneven cooling, material shrinkage, or internal stresses.
**Jetting**: Jetting happens when the molten plastic squirts into the mold cavity rapidly, causing a wavy pattern.
This defect usually arises from high injection speeds, low melt temperature, or improper gating design.
Causes of Molding Defects
Understanding the causes behind molding defects is critical for preventing them.
Some common causes include material defects, machine errors, and design issues.
Material Defects
Material quality plays a significant role in the molding process.
Impurities or inconsistencies in the material can lead to defects.
Moisture content is a particular area of concern, as excess moisture can cause bubbles or voids in the final product.
Using recycled material without proper preparation can also lead to inferior molding quality.
Machine Errors
Improper machine calibration is a frequent culprit of molding defects.
If the machine settings are not optimized for the specific material or mold, defects are likely to occur.
Equipment wear and tear over time can also affect performance, leading to inconsistencies during the molding process.
Design Issues
Design flaws are often at the heart of many molding problems.
If the mold design doesn’t account for areas where cooling rates might vary, it can lead to defects like warping or sink marks.
Poor gate design or incorrect runner size can also result in blemishes such as short shots or jetting.
Prevention and Detection
While understanding the causes of defects is essential, implementing measures to prevent and detect these issues early is equally critical.
Regular Maintenance
Routine maintenance of molding machines ensures they perform at optimal levels, reducing the likelihood of errors.
Regularly checking and calibrating the machine settings based on the material and product specification is also necessary.
Material Inspection
Choosing the right material and conducting thorough inspections can help prevent defects.
Ensuring the material is dry and free from impurities is crucial before it is used in production.
Additionally, understanding the material properties and how they behave under different molding conditions can help in setting the right parameters.
Optimizing the Mold Design
A well-designed mold can drastically reduce the risk of defects.
Designers should focus on ensuring uniform wall thickness, appropriate gate locations, and proper venting.
Using advanced simulation software can help predict potential defects and allow designers to adjust the mold design accordingly before production begins.
Checklist for Identifying Molding Defects
Having a checklist can aid in the early detection of molding defects, maintaining product quality, and reducing waste.
Visual Inspection
A thorough visual inspection should be the first step to identify any surface defects such as sink marks, warping, or inconsistent textures.
Look for visible irregularities or deformation in the shape of the part.
Dimensional Checks
Use precise measurements to ensure that the parts meet the specified dimensions.
Any deviation could indicate a defect that needs addressing.
Functional Testing
If the mold part has a functional purpose, testing it under real-world conditions will help ensure its performance isn’t compromised by defects.
Regular Performance Reviews
Schedule regular reviews to evaluate the manufacturing process and make necessary adjustments.
This should include reviews of both machine performance and operator handling.
Conclusion
Molding defects can disrupt manufacturing efficiency and product quality.
However, by understanding their causes and implementing preventative measures, manufacturers can significantly reduce the occurrence of these defects.
Regular maintenance, proper material selection, and optimized mold design are crucial steps in achieving defect-free production.
Adhering to thorough inspection protocols will ensure any issues are detected early, maintaining product quality and customer satisfaction.
資料ダウンロード
QCD管理受発注クラウド「newji」は、受発注部門で必要なQCD管理全てを備えた、現場特化型兼クラウド型の今世紀最高の受発注管理システムとなります。
ユーザー登録
受発注業務の効率化だけでなく、システムを導入することで、コスト削減や製品・資材のステータス可視化のほか、属人化していた受発注情報の共有化による内部不正防止や統制にも役立ちます。
NEWJI DX
製造業に特化したデジタルトランスフォーメーション(DX)の実現を目指す請負開発型のコンサルティングサービスです。AI、iPaaS、および先端の技術を駆使して、製造プロセスの効率化、業務効率化、チームワーク強化、コスト削減、品質向上を実現します。このサービスは、製造業の課題を深く理解し、それに対する最適なデジタルソリューションを提供することで、企業が持続的な成長とイノベーションを達成できるようサポートします。
製造業ニュース解説
製造業、主に購買・調達部門にお勤めの方々に向けた情報を配信しております。
新任の方やベテランの方、管理職を対象とした幅広いコンテンツをご用意しております。
お問い合わせ
コストダウンが利益に直結する術だと理解していても、なかなか前に進めることができない状況。そんな時は、newjiのコストダウン自動化機能で大きく利益貢献しよう!
(β版非公開)