- お役立ち記事
- Checkpoints for process-specific reviews
月間76,176名の
製造業ご担当者様が閲覧しています*
*2025年3月31日現在のGoogle Analyticsのデータより
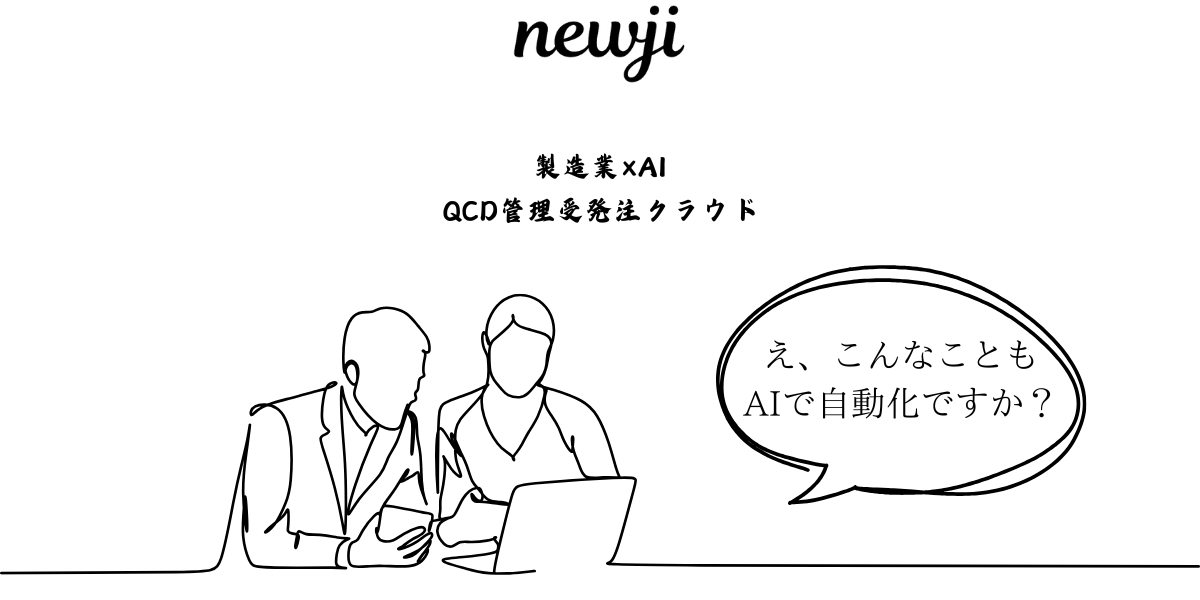
Checkpoints for process-specific reviews
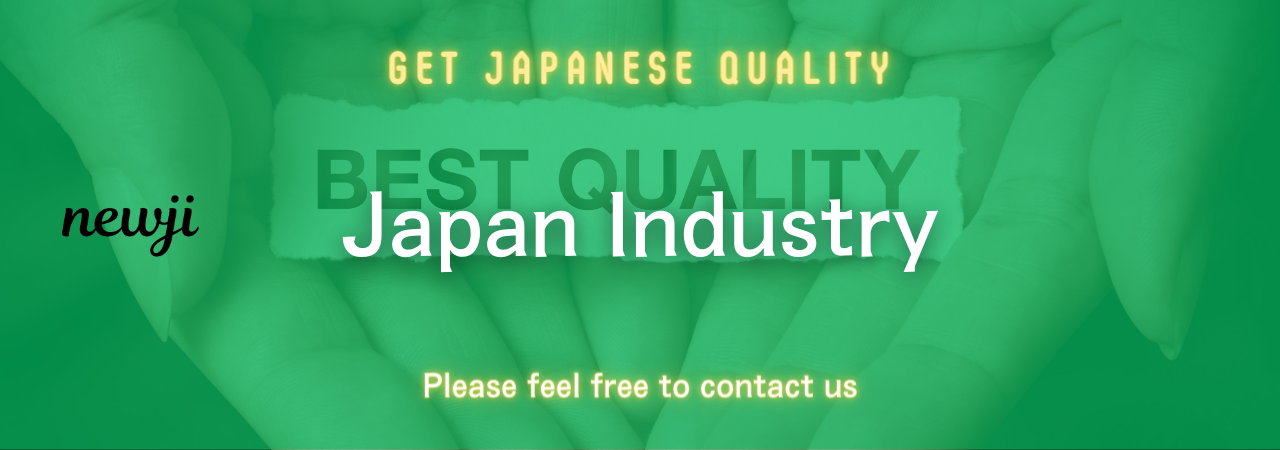
目次
Understanding Process-Specific Reviews
Process-specific reviews are an essential part of any project or operational workflow.
They focus on evaluating each phase or step in a process to ensure that it meets the required standards and objectives.
These reviews help in identifying areas for improvement, ensuring quality, and optimizing efficiency.
Whether you’re working in manufacturing, software development, or any other field, process-specific reviews are crucial for maintaining high standards and achieving success.
The Importance of Process-Specific Reviews
Process-specific reviews play a significant role in maintaining and improving the quality of outputs.
They allow teams to identify and correct errors early in the process, which saves time and resources in the long run.
By evaluating each step, organizations can ensure that processes are streamlined and effective.
Additionally, these reviews help in setting standards, training new team members, and implementing best practices.
Ultimately, process-specific reviews contribute to the overall success of projects and operations.
Key Checkpoints for Process-Specific Reviews
1. **Define Objectives Clearly**
Each process-specific review should begin with a clear definition of objectives.
Understanding the goals and desired outcomes ensures that the review is aligned with organizational priorities.
This helps in providing focus and direction throughout the review process.
2. **Evaluate Inputs and Resources**
Assessing the inputs and resources utilized in a process is a vital checkpoint.
This includes examining the quality of data, materials, and human resources.
Adequate and appropriate inputs create a strong foundation for successful outcomes.
3. **Analyze Process Steps**
Each step in the process should be analyzed for efficiency and effectiveness.
Review whether the steps are logically sequenced and if there are any redundancies.
Identifying bottlenecks or unnecessary tasks can lead to better resource allocation and improved productivity.
4. **Assess Technology and Tools**
Technology and tools used within a process should be evaluated to ensure they are up-to-date and suitable for current demands.
This includes software, machinery, and any other hardware or digital tools.
Ensuring that technology is being utilized optimally can significantly impact process performance.
5. **Review Quality Control Measures**
Quality control is a fundamental aspect of process-specific reviews.
Checkpoints should include an assessment of the measures in place to maintain or enhance quality.
This includes examining testing protocols, inspection methods, and feedback mechanisms.
6. **Monitor Performance Indicators**
Reviewing the key performance indicators (KPIs) related to a process can provide valuable insights.
These metrics should reflect the process’s effectiveness, efficiency, and quality.
Regularly monitoring and evaluating KPIs helps in making data-driven decisions and improvements.
7. **Identify Risks and Challenges**
It is crucial to identify potential risks and challenges that may impact the process.
This includes analyzing factors such as market changes, regulatory requirements, and operational dependencies.
Early identification of risks allows for proactive planning and mitigation strategies.
8. **Solicit Stakeholder Feedback**
Gathering feedback from stakeholders involved in or affected by the process can provide diverse perspectives.
This includes employees, customers, and partners who can offer insights into areas of success and those needing improvement.
Constructive feedback aids in making informed adjustments and enhancements.
Implementing Improvements Post-Review
After completing a process-specific review, it is essential to act on the findings.
Develop an action plan that prioritizes areas needing improvement.
This plan should include specific steps, timelines, and responsibilities to ensure accountability and progress.
Regularly revisit and revise processes to integrate new insights, technologies, and market developments.
Continuous improvement is key to maintaining competitive advantage and achieving organizational goals.
Best Practices for Conducting Process-Specific Reviews
– **Schedule Regular Reviews:** Establish a routine for conducting process-specific reviews to ensure consistency and relevance.
– **Use a Structured Approach:** Implement a standardized methodology to conduct reviews for clarity and reliability.
– **Engage Subject Matter Experts:** Involve individuals with expertise and experience in the relevant areas to provide informed assessments.
– **Document Findings Thoroughly:** Maintain comprehensive records of review findings and action plans for reference and accountability.
– **Encourage a Culture of Openness:** Foster an environment where team members feel comfortable sharing insights and suggestions.
Conclusion
Process-specific reviews are a critical component of organizational success.
By thoroughly evaluating each step and component within a process, teams can identify areas for improvement and implement strategies for optimization.
Through clear objectives, regular assessments, and stakeholder engagement, organizations can ensure their processes remain efficient, effective, and competitive.
Embracing process-specific reviews not only enhances quality and performance but also contributes to achieving long-term goals.
資料ダウンロード
QCD管理受発注クラウド「newji」は、受発注部門で必要なQCD管理全てを備えた、現場特化型兼クラウド型の今世紀最高の受発注管理システムとなります。
ユーザー登録
受発注業務の効率化だけでなく、システムを導入することで、コスト削減や製品・資材のステータス可視化のほか、属人化していた受発注情報の共有化による内部不正防止や統制にも役立ちます。
NEWJI DX
製造業に特化したデジタルトランスフォーメーション(DX)の実現を目指す請負開発型のコンサルティングサービスです。AI、iPaaS、および先端の技術を駆使して、製造プロセスの効率化、業務効率化、チームワーク強化、コスト削減、品質向上を実現します。このサービスは、製造業の課題を深く理解し、それに対する最適なデジタルソリューションを提供することで、企業が持続的な成長とイノベーションを達成できるようサポートします。
製造業ニュース解説
製造業、主に購買・調達部門にお勤めの方々に向けた情報を配信しております。
新任の方やベテランの方、管理職を対象とした幅広いコンテンツをご用意しております。
お問い合わせ
コストダウンが利益に直結する術だと理解していても、なかなか前に進めることができない状況。そんな時は、newjiのコストダウン自動化機能で大きく利益貢献しよう!
(β版非公開)