- お役立ち記事
- Cavity Pressure Control Technology in Blow Molding: The Key to Quality Stabilization
Cavity Pressure Control Technology in Blow Molding: The Key to Quality Stabilization
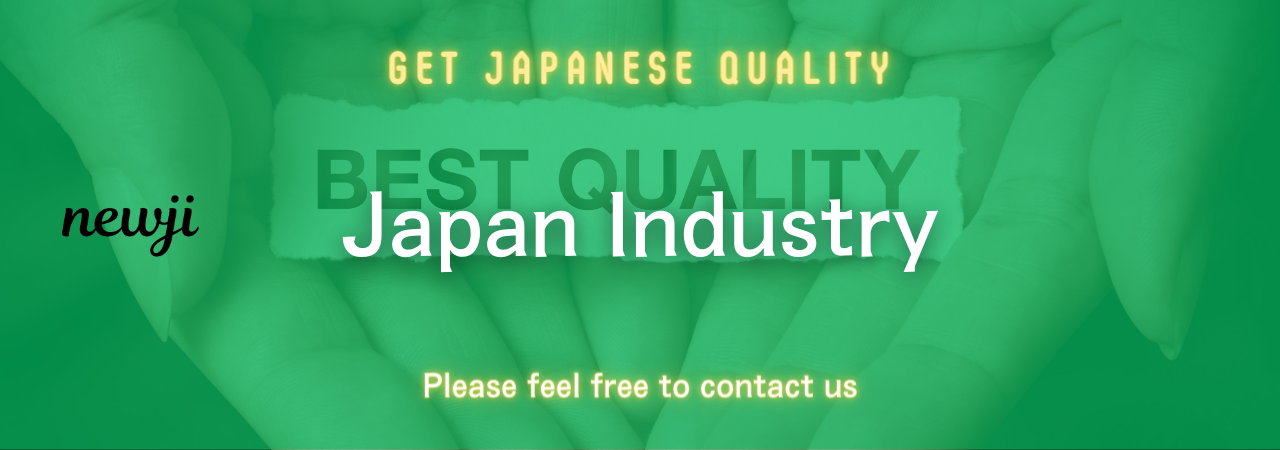
Blow molding is a vital manufacturing process used to produce hollow plastic products like bottles, containers, and automotive parts.
One of the critical factors that ensure the quality and consistency of these products is cavity pressure control technology.
In this article, we’ll explore the importance of cavity pressure control in blow molding, how it works, and its advantages in quality stabilization.
目次
Understanding Blow Molding
Blow molding involves inflating a heated plastic tube, called a parison, inside a mold cavity until it takes the shape of the mold.
This process is widely used because it is efficient for mass production.
There are three primary types of blow molding: extrusion blow molding, injection blow molding, and stretch blow molding.
Each type has its applications and benefits, but they all share the need for precise control over the process parameters to ensure product quality.
The Role of Cavity Pressure
During blow molding, the cavity pressure refers to the pressure exerted on the molten plastic within the mold.
This pressure is crucial because it directly impacts the thickness, uniformity, and overall quality of the final product.
Why Cavity Pressure Control is Crucial
1. Consistency in Product Quality
The most significant advantage of cavity pressure control technology is the ability to produce consistent products.
Uniform cavity pressure ensures that every item produced meets the same quality standards.
This consistency is especially important in industries like food and beverage, where any deviation can lead to issues with packaging integrity.
2. Optimized Material Usage
Controlling cavity pressure helps optimize the amount of material used in each product.
Uniform pressure distribution ensures that the plastic material is evenly spread, minimizing material waste.
This not only reduces costs but also contributes to more sustainable manufacturing practices.
3. Improved Mechanical Properties
Products manufactured with consistent cavity pressure tend to have better mechanical properties.
This includes improved strength, durability, and resistance to deformation.
For industries relying on high-performance plastic parts, such as automotive and aerospace, this is a critical factor.
4. Reduction in Defects
Defects like wall thinning, weak points, and uneven surfaces often result from fluctuations in cavity pressure.
Effective pressure control technology can significantly reduce these defects, leading to higher-quality products and fewer production rejections.
How Cavity Pressure Control Technology Works
Monitoring and Measurement
Cavity pressure control technology starts with accurate monitoring and measurement of the pressure inside the mold.
Sensors are placed strategically within the mold to continuously measure the pressure.
These sensors can detect even the slightest variations, allowing for real-time adjustments.
Feedback Loop Systems
A feedback loop system is a critical component of modern cavity pressure control technology.
This system constantly compares the measured pressure with the desired set point.
If any deviation is detected, it sends signals to adjust the process parameters, such as airflow or cooling rates, to bring the pressure back to the desired level.
Advanced Control Algorithms
Advanced control algorithms are used to predict and correct pressure variations.
These algorithms can analyze the pressure trends and make proactive adjustments to prevent deviations before they occur.
This ensures that the cavity pressure remains stable throughout the blow molding process.
Integration with Manufacturing Execution Systems (MES)
Integration with MES allows for seamless communication between the cavity pressure control system and other manufacturing processes.
This ensures that the entire production line operates in harmony, further enhancing product quality and consistency.
Benefits of Implementing Cavity Pressure Control Technology
Enhanced Process Control
By implementing cavity pressure control technology, manufacturers can achieve enhanced process control.
This means fewer manual interventions are needed, reducing the chances of human error and increasing overall efficiency.
Reduced Downtime
Effective pressure control minimizes defects, leading to fewer production disruptions.
This translates to reduced downtime and increased production uptime, ultimately boosting productivity.
Cost Savings
With optimized material usage and reduced waste, manufacturers can achieve significant cost savings.
Additionally, higher product quality means fewer returns and rejections, further contributing to cost-efficiency.
Compliance with Industry Standards
In industries with strict quality standards and regulations, such as pharmaceuticals and food packaging, cavity pressure control technology is essential.
It helps manufacturers meet and exceed these standards, ensuring the safety and reliability of their products.
Challenges and Future Trends
Initial Investment
One of the challenges in implementing cavity pressure control technology is the initial investment.
High-quality sensors, control systems, and integration can be costly.
However, the long-term benefits often outweigh the initial expenditure.
Complexity of Integration
Integrating cavity pressure control technology into existing manufacturing lines can be complex.
It requires careful planning and expertise to ensure seamless integration without disrupting production.
Advancements in Sensor Technology
As sensor technology continues to evolve, we can expect even more precise and reliable pressure measurements.
This will further enhance the effectiveness of cavity pressure control systems.
AI and Machine Learning
The future of cavity pressure control technology lies in the integration of artificial intelligence (AI) and machine learning.
These technologies can analyze vast amounts of data to predict and control pressure variations with unprecedented accuracy.
Sustainability Initiatives
As sustainability becomes a top priority for manufacturers, cavity pressure control technology will play a crucial role.
By optimizing material usage and reducing waste, this technology will contribute to more sustainable manufacturing practices.
In conclusion, cavity pressure control technology is the key to quality stabilization in blow molding.
By ensuring consistent pressure throughout the molding process, manufacturers can achieve uniform product quality, reduce defects, and optimize material usage.
While there are challenges to implementation, the long-term benefits make it a worthwhile investment for any blow molding operation.
As technology continues to advance, we can expect even greater improvements in cavity pressure control, further enhancing the quality and sustainability of manufacturing processes.
資料ダウンロード
QCD調達購買管理クラウド「newji」は、調達購買部門で必要なQCD管理全てを備えた、現場特化型兼クラウド型の今世紀最高の購買管理システムとなります。
ユーザー登録
調達購買業務の効率化だけでなく、システムを導入することで、コスト削減や製品・資材のステータス可視化のほか、属人化していた購買情報の共有化による内部不正防止や統制にも役立ちます。
NEWJI DX
製造業に特化したデジタルトランスフォーメーション(DX)の実現を目指す請負開発型のコンサルティングサービスです。AI、iPaaS、および先端の技術を駆使して、製造プロセスの効率化、業務効率化、チームワーク強化、コスト削減、品質向上を実現します。このサービスは、製造業の課題を深く理解し、それに対する最適なデジタルソリューションを提供することで、企業が持続的な成長とイノベーションを達成できるようサポートします。
オンライン講座
製造業、主に購買・調達部門にお勤めの方々に向けた情報を配信しております。
新任の方やベテランの方、管理職を対象とした幅広いコンテンツをご用意しております。
お問い合わせ
コストダウンが利益に直結する術だと理解していても、なかなか前に進めることができない状況。そんな時は、newjiのコストダウン自動化機能で大きく利益貢献しよう!
(Β版非公開)