- お役立ち記事
- Causes of rework and countermeasure points
月間76,176名の
製造業ご担当者様が閲覧しています*
*2025年3月31日現在のGoogle Analyticsのデータより
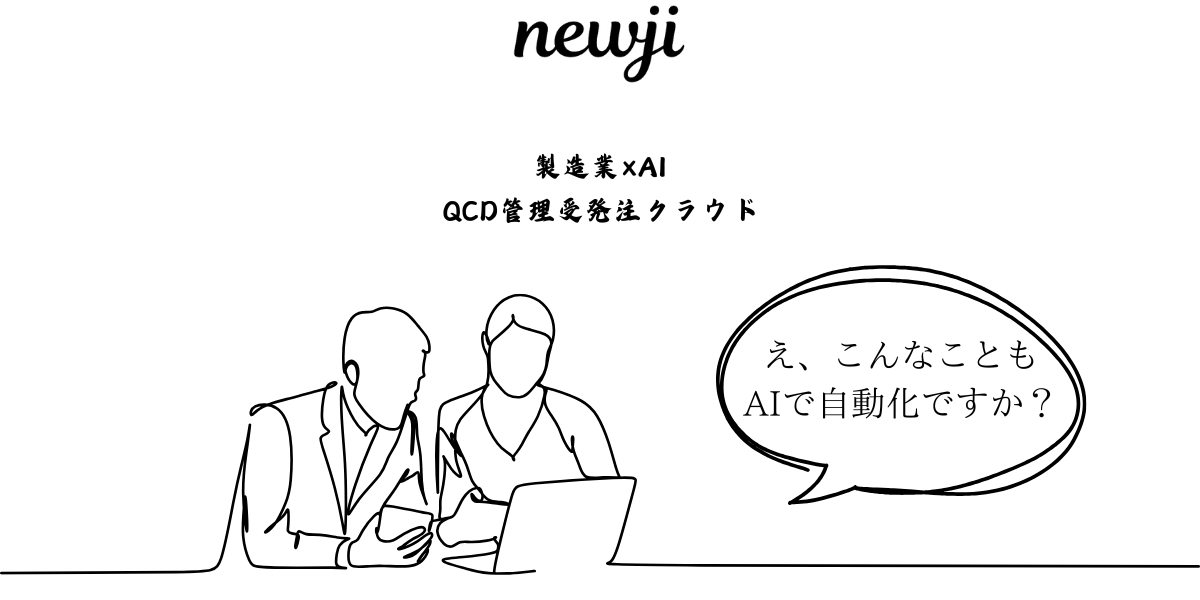
Causes of rework and countermeasure points
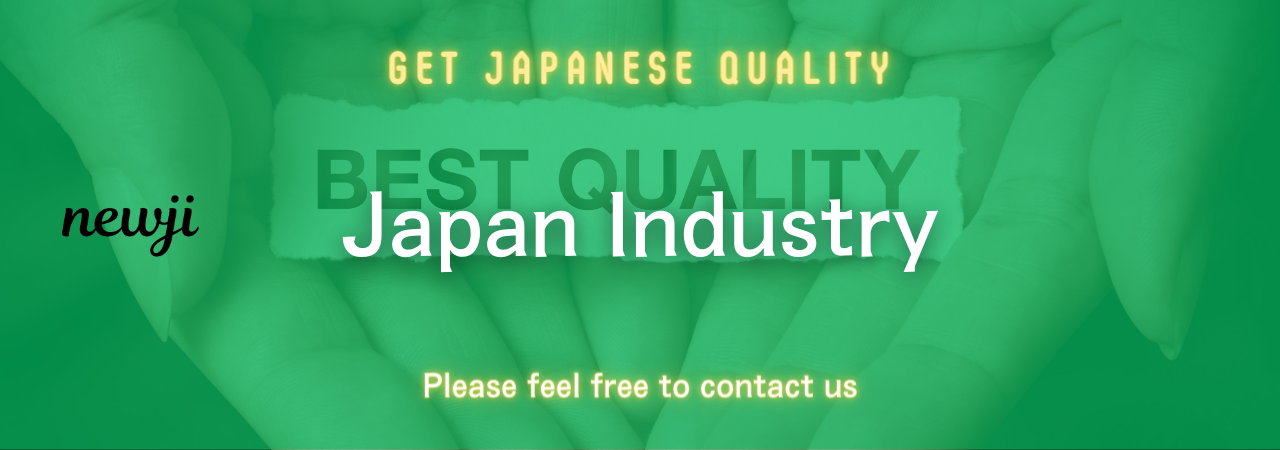
目次
Understanding the Causes of Rework
Rework can be a significant challenge in many industries, often leading to increased costs, extended project timelines, and lower overall efficiency.
To effectively tackle this issue, it’s crucial first to understand its root causes.
By identifying the reasons behind rework, businesses can implement strategies to minimize its occurrence and boost productivity.
Let’s explore some common causes of rework and discuss the countermeasure points associated with each.
Poor Communication
One of the most prevalent causes of rework is poor communication.
When team members are not clear on project requirements, objectives, or instructions, misunderstandings can occur, leading to mistakes that need to be corrected later.
This lack of clarity can result from vague directions, assumptions, or the absence of a cohesive communication plan.
Effective communication is the key to preventing rework due to misunderstandings.
Creating a detailed project brief, holding regular team meetings, and ensuring everyone has access to the necessary information can significantly reduce the likelihood of mistakes.
Inadequate Planning
Another major contributor to rework is inadequate planning.
When a project is not properly planned out from the beginning, it can lead to unforeseen challenges and obstacles down the line.
These issues may require changes or adjustments, resulting in rework.
Comprehensive planning is essential to avoid this scenario.
By taking the time to outline a detailed project plan, teams can anticipate potential problems and develop contingency strategies.
This proactive approach can help prevent rework by ensuring that all necessary resources and steps are considered from the outset.
Poor Quality Control
Poor quality control is often a direct cause of rework, as mistakes or defects in a product or service require corrections.
Without a robust quality control process, errors can go unnoticed until it’s too late, necessitating rework.
Implementing a strong quality control process is crucial for reducing rework.
By performing regular inspections, setting quality benchmarks, and employing quality assurance techniques, businesses can catch errors early and address them before they escalate into larger issues.
Inadequate Skills or Training
When team members lack the necessary skills or training, it can lead to mistakes that need to be corrected, thus causing rework.
Ensuring that all team members are properly trained and equipped to handle their tasks can significantly reduce the occurrence of rework.
Ongoing training and professional development programs can help keep employees up-to-date with the latest skills and techniques in their respective fields.
Providing access to appropriate learning resources can ensure that team members are well-prepared to carry out their roles effectively.
Changing Requirements
When project requirements change after work has already begun, it can lead to rework as teams adjust to meet new expectations.
While some changes may be unavoidable, many can be managed more effectively.
Establishing a clear process for handling changes is important for minimizing rework.
This includes setting guidelines for how changes will be communicated and assessed, as well as determining their impact on the project.
By having a structured approach to managing change, teams can adapt more efficiently and reduce the negative impacts of rework.
Countermeasure Points to Reduce Rework
Understanding the causes of rework is only half the battle.
Implementing countermeasures to address these causes is essential to improving efficiency and productivity.
Below are some key points to consider when developing strategies to reduce rework:
Enhance Communication
Improving communication within a team is critical for minimizing misunderstandings that can lead to rework.
Establish clear guidelines for how information should be shared and ensure that all team members have access to the necessary resources and information.
Invest in Comprehensive Training
Investing in ongoing training and development ensures that team members have the skills and knowledge necessary to perform their tasks effectively.
Providing continuous learning opportunities can help prevent mistakes resulting from inadequate skill levels.
Implement Strong Quality Control Procedures
Establishing a robust quality control process can help catch errors early and minimize the need for rework.
Regular inspections, setting quality standards, and employing effective quality assurance techniques are crucial for maintaining high-quality outcomes.
Plan Thoroughly and Anticipate Challenges
Taking the time to develop a comprehensive project plan can help anticipate potential challenges and reduce the likelihood of rework.
Outline all necessary resources and steps, and create contingency strategies to address any unforeseen issues that may arise.
Develop a Process for Managing Change
Having a structured approach to managing changes in project requirements can help teams adapt efficiently while minimizing the need for rework.
Establish guidelines for assessing and implementing changes and communicating their impact on the project.
Conclusion
Rework can be a significant drain on time and resources if not managed properly.
By understanding its root causes and implementing effective countermeasures, businesses can minimize its occurrence and improve their overall efficiency and productivity.
Ultimately, addressing the causes of rework and applying the appropriate countermeasures can lead to better outcomes, enhanced customer satisfaction, and a more successful project completion.
資料ダウンロード
QCD管理受発注クラウド「newji」は、受発注部門で必要なQCD管理全てを備えた、現場特化型兼クラウド型の今世紀最高の受発注管理システムとなります。
ユーザー登録
受発注業務の効率化だけでなく、システムを導入することで、コスト削減や製品・資材のステータス可視化のほか、属人化していた受発注情報の共有化による内部不正防止や統制にも役立ちます。
NEWJI DX
製造業に特化したデジタルトランスフォーメーション(DX)の実現を目指す請負開発型のコンサルティングサービスです。AI、iPaaS、および先端の技術を駆使して、製造プロセスの効率化、業務効率化、チームワーク強化、コスト削減、品質向上を実現します。このサービスは、製造業の課題を深く理解し、それに対する最適なデジタルソリューションを提供することで、企業が持続的な成長とイノベーションを達成できるようサポートします。
製造業ニュース解説
製造業、主に購買・調達部門にお勤めの方々に向けた情報を配信しております。
新任の方やベテランの方、管理職を対象とした幅広いコンテンツをご用意しております。
お問い合わせ
コストダウンが利益に直結する術だと理解していても、なかなか前に進めることができない状況。そんな時は、newjiのコストダウン自動化機能で大きく利益貢献しよう!
(β版非公開)