- お役立ち記事
- Clean room basics, foreign matter countermeasures, and optimal management “visualization technology” and know-how practical course
月間76,176名の
製造業ご担当者様が閲覧しています*
*2025年3月31日現在のGoogle Analyticsのデータより
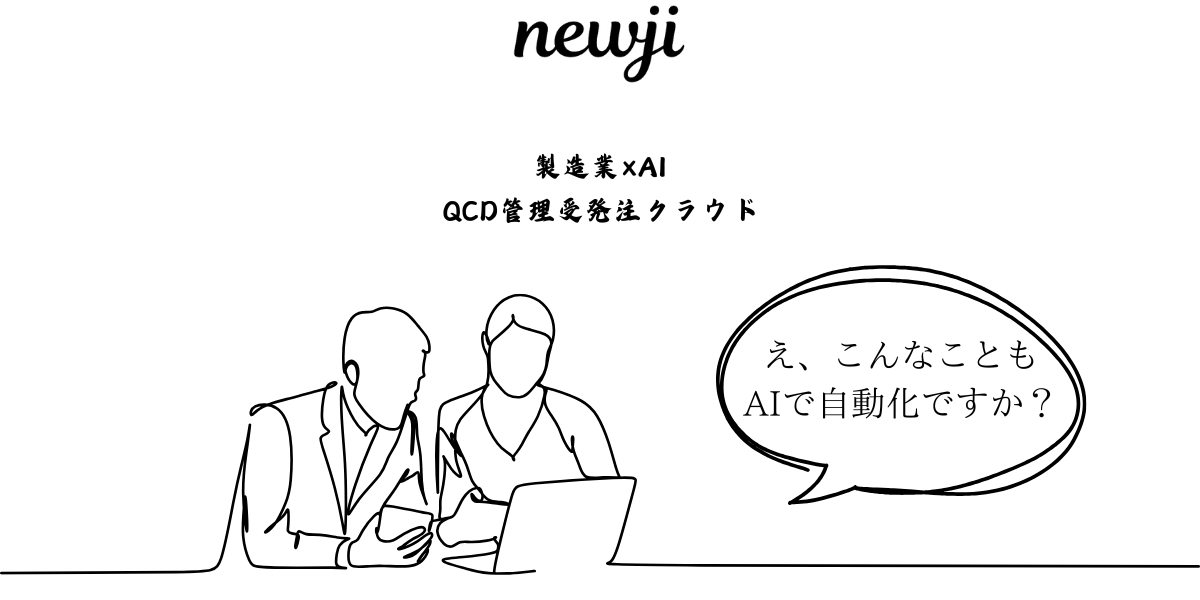
Clean room basics, foreign matter countermeasures, and optimal management “visualization technology” and know-how practical course
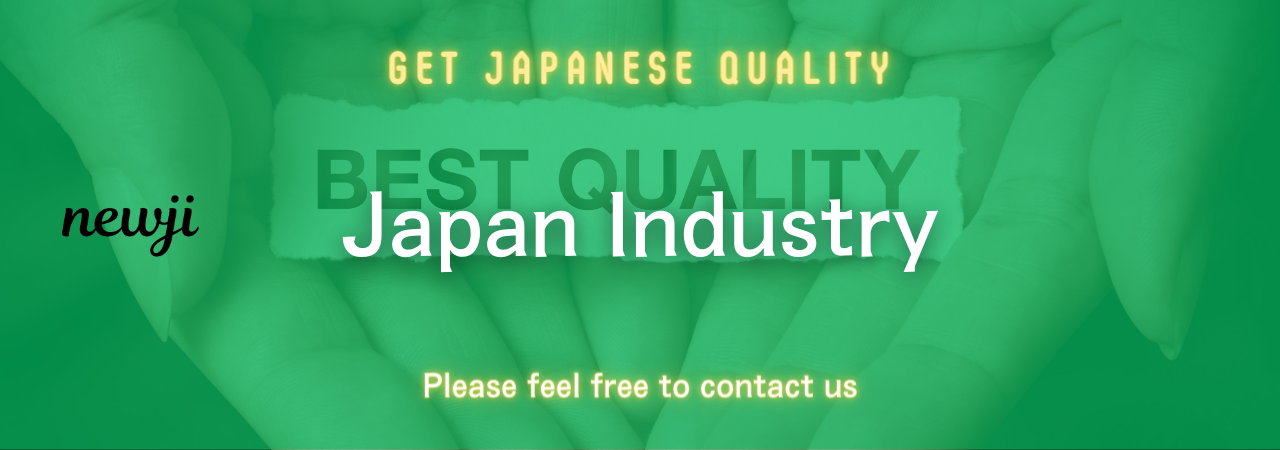
目次
Understanding Clean Room Basics
Clean rooms are specialized environments designed to maintain extremely low levels of airborne particles and contaminants.
They are essential in various industries, such as pharmaceuticals, biotechnology, electronics, and aerospace, where even the smallest impurity can compromise product quality and safety.
To appreciate the significance of clean rooms, it’s crucial to start with the basics.
The primary objective of a clean room is to control contamination.
This is achieved through strict regulation of air filtration, temperature, humidity, and air pressure.
Clean rooms are classified by the maximum allowable particulate concentration per cubic meter, often following guidelines like ISO 14644-1.
For instance, an ISO Class 5 clean room allows only 100 particles per cubic meter, each no more than 0.5 microns in size.
Understanding these parameters is the foundation of managing a clean room environment effectively.
Key Elements of Clean Room Design
A well-designed clean room incorporates various critical elements.
First, the HVAC (heating, ventilation, and air conditioning) system is pivotal in controlling air quality and maintaining the required clean room class.
High-efficiency particulate air (HEPA) or ultra-low penetration air (ULPA) filters are employed to capture even the smallest particles.
Second, the construction materials and surfaces within a clean room are chosen to minimize particle generation and facilitate cleaning.
Smooth, nonporous materials are best for walls, floors, and ceilings, while furnishings are designed to resist particle accumulation.
Third, the airflow pattern—whether unidirectional or non-unidirectional—plays an essential role in the displacement and removal of contaminants.
Understanding these design aspects helps in optimizing a clean room to meet specific industry needs.
Foreign Matter Countermeasures
Foreign matter in clean rooms can originate from various sources, including personnel, equipment, and processes.
Effectively controlling these contaminants is crucial to maintaining a clean room’s integrity.
Personnel Management
The human factor is a significant source of contamination.
Appropriate attire, such as clean room suits, masks, gloves, and shoe covers, is mandatory to minimize particle emission from skin and clothing.
Personnel should also be trained in proper clean room entry and exit procedures to reduce contamination risk.
Equipment and Process Control
Equipment used in clean rooms must be regularly cleaned and maintained to prevent particle generation.
Selecting equipment with smooth surfaces and minimal moving parts can reduce the risk of contamination.
Additionally, implementing rigorous protocols for sterilization and decontamination of tools and surfaces is vital.
Environmental Monitoring
Continuously monitoring the clean room environment helps identify potential contamination sources.
Air quality sensors and particle counters provide real-time data, enabling swift corrective actions if contaminant levels exceed acceptable limits.
Optimal Management Through Visualization Technology
Technological advancements have paved the way for innovative solutions in clean room management.
Visualization technology offers significant benefits in monitoring and optimizing clean room operations.
Real-time Monitoring
Advanced visualization tools provide a comprehensive picture of the clean room’s air quality and environmental conditions.
Real-time data on particulate levels, temperature, humidity, and air pressure allows for immediate identification and rectification of deviations.
This proactive approach ensures that clean room conditions remain within the prescribed limits.
Data Analytics and Predictive Maintenance
Visualization technology coupled with data analytics provides insights into patterns and trends in clean room operations.
By analyzing historical data, managers can identify potential issues before they manifest as significant problems.
Predictive maintenance ensures equipment is serviced at optimal intervals, minimizing downtimes and reducing contamination risks.
Improved Decision-Making
Visualization technology not only aids in maintaining clean room standards but also enhances decision-making processes.
With clear visual representations of data, stakeholders can make informed choices about process improvements, resource allocation, and quality assurance.
This level of insight is invaluable for maintaining high standards and ensuring regulatory compliance.
Practical Know-How for Clean Room Management
Managing a clean room requires a comprehensive understanding of both theoretical principles and practical know-how.
Here are a few practical steps that can be implemented to ensure optimal clean room management.
Regular Training and Audits
Personnel should receive regular training on clean room protocols and best practices.
Routine audits of procedures and processes help reinforce training and identify areas for improvement.
A well-informed team is essential for maintaining a high-functioning clean room environment.
Standard Operating Procedures (SOPs)
Detailed SOPs should be developed for every aspect of clean room management, from gowning procedures to equipment maintenance.
These documents ensure consistency and compliance, serving as references for staff at all levels.
Continuous Improvement
Clean room management is an ongoing process of improvement.
Regularly reviewing performance metrics, identifying inefficiencies, and implementing corrective measures lead to enhanced productivity and product quality.
Adopting a mindset of continuous improvement ensures that clean room operations remain state-of-the-art.
In conclusion, understanding clean room basics, implementing foreign matter countermeasures, utilizing visualization technology, and fostering practical know-how are keys to achieving optimal clean room management.
By staying informed and proactive, industries can maintain the highest standards of cleanliness and efficiency, ensuring the safety and quality of their products.
資料ダウンロード
QCD管理受発注クラウド「newji」は、受発注部門で必要なQCD管理全てを備えた、現場特化型兼クラウド型の今世紀最高の受発注管理システムとなります。
ユーザー登録
受発注業務の効率化だけでなく、システムを導入することで、コスト削減や製品・資材のステータス可視化のほか、属人化していた受発注情報の共有化による内部不正防止や統制にも役立ちます。
NEWJI DX
製造業に特化したデジタルトランスフォーメーション(DX)の実現を目指す請負開発型のコンサルティングサービスです。AI、iPaaS、および先端の技術を駆使して、製造プロセスの効率化、業務効率化、チームワーク強化、コスト削減、品質向上を実現します。このサービスは、製造業の課題を深く理解し、それに対する最適なデジタルソリューションを提供することで、企業が持続的な成長とイノベーションを達成できるようサポートします。
製造業ニュース解説
製造業、主に購買・調達部門にお勤めの方々に向けた情報を配信しております。
新任の方やベテランの方、管理職を対象とした幅広いコンテンツをご用意しております。
お問い合わせ
コストダウンが利益に直結する術だと理解していても、なかなか前に進めることができない状況。そんな時は、newjiのコストダウン自動化機能で大きく利益貢献しよう!
(β版非公開)