- お役立ち記事
- Checkpoints and systemization recommendations to prevent mistakes in procurement operations
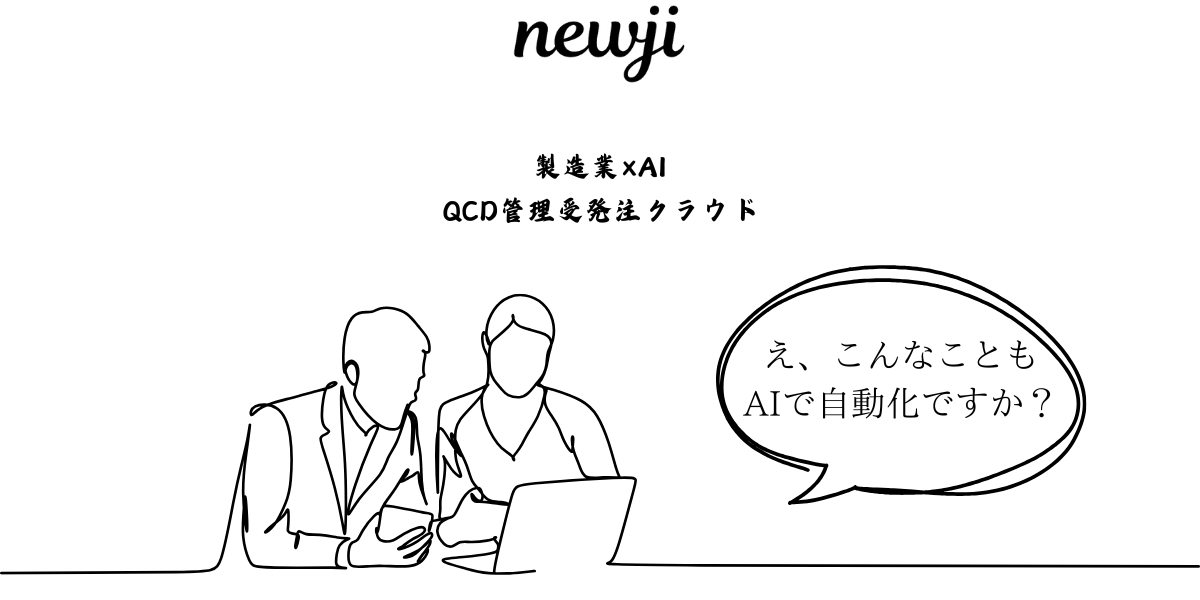
Checkpoints and systemization recommendations to prevent mistakes in procurement operations
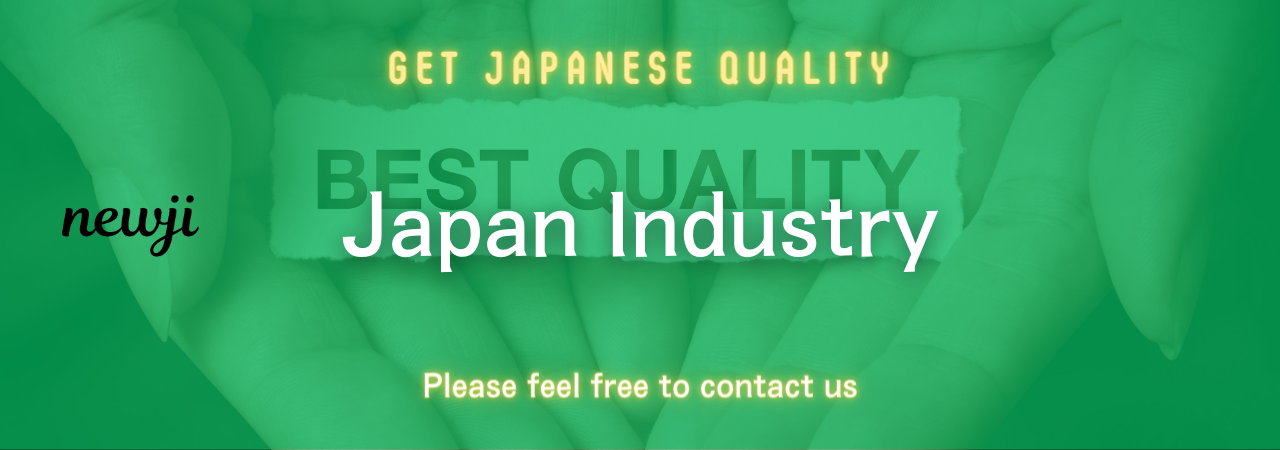
目次
Understanding Procurement Operations
Procurement is a critical business function that involves sourcing, acquiring, and managing the goods and services that an organization needs to fulfill its operations.
The process encompasses various activities such as identifying needs, selecting suppliers, negotiating contracts, and managing supplier relationships.
With so many moving parts, there is a high potential for mistakes that can lead to financial loss, inefficiencies, or damage to the company’s reputation.
Common Mistakes in Procurement
To address these potential pitfalls, it’s essential to recognize common mistakes that occur in procurement operations.
One typical error is the lack of a clear procurement strategy.
Without a well-defined strategy, procurement teams may make ad-hoc decisions that can lead to inconsistencies, missed opportunities, or missed savings.
Another common mistake is inadequate supplier evaluation.
Organizations may fail to conduct thorough due diligence, resulting in partnerships with unreliable or non-compliant suppliers.
Mismanaged supplier relationships can lead to supply chain disruptions and quality issues.
Procurement teams often encounter challenges with contract management.
Without meticulous attention to contract details, organizations may face compliance problems, unexpected costs, or contractual disputes.
Failure to monitor and review contracts regularly can be detrimental to the procurement operation’s success.
Implementing Checkpoints in Procurement
Introducing checkpoints throughout the procurement process can significantly reduce mistakes.
These checkpoints act as quality control measures to ensure that procurement activities align with the organization’s objectives and standards.
1. Establishing a Clear Strategy
The first checkpoint is the creation of a comprehensive procurement strategy.
This strategy should outline the goals, processes, and policies for procurement activities.
It should align with the broader business objectives and include guidelines for supplier selection, contract management, and risk mitigation.
2. Supplier Evaluation and Selection
Another critical checkpoint involves the evaluation and selection of suppliers.
Organizations should develop a rigorous supplier assessment process.
This process should include criteria for financial stability, compliance with industry standards, and the ability to meet delivery requirements.
By implementing a scoring system, procurement teams can objectively assess potential suppliers and make informed decisions.
3. Contract Management
An effective contract management system is vital for preventing mistakes.
Establishing a centralized repository for contracts allows for easier access and monitoring.
Setting regular review schedules ensures compliance and helps identify any changes in supplier terms or performance issues that need addressing.
4. Regular Performance Reviews
Conducting regular performance reviews with suppliers is also crucial.
These reviews should evaluate key performance indicators (KPIs) to assess supplier performance against agreed-upon standards.
Addressing any discrepancies early can prevent minor issues from escalating.
5. Risk Assessment
Lastly, incorporating a risk assessment process into procurement operations is essential.
Risk assessments should identify potential risks in the supply chain, including geopolitical, financial, and operational threats.
Developing contingency plans and risk mitigation strategies can safeguard the organization against unforeseen disruptions.
Systemization Recommendations
Systemizing procurement operations can enhance efficiency and further minimize the risk of errors.
Using technology and best practices, organizations can streamline procurement processes and achieve better outcomes.
1. Procurement Software
Implementing procurement management software can automate many manual tasks.
These systems can manage supplier data, track orders, handle contracts, and generate reports, significantly reducing human error.
Moreover, they provide valuable analytics that can guide decision-making and improve efficiency.
2. E-Procurement Solutions
E-procurement solutions facilitate electronic communication between buyers and suppliers.
This integration enables real-time updates, faster order processing, and improved transparency.
Such systems can reduce paper-based processes and enhance overall procurement collaboration.
3. Training and Development
Providing continuous training and development for procurement staff is vital.
Training programs should focus on industry best practices, new technologies, negotiation skills, and regulatory compliance.
A well-trained team is more equipped to prevent mistakes and adapt to evolving challenges.
4. Supplier Relationship Management (SRM)
Implementing a Supplier Relationship Management (SRM) system can enhance supplier cooperation and performance.
SRM systems help track interactions, manage performance metrics, and maintain supplier communication, resulting in stronger, more reliable relationships.
5. Data Management and Analytics
Utilizing data management tools and analytics can offer insights into procurement spend patterns, supplier performance, and market trends.
Analyzing this data helps optimize procurement strategies, negotiate better terms, and improve cost-saving measures.
Conclusion
In summary, preventing mistakes in procurement operations requires a combination of well-defined processes, thorough checkpoints, and an effective systemization strategy.
By establishing clear strategies, implementing technological solutions, and continuously reviewing supplier performance, organizations can mitigate risks and enhance their procurement success.
Ultimately, a proactive approach to procurement can drive efficiency and contribute significantly to the organization’s overall performance.
資料ダウンロード
QCD調達購買管理クラウド「newji」は、調達購買部門で必要なQCD管理全てを備えた、現場特化型兼クラウド型の今世紀最高の購買管理システムとなります。
ユーザー登録
調達購買業務の効率化だけでなく、システムを導入することで、コスト削減や製品・資材のステータス可視化のほか、属人化していた購買情報の共有化による内部不正防止や統制にも役立ちます。
NEWJI DX
製造業に特化したデジタルトランスフォーメーション(DX)の実現を目指す請負開発型のコンサルティングサービスです。AI、iPaaS、および先端の技術を駆使して、製造プロセスの効率化、業務効率化、チームワーク強化、コスト削減、品質向上を実現します。このサービスは、製造業の課題を深く理解し、それに対する最適なデジタルソリューションを提供することで、企業が持続的な成長とイノベーションを達成できるようサポートします。
オンライン講座
製造業、主に購買・調達部門にお勤めの方々に向けた情報を配信しております。
新任の方やベテランの方、管理職を対象とした幅広いコンテンツをご用意しております。
お問い合わせ
コストダウンが利益に直結する術だと理解していても、なかなか前に進めることができない状況。そんな時は、newjiのコストダウン自動化機能で大きく利益貢献しよう!
(Β版非公開)