- お役立ち記事
- Challenges faced by purchasing departments in improving supply chain efficiency and how to solve them
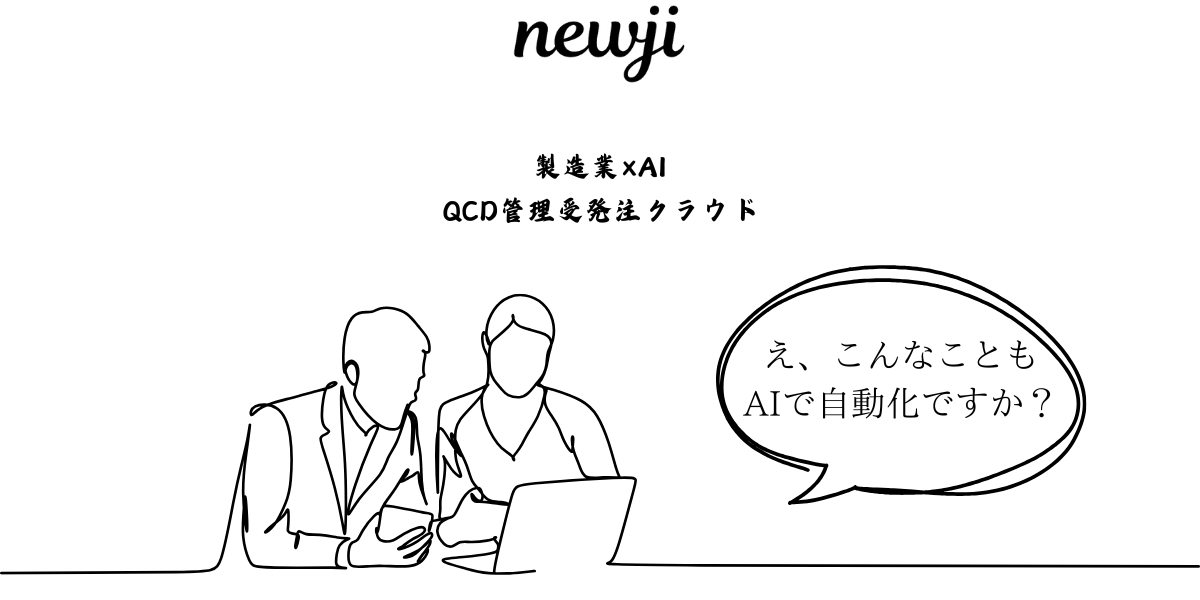
Challenges faced by purchasing departments in improving supply chain efficiency and how to solve them
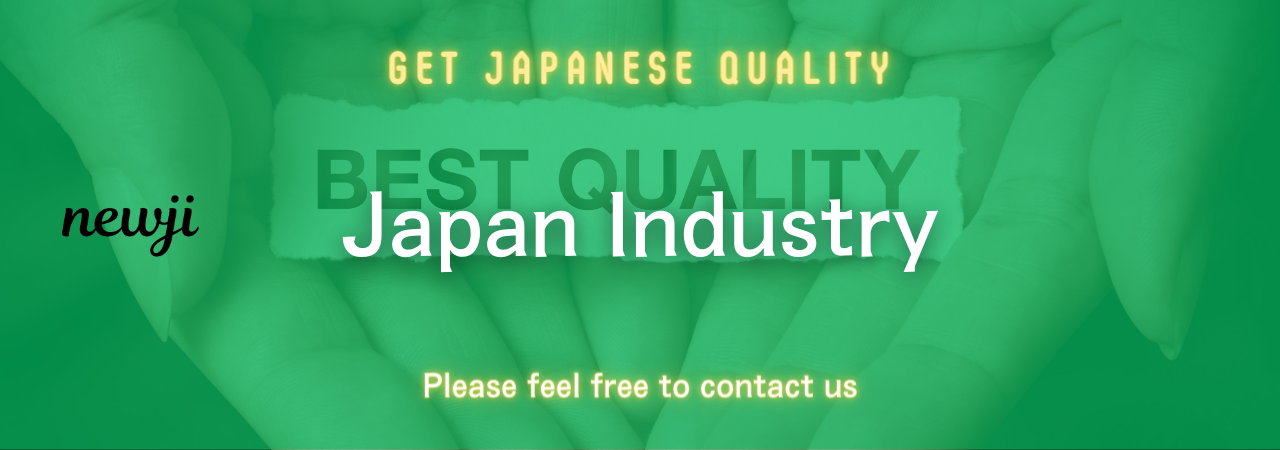
目次
Understanding the Role of Purchasing Departments
Purchasing departments are pivotal in any organization, acting as the critical link between suppliers and the company.
Their primary responsibility is to acquire the goods and services needed for the organization to operate efficiently.
However, these departments face a myriad of challenges that can impact the overall efficiency of the supply chain.
Understanding these challenges and finding effective solutions is essential for the seamless functioning of the supply chain.
Common Challenges Faced by Purchasing Departments
1. Supplier Relationship Management
Strong relationships with suppliers are crucial.
However, maintaining these relationships can be challenging due to factors such as communication barriers, cultural differences, or geographic distances.
Issues like late deliveries or inconsistent quality can strain these relationships further.
2. Cost Management
Ensuring cost efficiency while maintaining quality is a significant challenge.
Purchasing departments are often tasked with finding the best prices while keeping within budget constraints.
Market fluctuations, changes in demand, or unexpected events can impact costs, making management difficult.
3. Compliance and Regulation
Navigating the complex web of international regulations and compliance standards is daunting.
Purchasing departments must ensure that suppliers adhere to these legal and ethical standards, which can vary significantly across regions.
Failure to comply can lead to severe penalties and damage to the company’s reputation.
4. Technological Integration
Keeping up with technological advancements is vital for improving supply chain efficiency.
However, integrating new technology can be challenging due to costs, training requirements, and resistance to change from staff.
A lack of technological proficiency can lead to inefficiencies and errors.
5. Risk Management
Purchasing departments must identify and mitigate risks associated with supply chain disruptions.
Natural disasters, political instability, and economic shifts can all impact the supply chain.
Failure to manage these risks can lead to significant operational setbacks.
Strategies to Improve Supply Chain Efficiency
1. Enhancing Supplier Relationships
Building strong, collaborative relationships with suppliers is essential.
Regular communication, fostering trust, and creating mutual benefits can help improve these relationships.
Companies can use supplier performance evaluations and feedback mechanisms to ensure continuous improvement.
2. Effective Cost Management
Implementing strategic sourcing practices can help organizations negotiate better prices and terms.
Purchasing departments can leverage market research, cost analysis, and supplier competition to achieve cost savings.
Additionally, partnering with finance departments to monitor spending and budget adherence can improve overall cost management.
3. Ensuring Compliance and Regulation
Establishing a robust compliance framework helps organizations stay ahead of regulatory changes.
Training staff on current regulations and employing compliance software can enhance adherence.
Partnering with legal experts ensures that all contracts and practices meet international standards.
4. Embracing Technological Solutions
Investing in supply chain management software and tools can significantly improve efficiency.
These technologies can enhance visibility, streamline processes, and provide real-time data for decision-making.
Ensuring staff are trained and comfortable with new technologies is crucial for successful integration.
5. Effective Risk Management
Developing a comprehensive risk management strategy is essential.
This involves identifying potential risks, assessing their impact, and creating contingency plans.
Regular risk assessments and a proactive approach can mitigate potential disruptions.
Conclusion
Purchasing departments are integral to the smooth operation of the supply chain.
While they face numerous challenges, implementing strategic approaches can enhance their efficiency.
By addressing supplier relationships, cost management, compliance, technological integration, and risk management, organizations can improve their supply chain operations.
Ultimately, overcoming these challenges leads to better organizational performance, cost savings, and a more resilient supply chain.
資料ダウンロード
QCD調達購買管理クラウド「newji」は、調達購買部門で必要なQCD管理全てを備えた、現場特化型兼クラウド型の今世紀最高の購買管理システムとなります。
ユーザー登録
調達購買業務の効率化だけでなく、システムを導入することで、コスト削減や製品・資材のステータス可視化のほか、属人化していた購買情報の共有化による内部不正防止や統制にも役立ちます。
NEWJI DX
製造業に特化したデジタルトランスフォーメーション(DX)の実現を目指す請負開発型のコンサルティングサービスです。AI、iPaaS、および先端の技術を駆使して、製造プロセスの効率化、業務効率化、チームワーク強化、コスト削減、品質向上を実現します。このサービスは、製造業の課題を深く理解し、それに対する最適なデジタルソリューションを提供することで、企業が持続的な成長とイノベーションを達成できるようサポートします。
オンライン講座
製造業、主に購買・調達部門にお勤めの方々に向けた情報を配信しております。
新任の方やベテランの方、管理職を対象とした幅広いコンテンツをご用意しております。
お問い合わせ
コストダウンが利益に直結する術だと理解していても、なかなか前に進めることができない状況。そんな時は、newjiのコストダウン自動化機能で大きく利益貢献しよう!
(Β版非公開)