- お役立ち記事
- Clamp & Fastener OEM Manufacturing: Achieving High Stability
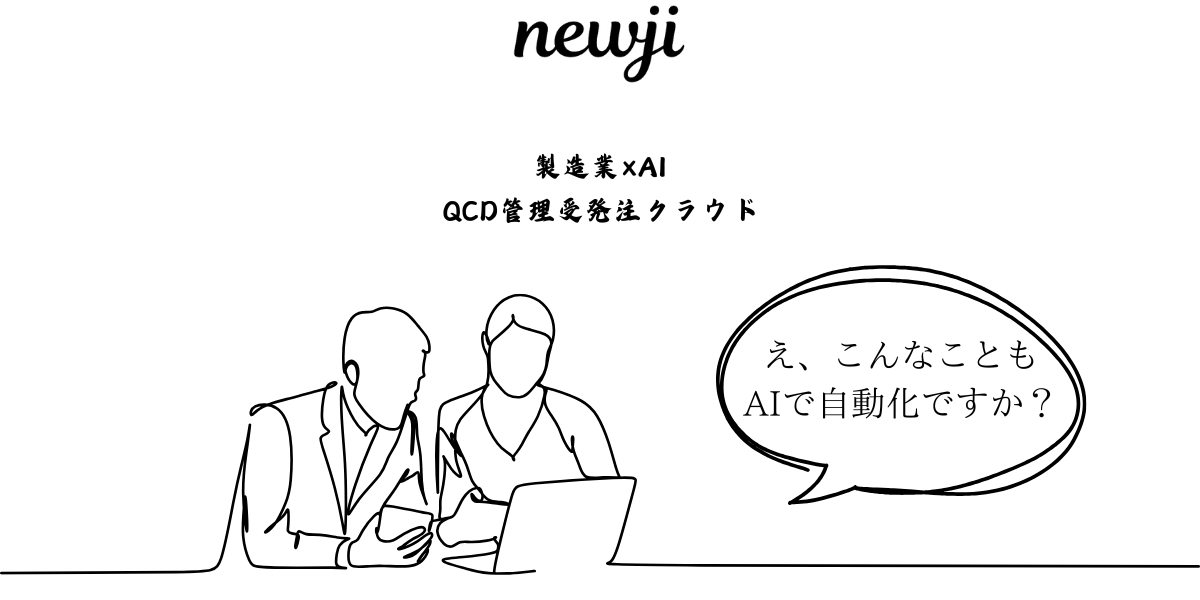
Clamp & Fastener OEM Manufacturing: Achieving High Stability
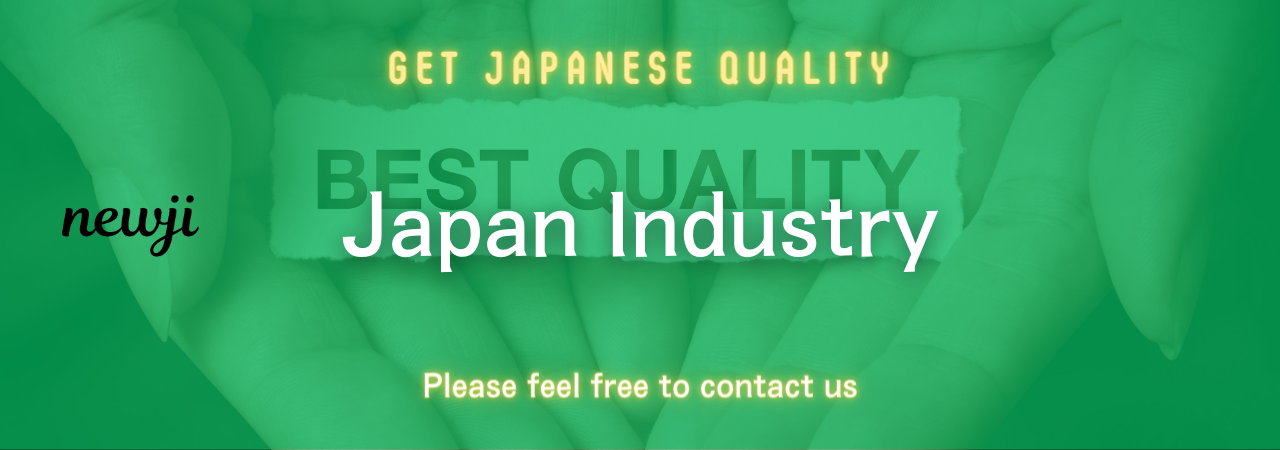
OEM manufacturing plays a critical role in the production of clamps and fasteners, products that are essential in various industries including automotive, aerospace, and construction.
These components are often small yet crucial for the stability and safety of larger structures or machines.
Given the importance of achieving high stability, this article will delve into the key considerations for successful OEM manufacturing of clamps and fasteners, from material selection to quality control processes.
目次
Understanding the Importance of Material Selection
Material selection is a foundational aspect in the manufacturing of clamps and fasteners.
Using high-quality materials ensures that the end products will be durable and capable of withstanding stress, wear, and tear.
Metals such as stainless steel, carbon steel, and alloys are commonly used due to their strength and resistance to corrosion.
However, there are circumstances where plastics or composite materials may be more suitable, particularly in situations where weight is a factor.
Choosing the right material requires an understanding of the environment in which the clamp or fastener will be used, and the forces it is expected to endure.
Strength and Durability
One of the primary considerations in material selection is strength.
For applications requiring a substantial load-bearing capacity, metals like high-tensile steel are often chosen.
Generally, fasteners and clamps made from such strong materials are used in heavy-duty applications such as in the automotive and construction sectors.
Corrosion Resistance
Clamps and fasteners exposed to harsh environmental conditions need to be highly resistant to corrosion.
Stainless steel is a popular choice for its anti-corrosion properties, making it suitable for marine applications and areas with high humidity levels.
Weight Considerations
In aerospace and other high-precision industries, the weight of each component is critical.
Using lighter materials like titanium or specialized alloys can help achieve the necessary performance without adding extra weight.
Precision Manufacturing Techniques
Another critical factor in achieving high stability in OEM-manufactured clamps and fasteners is the use of precision manufacturing techniques.
These methods ensure that each product meets exact specifications and tolerances, thereby enhancing its performance and longevity.
Computer Numerical Control (CNC) Machining
CNC machining is a staple in modern manufacturing processes.
This technology enables the production of components with high precision and consistency.
By automating the machining process, CNC machines minimize the risk of human error and ensure that each piece produced follows the exact design specifications.
Injection Molding
For plastic and composite materials, injection molding is often the method of choice.
This technique is ideal for producing large volumes of components with consistent quality. It also allows for complex geometries that would be difficult or impossible to achieve through traditional methods.
3D Printing
The rise of 3D printing has provided manufacturers with new possibilities for rapid prototyping and small batch production.
This method is particularly useful for creating custom clamps and fasteners, allowing for quick adjustments to the design based on performance testing and client feedback.
Quality Control Measures
Ensuring the high stability of clamps and fasteners also involves rigorous quality control measures.
These checks are crucial for identifying any flaws or weaknesses in the manufacturing process.
Material Testing
Material testing is typically carried out to verify that the chosen materials meet the required standards for strength, durability, and other properties.
Common tests include tensile strength testing, hardness testing, and corrosion resistance testing.
Dimensional Inspection
Dimensional inspection involves checking that each manufactured component adheres to the specified measurements and tolerances.
Tools such as calipers, micrometers, and coordinate measuring machines (CMM) are used for this purpose.
Load Testing
Load testing is conducted to ensure that clamps and fasteners can withstand the forces they are expected to endure in their intended applications.
This involves applying controlled loads to the components and observing their performance.
Real-World Performance Testing
In some cases, components may undergo real-world performance testing under simulated conditions that mimic their actual use environments.
This is particularly important for parts that are expected to perform under extreme conditions, such as high temperatures or highly corrosive environments.
Customization and Flexibility in OEM Manufacturing
One of the significant advantages of OEM manufacturing is the ability to offer customized solutions.
Different industries have unique requirements, and by providing tailor-made clamps and fasteners, manufacturers can better meet these specific needs.
Design Flexibility
OEM manufacturers often work closely with customers to develop designs that fulfill the exact requirements of a particular application.
This collaboration allows for the optimization of the component’s geometry, material, and manufacturing processes.
Batch Production
Depending on the needs of the customer, OEM manufacturers can produce small or large batches of customized components.
This flexibility is particularly beneficial for industries with varying production scales.
Integration with Existing Systems
Clamps and fasteners often need to integrate seamlessly with other parts and systems.
OEM manufacturers can design components that align perfectly with existing products, thereby ensuring a coherent and efficient assembly process.
The Importance of Supplier Partnerships
Lastly, achieving high stability in OEM-manufactured clamps and fasteners often involves building strong partnerships with reliable suppliers.
These relationships ensure a consistent supply of high-quality materials and components, which is vital for maintaining the quality of the final product.
Reliable Supply Chains
A stable supply chain is crucial for minimizing delays and disruptions in the manufacturing process.
Working with reputable suppliers ensures that materials and components are delivered on time and meet the required quality standards.
Collaborative Development
Partnerships with suppliers can also facilitate collaborative development efforts.
By sharing knowledge and expertise, manufacturers and suppliers can work together to find innovative solutions to challenges, leading to better products and more efficient processes.
OEM manufacturing of clamps and fasteners is a complex process that requires careful consideration of material selection, precision manufacturing techniques, quality control measures, and supplier partnerships.
By focusing on these critical aspects, manufacturers can produce high-stability components that meet the stringent demands of various industries, ensuring safety and reliability in their applications.
資料ダウンロード
QCD調達購買管理クラウド「newji」は、調達購買部門で必要なQCD管理全てを備えた、現場特化型兼クラウド型の今世紀最高の購買管理システムとなります。
ユーザー登録
調達購買業務の効率化だけでなく、システムを導入することで、コスト削減や製品・資材のステータス可視化のほか、属人化していた購買情報の共有化による内部不正防止や統制にも役立ちます。
NEWJI DX
製造業に特化したデジタルトランスフォーメーション(DX)の実現を目指す請負開発型のコンサルティングサービスです。AI、iPaaS、および先端の技術を駆使して、製造プロセスの効率化、業務効率化、チームワーク強化、コスト削減、品質向上を実現します。このサービスは、製造業の課題を深く理解し、それに対する最適なデジタルソリューションを提供することで、企業が持続的な成長とイノベーションを達成できるようサポートします。
オンライン講座
製造業、主に購買・調達部門にお勤めの方々に向けた情報を配信しております。
新任の方やベテランの方、管理職を対象とした幅広いコンテンツをご用意しております。
お問い合わせ
コストダウンが利益に直結する術だと理解していても、なかなか前に進めることができない状況。そんな時は、newjiのコストダウン自動化機能で大きく利益貢献しよう!
(Β版非公開)