- お役立ち記事
- Classification and characteristics of grinding
Classification and characteristics of grinding
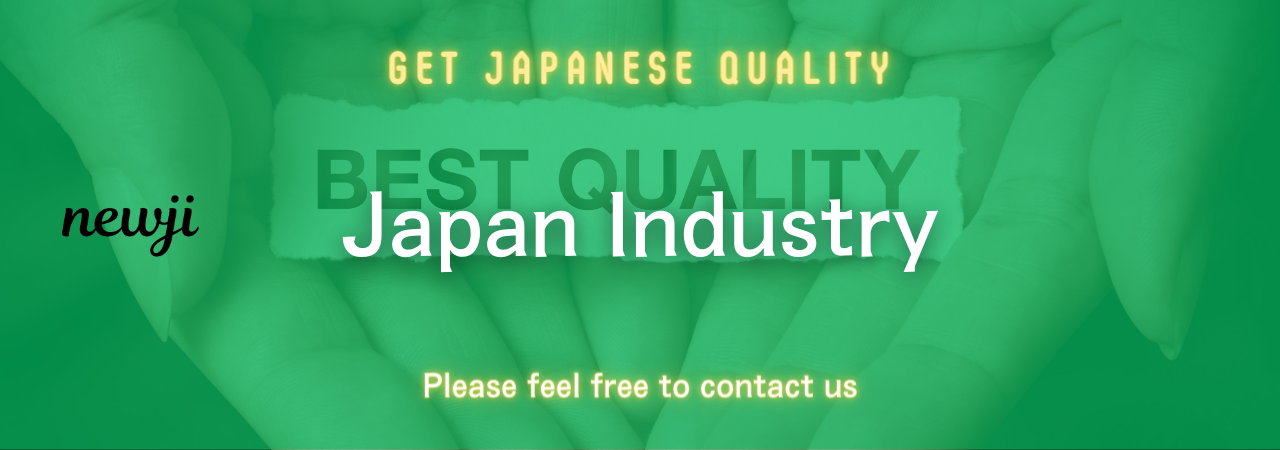
目次
Introduction to Grinding
Grinding is a critical process in numerous industries, including manufacturing, engineering, and construction.
It involves the use of abrasive particles to remove material from a workpiece, resulting in a smooth and precise finish.
Understanding the classification and characteristics of grinding is essential for selecting the appropriate method and tools for specific tasks.
Types of Grinding Processes
There are several types of grinding processes, each designed for different applications and materials.
The main types include surface grinding, cylindrical grinding, centerless grinding, internal grinding, and tool and cutter grinding.
Surface Grinding
Surface grinding is one of the most common grinding processes.
It involves the use of a rotating abrasive wheel to produce a smooth finish on flat surfaces.
The workpiece is held in place by a magnetic chuck or secured to a fixture, and the wheel removes small amounts of material to achieve the desired surface finish.
Surface grinding is ideal for achieving tight tolerances and precise dimensions.
Cylindrical Grinding
Cylindrical grinding is used to shape the outside surface of a cylindrical part.
The process is performed on cylindrical components such as shafts, rolls, and various engine parts.
There are two main types of cylindrical grinding: external and internal.
External cylindrical grinding machines grind the outer surface of a component, while internal grinding machines are used to finish the inside of a hollow area.
This method can produce highly accurate parts with fine surface finishes.
Centerless Grinding
Centerless grinding is a versatile method for grinding small, cylindrical parts without the need for centers or chucks.
Instead, the workpiece is supported by a work rest blade positioned between a rotating grinding wheel and a smaller regulating wheel.
This method allows for high throughput, as it is continuous and can accommodate longer parts.
Centerless grinding is often used in the production of precision tubes, rods, and bars for various industries.
Internal Grinding
Internal grinding is a method used to finish the inside diameter of a cylindrical or conical object.
It is particularly useful for high-precision components like bearings, bushings, and sleeves.
The process leverages smaller grinding wheels that can fit inside the hollow space of a workpiece.
Internal grinding requires specialized equipment and skilled operators to achieve highly accurate results.
Tool and Cutter Grinding
Tool and cutter grinding involves sharpening and resharpening cutting tools.
It ensures the effective performance of tools like drill bits, milling cutters, and lathe tools.
These grinders can perform a variety of precise operations, making them indispensable in machine shops and manufacturing facilities.
Characteristics of Grinding
Grinding techniques exhibit distinct characteristics that determine the suitability of processes and materials.
Material Removal Rates
The material removal rate in grinding is generally lower than in other machining processes like milling or turning.
However, it produces finer finishes and tighter tolerances.
The grinding wheel’s speed, feed rate, and depth of cut are critical variables that influence material removal rates.
Surface Finish
Grinding is known for yielding superior surface finishes.
Proper selection of the grinding wheel, along with accurate control of the process parameters, can result in mirror-like finishes.
The surface roughness is highly dependent on the grit size of the abrasive used.
Tolerances
Grinding processes can achieve extremely tight tolerances, often within microns.
The precision of grinding is due to the small depth of cuts that can be applied, which helps maintain high accuracy levels throughout the process.
Heat Generation
One of the significant challenges in grinding is managing heat generation.
The friction produced during grinding can lead to temperature rises that may cause thermal damage to both the workpiece and the grinding wheel.
Coolants and lubricants are crucial in controlling temperatures and maintaining the integrity of both the tools and materials involved.
Wheel Wear and Tool Life
Grinding wheels gradually wear down over time.
Understanding the wear characteristics is essential to optimize tool life and maintain consistent quality.
Regular dressing and truing of the wheel help restore its sharpness and balance, prolonging its effective use.
Choosing a Grinding Process
Selecting the right grinding process depends on several factors, including the material properties, required tolerances, surface finish requirements, and production volume.
A thorough understanding of the workpiece material, such as its hardness, brittleness, and ductility, is essential in selecting the appropriate type of grinder and grinding wheel.
Material Considerations
Different materials respond uniquely to grinding.
Hard materials like carbide and ceramics require special abrasives, such as diamond wheels, whereas softer metals like aluminum can be ground with conventional abrasive wheels.
The mechanical properties of the workpiece material greatly influence the choice of grinding method.
Application Needs
The requirements of the finished component determine the choice of grinding process.
High precision parts may necessitate cylindrical or internal grinding, while simpler applications might use surface grinding for efficiency.
Production volume plays a role; high-volume production often benefits from automated grinding solutions for cost-effectiveness.
Conclusion
Grinding is a crucial process in achieving fine finishes and precise dimensions in modern manufacturing.
Understanding the different classifications and characteristics allows for the selection of the best method suited to a particular task.
With careful process control, the challenges of heat management, material choice, and equipment wear can be effectively managed to produce optimal results.
資料ダウンロード
QCD調達購買管理クラウド「newji」は、調達購買部門で必要なQCD管理全てを備えた、現場特化型兼クラウド型の今世紀最高の購買管理システムとなります。
ユーザー登録
調達購買業務の効率化だけでなく、システムを導入することで、コスト削減や製品・資材のステータス可視化のほか、属人化していた購買情報の共有化による内部不正防止や統制にも役立ちます。
NEWJI DX
製造業に特化したデジタルトランスフォーメーション(DX)の実現を目指す請負開発型のコンサルティングサービスです。AI、iPaaS、および先端の技術を駆使して、製造プロセスの効率化、業務効率化、チームワーク強化、コスト削減、品質向上を実現します。このサービスは、製造業の課題を深く理解し、それに対する最適なデジタルソリューションを提供することで、企業が持続的な成長とイノベーションを達成できるようサポートします。
オンライン講座
製造業、主に購買・調達部門にお勤めの方々に向けた情報を配信しております。
新任の方やベテランの方、管理職を対象とした幅広いコンテンツをご用意しております。
お問い合わせ
コストダウンが利益に直結する術だと理解していても、なかなか前に進めることができない状況。そんな時は、newjiのコストダウン自動化機能で大きく利益貢献しよう!
(Β版非公開)