- お役立ち記事
- Characteristics of aluminum, selection of appropriate materials and processing methods, and key points
月間76,176名の
製造業ご担当者様が閲覧しています*
*2025年3月31日現在のGoogle Analyticsのデータより
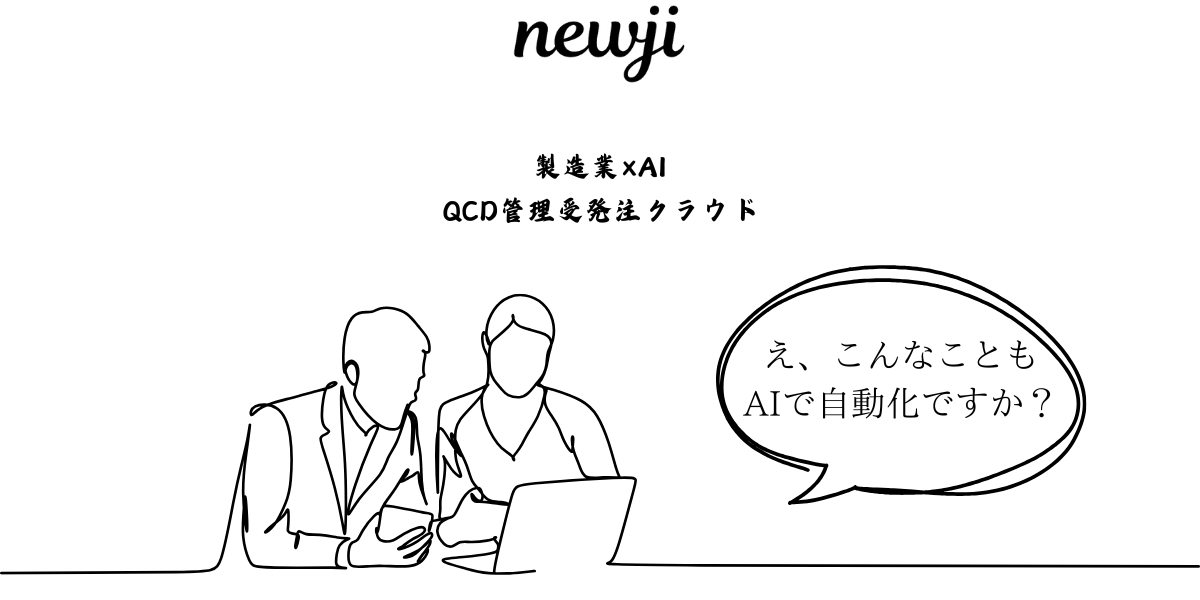
Characteristics of aluminum, selection of appropriate materials and processing methods, and key points
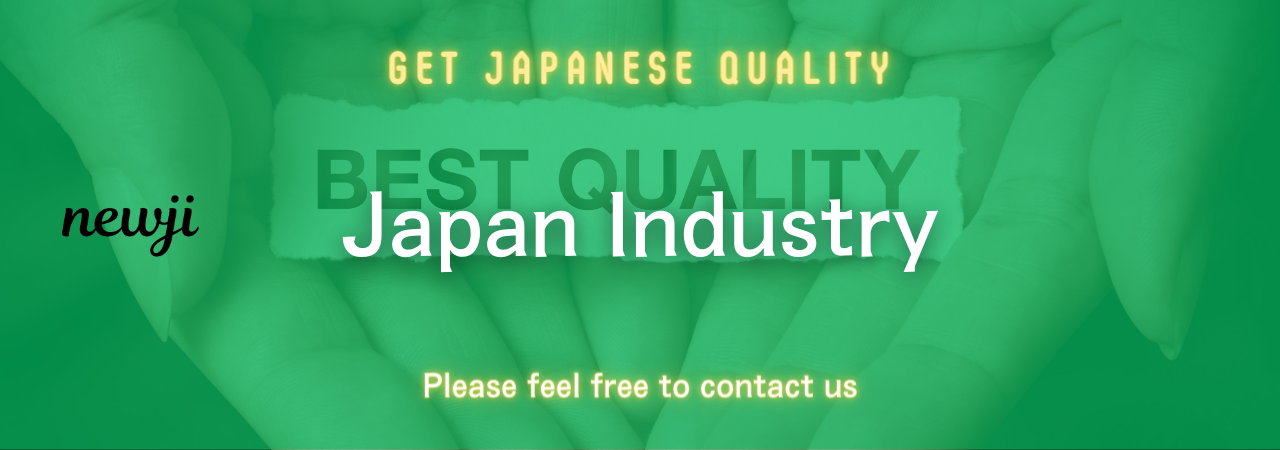
目次
Understanding the Characteristics of Aluminum
Aluminum is widely known for its unique combination of properties, making it one of the most versatile materials in the world.
Its characteristics include being lightweight, corrosion-resistant, and highly conductive.
Understanding these attributes is essential for selecting the right materials and processing methods for your project.
Aluminum’s low density is one of its most celebrated characteristics.
This makes it significantly lighter than other metals like steel, which is beneficial in industries such as automotive and aerospace, where weight reduction is crucial.
Despite being lightweight, aluminum maintains a good strength-to-weight ratio, ensuring structural integrity in various applications.
Another notable property of aluminum is its excellent resistance to corrosion.
When exposed to air, it forms a thin layer of aluminum oxide that prevents further oxidation.
This self-protecting process makes aluminum ideal for outdoor uses and products prone to moisture exposure.
Industries such as construction and marine highly value this corrosion resistance.
Aluminum is also an excellent conductor of both electricity and heat.
Its high thermal conductivity allows for efficient heat dissipation in applications like radiators and heat exchangers.
Similarly, aluminum’s electrical conductivity makes it ideal for electrical transmission lines and components.
Furthermore, aluminum is non-magnetic, enhancing its utility in electrical and electronic applications.
Selecting the Right Aluminum Material
Choosing the appropriate type of aluminum material depends on the specific requirements of the project.
Aluminum is available in various grades, each with distinct properties suited for different uses.
Aluminum Alloys
Aluminum rarely exists in its pure form for industrial use.
Instead, it is combined with other elements to form alloys that enhance its natural properties.
Common aluminum alloy groups include the 1000, 3000, 5000, 6000, and 7000 series, each with unique strengths and applications.
The 1000 series is the purest form of aluminum, containing 99% or higher aluminum content.
It is highly malleable and corrosion-resistant, making it suitable for chemical and food processing industries.
The 3000 series is known for its excellent corrosion resistance and moderate strength.
It contains manganese, enhancing its workability and making it suitable for manufacturing beverage cans and chemical equipment.
The 5000 series alloys are characterized by magnesium content.
These alloys have good weldability and corrosion resistance, making them ideal for marine applications and architecture.
The 6000 series, primarily composed of magnesium and silicon, is renowned for its versatility and machinability.
It is commonly used in construction and automotive applications due to its good corrosion resistance and mechanical properties.
Lastly, the 7000 series features zinc as the primary alloying element.
These high-strength alloys are extensively used in aerospace applications where toughness is pivotal.
Understanding Processing Methods
Proper processing is key to maximizing the benefits of aluminum in any application.
Different processes can be employed depending on the intended use.
Forming and Shaping
Forming processes include bending, drawing, and rolling, which transform aluminum sheets and plates into various shapes.
These processes leverage aluminum’s malleability, allowing for complex designs and structures.
Machining
Machining processes such as drilling, milling, and turning are crucial for creating precise and intricate components.
Aluminum’s soft nature makes it easy to machine, as it poses less resistance and wear on cutting tools.
Welding
Aluminum welding requires specialized techniques due to its high thermal conductivity and oxide layer.
TIG (tungsten inert gas) welding is commonly used, offering a high-quality finish and strong welds.
MIG (metal inert gas) welding is also employed for thicker materials requiring faster welding speeds.
Surface Treatment
Surface treatment processes are vital for enhancing the durability and aesthetic appeal of aluminum products.
Anodizing is a popular surface finish that increases corrosion resistance and allows for coloring.
Powder coating is another method that provides a decorative finish and improves surface protection.
Key Points to Remember
When working with aluminum, several key points should be considered to ensure optimal results.
First, evaluate the specific application needs before selecting an aluminum alloy.
Consider factors such as strength, corrosion resistance, and machinability.
Second, during processing, always account for aluminum’s high thermal conductivity when welding and machining.
Use techniques and tools appropriate for aluminum to avoid damage or compromised integrity.
Finally, surface treatments not only enhance appearance but also extend the lifespan of aluminum products by adding protective layers against environmental factors.
Understanding these characteristics and considerations will guide you in making informed decisions when selecting aluminum for your projects.
By leveraging aluminum’s unique properties and processing methods, you can achieve cost-effective, durable, and high-quality solutions across a variety of industries.
資料ダウンロード
QCD管理受発注クラウド「newji」は、受発注部門で必要なQCD管理全てを備えた、現場特化型兼クラウド型の今世紀最高の受発注管理システムとなります。
ユーザー登録
受発注業務の効率化だけでなく、システムを導入することで、コスト削減や製品・資材のステータス可視化のほか、属人化していた受発注情報の共有化による内部不正防止や統制にも役立ちます。
NEWJI DX
製造業に特化したデジタルトランスフォーメーション(DX)の実現を目指す請負開発型のコンサルティングサービスです。AI、iPaaS、および先端の技術を駆使して、製造プロセスの効率化、業務効率化、チームワーク強化、コスト削減、品質向上を実現します。このサービスは、製造業の課題を深く理解し、それに対する最適なデジタルソリューションを提供することで、企業が持続的な成長とイノベーションを達成できるようサポートします。
製造業ニュース解説
製造業、主に購買・調達部門にお勤めの方々に向けた情報を配信しております。
新任の方やベテランの方、管理職を対象とした幅広いコンテンツをご用意しております。
お問い合わせ
コストダウンが利益に直結する術だと理解していても、なかなか前に進めることができない状況。そんな時は、newjiのコストダウン自動化機能で大きく利益貢献しよう!
(β版非公開)