- お役立ち記事
- Ceramic structural analysis and quality control method [Manufacturing industry]
月間76,176名の
製造業ご担当者様が閲覧しています*
*2025年3月31日現在のGoogle Analyticsのデータより
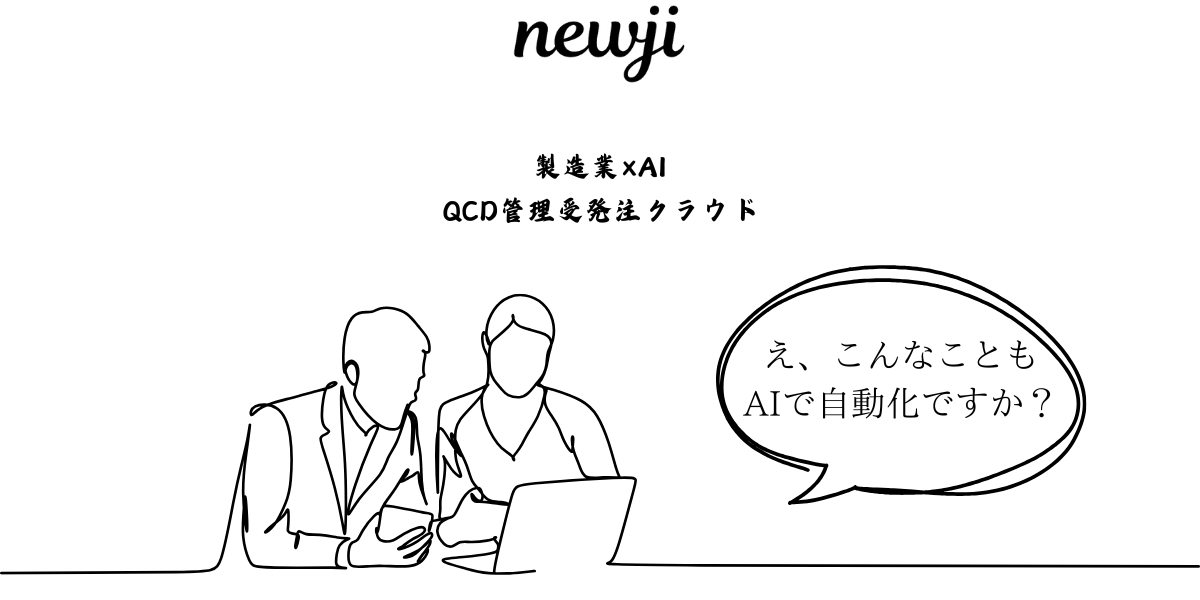
Ceramic structural analysis and quality control method [Manufacturing industry]
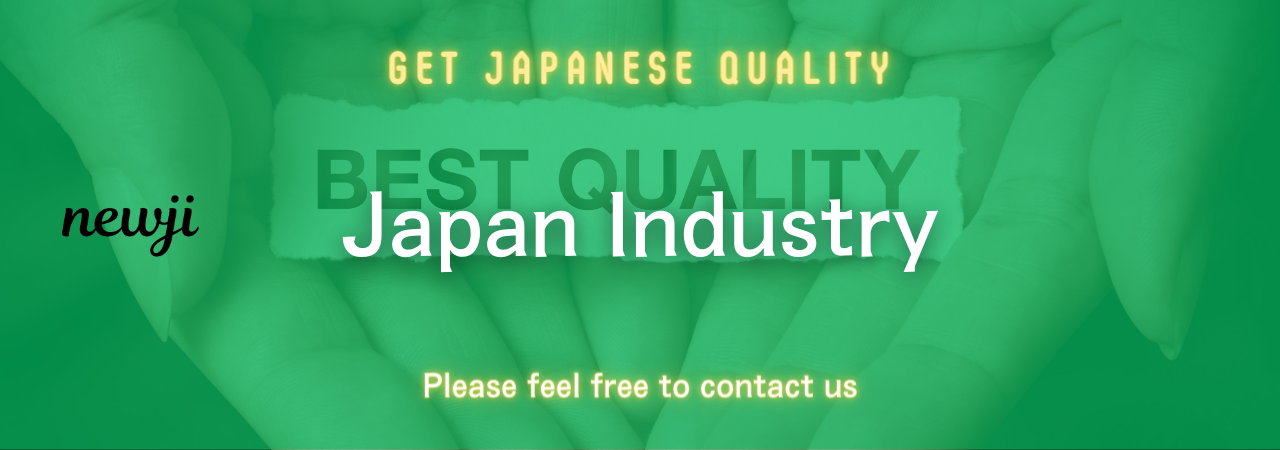
目次
Understanding Ceramic Structural Analysis
Ceramics play a crucial role in various industries due to their unique properties such as high resistance to heat, wear, and corrosion.
Understanding the structural characteristics of ceramics is essential for ensuring their durability and performance in different applications.
Ceramic structural analysis involves examining the microstructure and composition to evaluate quality and potential applications.
This analysis helps in identifying flaws, predicting life expectancy, and enhancing performance tailored to specific needs.
There are several methods used in ceramic structural analysis.
Some of these methods focus on the composition, while others examine mechanical properties or microstructural characteristics.
Among these techniques, X-ray diffraction (XRD) and scanning electron microscopy (SEM) are prominent tools used in this field.
XRD is particularly helpful in identifying the crystalline phases present in ceramics, while SEM provides detailed images of the surface and composition.
X-ray Diffraction in Ceramic Analysis
X-ray diffraction (XRD) is an essential technique for determining the crystalline structure of ceramics.
It involves directing X-rays at a ceramic sample and measuring the diffraction patterns produced.
These patterns offer insights into the material’s crystalline phases, possible stress, and any defects present.
XRD is highly effective in distinguishing between different polymorphs and assessing phase purity.
This is critical in applications where specific phases enhance material properties, such as in superconducting ceramics or heat-resistant tiles.
In addition to phase identification, XRD allows analysts to determine particle size, lattice parameters, and internal strains.
This information is crucial for optimizing processing techniques and tailoring material properties to specific applications.
The non-destructive nature of XRD makes it a preferred method for ongoing quality assessments and research.
Advancements in Scanning Electron Microscopy
Scanning Electron Microscopy (SEM) provides detailed, high-resolution images of the ceramic surfaces and their microstructure.
SEM uses electrons instead of photons, which allows for greater magnification and resolving power compared to traditional optical microscopes.
This makes SEM an invaluable tool for detailed surface examinations and microstructural analysis.
SEM can reveal surface defects such as cracks, pores, and inclusions that could compromise ceramic strength.
By identifying and understanding these imperfections, manufacturers can adjust processing techniques to minimize defects and ensure optimal performance.
Furthermore, SEM with energy-dispersive X-ray spectroscopy (EDS) helps in elemental analysis, offering insights into the sample’s chemical composition alongside its structural attributes.
Mechanical Testing for Structural Integrity
While XRD and SEM provide insights into the chemical and microstructural aspects of ceramics, mechanical testing is indispensable for assessing structural integrity.
Mechanical properties such as hardness, fracture toughness, and flexural strength determine how a ceramic will perform under stress conditions.
These tests simulate real-world applications, providing data on material behavior in different environmental conditions.
Tests such as Vickers or Knoop hardness testing measure a ceramic’s ability to resist indentation, while bending tests evaluate flexibility and tensile strength.
Fracture toughness tests, such as the Single Edge Notched Beam (SENB) method, reveal how much energy a ceramic can absorb before fracturing.
This parameter is especially important in applications exposed to sudden impacts or extreme conditions.
Quality Control in Ceramic Manufacturing
Quality control in ceramic manufacturing is vital to ensure that the final products meet specified standards and performance criteria.
Quality control processes involve regular inspections and tests conducted at various stages from raw material selection to final product assessment.
These processes are designed to detect and rectify flaws, ultimately enhancing reliability, safety, and customer satisfaction.
Raw Material Assessment
The quality of ceramics begins with the selection of raw materials.
Comprehensive testing ensures that inputs meet chemical and physical specifications which influence the manufacturing process and final product properties.
Raw materials are examined for impurities, particle size distribution, and moisture content.
Inconsistent quality in raw materials can lead to defects, resulting in decreased product performance and increased production costs.
Process Monitoring and Control
Process monitoring involves tracking critical parameters such as temperature, pressure, and processing time across different production stages.
Maintaining control over these parameters ensures repeatability and consistency in manufacturing, which directly affects the quality of the ceramics.
Statistical process control (SPC) methods are often employed to analyze data and keep processes within predefined limits.
This proactive approach can help identify trends, anticipate issues, and implement timely corrective measures.
Finished Product Inspection and Testing
Upon completion, ceramics are subjected to rigorous inspection and testing to verify compliance with specifications.
Non-destructive tests such as X-ray inspection and ultrasonic testing can detect internal flaws without damaging the product.
Destructive tests, though carried out on a sample basis, provide insights into strength and durability.
Visual inspections ensure that surface finishes and dimensions meet the aesthetic and functional requirements.
Performing thorough testing at the finished product stage helps manufacturers validate their processes, bolster quality assurance, and uphold customer trust.
Conclusion
Ceramic structural analysis and quality control are fundamental practices for the manufacturing industry.
These techniques provide insights into material characteristics, enabling manufacturers to enhance product performance and longevity.
Employing methods such as X-ray diffraction, scanning electron microscopy, and mechanical testing ensures comprehensive material understanding and superior product quality.
At the same time, robust quality control practices from raw material assessment to process monitoring and final inspection ensure that ceramics meet stringent industry standards.
By focusing on these essential aspects, manufacturers can maintain high-quality production that meets diverse market needs and withstands environmental challenges.
Ceramic structural analysis and quality control ultimately contribute to improved safety, reliability, and customer satisfaction in various applications.
資料ダウンロード
QCD管理受発注クラウド「newji」は、受発注部門で必要なQCD管理全てを備えた、現場特化型兼クラウド型の今世紀最高の受発注管理システムとなります。
ユーザー登録
受発注業務の効率化だけでなく、システムを導入することで、コスト削減や製品・資材のステータス可視化のほか、属人化していた受発注情報の共有化による内部不正防止や統制にも役立ちます。
NEWJI DX
製造業に特化したデジタルトランスフォーメーション(DX)の実現を目指す請負開発型のコンサルティングサービスです。AI、iPaaS、および先端の技術を駆使して、製造プロセスの効率化、業務効率化、チームワーク強化、コスト削減、品質向上を実現します。このサービスは、製造業の課題を深く理解し、それに対する最適なデジタルソリューションを提供することで、企業が持続的な成長とイノベーションを達成できるようサポートします。
製造業ニュース解説
製造業、主に購買・調達部門にお勤めの方々に向けた情報を配信しております。
新任の方やベテランの方、管理職を対象とした幅広いコンテンツをご用意しております。
お問い合わせ
コストダウンが利益に直結する術だと理解していても、なかなか前に進めることができない状況。そんな時は、newjiのコストダウン自動化機能で大きく利益貢献しよう!
(β版非公開)