- お役立ち記事
- Challenges and Solutions in Customized Product Procurement
Challenges and Solutions in Customized Product Procurement
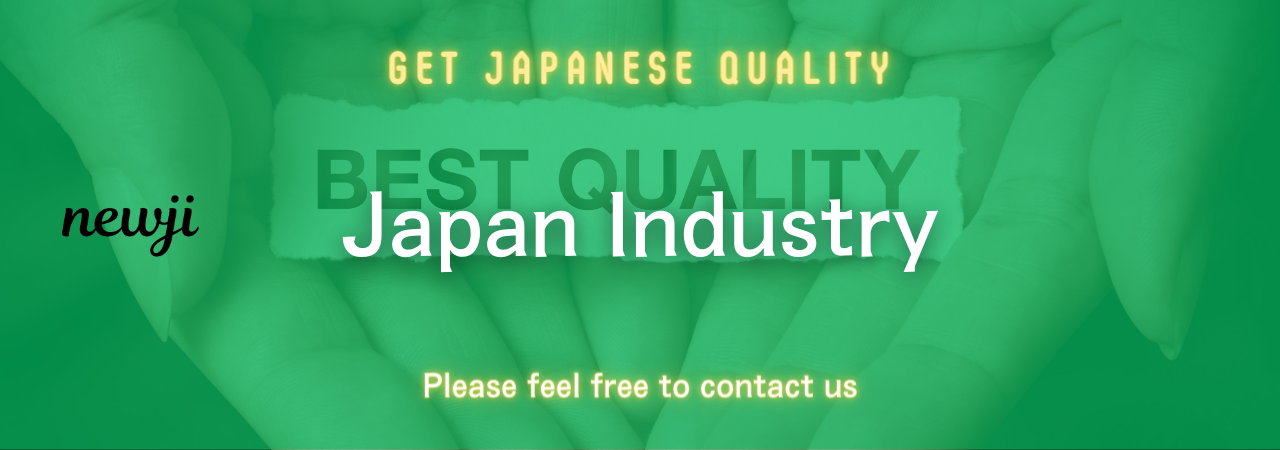
In today’s competitive market, businesses are increasingly turning to customized products to meet specific customer needs and stand out from their competitors.
However, procuring customized products presents unique challenges.
Understanding these challenges and the solutions available can help businesses streamline their processes and deliver high-quality products to their customers.
目次
Understanding the Challenges in Customized Product Procurement
1. Complexity in Design and Specifications
Customized products require detailed designs and specifications, tailored to precise customer requirements.
This complexity can result in longer lead times and increased potential for errors.
Miscommunication between the customer, designer, and manufacturer can lead to incorrect specifications, which can be costly to rectify.
Clear, concise communication and comprehensive documentation are essential to overcoming this challenge.
2. Sourcing Specialized Materials
Customized products often need unique or rare materials that may not be readily available.
Finding reliable suppliers who can provide these materials in the required quantity and quality can be challenging.
Additionally, lead times for specialized materials can be significantly longer, impacting overall production schedules.
Building relationships with multiple suppliers and maintaining a robust procurement network can mitigate this issue.
3. Quality Assurance
Ensuring the quality of customized products is a complex task.
Standard quality control measures might not apply due to the unique nature of each product.
Quality assurance processes have to be adjusted to account for the specific requirements of customized products.
Implementing rigorous quality checks at various stages of production can help maintain high standards.
4. Cost Management
Customized products often come with higher costs due to specialized design, materials, and production processes.
Managing these costs while maintaining profitability is a significant challenge.
Careful budgeting, cost monitoring, and efficient resource allocation are crucial to minimizing expenses without compromising quality.
Effective Solutions for Customized Product Procurement
1. Leveraging Technology
Technology plays a pivotal role in streamlining customized product procurement.
Using CAD (Computer-Aided Design) systems can help in creating precise designs and specifications.
ERP (Enterprise Resource Planning) software can assist in managing the procurement process, tracking materials, and ensuring timely delivery.
Automation tools can reduce human errors and accelerate various stages of procurement and production.
2. Building Strong Supplier Relationships
Collaborating closely with suppliers is crucial for sourcing specialized materials efficiently.
Long-term, strategic partnerships with suppliers can ensure a steady supply of high-quality materials.
Regular communication and collaboration can help in resolving any supply chain issues quickly.
Investing in supplier relationship management tools can facilitate better coordination and transparency.
3. Implementing Robust Quality Control Systems
Developing a comprehensive quality control system tailored to customized products is essential.
Implementing stage-wise quality checks can help identify and rectify issues early in the production process.
Using quality management software can streamline inspections and ensure consistent quality.
Training employees on quality standards and best practices can enhance overall product quality.
4. Efficient Cost Management
Efficient cost management starts with accurate cost estimation during the planning stage.
Using cost management software can help in tracking expenses and identifying cost-saving opportunities.
Regular financial audits and reviews can help in staying within budget.
Investing in efficient production technologies can reduce wastage and lower production costs.
Case Study: Successful Customized Product Procurement
Let’s look at a hypothetical case study to understand how businesses can successfully navigate the challenges of customized product procurement.
Imagine a company that designs customized furniture for luxury hotels.
To meet the unique design specifications of each hotel, the company uses advanced CAD software for precision design work.
They have established strong relationships with a network of suppliers who provide high-quality, rare materials essential for their bespoke furniture pieces.
The company implements a robust quality control process, including multiple quality checkpoints throughout production.
They use quality management software to track inspections and ensure that every piece meets the client’s standards.
For cost management, the company employs ERP software to monitor expenses and optimize resource allocation.
Regular financial reviews and audits help them stay on budget while maintaining high quality.
This systematic approach enables the company to deliver customized furniture on time and within budget, ensuring high customer satisfaction.
Future Trends in Customized Product Procurement
As technology advances, the landscape of customized product procurement continues to evolve.
3D printing has the potential to revolutionize the production of customized products, offering unprecedented precision and flexibility.
AI and machine learning can enhance demand forecasting, inventory management, and supplier selection.
Sustainability is becoming a significant focus, with businesses seeking eco-friendly materials and processes for their customized products.
Investing in sustainable procurement practices can help in meeting customer expectations and regulatory requirements.
The increasing use of digital twins, virtual simulations of physical products, can enhance design accuracy and accelerate the production process.
Conclusion
Customized product procurement presents several challenges, from design complexities and material sourcing to quality assurance and cost management.
However, by leveraging technology, building strong supplier relationships, implementing robust quality control systems, and managing costs efficiently, businesses can overcome these challenges.
Staying informed about emerging trends in technology and sustainability can further enhance procurement processes.
With a strategic approach, businesses can successfully navigate the complexities of customized product procurement and deliver high-quality, bespoke products to their clients.
資料ダウンロード
QCD調達購買管理クラウド「newji」は、調達購買部門で必要なQCD管理全てを備えた、現場特化型兼クラウド型の今世紀最高の購買管理システムとなります。
ユーザー登録
調達購買業務の効率化だけでなく、システムを導入することで、コスト削減や製品・資材のステータス可視化のほか、属人化していた購買情報の共有化による内部不正防止や統制にも役立ちます。
NEWJI DX
製造業に特化したデジタルトランスフォーメーション(DX)の実現を目指す請負開発型のコンサルティングサービスです。AI、iPaaS、および先端の技術を駆使して、製造プロセスの効率化、業務効率化、チームワーク強化、コスト削減、品質向上を実現します。このサービスは、製造業の課題を深く理解し、それに対する最適なデジタルソリューションを提供することで、企業が持続的な成長とイノベーションを達成できるようサポートします。
オンライン講座
製造業、主に購買・調達部門にお勤めの方々に向けた情報を配信しております。
新任の方やベテランの方、管理職を対象とした幅広いコンテンツをご用意しております。
お問い合わせ
コストダウンが利益に直結する術だと理解していても、なかなか前に進めることができない状況。そんな時は、newjiのコストダウン自動化機能で大きく利益貢献しよう!
(Β版非公開)