- お役立ち記事
- Cleaning Basics and Troubleshooting Techniques for Manufacturing
月間76,176名の
製造業ご担当者様が閲覧しています*
*2025年3月31日現在のGoogle Analyticsのデータより
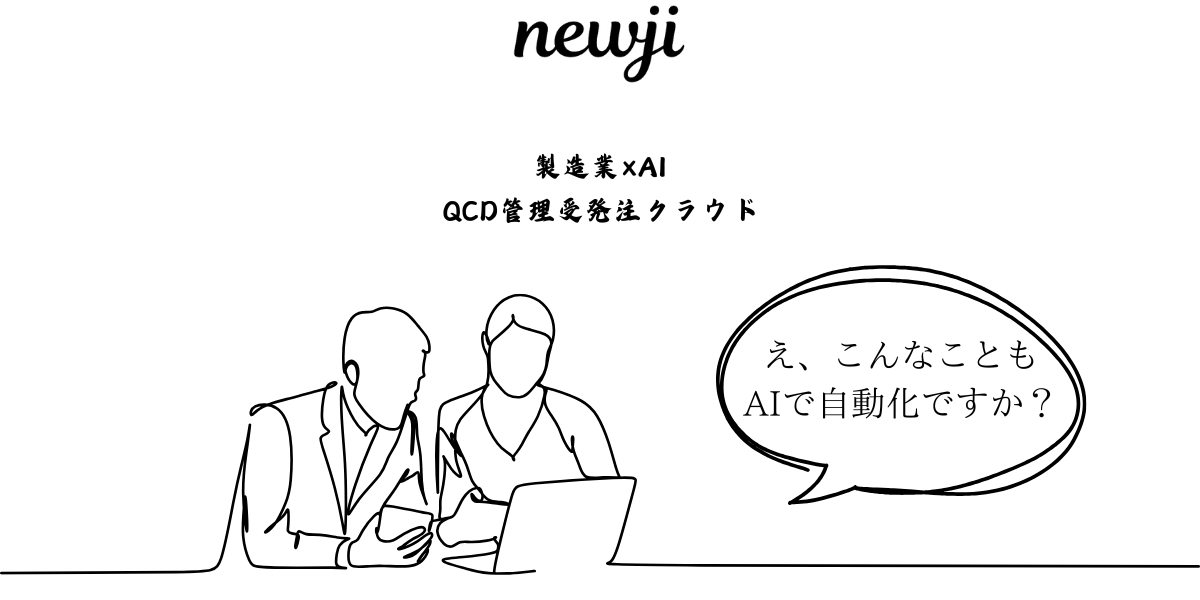
Cleaning Basics and Troubleshooting Techniques for Manufacturing
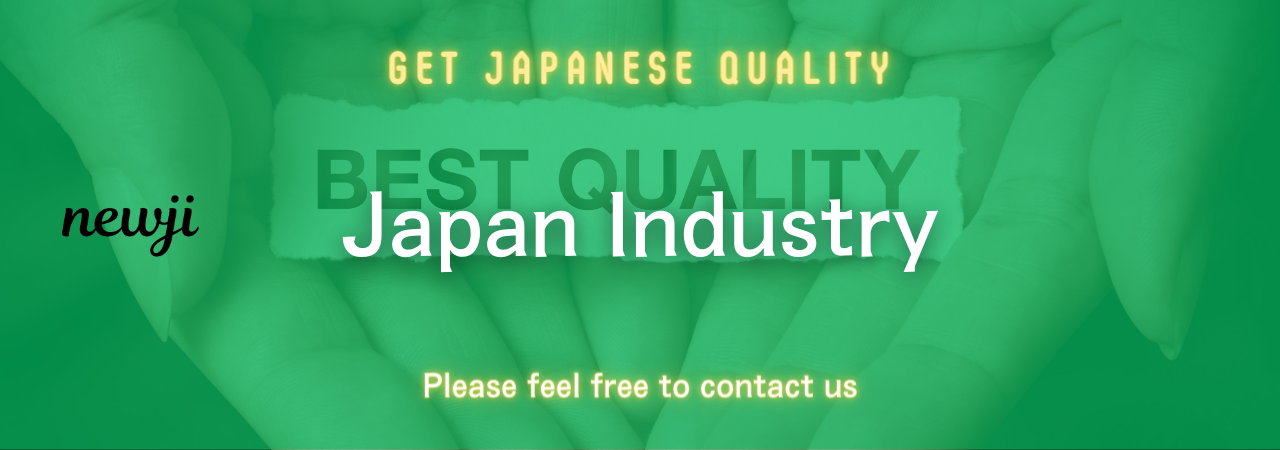
目次
Introduction to Cleaning in Manufacturing
In the manufacturing industry, cleanliness is more than just a matter of aesthetics.
It is a crucial element that significantly impacts the quality and safety of the products.
A clean manufacturing environment ensures that machinery operates efficiently, reduces the risk of contamination in products, and extends the life of equipment.
Understanding the basics of cleaning and troubleshooting techniques is essential for maintaining an effective manufacturing process.
This article will explore the fundamental aspects of cleaning in manufacturing and provide insights into troubleshooting techniques to resolve issues that may arise.
Why Cleanliness Matters in Manufacturing
Maintaining a clean manufacturing facility is vital for several reasons.
First and foremost, it ensures the production of high-quality products.
Contaminants such as dust, chemicals, or biological substances can compromise the integrity of the manufactured items, leading to defects or even product recalls.
Moreover, cleanliness in manufacturing contributes to the safety of workers.
A tidy environment reduces the likelihood of accidents, such as slips, trips, and falls, by keeping pathways clear and machinery free from obstructions.
Finally, maintaining a clean facility ensures compliance with industry standards and regulations.
Many manufacturing sectors are subject to stringent cleanliness requirements to ensure product safety, especially in industries such as food processing, pharmaceuticals, and electronics.
Basic Cleaning Techniques in Manufacturing
Effective cleaning in a manufacturing setting involves a combination of techniques tailored to the specific needs of the production environment.
Here are some basic cleaning techniques to consider:
Regular Cleaning Schedules
Establishing a regular cleaning schedule is essential to ensure consistent cleanliness.
Daily, weekly, and monthly cleaning tasks should be defined and assigned to specific personnel.
Regular cleaning helps prevent the buildup of contaminants and maintains a stable production environment.
Appropriate Cleaning Agents
Selecting the appropriate cleaning agents for various surfaces and equipment is crucial.
The choice of cleaning agents depends on the type of material to be cleaned and the nature of the contaminants.
Using the wrong cleaning agent can damage equipment or fail to remove contaminants effectively.
Effective Equipment Cleaning
Equipment should be thoroughly cleaned to prevent the accumulation of dirt, grease, and debris that can hinder performance.
Disassembling machinery for deep cleaning, if necessary, ensures that hidden areas are not neglected.
Use of Automated Cleaning Systems
Incorporating automated cleaning systems can enhance efficiency and consistency in maintaining cleanliness.
Automated systems can be programmed to clean machinery and production areas at set intervals, reducing the reliance on manual labor and minimizing human error.
Troubleshooting Cleaning Issues
Even with the best cleaning practices, issues may arise that require prompt attention and troubleshooting.
Identifying and resolving cleaning-related problems is essential to maintain a smooth production process.
Identifying Contamination Sources
One of the first steps in troubleshooting is identifying the source of contamination.
Contamination can originate from various sources, including raw materials, personnel, or the environment.
Understanding the origin of contaminants helps in developing targeted cleaning solutions.
Evaluating Cleaning Procedures
When cleaning issues occur, it is important to evaluate existing cleaning procedures.
Assess whether the current methods are adequate for the specific contaminants encountered and make necessary adjustments.
Updating cleaning protocols and retraining staff can address recurring problems effectively.
Ensuring Equipment Functionality
Malfunctioning equipment can contribute to cleanliness issues in manufacturing.
Regular maintenance checks and timely repairs of machinery are critical to ensuring that equipment functions optimally and does not become a source of contamination.
Routine checks can also prevent small issues from escalating into more significant problems.
Implementing Root Cause Analysis
Root cause analysis involves investigating and identifying the underlying reasons for a particular issue.
This method allows manufacturers to implement long-term solutions rather than just temporary fixes.
By addressing the root causes, recurring cleaning issues can be effectively minimized.
Optimizing Cleaning Practices with Technology
Advancements in technology have paved the way for innovative solutions that enhance cleaning practices in manufacturing.
Implementing these technologies can lead to smarter and more efficient cleaning processes.
Use of Sensors and Monitoring Systems
Sensors and monitoring systems can be deployed to detect contamination levels and conditions in real-time.
These systems provide valuable data that can inform decisions about cleaning frequency and methods.
Predictive analytics can also anticipate potential issues, allowing proactive measures to be taken.
Robotics in Cleaning
Robotics can automate repetitive cleaning tasks, increasing efficiency and precision.
Robotic cleaners can reach areas that are difficult for human cleaners and can operate in hazardous environments, ensuring a higher level of safety for workers.
Data-Driven Decision Making
Utilizing data collected from various cleaning processes can aid in optimizing cleaning strategies.
Analytics can identify trends and patterns, helping manufacturers make informed decisions to improve overall cleanliness.
Conclusion
Cleanliness in manufacturing is a critical component that influences product quality, safety, and compliance with regulations.
By understanding the basics of cleaning and implementing effective troubleshooting techniques, manufacturers can maintain a clean and efficient production environment.
Regular cleaning schedules, appropriate cleaning agents, and advanced technology are foundational to achieving high cleanliness standards.
Moreover, identifying contamination sources, evaluating procedures, and leveraging technology contribute significantly to resolving cleaning challenges.
By prioritizing cleanliness, manufacturers can ensure the production of high-quality products, safeguard their workforce, and uphold their industry reputation.
資料ダウンロード
QCD管理受発注クラウド「newji」は、受発注部門で必要なQCD管理全てを備えた、現場特化型兼クラウド型の今世紀最高の受発注管理システムとなります。
ユーザー登録
受発注業務の効率化だけでなく、システムを導入することで、コスト削減や製品・資材のステータス可視化のほか、属人化していた受発注情報の共有化による内部不正防止や統制にも役立ちます。
NEWJI DX
製造業に特化したデジタルトランスフォーメーション(DX)の実現を目指す請負開発型のコンサルティングサービスです。AI、iPaaS、および先端の技術を駆使して、製造プロセスの効率化、業務効率化、チームワーク強化、コスト削減、品質向上を実現します。このサービスは、製造業の課題を深く理解し、それに対する最適なデジタルソリューションを提供することで、企業が持続的な成長とイノベーションを達成できるようサポートします。
製造業ニュース解説
製造業、主に購買・調達部門にお勤めの方々に向けた情報を配信しております。
新任の方やベテランの方、管理職を対象とした幅広いコンテンツをご用意しております。
お問い合わせ
コストダウンが利益に直結する術だと理解していても、なかなか前に進めることができない状況。そんな時は、newjiのコストダウン自動化機能で大きく利益貢献しよう!
(β版非公開)