- お役立ち記事
- Ceramic Injection Molding Technology and Its Application in Manufacturing
Ceramic Injection Molding Technology and Its Application in Manufacturing
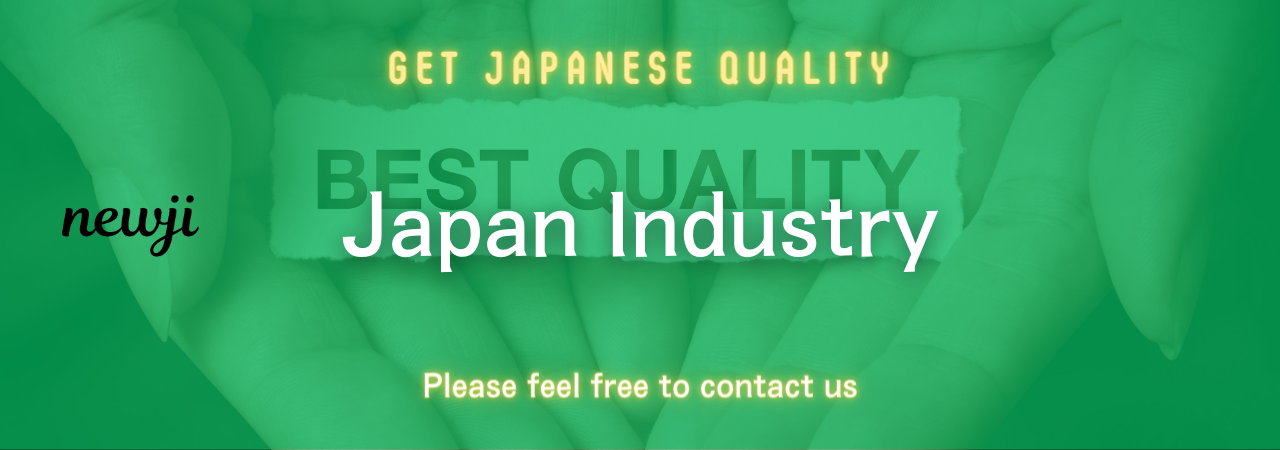
Ceramic Injection Molding (CIM) is a pioneering technology making waves in modern manufacturing. This sophisticated method enables the production of intricate ceramic components with remarkable precision. As industries continually demand high-performance materials, CIM has proven to be a game-changer by offering a blend of flexibility, efficiency, and quality.
目次
What is Ceramic Injection Molding?
Ceramic Injection Molding is a specialized process that combines ceramic powders with thermoplastic binders to form a homogeneous mixture. This mixture is then injected into molds to create complex shapes.
After molding, the parts go through debinding to remove the binder material, followed by sintering, which solidifies the ceramic by heating it to a high temperature. During sintering, the ceramic particles fuse together, resulting in a dense and robust final product.
The CIM Process: Step-by-Step
Step 1: Material Preparation
The first step in CIM involves mixing fine ceramic powders with a thermoplastic binder system. The binder helps to give the ceramic mixture the necessary plasticity for molding. Various binders are used depending on the specific application and desired properties of the ceramic.
Step 2: Injection Molding
Once the material is mixed, it is loaded into an injection molding machine. Here, the ceramic-binder mixture is heated and injected into a metal mold at high pressure. This process allows for the creation of complex geometries and fine details that are challenging to achieve with traditional ceramic forming techniques.
Step 3: Debinding
After the part is molded, the next step is debinding. This step removes the majority of the binder material from the green (unfired) ceramic part. There are various debinding methods, including solvent extraction and thermal debinding, depending on the binder system used.
Step 4: Sintering
The final step is sintering. During sintering, the debound ceramic part is heated to temperatures high enough to cause the ceramic particles to bond together, eliminating pores and increasing the density. The part shrinks during this process, which must be carefully controlled to ensure dimensional accuracy.
Advantages of Ceramic Injection Molding
Complex Geometries
One of the most significant advantages of CIM is its ability to create complex geometries that are nearly impossible to achieve with traditional manufacturing methods. Thin walls, intricate internal features, and fine details are all possible with CIM.
High Precision and Consistency
CIM allows for high precision and consistency in manufacturing. The repeatability of the process means that each component produced is nearly identical, reducing variability and ensuring quality.
Material Versatility
CIM can be used with a wide range of ceramic materials, including alumina, zirconia, and silicon nitride. Each material offers unique properties, making CIM suitable for various applications, from structural components to electronic devices.
Cost Efficiency
While the initial setup for CIM can be costly, the process becomes highly cost-effective for large production runs. The ability to produce large quantities of complex parts quickly reduces labor and machining costs.
Applications of Ceramic Injection Molding
Medical Devices
CIM technology is extensively used in the medical industry to produce components like surgical tools, dental implants, and prosthetics. The biocompatibility and strength of ceramics make them ideal for medical applications where precision and reliability are critical.
Electronics
In the electronics sector, CIM is used to manufacture components such as insulators, substrates, and connectors. The excellent electrical insulation properties and thermal stability of ceramics make them invaluable in electronic devices.
Aerospace
The aerospace industry benefits from the high strength-to-weight ratio of ceramic materials produced through CIM. Components like turbine blades, heat shields, and engine parts are manufactured using CIM to withstand extreme temperatures and stress.
Automotive
In the automotive industry, CIM is employed to produce parts like fuel injectors, pump seals, and sensor components. The wear resistance and durability of ceramics make them suitable for challenging environments found in automotive systems.
Industrial Machinery
CIM is also used in manufacturing industrial machinery components that require high wear resistance, such as cutting tools, nozzles, and valve components. Ceramics’ hardness and ability to maintain integrity under harsh conditions enhance the performance and longevity of these parts.
Future Prospects of Ceramic Injection Molding
Ceramic Injection Molding is set to play an increasingly pivotal role in manufacturing due to ongoing advancements in materials science and process technology. Researchers are continuously exploring new ceramic materials with enhanced properties, broadening the scope of CIM applications.
Emerging technologies, such as hybrid injection molding, combine CIM with metal injection molding (MIM) to produce parts composed of both ceramic and metal. This hybrid approach offers even greater design flexibility and functionality, paving the way for innovative solutions across industries.
Automation and AI are also expected to revolutionize the CIM process, further improving efficiency, reducing errors, and enabling real-time monitoring and control. The integration of smart manufacturing technologies will facilitate the adoption of CIM in more sectors, driving advancements in product performance and manufacturing capabilities.
Ceramic Injection Molding represents a cutting-edge manufacturing technology that delivers unparalleled precision, complexity, and material performance. Its versatile applications across medical, electronics, aerospace, automotive, and industrial sectors demonstrate its transformative impact.
As technology advances, CIM will continue to redefine manufacturing possibilities, offering innovative solutions to meet the ever-evolving demands of modern industries.
資料ダウンロード
QCD調達購買管理クラウド「newji」は、調達購買部門で必要なQCD管理全てを備えた、現場特化型兼クラウド型の今世紀最高の購買管理システムとなります。
ユーザー登録
調達購買業務の効率化だけでなく、システムを導入することで、コスト削減や製品・資材のステータス可視化のほか、属人化していた購買情報の共有化による内部不正防止や統制にも役立ちます。
NEWJI DX
製造業に特化したデジタルトランスフォーメーション(DX)の実現を目指す請負開発型のコンサルティングサービスです。AI、iPaaS、および先端の技術を駆使して、製造プロセスの効率化、業務効率化、チームワーク強化、コスト削減、品質向上を実現します。このサービスは、製造業の課題を深く理解し、それに対する最適なデジタルソリューションを提供することで、企業が持続的な成長とイノベーションを達成できるようサポートします。
オンライン講座
製造業、主に購買・調達部門にお勤めの方々に向けた情報を配信しております。
新任の方やベテランの方、管理職を対象とした幅広いコンテンツをご用意しております。
お問い合わせ
コストダウンが利益に直結する術だと理解していても、なかなか前に進めることができない状況。そんな時は、newjiのコストダウン自動化機能で大きく利益貢献しよう!
(Β版非公開)