- お役立ち記事
- Clean Booth Implementation for Enhanced Quality Control in Manufacturing
Clean Booth Implementation for Enhanced Quality Control in Manufacturing
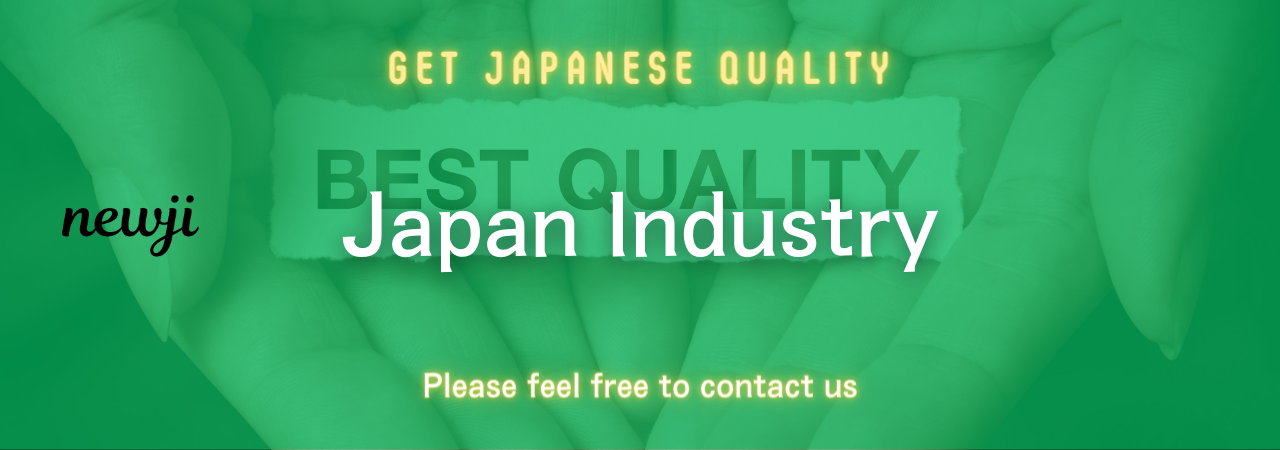
In the world of manufacturing, ensuring high-quality products is paramount. Products that do not meet stringent quality standards can lead to costly recalls, customer dissatisfaction, and even damage to a company’s reputation. One highly effective way to maintain and improve quality control in the manufacturing process is by implementing a clean booth. Clean booths play a crucial role in preventing contamination, ensuring the integrity of the manufacturing process, and ultimately enhancing product quality.
目次
What is a Clean Booth?
A clean booth, also known as a cleanroom booth, is a controlled environment designed to minimize the presence of airborne particles, contaminants, and pollutants. These contaminants can negatively affect the manufacturing process and the quality of the final product. Clean booths are equipped with specialized filtration systems, controlled airflow, and often specific temperature and humidity controls to maintain a sterile and clean environment.
The primary function of a clean booth is to protect sensitive manufacturing processes and products from contamination. This is particularly important in industries such as pharmaceuticals, electronics, aerospace, and food processing where even the smallest contaminants can have significant consequences.
Benefits of Implementing a Clean Booth
Improved Product Quality
One of the most significant benefits of implementing a clean booth is the substantial improvement in product quality. By providing a controlled environment, clean booths eliminate many of the variables that can lead to defects and inconsistencies in products. This is particularly crucial in industries where precision and reliability are essential, such as semiconductor manufacturing and medical device production.
Enhanced Process Control
Clean booths allow for better control over the manufacturing environment, making it easier to maintain consistent process parameters. This enhanced control reduces the likelihood of production errors and variations, ensuring that each product meets the required specifications. Improved process control also leads to higher yields and less waste, making the overall manufacturing process more efficient and cost-effective.
Reduced Contamination Risk
Contaminants such as dust, microbes, and chemical vapors can have a detrimental impact on product quality. Clean booths are designed to minimize these risks by using high-efficiency particulate air (HEPA) filters and other advanced filtration technologies. These filters capture and remove airborne particles, creating an environment that is significantly cleaner than a typical manufacturing setting.
Compliance with Industry Standards
Many industries have strict regulatory requirements regarding cleanliness and contamination control. Implementing a clean booth can help manufacturers comply with these standards, reducing the risk of non-compliance and potential legal issues. Adhering to industry standards also enhances a company’s reputation and can lead to increased customer trust and satisfaction.
Increased Production Efficiency
A clean booth creates an environment where manufacturing processes can be optimized for maximum efficiency. By minimizing contamination and maintaining consistent process parameters, clean booths reduce downtime and maintenance requirements. This leads to faster production times and increased overall productivity.
Key Components of a Clean Booth
Filtration Systems
The heart of any clean booth is its filtration system. HEPA filters and ultra-low particulate air (ULPA) filters are commonly used to remove airborne particles as small as 0.3 microns. These filters are essential for maintaining a clean environment and preventing contamination.
Controlled Airflow
Clean booths utilize controlled airflow to ensure that air moves in a specific pattern, preventing airborne particles from settling on surfaces. Laminar airflow, where air moves in parallel paths, is often used in clean booths to reduce turbulence and maintain a clean environment.
Temperature and Humidity Control
Maintaining the right temperature and humidity levels is crucial for preventing contamination and ensuring product quality. Clean booths are equipped with systems to precisely control these parameters, creating an optimal environment for sensitive manufacturing processes.
Construction Materials
The materials used to construct a clean booth are chosen to minimize particle generation and contamination. Smooth, non-porous surfaces such as stainless steel and specialized coatings are commonly used to make cleaning easier and reduce the risk of contamination.
Steps to Implementing a Clean Booth
Assessment and Planning
The first step in implementing a clean booth is to conduct a thorough assessment of your manufacturing process and identify areas where contamination is a concern. This will help you determine the specific requirements for your clean booth, including the necessary filtration systems, airflow patterns, and environmental controls.
Design and Construction
Once you have identified your needs, the next step is to design and construct the clean booth. This involves selecting the appropriate materials, filtration systems, and environmental controls to meet your specific requirements. Working with experienced professionals in clean booth design and construction can help ensure that your clean booth meets industry standards and provides the necessary level of contamination control.
Installation and Testing
After the clean booth has been constructed, it must be installed and tested to ensure that it meets the required specifications. This includes testing the filtration systems, airflow patterns, and environmental controls to verify that they are functioning correctly and providing the necessary level of contamination control.
Training and Implementation
Proper training for personnel is essential to the successful implementation of a clean booth. Employees must be trained on the proper procedures for working in the clean booth, including gowning, cleaning, and maintenance protocols. This will help ensure that the clean booth remains effective in preventing contamination and maintaining product quality.
Conclusion
Implementing a clean booth is a highly effective way to enhance quality control in manufacturing. By providing a controlled environment free from airborne contaminants, clean booths help improve product quality, enhance process control, reduce contamination risk, and increase production efficiency.
With the right planning, design, and implementation, a clean booth can be a valuable asset to any manufacturing operation, helping to ensure that products meet the highest standards of quality and reliability. As the demand for high-quality products continues to grow, investing in a clean booth is an investment in the future success of your manufacturing business.
資料ダウンロード
QCD調達購買管理クラウド「newji」は、調達購買部門で必要なQCD管理全てを備えた、現場特化型兼クラウド型の今世紀最高の購買管理システムとなります。
ユーザー登録
調達購買業務の効率化だけでなく、システムを導入することで、コスト削減や製品・資材のステータス可視化のほか、属人化していた購買情報の共有化による内部不正防止や統制にも役立ちます。
NEWJI DX
製造業に特化したデジタルトランスフォーメーション(DX)の実現を目指す請負開発型のコンサルティングサービスです。AI、iPaaS、および先端の技術を駆使して、製造プロセスの効率化、業務効率化、チームワーク強化、コスト削減、品質向上を実現します。このサービスは、製造業の課題を深く理解し、それに対する最適なデジタルソリューションを提供することで、企業が持続的な成長とイノベーションを達成できるようサポートします。
オンライン講座
製造業、主に購買・調達部門にお勤めの方々に向けた情報を配信しております。
新任の方やベテランの方、管理職を対象とした幅広いコンテンツをご用意しております。
お問い合わせ
コストダウンが利益に直結する術だと理解していても、なかなか前に進めることができない状況。そんな時は、newjiのコストダウン自動化機能で大きく利益貢献しよう!
(Β版非公開)