- お役立ち記事
- Cavity Pressure Control in Blow Molding: Key to Quality Stabilization
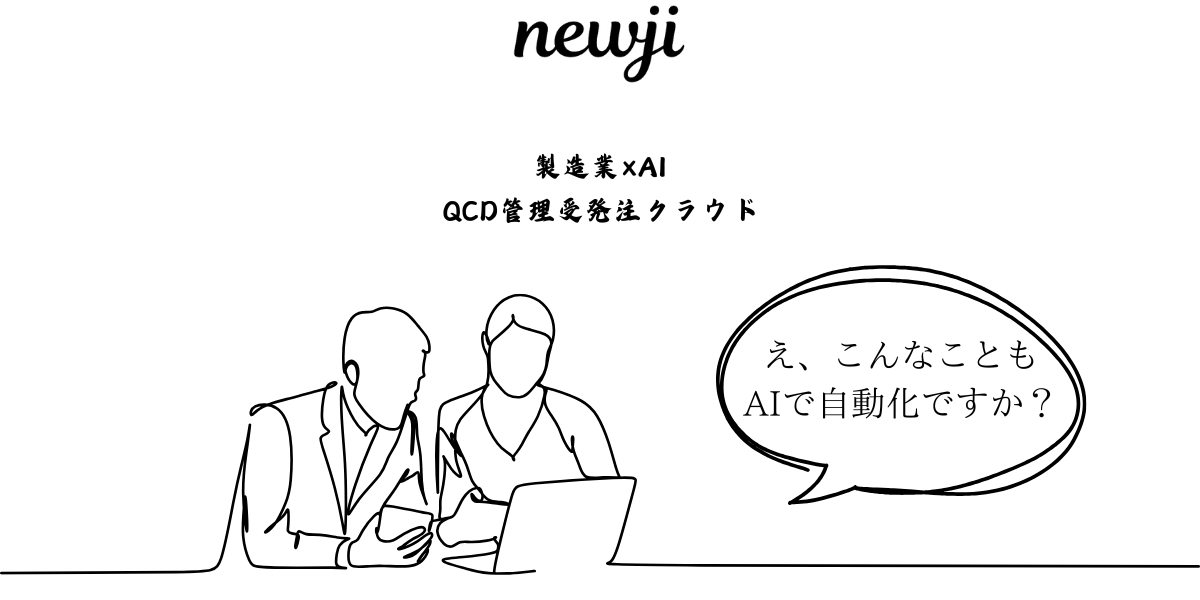
Cavity Pressure Control in Blow Molding: Key to Quality Stabilization
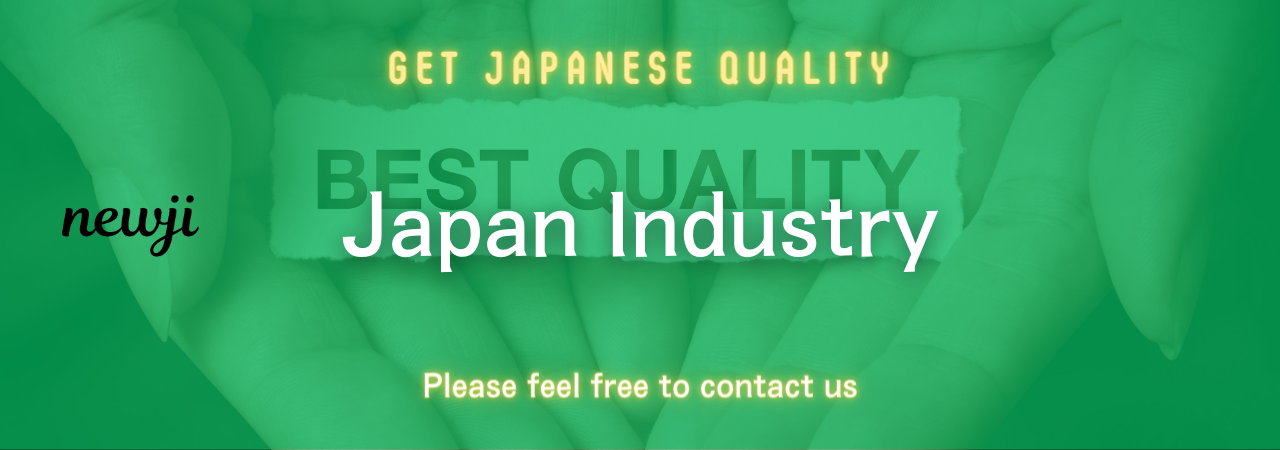
Blow molding is an important manufacturing process used to create hollow plastic parts, like bottles and containers.
Ensuring the quality of these products is essential, which is where cavity pressure control comes in.
Proper cavity pressure control plays a significant role in quality stabilization during blow molding.
Understanding how this works can help manufacturers achieve consistent and reliable results.
目次
What is Blow Molding?
Blow molding is a process used to create hollow plastic objects.
The process involves heating plastic material until it becomes pliable and then injecting it into a mold.
Air is then blown into the mold, forcing the plastic to take its shape.
After cooling, the finished product is removed from the mold, resulting in a hollow object.
There are different types of blow molding, including extrusion blow molding, injection blow molding, and stretch blow molding.
Each type has its specific applications and advantages.
Regardless of the type, cavity pressure control plays a crucial role in ensuring quality products.
Importance of Cavity Pressure Control
Cavity pressure control refers to monitoring and adjusting the pressure within the mold cavity during the blow molding process.
Here’s why it is important:
Consistent Wall Thickness
Maintaining consistent pressure within the mold ensures that the plastic material spreads evenly.
This leads to uniform wall thickness in the final product, which is crucial for both functionality and aesthetics.
Products with inconsistent wall thickness may result in weak spots or deformities.
Improved Strength and Durability
Proper cavity pressure ensures that the plastic material is compacted uniformly.
This leads to improved strength and durability of the final product.
Consistent pressure helps avoid any weak points that might otherwise compromise the product’s integrity.
Enhanced Aesthetic Quality
Proper pressure control helps achieve smoother surfaces and better finishes in the final product.
Irregular pressure can lead to blemishes, marks, or other imperfections that detract from the overall quality.
Minimized Material Waste
By maintaining proper pressure, manufacturers can optimize the amount of material used.
This results in less waste and more cost-effective production.
Inconsistent pressure may lead to excess material usage, which can be costly.
How to Achieve Effective Cavity Pressure Control
Achieving effective cavity pressure control requires a combination of techniques and tools.
Here are some essential steps:
Using Precision Instruments
Utilizing pressure sensors and control systems is key to monitoring the cavity pressure accurately.
These instruments provide real-time data, allowing for adjustments to be made as needed.
High-quality sensors can detect even minor changes in pressure, ensuring optimal control.
Implementing Closed-Loop Systems
Closed-loop control systems are essential for maintaining consistent pressure within the mold cavity.
These systems automatically adjust the pressure based on real-time data from sensors.
By doing so, they ensure that the pressure remains within the desired range, leading to consistent product quality.
Regular Calibration
Regular calibration of instruments is crucial to ensure their accuracy.
Calibration helps in maintaining reliable readings and enables better control over the molding process.
Manufacturers should have a routine schedule for calibrating their instruments.
Proper Maintenance
Regular maintenance of all equipment involved in the blow molding process is vital.
This includes cleaning, inspecting, and replacing worn-out parts.
Proper maintenance ensures that the equipment functions efficiently, leading to better pressure control and product quality.
Challenges in Cavity Pressure Control
While cavity pressure control is crucial, it comes with its set of challenges.
Here are some common issues:
Temperature Fluctuations
Changes in temperature can affect the pressure within the mold cavity.
It is crucial to monitor and control the temperature to ensure consistent pressure levels.
Using temperature control systems can help mitigate this issue.
Material Variations
Different batches of plastic material may have varying properties.
These variations can impact the pressure required for optimal molding.
Manufacturers should perform material testing and adjust the pressure settings accordingly.
Equipment Wear and Tear
Over time, equipment can wear out, leading to inconsistencies in pressure control.
Regular maintenance and timely replacement of parts are essential to avoid such issues.
Proactive equipment management helps sustain reliable pressure control.
Future Trends in Cavity Pressure Control
The field of cavity pressure control is constantly evolving with advancements in technology.
Here are some emerging trends:
Smart Sensors
The development of smart sensors that can provide more detailed data and analytics is on the rise.
These sensors can help manufacturers gain deeper insights into the molding process and make more precise adjustments.
Automation and AI
The integration of automation and artificial intelligence is set to revolutionize cavity pressure control.
AI algorithms can analyze data in real-time and make intelligent decisions to optimize pressure settings.
This leads to more efficient and consistent production processes.
Sustainable Practices
Sustainability is becoming a key focus in manufacturing.
New technologies and practices are being developed to minimize material waste and energy consumption.
Efficient cavity pressure control plays a significant role in achieving these sustainability goals.
In conclusion, cavity pressure control is a critical aspect of the blow molding process.
It ensures consistent quality, enhances product strength and durability, and minimizes material waste.
By using precision instruments, closed-loop systems, and regular maintenance, manufacturers can achieve effective pressure control.
Despite the challenges, advancements in technology are paving the way for more efficient and sustainable practices.
資料ダウンロード
QCD調達購買管理クラウド「newji」は、調達購買部門で必要なQCD管理全てを備えた、現場特化型兼クラウド型の今世紀最高の購買管理システムとなります。
ユーザー登録
調達購買業務の効率化だけでなく、システムを導入することで、コスト削減や製品・資材のステータス可視化のほか、属人化していた購買情報の共有化による内部不正防止や統制にも役立ちます。
NEWJI DX
製造業に特化したデジタルトランスフォーメーション(DX)の実現を目指す請負開発型のコンサルティングサービスです。AI、iPaaS、および先端の技術を駆使して、製造プロセスの効率化、業務効率化、チームワーク強化、コスト削減、品質向上を実現します。このサービスは、製造業の課題を深く理解し、それに対する最適なデジタルソリューションを提供することで、企業が持続的な成長とイノベーションを達成できるようサポートします。
オンライン講座
製造業、主に購買・調達部門にお勤めの方々に向けた情報を配信しております。
新任の方やベテランの方、管理職を対象とした幅広いコンテンツをご用意しております。
お問い合わせ
コストダウンが利益に直結する術だと理解していても、なかなか前に進めることができない状況。そんな時は、newjiのコストダウン自動化機能で大きく利益貢献しよう!
(Β版非公開)