- お役立ち記事
- Centrifuge Manufacturing Process and Rotary Speed Control Technology
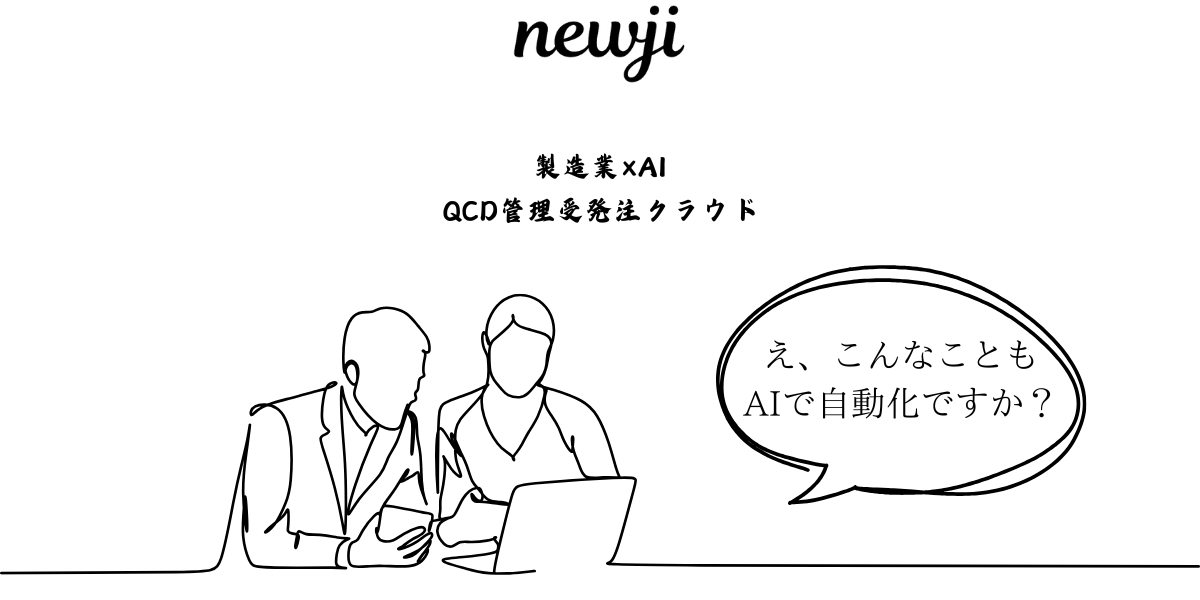
Centrifuge Manufacturing Process and Rotary Speed Control Technology
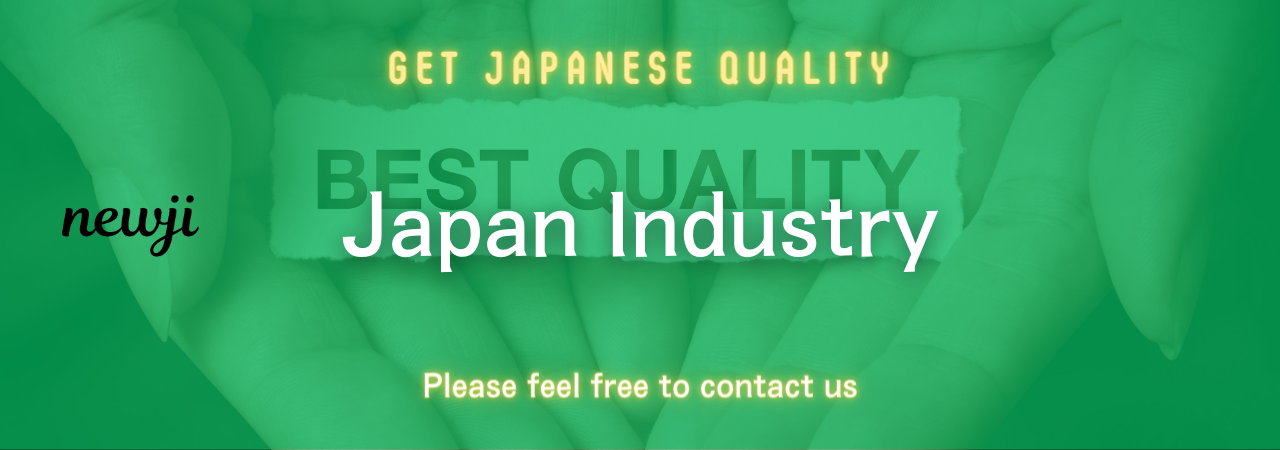
Centrifuges are essential machines used across various industries, from medical labs to food production.
They work by spinning containers filled with substances at high speeds, causing materials of different densities to separate due to centripetal force.
Understanding the centrifuge manufacturing process and rotary speed control technology is crucial, given the critical roles these devices play in daily operations.
目次
Understanding the Basics of Centrifuges
A centrifuge is a machine that uses centrifugal force to separate components in a mixture.
By spinning at high rotational speeds, the centrifuge forces heavier substances to move outward and lighter substances to remain closer to the center.
This principle is widely applied in scientific research, clinical laboratories, and various industrial processes.
Types of Centrifuges
Several types of centrifuges exist, each designed for specific applications.
These include:
– **Laboratory Centrifuges:** Common in medical and research laboratories for tasks such as blood separation and DNA analysis.
– **Industrial Centrifuges:** Used in wastewater treatment, food production, and chemical processing.
– **Microcentrifuges:** Small devices used for small sample volumes often found in biology and chemistry labs.
The Manufacturing Process of Centrifuges
Manufacturing a centrifuge involves several detailed steps, from initial design to the final assembly.
Here’s a breakdown of the entire process:
Design Phase
The first step in manufacturing a centrifuge is the design phase.
Engineers consider various factors such as the intended application, desired capacity, material compatibility, and safety requirements.
Computer-aided design (CAD) software is often used to create detailed drawings and models.
These blueprints guide the subsequent stages of manufacturing.
Material Selection
Choosing the right materials is crucial for the performance and durability of the centrifuge.
Components must withstand high rotational speeds, chemical exposure, and physical stress.
Common materials used include stainless steel, aluminum, and specific polymers designed for strength and resistance to corrosion.
Each material is selected based on the centrifuge’s intended use.
Component Manufacturing
Once the design and materials are finalized, individual components are manufactured.
This stage includes machining metal parts, molding plastic components, and fabricating electronic circuits.
High precision is essential to ensure smooth operation and longevity of the machine.
Assembly and Testing
Next, all the components are assembled into the final product.
Highly skilled technicians follow detailed instructions to fit parts together accurately.
After assembly, each centrifuge undergoes rigorous testing.
Tests check for balance, rotational stability, speed accuracy, and safety features.
Rotary Speed Control Technology
Controlling the rotary speed of a centrifuge is vital for achieving accurate and consistent results.
Modern centrifuges employ advanced speed control technologies to maintain precision.
Electronic Speed Controllers
Most modern centrifuges use electronic speed controllers to regulate the motor’s speed.
These controllers use sensors to monitor the current speed and adjust it in real time to ensure consistent performance.
In some models, microprocessors help achieve even more accurate speed control by continuously analyzing data and making necessary adjustments.
Feedback Systems
Feedback systems play an essential role in maintaining optimal rotary speed.
These systems include encoders and tachometers that provide real-time feedback on the spinning rotor’s speed.
This information allows the electronic controller to make quick adjustments, keeping the speed within the desired range.
Programmable Speed Settings
Many centrifuges offer programmable speed settings, giving users the flexibility to set specific speeds for different applications.
This feature is particularly useful in laboratories, where protocols often require precise speeds for different procedures.
Safety Considerations
Given the high rotational speeds involved, safety is a top priority in centrifuge manufacturing and operation.
Designers incorporate several safety features to protect users and ensure the machine operates correctly.
Automatic Shutoff Mechanisms
Modern centrifuges are equipped with automatic shutoff mechanisms.
These systems detect imbalances or mechanical issues and shut down the machine to prevent damage and ensure operator safety.
Secure Lid Locks
To prevent accidents, centrifuges feature secure lid locks.
These locks ensure the lid remains closed while the rotor is spinning, preventing materials from being ejected.
Vibration Damping
Excessive vibration can lead to machine damage and inaccurate results.
Therefore, modern centrifuges include vibration damping systems.
These systems help absorb and mitigate vibrations, ensuring smooth operation.
Maintenance and Care
Maintaining a centrifuge properly is crucial for its longevity and reliable performance.
Regular maintenance and care can prevent unexpected failures and extend the machine’s lifespan.
Routine Inspections
Regular inspections are essential to identify any wear and tear on machine components.
Technicians should check for signs of imbalance, unusual noises, or visible damage and address issues promptly.
Cleaning Procedures
Cleaning is vital to avoid contamination and ensure accurate results, especially in laboratory settings.
Cleaning protocols vary based on the materials and substances involved, but generally include wiping down surfaces and sterilizing removable parts.
Calibration and Servicing
Periodic calibration and servicing by the manufacturer or an authorized service provider ensure the centrifuge operates within specified parameters.
Service includes checking the electronic controls, feedback systems, and mechanical parts for proper function.
Understanding the centrifuge manufacturing process and rotary speed control technology gives insight into these machines’ complexity and precision.
From design to routine maintenance, each step plays a crucial role in delivering reliable and safe centrifuge operations essential in numerous fields.
資料ダウンロード
QCD調達購買管理クラウド「newji」は、調達購買部門で必要なQCD管理全てを備えた、現場特化型兼クラウド型の今世紀最高の購買管理システムとなります。
ユーザー登録
調達購買業務の効率化だけでなく、システムを導入することで、コスト削減や製品・資材のステータス可視化のほか、属人化していた購買情報の共有化による内部不正防止や統制にも役立ちます。
NEWJI DX
製造業に特化したデジタルトランスフォーメーション(DX)の実現を目指す請負開発型のコンサルティングサービスです。AI、iPaaS、および先端の技術を駆使して、製造プロセスの効率化、業務効率化、チームワーク強化、コスト削減、品質向上を実現します。このサービスは、製造業の課題を深く理解し、それに対する最適なデジタルソリューションを提供することで、企業が持続的な成長とイノベーションを達成できるようサポートします。
オンライン講座
製造業、主に購買・調達部門にお勤めの方々に向けた情報を配信しております。
新任の方やベテランの方、管理職を対象とした幅広いコンテンツをご用意しております。
お問い合わせ
コストダウンが利益に直結する術だと理解していても、なかなか前に進めることができない状況。そんな時は、newjiのコストダウン自動化機能で大きく利益貢献しよう!
(Β版非公開)