- お役立ち記事
- Challenges and solutions for reducing lead times faced by purchasing managers
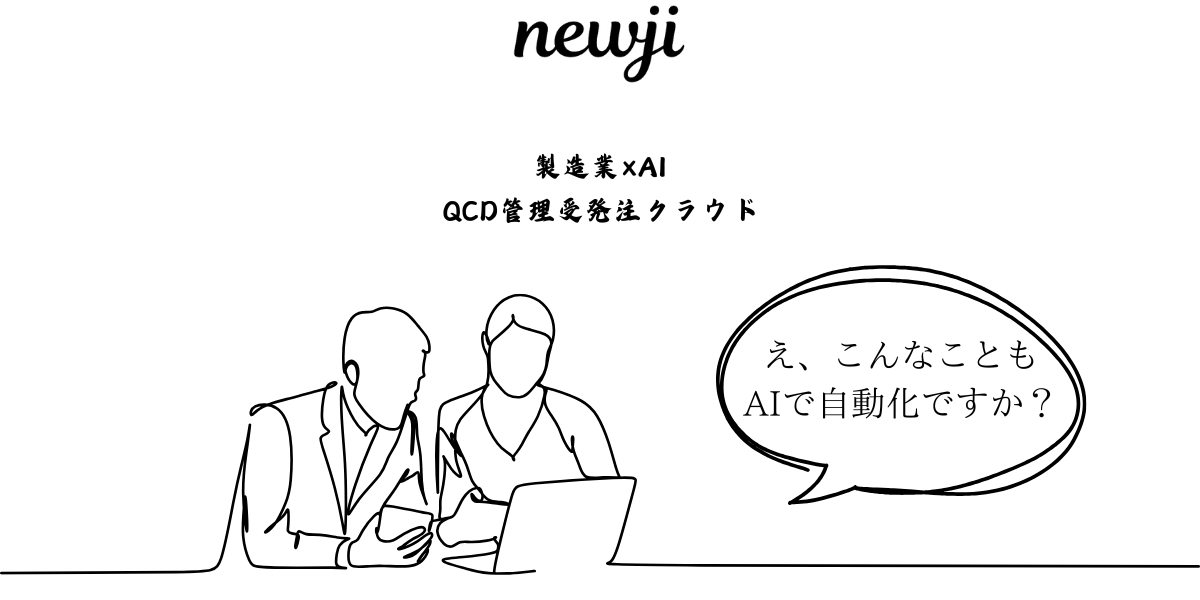
Challenges and solutions for reducing lead times faced by purchasing managers
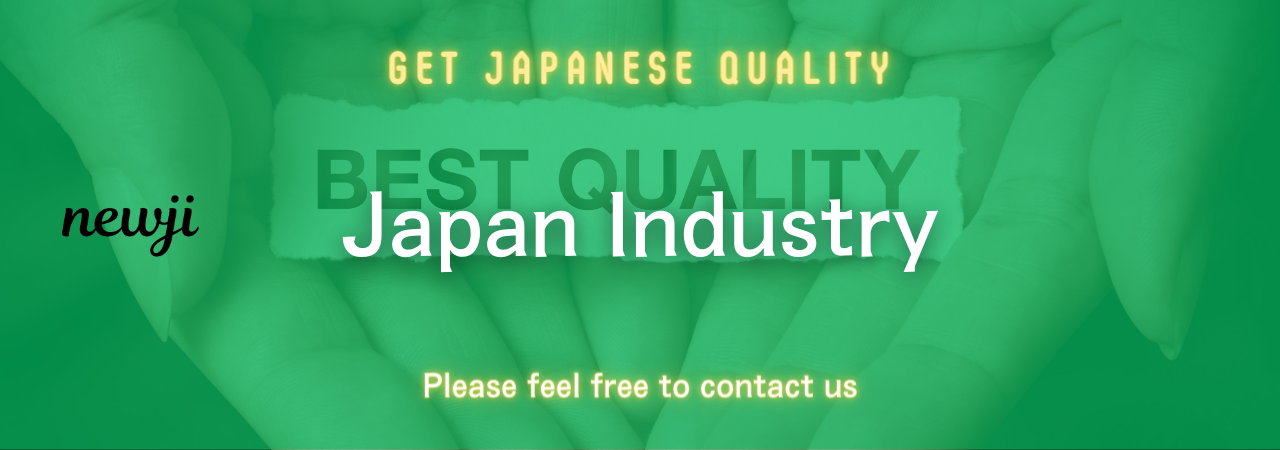
目次
Understanding the Importance of Lead Times
Purchasing managers play a crucial role in ensuring the smooth operation of supply chains.
One of the major challenges they face is reducing lead times, which is essential for maintaining an efficient and responsive supply chain.
Lead time refers to the period between the initiation of a purchase order and the delivery of the final product.
Reducing lead times is of utmost importance as it directly impacts inventory levels, production schedules, and customer satisfaction.
When lead times are extended, it can result in higher costs, stockouts, and disruptions in production.
Therefore, it is vital for purchasing managers to effectively address this challenge.
Identifying Factors Affecting Lead Times
To successfully reduce lead times, it is essential for purchasing managers to understand the factors that contribute to delays.
Several key factors can impact lead times:
Supplier Performance
The performance of suppliers plays a significant role in lead times.
Factors such as the supplier’s production capacity, reliability, and geographical location can influence how quickly they can fulfill orders.
Transportation and Logistics
Logistics is another critical component that affects lead times.
Delays can occur due to transportation issues, customs clearance, and freight availability.
Purchasing managers need to understand the transportation routes and potential hold-ups in the supply chain.
Order Processing and Workflow
Inefficient order processing and workflow can increase lead times.
Bottlenecks in approval processes or the transmission of order information can result in unnecessary delays.
Demand Variability
Fluctuating demand can also influence lead times.
Surges in demand can overwhelm suppliers, leading to delays in manufacturing and shipping.
Strategies to Reduce Lead Times
Once purchasing managers identify the factors causing lead time delays, they can implement strategies to address them effectively.
Building Strong Supplier Relationships
Maintaining healthy relationships with suppliers is vital for reducing lead times.
Regular communication and collaboration can help in understanding each other’s needs and capabilities.
Working closely with suppliers ensures they are aware of your requirements and are more likely to prioritize your orders.
Implementing Technology Solutions
Using technology to optimize supply chain management can significantly reduce lead times.
Automated systems help in processing orders more efficiently and tracking shipments in real time.
Technologies like AI and machine learning can predict potential delays, allowing purchasing managers to take preventive actions.
Streamlining Order Processing
Simplifying the order processing workflow can also reduce lead times.
By removing unnecessary steps and improving coordination among team members, purchasing managers can speed up the approval and execution of orders.
Enhancing Demand Forecasting
Accurate demand forecasting helps in aligning production and procurement activities with market needs.
By understanding demand patterns, purchasing managers can maintain adequate inventory levels and place orders proactively.
Innovative Approaches to Tackle Lead Time Challenges
In addition to conventional strategies, innovative approaches can further help in reducing lead times.
Leverage Supplier Scorecards
Implementing supplier scorecards can provide insights into supplier performance across various metrics like lead time, quality, and reliability.
This approach promotes transparency and motivates suppliers to improve their performance.
Adopt JIT (Just-In-Time) Inventory
JIT inventory systems focus on receiving goods only when they are needed, reducing the need for excessive storage.
By aligning inventory with production schedules, purchasing managers minimize lead times associated with large stockpiles.
Invest in Collaborative Platforms
Collaborative platforms enable real-time communication and data sharing among supply chain partners.
The use of such platforms ensures everyone is on the same page, reducing misunderstandings and delays.
Overcoming Challenges in Implementation
While solutions exist to reduce lead times, implementing these strategies is not without challenges.
Change Management
Shifting to new processes and technology requires change management efforts.
Employees and suppliers may need time to adapt to new practices.
Purchasing managers should provide training and support to facilitate a smooth transition.
Cost Considerations
Implementing technology solutions or adjusting supplier relationships often involves upfront costs.
Purchasing managers need to analyze the long-term benefits and returns on investment when contemplating these changes.
Balancing Stakeholder Interests
Reducing lead times may require negotiations and compromises among various stakeholders.
Purchasing managers should strive to balance cost, quality, and timeliness while maintaining strong relationships across the supply chain.
Conclusion
Reducing lead times remains one of the significant challenges for purchasing managers.
By understanding and addressing the factors contributing to delays, purchasing managers can implement effective strategies to optimize lead times.
Building strong supplier relationships, leveraging technology, and streamlining processes are actionable steps toward minimizing lead times.
Despite the challenges associated with implementation, the benefits of reduced lead times in terms of cost savings, improved customer satisfaction, and enhanced supply chain efficiency make it a worthwhile endeavor for purchasing managers.
資料ダウンロード
QCD調達購買管理クラウド「newji」は、調達購買部門で必要なQCD管理全てを備えた、現場特化型兼クラウド型の今世紀最高の購買管理システムとなります。
ユーザー登録
調達購買業務の効率化だけでなく、システムを導入することで、コスト削減や製品・資材のステータス可視化のほか、属人化していた購買情報の共有化による内部不正防止や統制にも役立ちます。
NEWJI DX
製造業に特化したデジタルトランスフォーメーション(DX)の実現を目指す請負開発型のコンサルティングサービスです。AI、iPaaS、および先端の技術を駆使して、製造プロセスの効率化、業務効率化、チームワーク強化、コスト削減、品質向上を実現します。このサービスは、製造業の課題を深く理解し、それに対する最適なデジタルソリューションを提供することで、企業が持続的な成長とイノベーションを達成できるようサポートします。
オンライン講座
製造業、主に購買・調達部門にお勤めの方々に向けた情報を配信しております。
新任の方やベテランの方、管理職を対象とした幅広いコンテンツをご用意しております。
お問い合わせ
コストダウンが利益に直結する術だと理解していても、なかなか前に進めることができない状況。そんな時は、newjiのコストダウン自動化機能で大きく利益貢献しよう!
(Β版非公開)