- お役立ち記事
- Challenges and ways to overcome them when the purchasing department reorganizes the material supply network
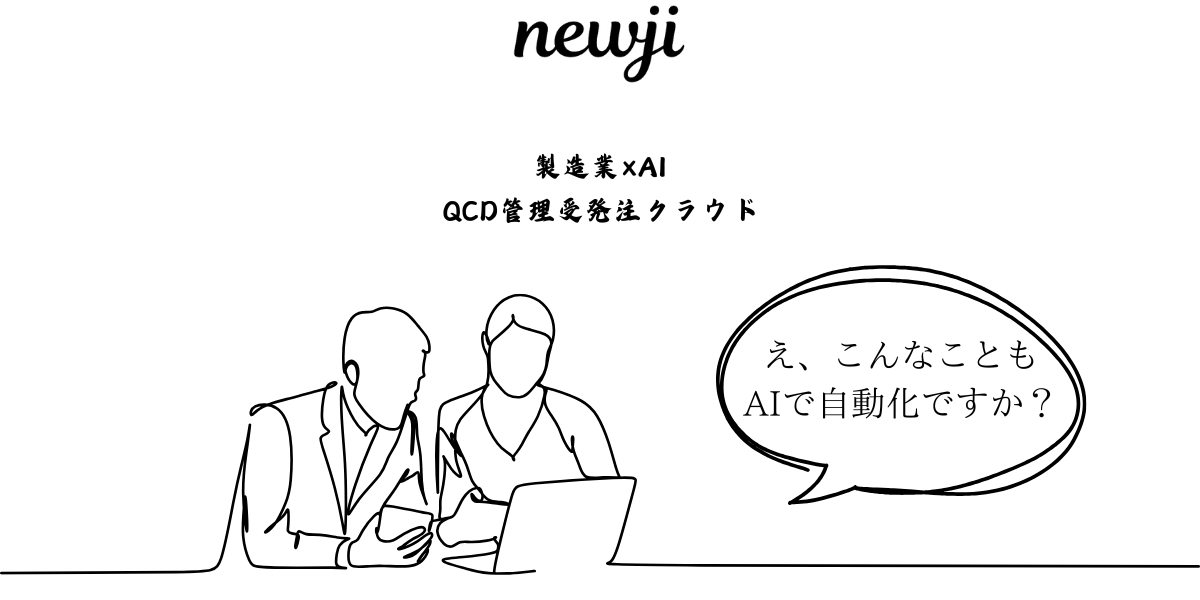
Challenges and ways to overcome them when the purchasing department reorganizes the material supply network
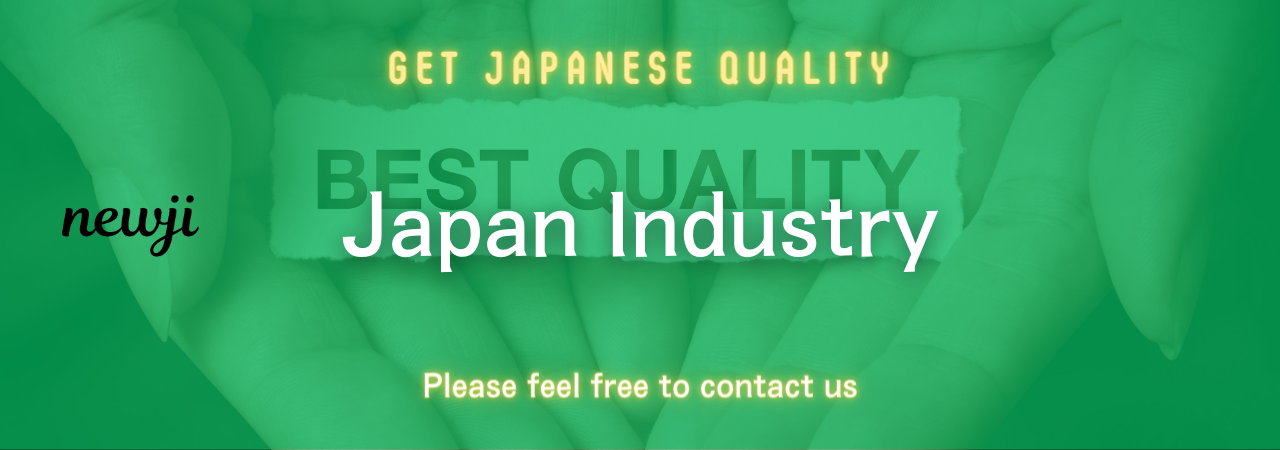
When a purchasing department decides to reorganize its material supply network, it faces several challenges that need strategic planning and problem-solving. The goal of this reorganization is often to improve efficiency, reduce costs, and enhance the quality of materials received. However, achieving this can be complex and involves addressing key issues head-on.
目次
Understanding the Challenges
Before diving into solutions, it’s crucial to understand the common challenges that arise during a reorganization of the material supply network.
1. Supplier Resistance
One of the primary challenges is resistance from existing suppliers. Suppliers who have been part of the supply chain for a long time may be reluctant to change their processes. They might fear losing business or having tighter controls imposed on them. This resistance can lead to delays and complications in the implementation of new strategies.
2. Coordination Across Departments
Reorganization often requires coordination between various departments within a company. The purchasing department must work closely with logistics, production, and finance. Each department has its own priorities and ways of operating, which can create friction and misunderstandings, further complicating the reorganization process.
3. Information Overload
During reorganization, the purchasing department may deal with a flood of information. Sorting through data about supplier performances, cost structures, and logistics can be overwhelming. It’s crucial to extract relevant insights while avoiding analysis paralysis, where the decision-making process gets stalled due to excessive information.
4. Cost Management
While the ultimate goal is to reduce costs, the initial phase of reorganization might incur additional expenses. These can include costs for new technology implementations, training staff, or even penalties for changing supplier contracts. Balancing these costs while maintaining quality is a delicate task.
5. Technology Integration
Integrating new technology to streamline operations is often a part of reorganization. However, adopting new technologies can be challenging. Systems may not be compatible with existing processes, requiring further customization and leading to potential downtime or disruptions.
Strategies for Overcoming Challenges
Despite these challenges, there are strategic approaches that can help overcome them effectively.
1. Engage Suppliers Early
To address supplier resistance, involve them early in the process. Conduct meetings and open discussions to explain the benefits of the reorganization. Emphasize how this change can strengthen partnerships and improve efficiencies. By making suppliers part of the planning phase, they’re likely to be more cooperative and supportive.
2. Foster Cross-Department Collaboration
Facilitate regular inter-departmental meetings to ensure all departments are on the same page. Create a shared platform where all stakeholders can communicate and coordinate efforts. Encourage a culture of collaboration rather than competition, emphasizing the shared goal of streamlining the supply network.
3. Simplify Data Handling
To avoid information overload, incorporate data management tools that can simplify data analysis. Use dashboards and data visualization tools to make insights accessible and understandable. Focus on key performance indicators that align with the organization’s strategic goals to prioritize decision-making processes.
4. Plan for Extra Costs
Anticipate the extra costs involved by setting aside a contingency budget. Conduct a cost-benefit analysis to understand where expenses can lead to long-term savings. Transparent budgeting and financial forecasting can prepare the department to handle these expenses without jeopardizing goals.
5. Leverage Scalable Technology Solutions
When it comes to technology integration, choose scalable solutions that can grow with the organization. Ensure the technology can be easily integrated with existing systems. Provide training sessions to equip the team with the necessary skills to adapt to new tools, reducing stress and resistance to change.
Building a Resilient Supply Network
Aligning the reorganization efforts with broader company goals is essential for building a resilient supply network. Here’s how:
1. Focus on Quality and Reliability
Prioritize quality and reliability when selecting and evaluating suppliers. A resilient supply network is built on a foundation of reliable suppliers who consistently deliver quality materials. Set clear performance metrics and conduct regular assessments to ensure suppliers meet expectations.
2. Diversify the Supplier Base
Diversification is key to reducing dependency on a single supplier. By having a range of suppliers, the purchasing department can negotiate better terms and reduce risks associated with supply disruptions. Develop relationships with multiple suppliers in different regions to safeguard against geopolitical or economic changes.
3. Implement Continuous Improvement
Reorganization isn’t a one-time task but an ongoing process. Implement a continuous improvement mindset by reviewing and adapting strategies based on performance data. Encourage feedback and input from all stakeholders to refine processes and make necessary adjustments.
Conclusion
Reorganizing a material supply network in the purchasing department is no small feat. By understanding the challenges and applying strategic solutions, purchasing departments can effectively enhance their operations. Engaging with suppliers, fostering collaboration, and focusing on scalable technology solutions are some of the ways to build a more resilient and efficient supply network. Through continuous improvement and adaptability, the purchasing department can navigate the complexities of reorganization to achieve long-term success.
資料ダウンロード
QCD調達購買管理クラウド「newji」は、調達購買部門で必要なQCD管理全てを備えた、現場特化型兼クラウド型の今世紀最高の購買管理システムとなります。
ユーザー登録
調達購買業務の効率化だけでなく、システムを導入することで、コスト削減や製品・資材のステータス可視化のほか、属人化していた購買情報の共有化による内部不正防止や統制にも役立ちます。
NEWJI DX
製造業に特化したデジタルトランスフォーメーション(DX)の実現を目指す請負開発型のコンサルティングサービスです。AI、iPaaS、および先端の技術を駆使して、製造プロセスの効率化、業務効率化、チームワーク強化、コスト削減、品質向上を実現します。このサービスは、製造業の課題を深く理解し、それに対する最適なデジタルソリューションを提供することで、企業が持続的な成長とイノベーションを達成できるようサポートします。
オンライン講座
製造業、主に購買・調達部門にお勤めの方々に向けた情報を配信しております。
新任の方やベテランの方、管理職を対象とした幅広いコンテンツをご用意しております。
お問い合わせ
コストダウンが利益に直結する術だと理解していても、なかなか前に進めることができない状況。そんな時は、newjiのコストダウン自動化機能で大きく利益貢献しよう!
(Β版非公開)