- お役立ち記事
- Challenges and prospects of developing technology for mixing metals, organic metals, and resins in high-temperature inert gas atmospheres
月間76,176名の
製造業ご担当者様が閲覧しています*
*2025年3月31日現在のGoogle Analyticsのデータより
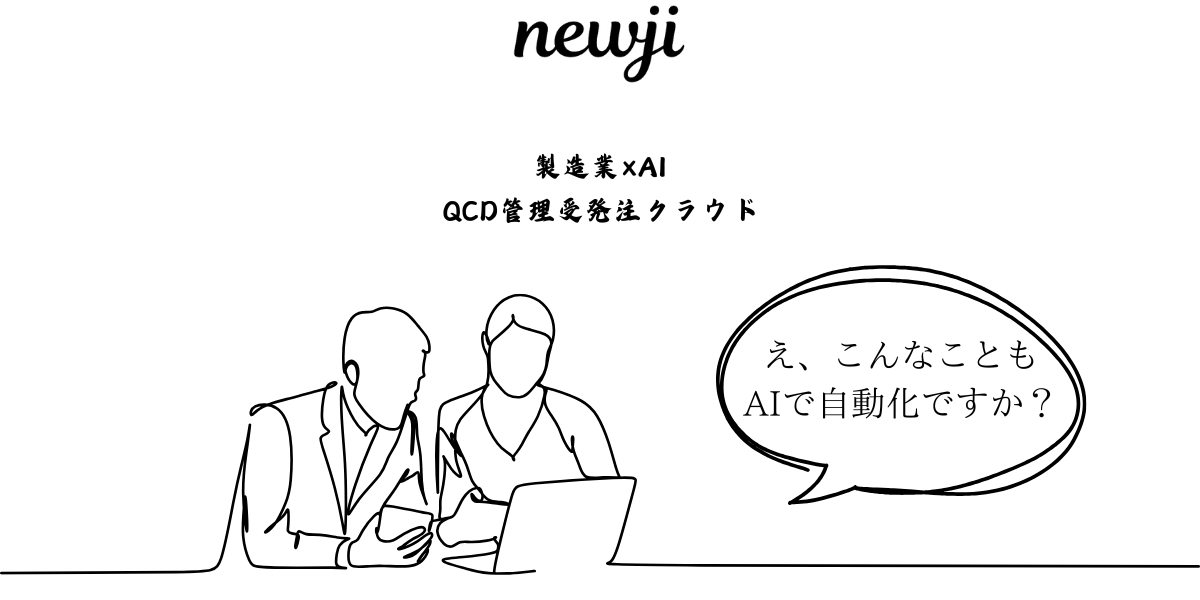
Challenges and prospects of developing technology for mixing metals, organic metals, and resins in high-temperature inert gas atmospheres
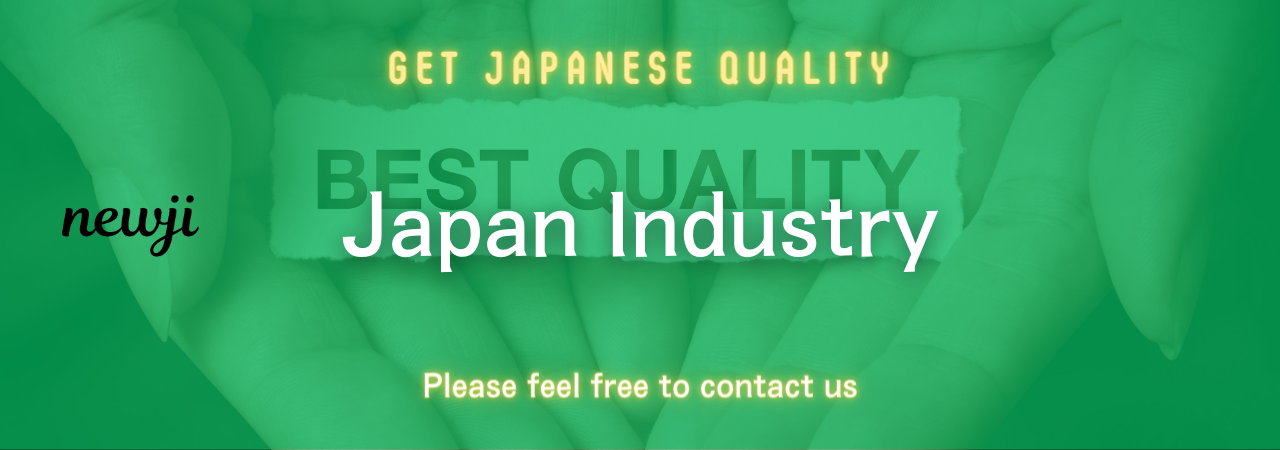
目次
Introduction
Developing technology for mixing metals, organic metals, and resins in high-temperature inert gas atmospheres is a complex and intriguing field.
This process requires an understanding of the properties of each component and the environment in which they are combined.
Such technology promises advancements in various industries, from automotive to electronics, by providing new materials with enhanced properties.
In this article, we will explore the challenges of this technology, the current progress, and the prospects it holds for the future.
Understanding the Components
Metals
Metals are materials known for their excellent conductivity, malleability, and durability.
When combined with other elements, metals can impart strength and electrical benefits to a composite material.
The challenge lies in selecting the right metal that will not react negatively with organic metals or resins during the mixing process.
Organic Metals
Organic metals, or conductive polymers, bridge the properties of metals and typical plastics.
They offer flexibility and can conduct electricity, providing unique opportunities for new material development.
One of the hurdles is ensuring that these organic metals maintain their conductive properties when mixed with metals and resins.
Resins
Resins, often used in plastics, add beneficial properties like being lightweight and corrosion-resistant.
Integrating resins with metals and organic metals can result in materials that are both lightweight and highly durable.
A challenge is to ensure the resins do not degrade under high temperatures used in mixing processes.
The Role of Inert Gas Atmospheres
Creating a high-temperature inert gas atmosphere is crucial in this mixing technology.
Inert gases, such as argon or nitrogen, provide a non-reactive environment that prevents undesirable reactions between the components.
The stable and controlled environment ensures the integrity of each material while they are combined.
However, there are challenges in maintaining stable high-temperature conditions within an inert gas atmosphere.
The equipment must withstand these conditions without failing.
Moreover, the choice of inert gas may influence the reaction outcomes, so selecting the appropriate gas is critical.
Challenges in Developing the Technology
Material Compatibility
One major challenge is ensuring the compatibility of the materials.
Metals, organic metals, and resins each have unique properties, and getting them to bond effectively without degrading each component’s properties is crucial.
Temperature Control
Managing high temperatures requires precision and control.
Not all materials react well at elevated temperatures, risking degradation or altered properties if the temperature is not strictly regulated.
Stability of the Inert Atmosphere
Maintaining a consistent inert gas atmosphere is another hurdle.
Fluctuations in the inert gas can lead to inconsistent reactions, affecting the quality and properties of the resulting material.
This requires advanced equipment and technology to control the environment precisely.
Current Progress in the Field
Research is ongoing to develop more efficient methods and equipment for this technology.
Recently, significant progress has been made in improving the understanding of how these materials interact at a molecular level.
Collaborations among industries and academic institutions have yielded new insights into mixing processes, leading to innovative solutions.
Advanced simulation technologies are also being used to predict the behavior of materials, helping scientists optimize the mixing process before actual trials.
Prospects for the Future
New Material Development
The potential for creating new materials is vast.
Mixing metals, organic metals, and resins could lead to breakthroughs in industries like aerospace, where materials need to be strong, lightweight, and heat-resistant.
Enhanced Product Performance
By combining these materials, products can achieve heightened performance properties.
For instance, electronics could benefit from more durable and conductive casings, while the automotive industry could see advancements in the creation of lighter, stronger car components.
Sustainability and Efficiency
This technology can contribute to sustainability by enabling materials that require less energy to produce and are more efficient in their applications.
Eco-friendly products can be developed by using materials that are less reliant on traditional manufacturing processes.
Conclusion
The development of technology to mix metals, organic metals, and resins in high-temperature inert gas atmospheres is a field rife with challenges yet filled with opportunities.
By overcoming obstacles like material compatibility and temperature control, scientists and engineers can pave the way for the creation of groundbreaking materials with enhanced properties.
As progress continues, the prospects for innovative solutions and sustainable applications grow, promising significant advancements across multiple industries.
資料ダウンロード
QCD管理受発注クラウド「newji」は、受発注部門で必要なQCD管理全てを備えた、現場特化型兼クラウド型の今世紀最高の受発注管理システムとなります。
ユーザー登録
受発注業務の効率化だけでなく、システムを導入することで、コスト削減や製品・資材のステータス可視化のほか、属人化していた受発注情報の共有化による内部不正防止や統制にも役立ちます。
NEWJI DX
製造業に特化したデジタルトランスフォーメーション(DX)の実現を目指す請負開発型のコンサルティングサービスです。AI、iPaaS、および先端の技術を駆使して、製造プロセスの効率化、業務効率化、チームワーク強化、コスト削減、品質向上を実現します。このサービスは、製造業の課題を深く理解し、それに対する最適なデジタルソリューションを提供することで、企業が持続的な成長とイノベーションを達成できるようサポートします。
製造業ニュース解説
製造業、主に購買・調達部門にお勤めの方々に向けた情報を配信しております。
新任の方やベテランの方、管理職を対象とした幅広いコンテンツをご用意しております。
お問い合わせ
コストダウンが利益に直結する術だと理解していても、なかなか前に進めることができない状況。そんな時は、newjiのコストダウン自動化機能で大きく利益貢献しよう!
(β版非公開)