- お役立ち記事
- Challenges in prototyping and mass production of fiber-reinforced resin
月間77,185名の
製造業ご担当者様が閲覧しています*
*2025年2月28日現在のGoogle Analyticsのデータより
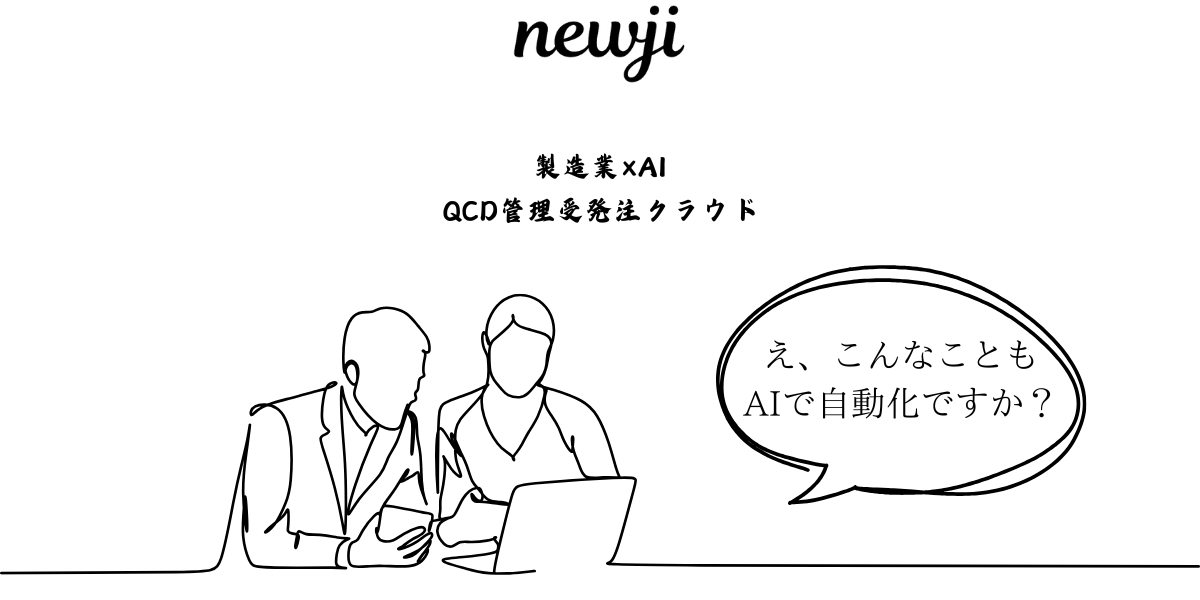
Challenges in prototyping and mass production of fiber-reinforced resin
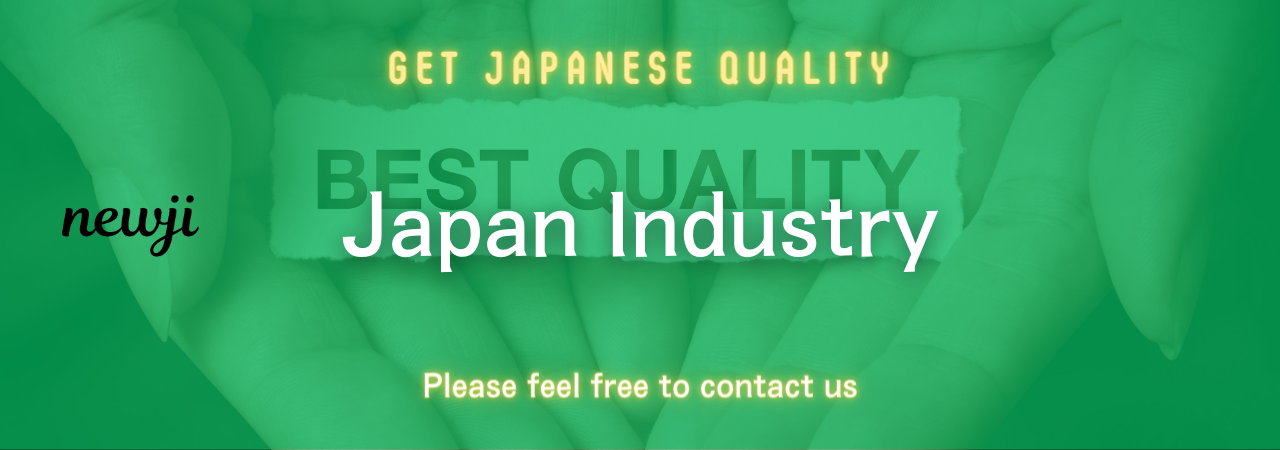
目次
Understanding Fiber-Reinforced Resin
Fiber-reinforced resin is a sturdy, lightweight material comprising a polymer matrix reinforced with fibers.
These fibers can be made from various materials, such as glass, carbon, or aramid.
The combination results in a composite material known for its high strength-to-weight ratio and resilience.
This makes it a popular choice in industries such as aerospace, automotive, and construction.
However, the journey from prototyping to mass production of fiber-reinforced resin products is not without its challenges.
The Prototyping Phase
Design Complexity
One of the major challenges during the prototyping phase is design complexity.
Designers aim to optimize the performance of the fiber-reinforced resin material by choosing the right combination of fiber type, orientation, and matrix material.
This involves considerable experimentation and simulation to ensure that the designed structure can withstand expected loads and environmental conditions.
Mistakes in design can lead to increased production costs and delays.
Material Behavior
Another challenge in prototyping is predicting how the material will behave under different conditions.
Fiber-reinforced resins are anisotropic, meaning their strength and stiffness are different in different directions.
Engineers must thoroughly test prototypes to understand their mechanical properties and ensure they meet the necessary performance criteria.
Tooling Development
Creating tools for the prototyping phase is another significant hurdle.
Tooling refers to the molds and fixtures used to shape the fiber-reinforced resin during manufacturing.
Developing high-precision tooling is costly and time-consuming, especially for complex geometries.
Any modification to the design may require new tooling, which increases costs further.
Challenges in Mass Production
Scalability
Once a prototype is approved, scaling up production becomes the next challenge.
Increasing production volume often requires re-evaluation of the manufacturing process to find more efficient methods.
This can involve investing in automated machinery, developing new production lines, or enhancing existing facilities.
Ensuring consistent quality while scaling up is crucial to maintain product integrity.
Cost Management
Mass-producing fiber-reinforced resin products can be expensive.
The cost of raw materials, energy, labor, and manufacturing facilities can quickly add up.
Manufacturers must find ways to optimize processes, reduce waste, and negotiate better terms with suppliers to keep costs manageable.
Implementing lean manufacturing principles and investing in cost-effective technologies can help achieve these goals.
Quality Control
Maintaining consistent quality in mass production is a challenge due to the variability in raw materials and fabrication processes.
Fiber-reinforced resins require precise control of variables such as temperature, pressure, and curing time.
Quality control systems must be robust and capable of detecting deviations promptly.
Failure to do so can result in defective products, recalls, and a tarnished brand reputation.
Environmental Concerns
Sustainability
The production of fiber-reinforced resins can have environmental impacts due to the use of non-renewable materials and energy-intensive processes.
As sustainability becomes a priority, manufacturers face pressure to adopt greener practices.
This might include using bio-based resins, recycling manufacturing waste, or employing energy-efficient processes.
Balancing environmental responsibility with production demands is a significant challenge.
Recycling and Disposal
Recycling fiber-reinforced resin products is complex due to the strong bonding between the fibers and the resin.
Current recycling methods are often energy-intensive and economically unfeasible on a large scale.
Finding efficient methods for recycling or safely disposing of these materials remains a key challenge.
Addressing this issue is crucial for manufacturers committed to environmental stewardship.
Conclusion
The path from prototyping to mass production of fiber-reinforced resin products is filled with challenges.
Design complexity and material behavior require careful consideration during prototyping, while scalability, cost management, and quality control are key issues in mass production.
Environmental concerns, including sustainability and recycling, add another layer of complexity.
Addressing these challenges requires industry collaboration, innovation, and a commitment to continuous improvement.
By overcoming these hurdles, manufacturers can harness the full potential of fiber-reinforced resin, delivering high-performance, lightweight products across various industries.
資料ダウンロード
QCD管理受発注クラウド「newji」は、受発注部門で必要なQCD管理全てを備えた、現場特化型兼クラウド型の今世紀最高の受発注管理システムとなります。
ユーザー登録
受発注業務の効率化だけでなく、システムを導入することで、コスト削減や製品・資材のステータス可視化のほか、属人化していた受発注情報の共有化による内部不正防止や統制にも役立ちます。
NEWJI DX
製造業に特化したデジタルトランスフォーメーション(DX)の実現を目指す請負開発型のコンサルティングサービスです。AI、iPaaS、および先端の技術を駆使して、製造プロセスの効率化、業務効率化、チームワーク強化、コスト削減、品質向上を実現します。このサービスは、製造業の課題を深く理解し、それに対する最適なデジタルソリューションを提供することで、企業が持続的な成長とイノベーションを達成できるようサポートします。
製造業ニュース解説
製造業、主に購買・調達部門にお勤めの方々に向けた情報を配信しております。
新任の方やベテランの方、管理職を対象とした幅広いコンテンツをご用意しております。
お問い合わせ
コストダウンが利益に直結する術だと理解していても、なかなか前に進めることができない状況。そんな時は、newjiのコストダウン自動化機能で大きく利益貢献しよう!
(β版非公開)