- お役立ち記事
- Checklist for purchasing departments to prevent supply chain disruptions
月間76,176名の
製造業ご担当者様が閲覧しています*
*2025年3月31日現在のGoogle Analyticsのデータより
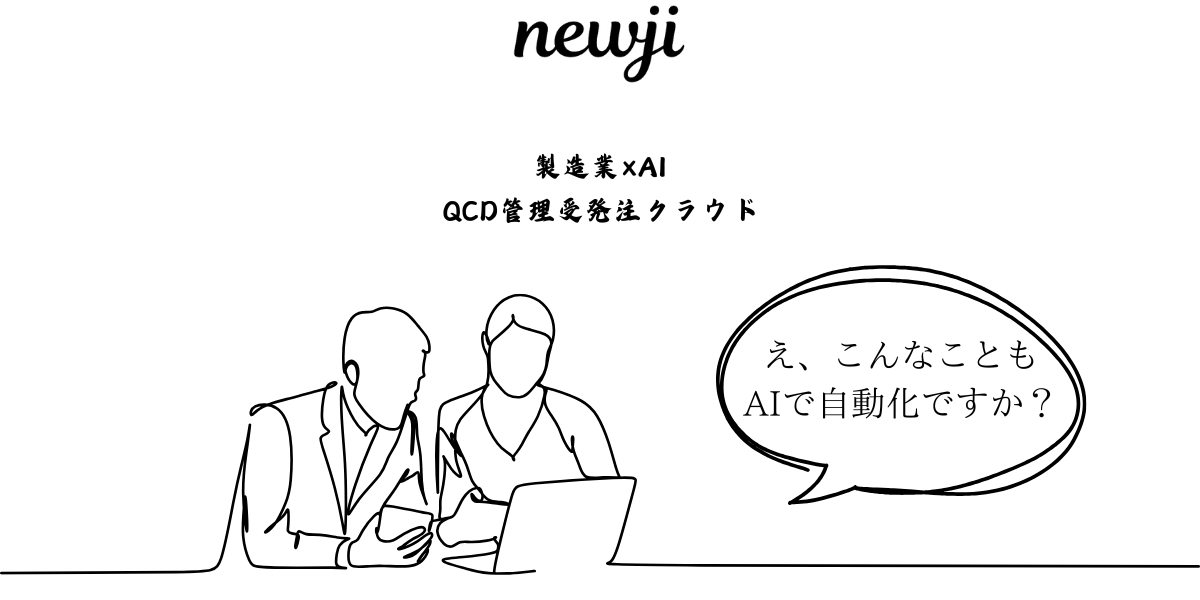
Checklist for purchasing departments to prevent supply chain disruptions
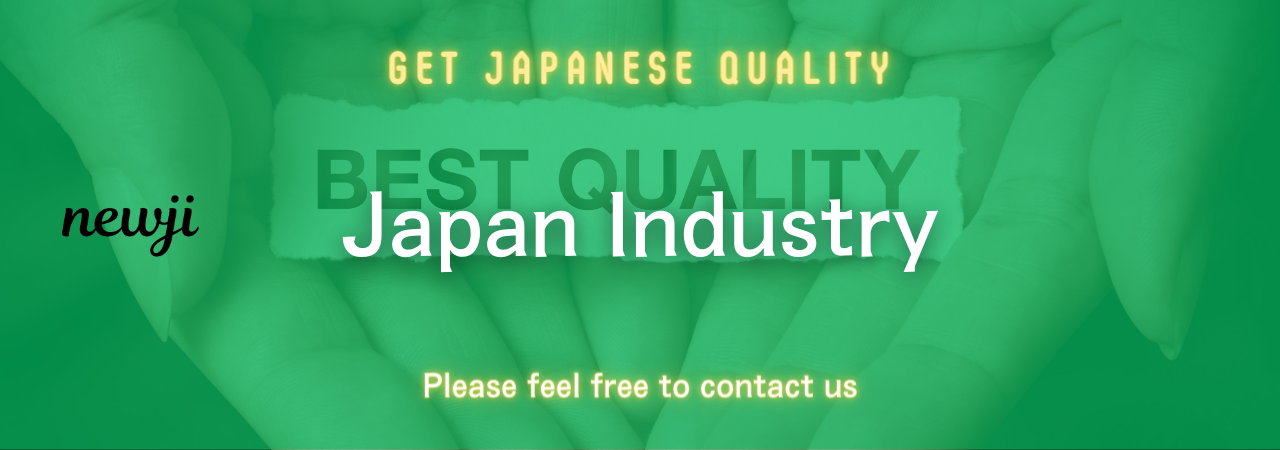
目次
Understanding the Importance of a Reliable Supply Chain
In today’s fast-paced business environment, ensuring an uninterrupted supply chain is crucial for the success of any company.
A well-functioning supply chain ensures that products reach their destination on time and in good condition.
However, disruptions in the supply chain can lead to increased costs, delayed deliveries, and customer dissatisfaction.
For purchasing departments, having a checklist to prevent supply chain disruptions is vital.
Assessing Supplier Reliability
One of the first things that purchasing departments should do is assess the reliability of their suppliers.
When evaluating suppliers, consider their track record for delivering goods on time and their ability to meet quality standards consistently.
It’s also essential to check their financial stability to ensure they can fulfill long-term contracts.
Being proactive in communicating with suppliers can help in identifying and resolving potential issues before they escalate.
Establishing a regular communication schedule allows both parties to stay updated on shipment statuses and any potential delays.
Implementing a Risk Management Strategy
A comprehensive risk management strategy is another key component for preventing supply chain disruptions.
Begin by identifying risks that could impact the supply chain, such as natural disasters, political instability, or manufacturing mishaps.
Once identified, create contingency plans that outline steps to take should these risks become realities.
Consider developing relationships with multiple suppliers for the same product.
This diversification minimizes the risk of disruption if one supplier faces challenges.
Additionally, having backup suppliers on hand ensures that the company can quickly transition if necessary.
Forecasting Demand Accurately
Accurate demand forecasting plays a critical role in maintaining a stable supply chain.
Using advanced analytics and historical data, companies can predict future demands more accurately.
This allows businesses to order the right amount of inventory, thus avoiding overstocking or stockouts, both of which can disrupt the supply chain.
Close collaboration with sales and marketing departments helps purchasing departments gather insights into upcoming promotions or shifts in consumer behavior.
These insights enable better forecasting and inventory planning.
Utilizing Technology for Efficiency
Embracing technology is essential for an efficient supply chain.
Modern software solutions can track inventory levels, manage order statuses, and analyze logistical data for improved decision-making.
Automating parts of the supply chain can also increase efficiency and reduce human error.
Implementing an Enterprise Resource Planning (ERP) system can centralize data and streamline operations.
With access to real-time information, purchasing departments can make informed decisions quickly and mitigate potential disruptions before they occur.
Establishing Strong Relationships
Building strong relationships with suppliers, vendors, and logistics partners is crucial for preventing supply chain issues.
A strong relationship means better collaboration and communication, which leads to quicker resolutions in case of disruptions.
Organizing regular meetings and joint planning sessions ensures alignment with partners.
Transparency about business goals and challenges can foster mutual trust, leading to a more resilient supply chain.
Regularly Reviewing Performance Metrics
Monitoring performance metrics is vital for maintaining an efficient supply chain.
Metrics such as on-time delivery rates, inventory turnover, and lead times should be routinely evaluated.
By analyzing these metrics, purchasing departments can identify bottlenecks and areas for improvement.
Implementing a continuous improvement program ensures that past mistakes are learned from and that processes are consistently optimized.
Feedback from other departments, such as sales and operations, can provide valuable insights into areas that require attention.
Training and Development
Investing in the training and development of staff is key to building a robust supply chain.
Ensuring that team members are knowledgeable about industry best practices, new technologies, and risk management strategies enables them to handle disruptions more effectively.
Encouraging cross-departmental training can also provide insights into how different parts of the business operate.
This holistic understanding can lead to better communication and collaboration across all levels of the company.
Conclusion
Preventing supply chain disruptions requires a proactive approach and a robust strategy.
By assessing supplier reliability, implementing risk management strategies, and utilizing technology, purchasing departments can ensure a smooth and efficient supply chain.
Regularly reviewing performance metrics and developing strong relationships with partners further fortify the supply chain against potential disruptions.
Investing in staff training ensures that employees are well-equipped to tackle any challenges that arise.
Adopting these practices can significantly reduce the risk of supply chain disruptions, leading to increased customer satisfaction and business success.
資料ダウンロード
QCD管理受発注クラウド「newji」は、受発注部門で必要なQCD管理全てを備えた、現場特化型兼クラウド型の今世紀最高の受発注管理システムとなります。
ユーザー登録
受発注業務の効率化だけでなく、システムを導入することで、コスト削減や製品・資材のステータス可視化のほか、属人化していた受発注情報の共有化による内部不正防止や統制にも役立ちます。
NEWJI DX
製造業に特化したデジタルトランスフォーメーション(DX)の実現を目指す請負開発型のコンサルティングサービスです。AI、iPaaS、および先端の技術を駆使して、製造プロセスの効率化、業務効率化、チームワーク強化、コスト削減、品質向上を実現します。このサービスは、製造業の課題を深く理解し、それに対する最適なデジタルソリューションを提供することで、企業が持続的な成長とイノベーションを達成できるようサポートします。
製造業ニュース解説
製造業、主に購買・調達部門にお勤めの方々に向けた情報を配信しております。
新任の方やベテランの方、管理職を対象とした幅広いコンテンツをご用意しております。
お問い合わせ
コストダウンが利益に直結する術だと理解していても、なかなか前に進めることができない状況。そんな時は、newjiのコストダウン自動化機能で大きく利益貢献しよう!
(β版非公開)