- お役立ち記事
- Characteristics and precautions of welding (fusion bonding) technology
月間77,185名の
製造業ご担当者様が閲覧しています*
*2025年2月28日現在のGoogle Analyticsのデータより
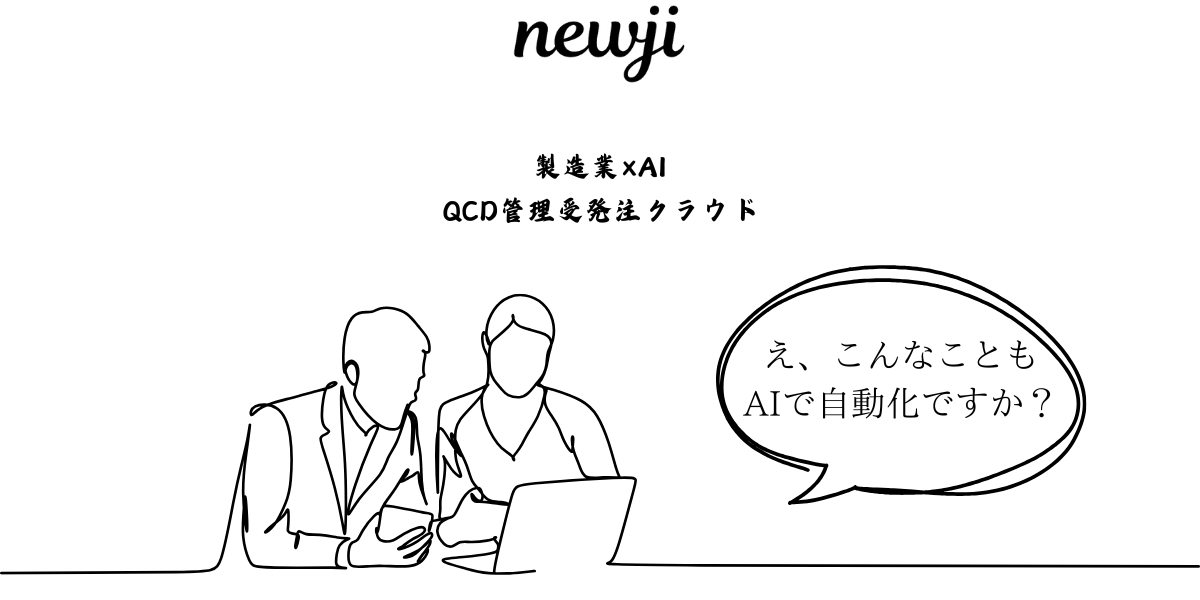
Characteristics and precautions of welding (fusion bonding) technology
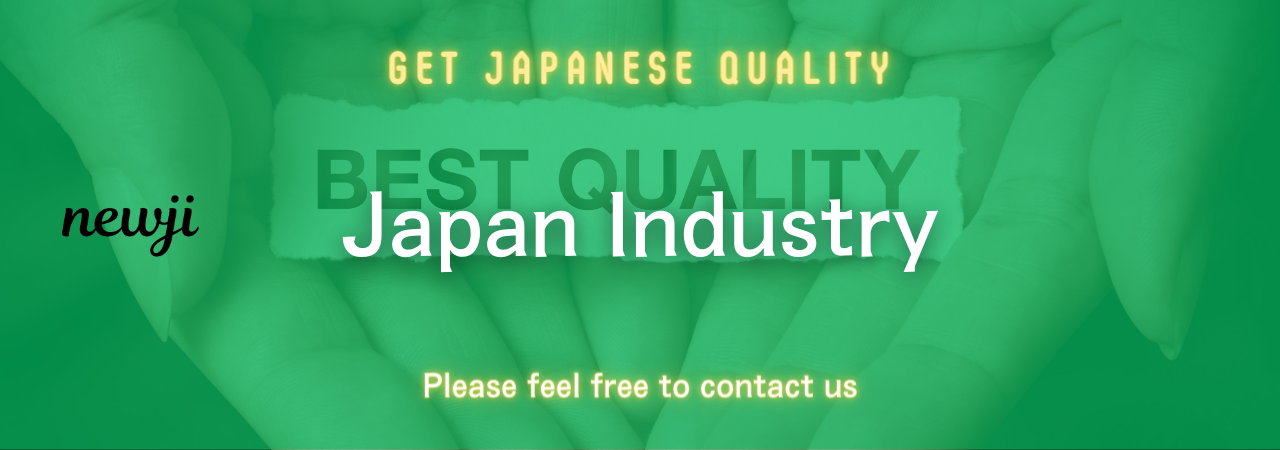
目次
Introduction to Welding Technology
Welding, also known as fusion bonding, is a critical process used in various industries to join metals and other materials.
It’s a technique that has been around for centuries and has evolved dramatically over the years.
In its essence, welding involves fusing two or more parts by applying heat, pressure, or both, to form a strong joint.
This technology is essential in construction, automotive, aerospace, and manufacturing industries, among others.
Types of Welding Processes
There are several types of welding processes, each suited for specific applications and materials.
Arc Welding
Arc welding is the most common type of welding used in industries.
It involves using an electrical arc between an electrode and the base material to melt and fuse the metals.
Subtypes of arc welding, such as Shielded Metal Arc Welding (SMAW), Gas Metal Arc Welding (GMAW), and Tungsten Inert Gas (TIG) welding, each cater to different needs based on material and thickness.
Resistance Welding
Resistance welding uses electric current and mechanical pressure to join materials.
It’s highly efficient and medium costly compared to other welding techniques.
Spot welding, a subtype, is particularly prevalent in the automotive industry for joining sheet metals quickly.
Gas Welding
Gas welding employs fuel gases and oxygen to produce the heat required for welding.
One of the most well-known forms is oxy-acetylene welding, which is versatile and applicable in repair work and metal fabrication.
Laser Welding
Laser welding uses a laser beam to provide a concentrated heat source, allowing for deep and narrow welds.
It’s particularly useful for applications requiring precision, such as in the medical and electronics fields.
Ultrasonic Welding
Ultrasonic welding is used for joining plastics and thin metals through high-frequency ultrasonic vibrations.
It’s a clean process, requiring no connective bolts or other unique additives.
Precautions in Welding
Welding is a powerful and useful technology, but it comes with specific precautionary measures to ensure safety and quality.
Personal Protective Equipment (PPE)
Welders must wear appropriate PPE, including gloves, helmets with face shields, and flame-resistant clothing.
These protect against sparks, intense heat, and harmful UV and IR radiation.
Ventilation and Fume Control
Proper ventilation is crucial in welding environments to eliminate potential exposure to dangerous fumes and gases.
Using local exhaust systems or wearing respirators can significantly reduce health risks.
Fire and Explosion Safety
Welders should be cautious of flammable materials being exposed to welding sparks.
It’s vital to maintain a clean and organized workspace, free of any fire hazards.
Electrical Safety
Since most welding equipment runs on electricity, maintaining it well and being aware of conductive surfaces is needed to prevent electric shock.
Characteristics of Welding Joints
The primary purpose of welding is to create strong, lasting joints.
Each type of weld has distinct characteristics that are suited to specific applications.
Strength
Welded joints typically have high tensile strength, making them ideal for structural applications where support under stress is essential.
Seamlessness
A well-executed weld is seamless and integrates seamlessly into the surrounding material.
It eliminates the need for additional mechanical fasteners, creating a smoother appearance and reducing weight.
Flexibility
Welding allows for flexibility in design.
This capability enables the joining of complex shapes and structures that would be difficult to achieve with conventional fastening techniques.
Cost-Effectiveness
For projects that require large-scale fabrication, welding can be a cost-effective solution due to its speed and minimal waste.
Applications of Welding Technology
Welding is pivotal across a broad spectrum of industries due to its versatility.
Construction
In construction, welding is employed for the fabrication and erection of steel structures like bridges, buildings, and pipelines.
Its strength characteristics make it ideal for handling substantial loads and stresses.
Automotive
The automotive industry relies heavily on welding for assembling car bodies, frames, and exhaust systems.
Advanced techniques such as laser welding are used to achieve precision and reliability.
Aerospace
In the aerospace industry, welding is essential for creating lightweight, durable components from high-strength alloys.
Specialized methods ensure safety and efficiency at high altitudes.
Manufacturing
In manufacturing, welding saves time and enhances productivity by allowing the quick assembly of machinery and equipment.
Whether it’s small electronics or large-scale industrial equipment, welding is essential.
Conclusion
Welding, as a fusion bonding technology, plays a vital role in shaping the infrastructure and products we rely on every day.
With a broad range of applications and the development of advanced technologies, it continues to be a field that evolves and adapts to meet industry demands.
By understanding the different types of welding processes and adhering to safety protocols, we can harness its power effectively while ensuring the well-being of those who perform these critical tasks.
資料ダウンロード
QCD管理受発注クラウド「newji」は、受発注部門で必要なQCD管理全てを備えた、現場特化型兼クラウド型の今世紀最高の受発注管理システムとなります。
ユーザー登録
受発注業務の効率化だけでなく、システムを導入することで、コスト削減や製品・資材のステータス可視化のほか、属人化していた受発注情報の共有化による内部不正防止や統制にも役立ちます。
NEWJI DX
製造業に特化したデジタルトランスフォーメーション(DX)の実現を目指す請負開発型のコンサルティングサービスです。AI、iPaaS、および先端の技術を駆使して、製造プロセスの効率化、業務効率化、チームワーク強化、コスト削減、品質向上を実現します。このサービスは、製造業の課題を深く理解し、それに対する最適なデジタルソリューションを提供することで、企業が持続的な成長とイノベーションを達成できるようサポートします。
製造業ニュース解説
製造業、主に購買・調達部門にお勤めの方々に向けた情報を配信しております。
新任の方やベテランの方、管理職を対象とした幅広いコンテンツをご用意しております。
お問い合わせ
コストダウンが利益に直結する術だと理解していても、なかなか前に進めることができない状況。そんな時は、newjiのコストダウン自動化機能で大きく利益貢献しよう!
(β版非公開)