- お役立ち記事
- Challenges and solutions for globalizing material procurement in the home appliance manufacturing industry
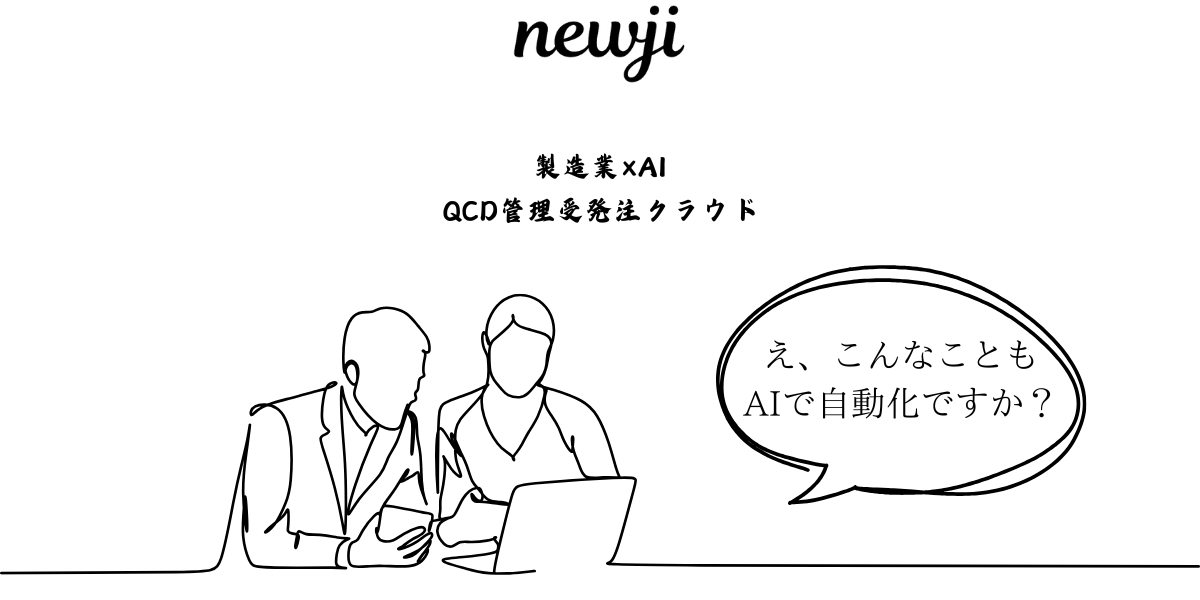
Challenges and solutions for globalizing material procurement in the home appliance manufacturing industry
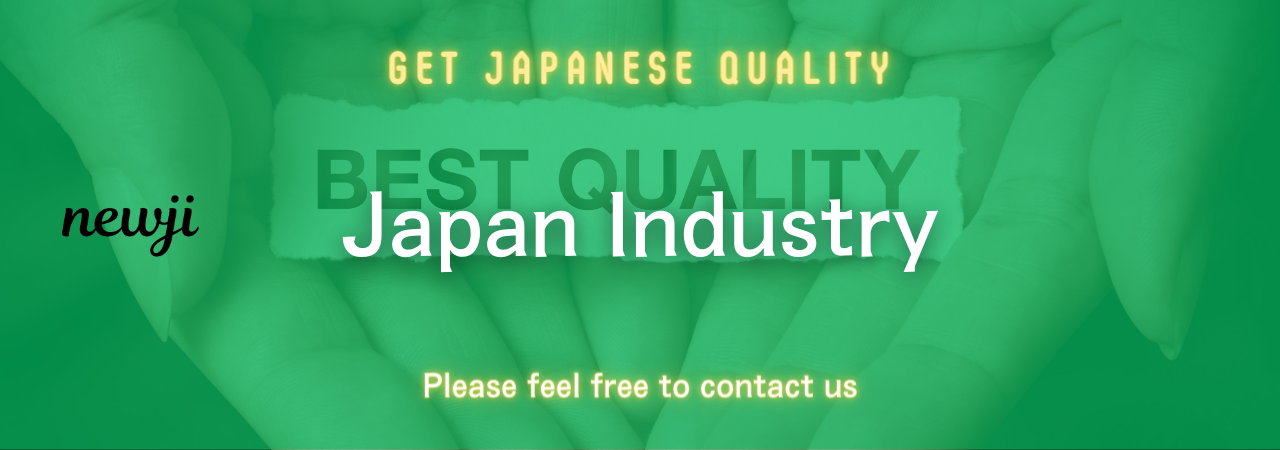
目次
Understanding Global Material Procurement
In recent years, the home appliance manufacturing industry has increasingly relied on a globalized supply chain for material procurement.
This approach is driven by the need to secure quality components and reduce costs, thereby enhancing competitiveness in an ever-changing market.
However, this globalization also presents new challenges that manufacturers must navigate to ensure the continuity and efficiency of their production processes.
The Complexities of Global Sourcing
Sourcing materials from around the world involves several complexities.
Manufacturers have to deal with varying regulations, fluctuating currencies, and differing quality standards.
Moreover, logistical issues such as transportation, storage, and border crossings can impact the delivery timeline and, consequently, the production schedule.
Understanding these factors is vital for manufacturers attempting to streamline their global supply chains.
Regulatory Considerations
Different countries have different regulations related to labor, environmental impact, and product standards.
Manufacturers need to ensure their suppliers comply with all applicable regulations to prevent legal complications.
As regulations can change frequently, staying informed and adapting quickly is a constant challenge.
It may involve fostering strong relationships with local entities and possibly hiring compliance specialists who understand the local laws and customs.
Economic Factors and Currency Fluctuations
One of the primary motivations for globalizing material procurement is the cost advantage.
However, currency volatility can quickly erode these savings and affect margins.
Home appliance manufacturers must develop strategies to manage financial risks associated with international transactions, which might include engaging in forward contracts or using currency options to hedge against unfavorable movements.
Quality Assurance Across Borders
Maintaining consistent quality across different jurisdictions is another challenge.
As components come from diverse regions, manufacturers must implement robust quality assurance systems.
Creating a standardized set of quality metrics and employing regular audits can help ensure that all materials meet the required standards.
Developing strong partnerships with suppliers who prioritize quality can also mitigate risks associated with cross-border sourcing.
Overcoming Logistical Hurdles
Logistics plays a critical role in global material procurement.
Delays in transportation can disrupt manufacturing schedules, leading to financial losses and strained customer relationships.
To minimize these risks, manufacturers can work with reliable logistics partners and invest in technology that provides real-time tracking and inventory management.
Transportation and Storage Considerations
Transporting materials across the globe often involves multimodal transportation, including air, sea, and land freight.
Each mode has its own set of challenges and risks, such as weather disruptions or port congestion, which can affect delivery times.
To address these challenges, manufacturers may diversify their supplier and logistics networks and create contingency plans for potential disruptions.
Moreover, efficient storage solutions near manufacturing hubs can help buffer against transportation delays.
Navigating Cross-Border Challenges
Cross-border movement involves dealing with customs procedures and tariffs that can be time-consuming and costly.
Developing expertise in international trade regulations and leveraging trade agreements can streamline the process.
By understanding these regulations and building strong partnerships with customs brokers, manufacturers can better handle the paperwork and logistical aspects of importing materials.
Strategic Solutions for Effective Global Sourcing
Despite these challenges, there are several strategies that home appliance manufacturers can adopt to optimize their global material procurement processes.
These include investing in technology, building strong supplier relationships, and fostering supply chain resilience.
Investing in Technology
Technological advancement is key to addressing many of the challenges associated with global sourcing.
Implementing supply chain management software can improve visibility across the supply chain, allowing manufacturers to track and manage materials in real-time.
Additionally, technologies such as blockchain can enhance transparency and traceability, ultimately ensuring the integrity of the entire procurement process.
Building Strong Supplier Relationships
Developing strong, long-term relationships with suppliers is fundamental.
It not only aids in quality assurance but also helps manufacturers negotiate better terms and ensures priority access in times of constrained supply.
Conducting regular supplier evaluations and fostering open communication can further strengthen these partnerships.
Enhancing Supply Chain Resilience
Resilience is critical for mitigating risks associated with global sourcing.
Manufacturers can enhance resilience by diversifying their supply base to avoid over-reliance on a single source.
Establishing local backup suppliers and maintaining inventory buffers can also help mitigate the impact of any supply chain disruptions.
Conclusion: Embracing a Global Procurement Strategy
Globalizing material procurement presents both challenges and opportunities for the home appliance manufacturing industry.
By understanding and addressing the complexities associated with this approach, manufacturers can reap significant benefits, such as reduced costs and enhanced competitiveness.
With strategic planning, investment in technology, and robust supplier relationships, home appliance manufacturers can overcome these challenges and build a resilient, efficient global supply chain.
Ultimately, the success of global procurement strategies hinges on the ability to adapt and respond to an ever-evolving international market landscape.
資料ダウンロード
QCD調達購買管理クラウド「newji」は、調達購買部門で必要なQCD管理全てを備えた、現場特化型兼クラウド型の今世紀最高の購買管理システムとなります。
ユーザー登録
調達購買業務の効率化だけでなく、システムを導入することで、コスト削減や製品・資材のステータス可視化のほか、属人化していた購買情報の共有化による内部不正防止や統制にも役立ちます。
NEWJI DX
製造業に特化したデジタルトランスフォーメーション(DX)の実現を目指す請負開発型のコンサルティングサービスです。AI、iPaaS、および先端の技術を駆使して、製造プロセスの効率化、業務効率化、チームワーク強化、コスト削減、品質向上を実現します。このサービスは、製造業の課題を深く理解し、それに対する最適なデジタルソリューションを提供することで、企業が持続的な成長とイノベーションを達成できるようサポートします。
オンライン講座
製造業、主に購買・調達部門にお勤めの方々に向けた情報を配信しております。
新任の方やベテランの方、管理職を対象とした幅広いコンテンツをご用意しております。
お問い合わせ
コストダウンが利益に直結する術だと理解していても、なかなか前に進めることができない状況。そんな時は、newjiのコストダウン自動化機能で大きく利益貢献しよう!
(Β版非公開)