- お役立ち記事
- Centerless Grinding Machine Technology and Its Application in Manufacturing
Centerless Grinding Machine Technology and Its Application in Manufacturing
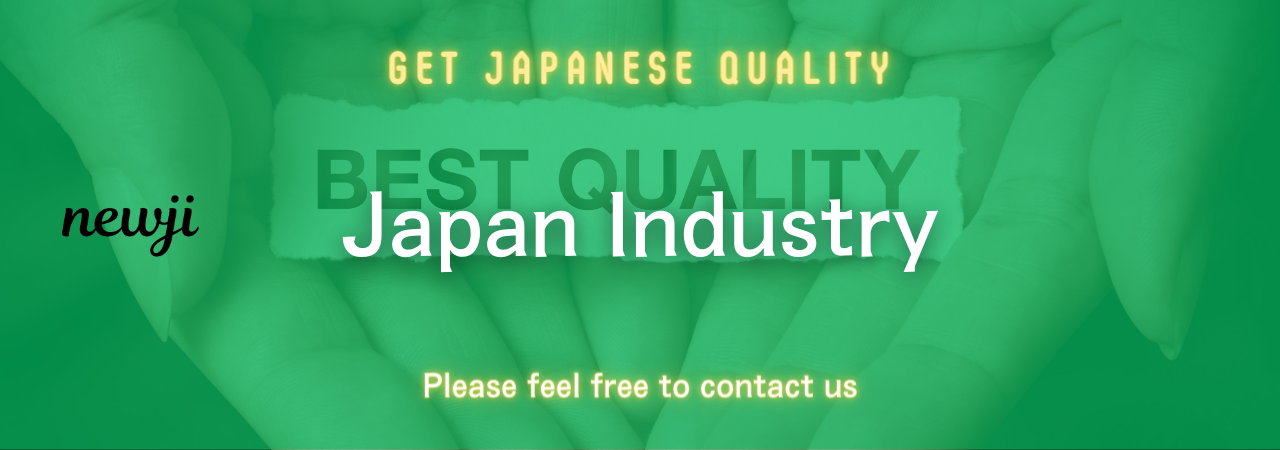
目次
Understanding Centerless Grinding Machine Technology
Centerless grinding is a unique machining process that removes material from the outside of a cylindrical workpiece without the need to grip or hold the workpiece in place.
This method is different from traditional grinding processes because it relies on the workpiece being supported between two rotating wheels.
One wheel is a grinding wheel, while the other is a regulating wheel that controls the rotational speed and keeps the workpiece steady.
How Centerless Grinding Works
The magic of centerless grinding lies in its three main components: the grinding wheel, the regulating wheel, and the work rest blade.
The grinding wheel is responsible for cutting and shaping the workpiece.
It rotates at high speeds, driven by a motor, and its abrasive surface removes material from the workpiece.
The regulating wheel, on the other hand, turns more slowly and is often made of softer material.
It ensures the workpiece rotates at a consistent speed, and it keeps the material from moving around haphazardly.
The work rest blade supports the workpiece at the correct height, making sure it stays between the grinding and regulating wheels.
Types of Centerless Grinding
There are several types of centerless grinding.
Understanding the different methods can help you choose the right one for your project.
Through-Feed Grinding
Through-feed grinding is the simplest and most common form of centerless grinding.
In this method, the workpiece is fed into the machine on one side and moves out the other.
It’s ideal for manufacturing large quantities of straight, cylindrical parts and is often used in automotive and furniture industries.
In-Feed Grinding
In-feed grinding, also known as plunge grinding, is useful when you need to grind a specific section of a workpiece.
Unlike through-feed grinding, the workpiece does not move during the grinding process.
Instead, it is placed in a fixed position, and the grinding wheel moves toward the workpiece.
This method is perfect for parts with complex shapes, as well as those with multiple diameters that need precision machining.
End-Feed Grinding
End-feed grinding is similar to in-feed grinding, but it is used to grind workpieces that have a taper or conical shape.
The workpiece is fed into the machine from one end, grinds the desired shape, and exits from the same end.
This type of grinding is ideal for producing precision automotive components and hydraulic lifters.
Advantages of Centerless Grinding
There are several advantages that make centerless grinding an appealing option for manufacturers.
High Production Efficiency
Centerless grinding is a highly efficient process.
Because there is no need for workpiece clamping, the setup time is reduced, and multiple workpieces can be processed simultaneously.
This leads to higher production rates and lower costs.
Precision and Consistency
Centerless grinding ensures a high level of precision and consistency across all workpieces.
The consistent pressure and support provided by the regulating wheel and work rest blade mean that each piece produced has the same dimensions and quality.
This consistency is crucial in industries where precision is key.
Versatility
Centerless grinding is a versatile process that can handle a variety of materials, including metals, plastics, and glass.
It can also produce complex shapes and designs, thanks to the various types of centerless grinding methods available.
Applications of Centerless Grinding in Manufacturing
Centerless grinding is widely used in various industries due to its many benefits.
Some common applications include:
Automotive Industry
In the automotive industry, centerless grinding is used to manufacture parts such as steering rods, crankshafts, and camshafts.
These components need to meet high standards of precision and durability, making centerless grinding the ideal process.
Medical Equipment
Medical equipment, such as surgical tools and prosthetics, requires precise manufacturing to ensure the safety and effectiveness of medical procedures.
Centerless grinding provides the high level of precision needed to produce these critical components.
Aerospace Industry
In the aerospace industry, components such as turbine blades and landing gear parts must withstand extreme conditions and stresses.
Centerless grinding is used to achieve the precision and consistency required to produce these high-performance parts.
Consumer Goods
Centerless grinding is also used to produce everyday consumer goods like appliances and furniture.
It helps create smooth, cylindrical components that are both functional and aesthetically pleasing.
Conclusion
Centerless grinding technology is an essential part of modern manufacturing.
Its ability to produce high-quality, precise, and consistent components makes it suitable for a wide range of industries.
Whether you’re producing automotive parts, medical equipment, or consumer goods, centerless grinding offers a versatile and efficient solution. As technology advances, we can expect centerless grinding to continue to evolve, further enhancing its capabilities and applications in manufacturing.
資料ダウンロード
QCD調達購買管理クラウド「newji」は、調達購買部門で必要なQCD管理全てを備えた、現場特化型兼クラウド型の今世紀最高の購買管理システムとなります。
ユーザー登録
調達購買業務の効率化だけでなく、システムを導入することで、コスト削減や製品・資材のステータス可視化のほか、属人化していた購買情報の共有化による内部不正防止や統制にも役立ちます。
NEWJI DX
製造業に特化したデジタルトランスフォーメーション(DX)の実現を目指す請負開発型のコンサルティングサービスです。AI、iPaaS、および先端の技術を駆使して、製造プロセスの効率化、業務効率化、チームワーク強化、コスト削減、品質向上を実現します。このサービスは、製造業の課題を深く理解し、それに対する最適なデジタルソリューションを提供することで、企業が持続的な成長とイノベーションを達成できるようサポートします。
オンライン講座
製造業、主に購買・調達部門にお勤めの方々に向けた情報を配信しております。
新任の方やベテランの方、管理職を対象とした幅広いコンテンツをご用意しております。
お問い合わせ
コストダウンが利益に直結する術だと理解していても、なかなか前に進めることができない状況。そんな時は、newjiのコストダウン自動化機能で大きく利益貢献しよう!
(Β版非公開)