- お役立ち記事
- Ceramic Component OEM for High-Performance Parts
Ceramic Component OEM for High-Performance Parts
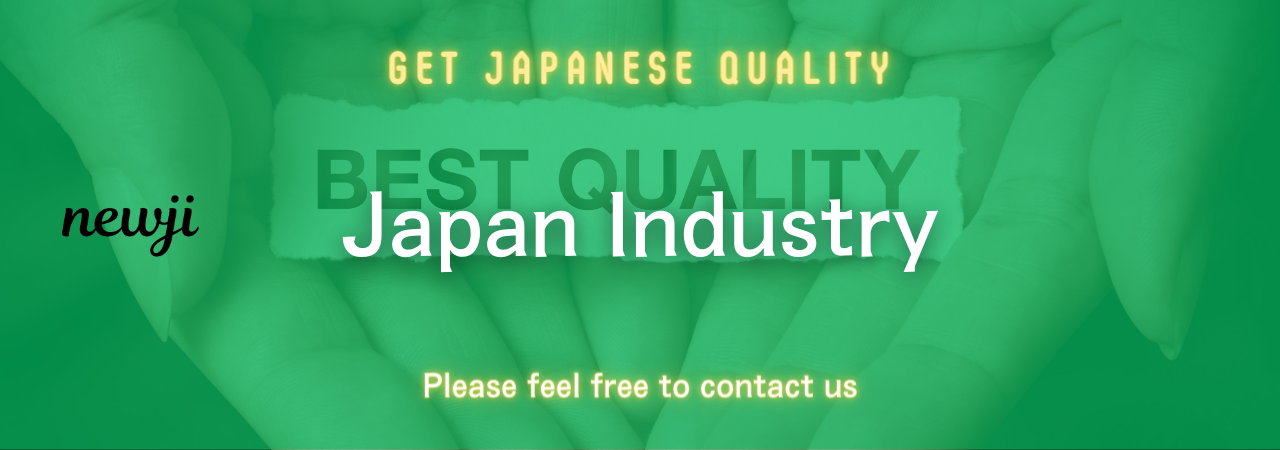
目次
Understanding Ceramic Components
Ceramic components play a crucial role in the world of high-performance parts.
These advanced materials are known for their impressive mechanical, thermal, and electrical properties.
Ceramic materials are non-metallic, inorganic solids that are typically composed of metal or non-metal compounds.
These components are highly sought after due to their ability to withstand extreme temperatures, resist wear and corrosion, and maintain stability under electrical and mechanical stress.
Ceramic components can be found in a variety of applications, from aerospace engineering and electronics to medical devices and automotive parts.
Their versatility makes them ideal for OEM (Original Equipment Manufacturer) partnerships, where precision and quality are paramount.
When it comes to creating high-performance parts, working with a ceramic component OEM ensures that the components meet the required specifications and standards.
Why Choose Ceramic Components?
There are several advantages to using ceramic components in high-performance applications.
One of the primary benefits is their excellent durability.
Ceramics can maintain their integrity under extreme conditions, such as high temperatures or corrosive environments.
This makes them perfect for applications where traditional materials, such as metal or plastic, would fail.
Another advantage of ceramic components is their electrical insulation properties.
Ceramic materials are excellent insulators, which makes them ideal for use in electronics and electrical engineering.
These properties help to prevent energy loss and improve the efficiency of electronic devices.
Additionally, ceramic components are lightweight, which is an essential consideration for many high-tech applications.
This makes them a popular choice in the aerospace and automotive industries, where reducing weight can lead to significant improvements in fuel efficiency and performance.
The OEM Process for Ceramic Components
Partnering with an OEM for ceramic components involves a systematic process that ensures the production of high-quality, customized parts.
This process begins with a thorough understanding of the specific requirements and application constraints of the client’s project.
Design and Prototyping
The initial stage of the OEM process involves detailed design and prototyping.
Engineers work closely with the client to develop an accurate design based on the part’s intended application.
The design phase may include computer-aided design (CAD) software to create precise models of the ceramic components.
Once the design is finalized, a prototype is created to test the component’s performance and ensure it meets the required specifications.
Prototyping helps identify any potential issues early in the process, allowing for adjustments before full-scale production begins.
Material Selection and Production
After the prototyping phase, the next step is selecting the appropriate ceramic material for the component.
The choice of material depends on various factors, including the application environment, mechanical and thermal requirements, and budget constraints.
Common ceramic materials used in OEM processes include alumina, zirconia, silicon carbide, and silicon nitride.
Once the material is selected, the production process can commence.
Ceramic components are typically manufactured using methods such as pressing, extrusion, or injection molding.
Each method offers different advantages, depending on the complexity and size of the component.
Quality Control and Testing
Quality control is a critical aspect of the OEM process for ceramic components.
Rigorous testing ensures that each part meets the high standards required for high-performance applications.
This may involve non-destructive testing methods, such as X-ray and ultrasonic testing, to identify any defects or inconsistencies in the material.
Additionally, mechanical tests are conducted to evaluate properties like hardness, strength, and wear resistance.
Thermal testing ensures that the components can withstand varying temperature conditions without degradation.
Applications of Ceramic Component OEM
Ceramic component OEMs cater to a diverse range of industries and applications, each with unique performance requirements.
Aerospace and Defense
In the aerospace and defense sectors, ceramic components are used in applications such as turbine engines, thermal barriers, and radomes.
Their high-temperature resistance and lightweight properties make them ideal for these demanding environments.
Electronics and Telecommunications
Ceramic components are essential in the electronics and telecommunications industries.
They are used in capacitors, insulators, and semiconductor substrates, offering excellent insulation properties and stability.
Medical Devices
In the medical field, ceramics play a vital role in the development of devices such as dental implants, prosthetics, and surgical instruments.
Their biocompatibility, strength, and wear resistance make them suitable for applications in the human body.
Conclusion
Ceramic component OEMs are essential partners in the creation of high-performance parts across various industries.
Their expertise in design, material selection, production, and quality control ensures that the components meet stringent performance standards.
By choosing ceramic components, manufacturers can enhance the durability, efficiency, and overall performance of their products, making them a valuable investment for future innovations.
資料ダウンロード
QCD調達購買管理クラウド「newji」は、調達購買部門で必要なQCD管理全てを備えた、現場特化型兼クラウド型の今世紀最高の購買管理システムとなります。
ユーザー登録
調達購買業務の効率化だけでなく、システムを導入することで、コスト削減や製品・資材のステータス可視化のほか、属人化していた購買情報の共有化による内部不正防止や統制にも役立ちます。
NEWJI DX
製造業に特化したデジタルトランスフォーメーション(DX)の実現を目指す請負開発型のコンサルティングサービスです。AI、iPaaS、および先端の技術を駆使して、製造プロセスの効率化、業務効率化、チームワーク強化、コスト削減、品質向上を実現します。このサービスは、製造業の課題を深く理解し、それに対する最適なデジタルソリューションを提供することで、企業が持続的な成長とイノベーションを達成できるようサポートします。
オンライン講座
製造業、主に購買・調達部門にお勤めの方々に向けた情報を配信しております。
新任の方やベテランの方、管理職を対象とした幅広いコンテンツをご用意しております。
お問い合わせ
コストダウンが利益に直結する術だと理解していても、なかなか前に進めることができない状況。そんな時は、newjiのコストダウン自動化機能で大きく利益貢献しよう!
(Β版非公開)