- お役立ち記事
- Ceramic Forming and Processing Technology and Its Application in Manufacturing
Ceramic Forming and Processing Technology and Its Application in Manufacturing
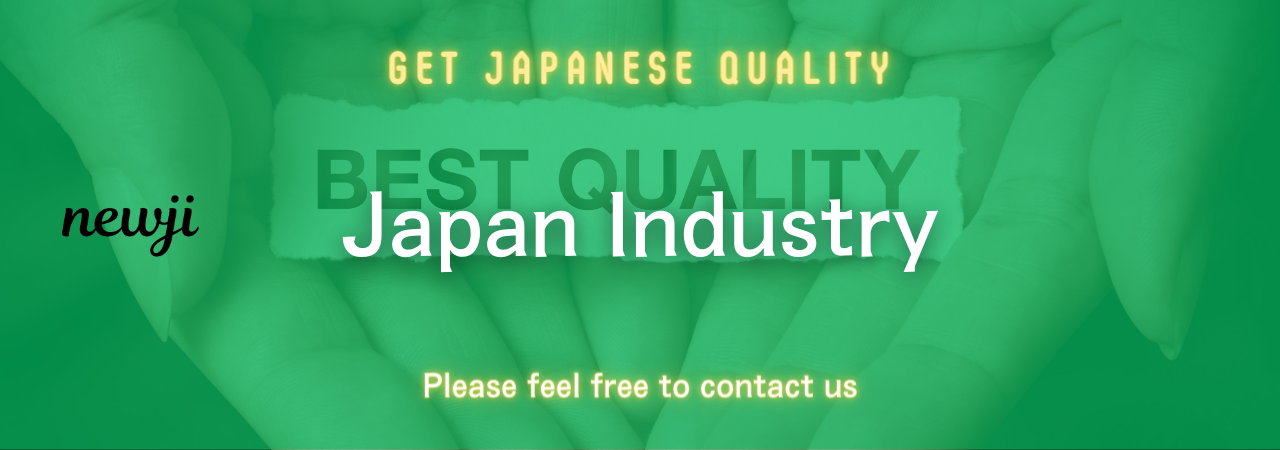
目次
Introduction to Ceramic Forming and Processing Technology
Ceramics play a crucial role in various sectors due to their unique properties such as high hardness, heat resistance, and chemical stability.
Ceramic forming and processing technology involves a series of methods and techniques used to shape and treat ceramic materials into desired forms and functions.
In this article, we’ll explore the key aspects of ceramic forming and processing technology and its applications across different industries.
Understanding Ceramic Materials
Ceramics are composed of inorganic, non-metallic materials that are typically crystalline in nature.
They are created through heating and subsequent cooling processes.
The primary components of ceramics include clay, clay minerals, and other naturally occurring raw materials.
Modern ceramics may also incorporate advanced compounds like carbides and nitrides for enhanced properties.
Types of Ceramics
There are two main categories of ceramics: traditional ceramics and advanced ceramics.
Traditional ceramics include items like bricks, pottery, china, and porcelain.
These are often made from natural clay and have been used for thousands of years.
Advanced ceramics, on the other hand, are produced using synthetic raw materials and are engineered for specific industrial applications.
Examples include alumina, silicon carbide, and zirconia.
Key Ceramic Forming Techniques
Ceramic forming techniques are the methods used to shape ceramic powders into desired shapes before they undergo firing.
Slip Casting
Slip casting involves pouring a liquid clay, known as slip, into a plaster mold.
The plaster absorbs water from the slip, leaving a layer of clay on the mold’s inner surface.
Once the desired thickness is achieved, the excess slip is poured out, and the formed piece is allowed to dry before firing.
Injection Molding
Injection molding of ceramics is similar to plastic injection molding.
It involves forcing a mixture of ceramic powder and a thermoplastic binder into a mold under high pressure.
Once the binder solidifies, the “green” part is removed and undergoes further processing like debinding and sintering.
Pressing
Pressing is a technique where ceramic powder is compacted into a desired shape using pressure.
There are two main types: uniaxial pressing, where the powder is compacted in one direction, and isostatic pressing, where the powder is compacted uniformly from all directions.
This method is ideal for producing high-density, uniform parts.
Extrusion
In the extrusion technique, a plasticized ceramic mass is forced through a die to create long shapes with uniform cross-sections.
The extruded pieces are cut to length and dried before firing.
This method is commonly used for making pipes, tiles, and structural ceramics.
Processing Techniques for Ceramics
After forming, ceramics undergo several processing steps to achieve their final properties.
Drying
Drying is a crucial step to remove water or other solvents from the ceramic body before firing.
Slow and controlled drying is essential to prevent cracking and warping of the piece.
Drying methods vary depending on the size and complexity of the item, ranging from air drying to controlled humidity environments.
Firing
Firing is the process where the ceramic pieces are heated at high temperatures to induce chemical and physical changes.
This step involves two stages: bisque firing and glaze firing.
Bisque firing removes any remaining water and organic materials, while glaze firing adds a glassy coating for aesthetics and functionality.
The temperature and duration of firing depend on the type of ceramic material and desired properties.
Glazing
Glazing involves applying a vitreous layer over the ceramic surface to enhance its appearance and properties.
Glazes can add color, waterproof the item, and provide a smooth surface.
They are mostly applied through dipping, spraying, or brushing.
Finishing
Finishing processes are applied to improve the final product.
These include grinding, polishing, and cutting to achieve precise dimensions and surface finishes.
Advanced finishing may involve laser machining for high-precision applications.
Applications of Ceramic Technology in Manufacturing
Ceramic forming and processing technology has widespread applications due to the exceptional properties of ceramics.
Electronics and Semiconductors
In the electronics and semiconductor industry, advanced ceramics are vital for their electrical insulation, thermal conductivity, and stability.
They are used to manufacture substrates, insulators, and semiconductors in devices like capacitors, resistors, and microchips.
Automotive Industry
The automotive industry uses ceramics in various components for their high temperature and wear resistance.
Applications include engine parts, brake pads, and catalytic converters.
Ceramics contribute to enhanced performance, fuel efficiency, and durability.
Medical Devices
Ceramics play a significant role in medical devices due to their biocompatibility and inert nature.
They are used in dental implants, bone replacement materials, and medical prosthetics.
Ceramic materials help improve the longevity and reliability of medical devices.
Construction and Architecture
Traditional and advanced ceramics are extensively used in construction and architecture.
Ceramic tiles, bricks, and sanitary ware are common applications.
Advanced structural ceramics contribute to modern architectural designs with their strength and durability.
Future Trends in Ceramic Technology
The ceramic industry continues to evolve with advancements in materials and processing techniques.
Research focuses on enhancing ceramics’ mechanical properties, developing new composites, and innovating sustainable manufacturing processes.
3D Printing
3D printing is revolutionizing ceramic manufacturing with the ability to create complex geometries and customized parts.
Advances in 3D printing technologies are enabling more efficient, precise, and cost-effective production of ceramic components.
Nanotechnology
Nanotechnology is enhancing the properties of ceramics at the molecular level.
Nano-ceramics exhibit superior mechanical, thermal, and electrical properties.
Applications include high-performance coatings, sensors, and electronics.
Environmentally Friendly Processes
The push for sustainability is driving the development of eco-friendly ceramic manufacturing processes.
Efforts include reducing energy consumption, recycling waste materials, and using renewable resources.
Conclusion
Ceramic forming and processing technology is integral to manufacturing across various industries.
The advanced properties of ceramics make them indispensable for applications ranging from electronics to medical devices.
Continuous advancements and innovations will likely expand the capabilities and applications of ceramic materials in the future.
資料ダウンロード
QCD調達購買管理クラウド「newji」は、調達購買部門で必要なQCD管理全てを備えた、現場特化型兼クラウド型の今世紀最高の購買管理システムとなります。
ユーザー登録
調達購買業務の効率化だけでなく、システムを導入することで、コスト削減や製品・資材のステータス可視化のほか、属人化していた購買情報の共有化による内部不正防止や統制にも役立ちます。
NEWJI DX
製造業に特化したデジタルトランスフォーメーション(DX)の実現を目指す請負開発型のコンサルティングサービスです。AI、iPaaS、および先端の技術を駆使して、製造プロセスの効率化、業務効率化、チームワーク強化、コスト削減、品質向上を実現します。このサービスは、製造業の課題を深く理解し、それに対する最適なデジタルソリューションを提供することで、企業が持続的な成長とイノベーションを達成できるようサポートします。
オンライン講座
製造業、主に購買・調達部門にお勤めの方々に向けた情報を配信しております。
新任の方やベテランの方、管理職を対象とした幅広いコンテンツをご用意しております。
お問い合わせ
コストダウンが利益に直結する術だと理解していても、なかなか前に進めることができない状況。そんな時は、newjiのコストダウン自動化機能で大きく利益貢献しよう!
(Β版非公開)