- お役立ち記事
- Challenges in procuring rubber molded parts for small volume production and how to choose the optimal supplier
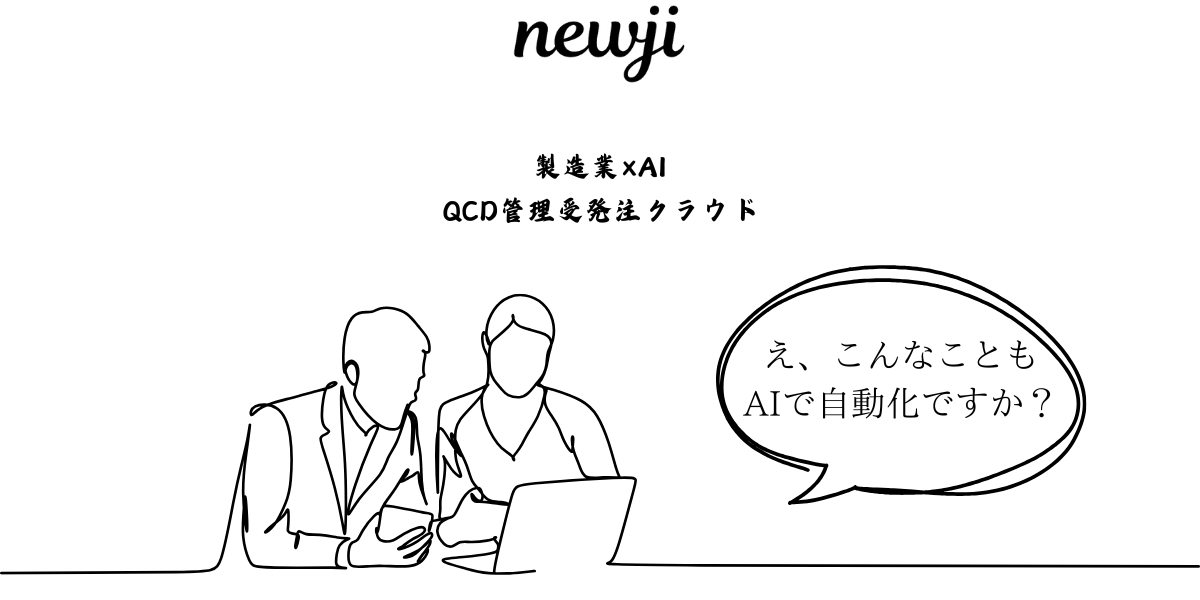
Challenges in procuring rubber molded parts for small volume production and how to choose the optimal supplier
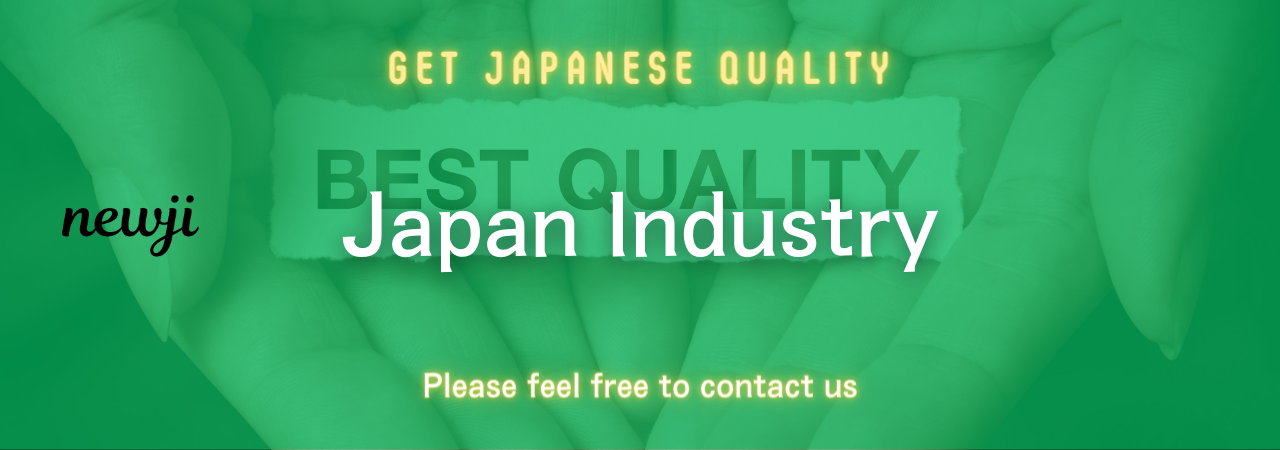
目次
Understanding Rubber Molded Parts
Rubber molded parts are essential components found in various industries, ranging from automotive to consumer electronics.
These parts can be crafted into diverse shapes and sizes, serving functionalities such as gaskets, seals, and connectors.
In essence, they provide solutions to problems like sealing, vibration reduction, and mechanical protection.
The significance of custom rubber molded parts lies in their adaptability to exact design specifications and operational conditions.
When it comes to small volume production, tailored approaches to manufacturing and procurement become pivotal.
Unlike mass production, small volume production demands intricate attention to detail and precision to meet specific requirements.
This is where the choice of supplier can make a substantial difference in both product quality and production efficiency.
Challenges Faced in Procuring Rubber Molded Parts
One of the primary challenges encountered in procuring rubber molded parts, especially for small volume production, is the balancing act between cost and quality.
High-quality rubber materials often come with a significant price tag, creating a conundrum for procurement teams striving to stay within budget.
For small volume production, the absence of economies of scale can exacerbate this issue, making every unit potentially more expensive to produce.
Meeting custom specifications is another critical hurdle.
The more specific the design and function of the part, the more complex the manufacturing process becomes.
This complexity requires specialized machinery, skilled labor, and tighter quality control, thereby escalating the production challenges.
Lead time is a significant constraint as well.
Production schedules in small volume manufacturing are typically tight, leaving little room for delays.
Rubber molded parts may need several iterations for perfection, further complicating lead time management.
Delays in this sector can reverberate through the supply chain, disturbing overall project timelines.
Quality assurance and regulatory compliance also pose challenges, as ensuring each part meets industry standards demands accurate testing and verification processes.
In some cases, companies might need custom testing solutions, which could be both time-consuming and costly.
Why Selecting the Right Supplier Matters
Selecting the right supplier is crucial to overcoming these production challenges.
Suppliers can impact material quality, production timelines, cost-effectiveness, and compliance with standards.
An ideal supplier acts as a partner, offering solutions and adaptations to match specific project needs.
A good supplier should have experience in handling small volume orders and a robust understanding of the rubber molding process.
They should offer competitive pricing without compromising quality, which involves transparent negotiation and clear communication.
Advanced technology and expertise in molding techniques are characteristics of a suitable supplier.
This means they utilize modern, efficient machinery and employ skilled workers who can precisely meet custom specifications.
Quality assurance processes should align with industry best practices.
Suppliers should provide a track record of adherence to quality standards and include testing in their manufacturing workflows to ensure defect-free products.
Moreover, adaptability is a trait that should not be overlooked.
The right supplier can quickly modify production strategies to accommodate design changes, material substitutions, or expedited delivery requests.
How to Choose the Optimal Supplier
Choosing the optimal supplier for rubber molded parts in small volume production involves several steps.
The first is conducting extensive research to identify potential suppliers that specialize in your required product type and volume.
Evaluate them based on past customer reviews, market reputation, and experience in the industry.
Next, assess their technical capabilities.
Visit their production facilities, if possible, to observe their machinery and production environment.
Discuss process details to ensure they can meet your product specifications without compromise.
It’s important to examine the quality control measures the supplier has in place.
Ask about the techniques used for testing and verifying part dimensions and functionality.
A supplier with a rigorous quality check procedure is more likely to deliver consistent product quality.
Cost assessment follows.
While budget constraints are a reality, strive for a balance between cost and quality.
Request detailed quotations, and make comparisons considering both price and the value provided by services and product quality.
Customer service and communication are paramount.
A supplier who maintains open, clear, and timely communication provides more than just parts – they offer peace of mind.
Addressing issues promptly and facilitating collaborative problem-solving makes the production process smoother and more efficient.
Finally, consider the capacity for innovation and development.
A progressive supplier is likely to stay updated with new technologies and processes that can enhance your product and reduce production costs.
They might even suggest alternatives or optimizations you hadn’t considered, adding value to your partnership.
Conclusion
Procuring rubber molded parts for small volume production is a nuanced process that presents various challenges.
Effectively managing these challenges means selecting a supplier equipped to facilitate high-quality production, flexible enough to adjust to specific needs, and committed to maintaining open communication.
By carefully evaluating suppliers based on their experience, technical capabilities, quality control processes, and customer service, companies can find the right partners for their needs.
This ensures not only a seamless production process but also enhances the overall quality and efficiency of the produced parts, contributing to the success of their product lines.
資料ダウンロード
QCD調達購買管理クラウド「newji」は、調達購買部門で必要なQCD管理全てを備えた、現場特化型兼クラウド型の今世紀最高の購買管理システムとなります。
ユーザー登録
調達購買業務の効率化だけでなく、システムを導入することで、コスト削減や製品・資材のステータス可視化のほか、属人化していた購買情報の共有化による内部不正防止や統制にも役立ちます。
NEWJI DX
製造業に特化したデジタルトランスフォーメーション(DX)の実現を目指す請負開発型のコンサルティングサービスです。AI、iPaaS、および先端の技術を駆使して、製造プロセスの効率化、業務効率化、チームワーク強化、コスト削減、品質向上を実現します。このサービスは、製造業の課題を深く理解し、それに対する最適なデジタルソリューションを提供することで、企業が持続的な成長とイノベーションを達成できるようサポートします。
オンライン講座
製造業、主に購買・調達部門にお勤めの方々に向けた情報を配信しております。
新任の方やベテランの方、管理職を対象とした幅広いコンテンツをご用意しております。
お問い合わせ
コストダウンが利益に直結する術だと理解していても、なかなか前に進めることができない状況。そんな時は、newjiのコストダウン自動化機能で大きく利益貢献しよう!
(Β版非公開)