- お役立ち記事
- Causes of Weld Lines and Solutions for SMEs
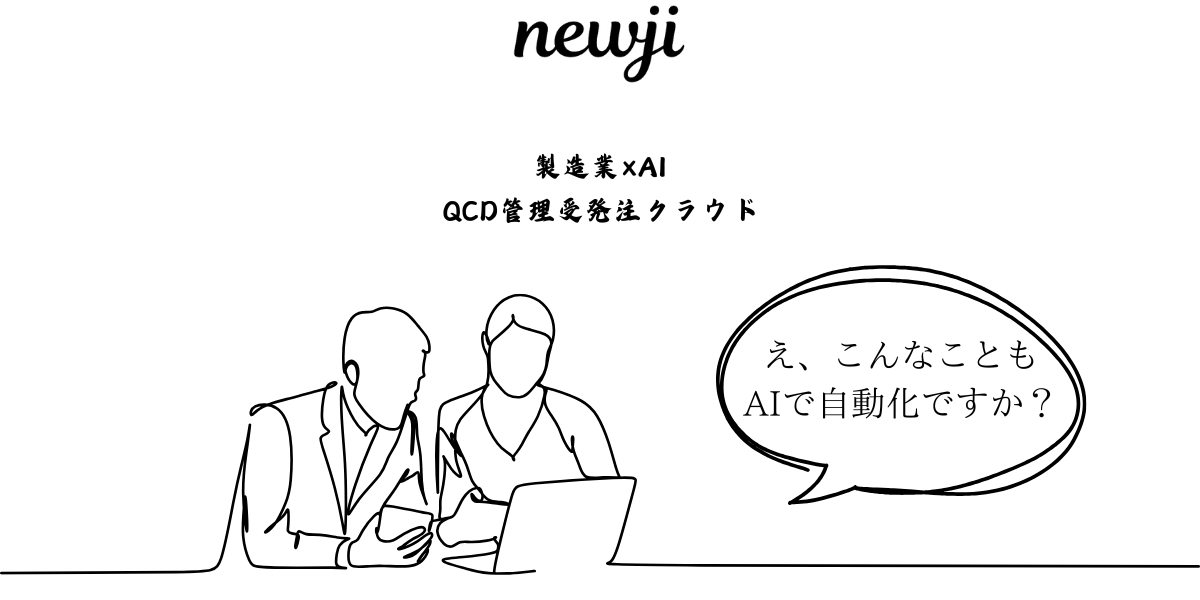
Causes of Weld Lines and Solutions for SMEs
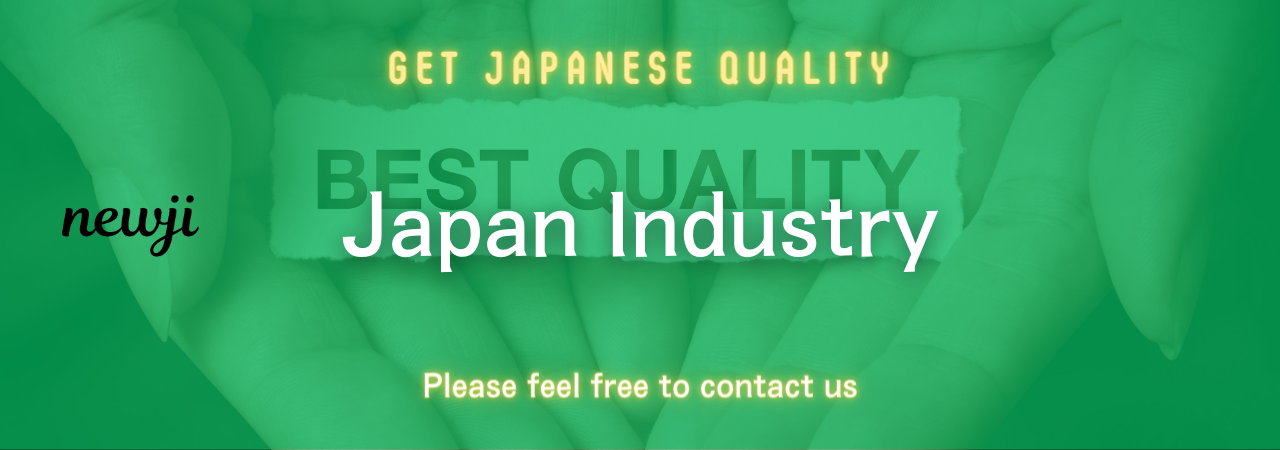
目次
Understanding Weld Lines
Weld lines, also known as knit lines, are a common issue encountered in the injection molding process.
They appear as visible lines on the surface of molded parts, where two or more flow fronts meet and solidify.
These lines not only mar the aesthetic quality of the product but can also compromise its structural integrity.
For small and medium-sized enterprises (SMEs), tackling weld lines is crucial to maintaining product quality and customer satisfaction.
Why Weld Lines Occur
Weld lines are primarily formed when molten material is injected into the mold and splits into two or more paths, later rejoining at some point.
The key causes of this include:
1. **Complex Mold Design**: Mold designs with multiple gates or intricate geometries can lead to the separation of flow fronts, increasing the chances of weld lines.
2. **Inadequate Material Flow**: Slow or unbalanced material flow can cause uneven cooling, which affects the quality of the weld line formed.
3. **Low Temperature and Pressure**: When the material temperature or injection pressure is too low, incomplete fusion of materials occurs at junction points, forming visible lines.
4. **Material Properties**: Certain materials are more prone to weld lines. For example, filled and reinforced plastics tend to show more prominent lines.
Impact on SMEs
For SMEs, weld lines can lead to several drawbacks:
– **Product Rejects**: Poor aesthetics or compromised part strength can lead to increased waste.
– **Customer Dissatisfaction**: Visible defects could result in loss of business or negative customer feedback.
– **Increased Costs**: Addressing defects post-production can increase labor and operational costs.
Effective Solutions to Minimize Weld Lines
Addressing weld lines requires a multi-faceted approach, balancing mold design, process parameters, and material selection.
Mold Design Optimization
1. **Smooth Transitions**: Ensure that the mold design promotes smooth transitions between paths, reducing abrupt flow fronts.
2. **Gate Location Adjustment**: Strategically place gates to control the flow of material, aiming to minimize separation of flow fronts.
3. **Vent Placement**: Ensure proper venting to reduce air traps, which can exacerbate weld line formation.
Process Parameter Adjustments
1. **Temperature Control**: Maintain optimal temperature throughout the mold and material to ensure consistent flow and proper fusion.
2. **Pressure Regulation**: Increase injection pressure to improve the flow of material, ensuring a seamless join at the intersecting paths.
3. **Injection Speed**: Fine-tune the injection speed to balance between quick fills and preventing temperature drop-offs that could cause weld lines.
Material Selection
1. **Choose Compatible Materials**: Select materials with good flow characteristics and fusion properties to reduce the likelihood of weld lines.
2. **Modify Material Properties**: Consider using additives that can improve the material’s flow and adhesion properties.
Advanced Techniques
1. **Vent and Gate Simulation**: Use simulation software to predict and address potential weld line issues early in the design phase.
2. **Variable Mold Temperature Technology**: Employ advanced temperature control techniques, such as localized heating or cooling, to promote better melding at flow fronts.
3. **Ultrasonic Welding**: Utilize ultrasonic energy to eliminate weld lines post-production.
While it may not be practical for all, it’s useful for high-value applications.
The Importance of Monitoring and Quality Assurance
Continuous monitoring during production can help SMEs quickly identify and address any issues.
Implementing a rigorous quality assurance process ensures defects are caught early, minimizing costs and enhancing product quality.
Regular Inspections
1. **Mold and Equipment Checks**: Routine inspections ensure equipment is functioning correctly and molds are undamaged, which affects flow consistency.
2. **Visual and Mechanical Testing**: Regularly check parts for visual defects and perform mechanical tests to ensure integrity.
Employee Training
Educate and train employees on recognizing and addressing weld line issues.
Skilled workers are better equipped to adjust machines and resolve defects efficiently.
Feedback Loop for Continuous Improvement
Establishing a feedback loop between production and design teams can help in identifying recurring issues and devising long-term solutions.
Encouraging open communication leads to shared insights and collaborative problem-solving, which is particularly beneficial for SMEs aiming to optimize their resources.
Conclusion
Managing weld lines efficiently is essential for SMEs to uphold product quality and remain competitive.
By optimizing mold design, adjusting process parameters, selecting suitable materials, and leveraging advanced technologies, SMEs can significantly mitigate weld line issues.
Moreover, fostering an environment of continuous improvement and quality assurance will help in maintaining high production standards and customer satisfaction.
資料ダウンロード
QCD調達購買管理クラウド「newji」は、調達購買部門で必要なQCD管理全てを備えた、現場特化型兼クラウド型の今世紀最高の購買管理システムとなります。
ユーザー登録
調達購買業務の効率化だけでなく、システムを導入することで、コスト削減や製品・資材のステータス可視化のほか、属人化していた購買情報の共有化による内部不正防止や統制にも役立ちます。
NEWJI DX
製造業に特化したデジタルトランスフォーメーション(DX)の実現を目指す請負開発型のコンサルティングサービスです。AI、iPaaS、および先端の技術を駆使して、製造プロセスの効率化、業務効率化、チームワーク強化、コスト削減、品質向上を実現します。このサービスは、製造業の課題を深く理解し、それに対する最適なデジタルソリューションを提供することで、企業が持続的な成長とイノベーションを達成できるようサポートします。
オンライン講座
製造業、主に購買・調達部門にお勤めの方々に向けた情報を配信しております。
新任の方やベテランの方、管理職を対象とした幅広いコンテンツをご用意しております。
お問い合わせ
コストダウンが利益に直結する術だと理解していても、なかなか前に進めることができない状況。そんな時は、newjiのコストダウン自動化機能で大きく利益貢献しよう!
(Β版非公開)