- お役立ち記事
- Checklist for reviewing the role played by the purchasing department in the manufacturing industry
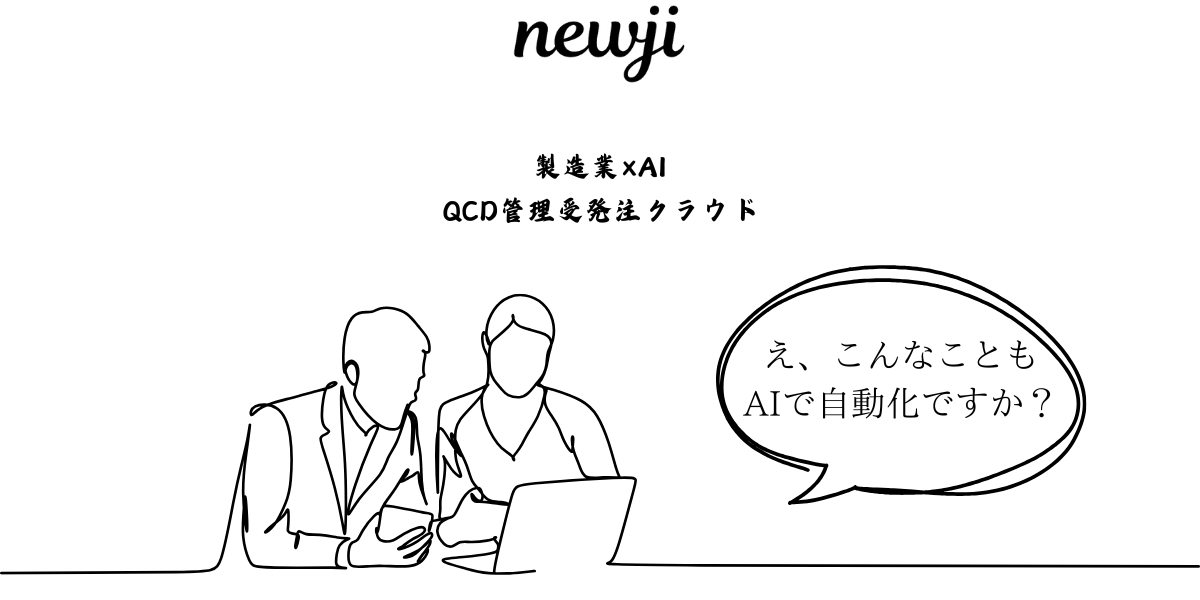
Checklist for reviewing the role played by the purchasing department in the manufacturing industry
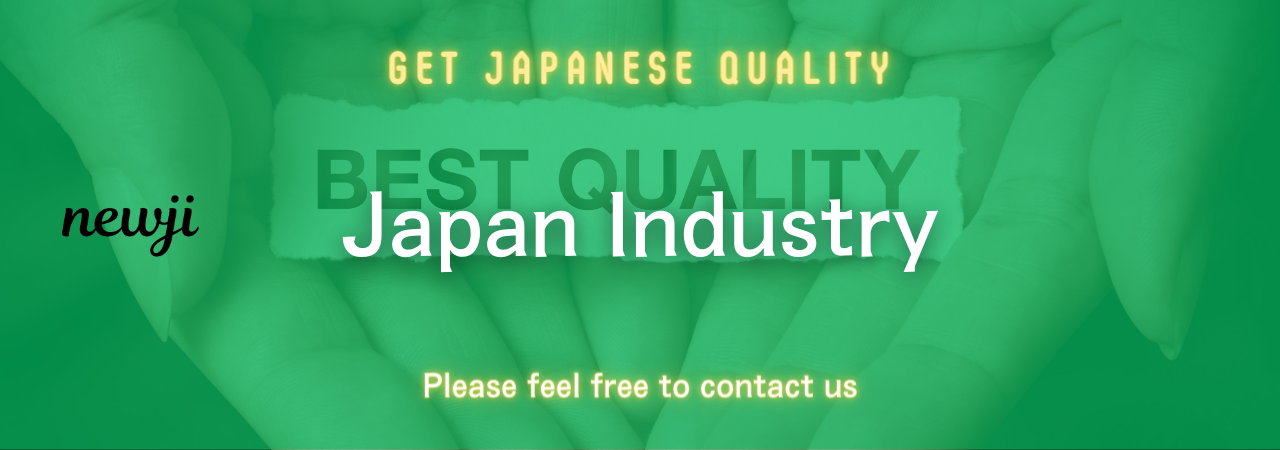
目次
Understanding the Role of the Purchasing Department
The purchasing department plays a crucial role in the manufacturing industry.
It is responsible for acquiring the raw materials and services necessary to produce goods.
This department ensures that the production processes are uninterrupted by procuring materials efficiently and cost-effectively.
Moreover, it establishes strong relationships with suppliers to secure favorable terms and prices.
A well-functioning purchasing department not only contributes to cost savings but also ensures the quality and timeliness of the materials procured.
By evaluating suppliers and negotiating contracts, the purchasing team directly impacts the overall success of the manufacturing operation.
Knowing the pivotal role this department plays, it becomes essential to periodically review its performance and processes.
Checklist for Reviewing the Purchasing Department
When reviewing the role of the purchasing department in the manufacturing industry, it is important to focus on key areas that greatly influence its efficiency and effectiveness.
Here is a checklist to guide you through the assessment process:
1. Supplier Selection and Management
One of the primary responsibilities of the purchasing department is the selection and management of suppliers.
Ensure that the department has a structured process for evaluating and selecting suppliers.
Look for qualities such as reliability, quality, and cost-effectiveness.
It is also essential that there is a system in place for monitoring supplier performance to ensure consistency in meeting quality standards and delivery schedules.
2. Cost Management
Cost management is a critical aspect of the purchasing department’s function.
Review the strategies implemented by the department to achieve cost savings.
Evaluate how effectively they engage in negotiations to secure the best possible prices for the materials needed.
Also, assess how well they forecast and anticipate market trends to make informed purchasing decisions.
3. Inventory Management
Effective inventory management is crucial to avoid overstocking or understocking, both of which can have financial implications.
Check whether the purchasing department uses inventory management systems to keep track of stock levels.
Ensure they utilize data analytics and forecasting to maintain optimal inventory levels and reduce holding costs.
4. Quality Assurance
The purchasing department contributes to the overall product quality by sourcing high-quality materials.
Confirm that there are rigorous quality control measures in place.
This includes testing samples, obtaining certifications, and conducting regular audits to verify that suppliers meet the required quality standards.
5. Purchase Order Management
Efficient handling of purchase orders is pivotal in maintaining the flow of materials.
Examine the department’s system for creating, approving, and managing purchase orders.
Ensure that the system minimizes errors and delays in the ordering process.
6. Compliance and Risk Management
Purchasing departments must adhere to various regulations and standards.
Evaluate their processes for ensuring compliance with legal and ethical sourcing standards.
Additionally, assess how well risks, such as supplier bankruptcy or geopolitical instability, are identified and mitigated.
7. Supplier Relationship Management
The relationship with suppliers is a critical aspect of the purchasing department’s operations.
Look into how relationships with key suppliers are managed and cultivated.
Evaluate whether there is effective communication and a collaborative approach to solving any issues that arise.
Benefits of a Thorough Review
Conducting a thorough review of the purchasing department brings numerous benefits to manufacturing operations.
By identifying strengths and areas for improvement, manufacturers can optimize purchasing decisions, leading to cost savings and improved production outcomes.
Additionally, ensuring compliance and risk management can protect the company from potential legal issues and disruptions.
A well-reviewed purchasing department also contributes to building stronger supplier relationships, which can improve negotiation outcomes and ensure a stable supply chain.
The emphasis on quality assurance ensures that only the best materials are used in production, enhancing the product quality and reputation of the manufacturing company.
Conclusion
The purchasing department is integral to the success of any manufacturing operation.
By regularly reviewing its roles and processes through a comprehensive checklist, manufacturers can ensure that their purchasing activities contribute positively to the overall business objectives.
Optimizing supplier relationships, managing costs, and ensuring compliance are key focus areas for a productive purchasing department.
Therefore, manufacturers must invest time in evaluating their purchasing departments, as this diligence will lead to long-term benefits such as increased efficiency, cost reduction, and product quality enhancement.
資料ダウンロード
QCD調達購買管理クラウド「newji」は、調達購買部門で必要なQCD管理全てを備えた、現場特化型兼クラウド型の今世紀最高の購買管理システムとなります。
ユーザー登録
調達購買業務の効率化だけでなく、システムを導入することで、コスト削減や製品・資材のステータス可視化のほか、属人化していた購買情報の共有化による内部不正防止や統制にも役立ちます。
NEWJI DX
製造業に特化したデジタルトランスフォーメーション(DX)の実現を目指す請負開発型のコンサルティングサービスです。AI、iPaaS、および先端の技術を駆使して、製造プロセスの効率化、業務効率化、チームワーク強化、コスト削減、品質向上を実現します。このサービスは、製造業の課題を深く理解し、それに対する最適なデジタルソリューションを提供することで、企業が持続的な成長とイノベーションを達成できるようサポートします。
オンライン講座
製造業、主に購買・調達部門にお勤めの方々に向けた情報を配信しております。
新任の方やベテランの方、管理職を対象とした幅広いコンテンツをご用意しております。
お問い合わせ
コストダウンが利益に直結する術だと理解していても、なかなか前に進めることができない状況。そんな時は、newjiのコストダウン自動化機能で大きく利益貢献しよう!
(Β版非公開)