- お役立ち記事
- Cleanroom-Compatible Design Methods for Semiconductor Manufacturing Equipment
月間76,176名の
製造業ご担当者様が閲覧しています*
*2025年3月31日現在のGoogle Analyticsのデータより
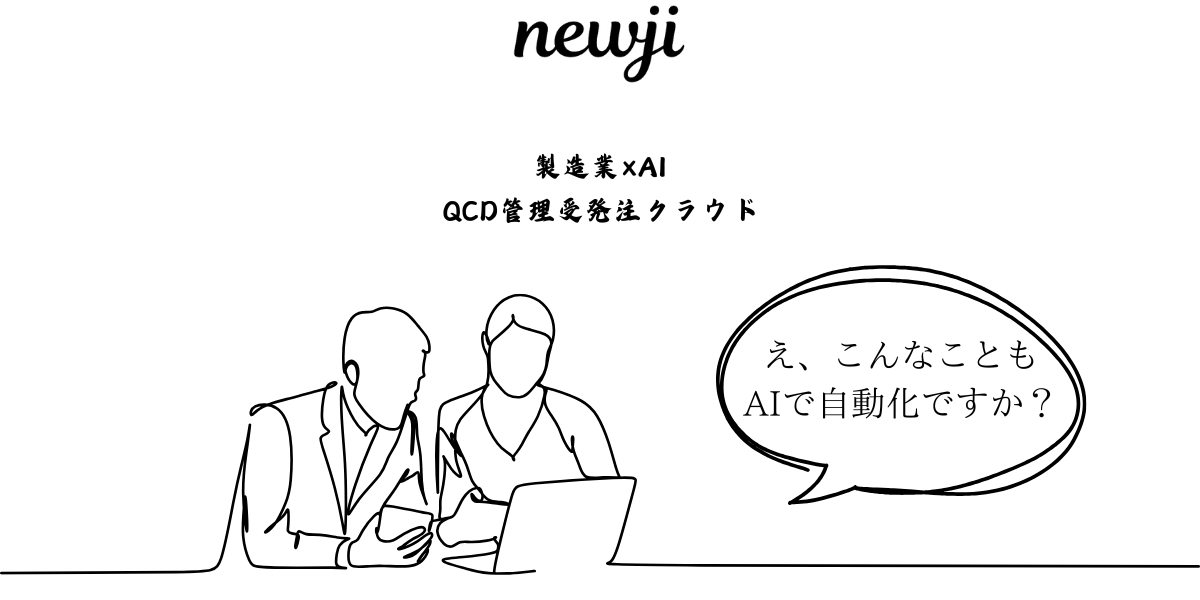
Cleanroom-Compatible Design Methods for Semiconductor Manufacturing Equipment
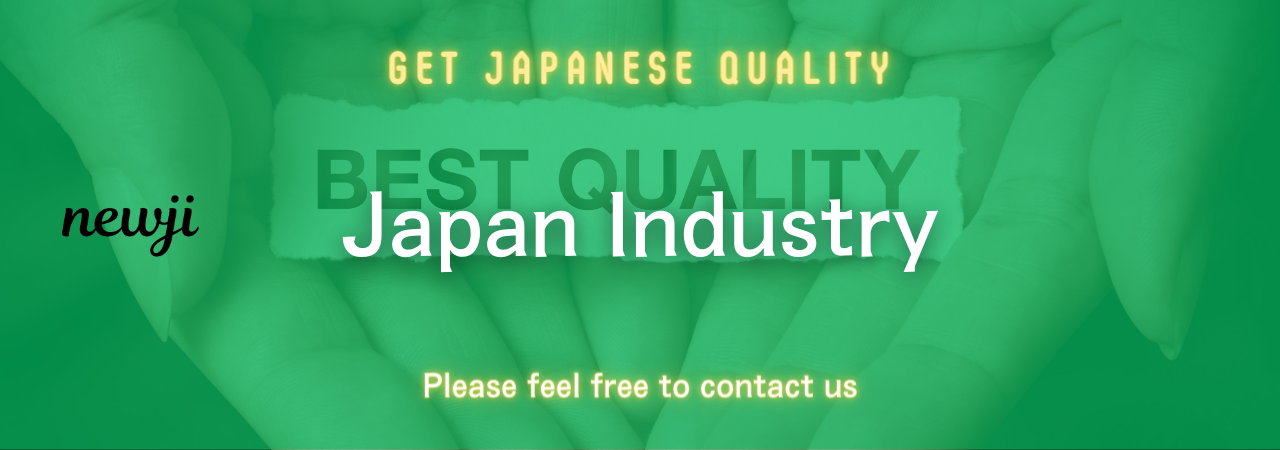
In the complex and highly sensitive field of semiconductor manufacturing, maintaining a contaminant-free environment is crucial.
Cleanroom-compatible design methods for semiconductor manufacturing equipment play a vital role in ensuring high-quality production.
This article delves into the fundamental principles and practical strategies for designing equipment that meets stringent cleanroom standards.
目次
The Importance of Cleanroom-Compatible Design
Semiconductor manufacturing requires an environment free from pollutants that could compromise the integrity of the microchips.
Contaminants such as dust, airborne microbes, and chemical vapors can adversely affect the manufacturing process.
Therefore, the design and construction of semiconductor manufacturing equipment must prioritize cleanroom compatibility.
A cleanroom-compatible design minimizes the generation of particles and facilitates easier maintenance and cleaning.
By integrating these principles into the design, manufacturers can reduce the risk of contamination, thereby increasing yield and efficiency.
Material Selection
Choosing Non-Contaminating Materials
The materials used in semiconductor manufacturing equipment must not release particles, outgas, or react chemically with other substances in the cleanroom.
Materials such as stainless steel, anodized aluminum, and specially formulated polymers are commonly used due to their low particle generation and non-reactive properties.
Surface Finishes
The surface finish of equipment can significantly affect its cleanliness.
Smooth surfaces are easier to clean and less likely to harbor particles.
Electro-polishing and passivation are common techniques used to achieve cleanroom-compatible surface finishes.
Design for Reduced Particle Generation
Minimizing Moving Parts
Moving parts within equipment are prone to generating particles.
Design strategies that reduce the number of moving parts, such as using linear motors instead of traditional rotary motors, can significantly decrease particle generation.
Sealing and Containment
Effective sealing and containment strategies are essential for preventing contaminants from escaping or entering the equipment.
Utilizing high-quality seals, gaskets, and barriers can help maintain a contaminant-free environment within the cleanroom.
Maintenance and Cleaning Considerations
Ease of Disassembly
Designing equipment with ease of disassembly in mind can facilitate regular maintenance and cleaning.
Quick-release fasteners, modular components, and accessible assembly points make it easier for technicians to clean and service equipment without introducing contaminants.
Cleanable Components
Components should be designed in such a way that they can withstand frequent cleaning with the chemicals and methods used in cleanroom environments.
This includes selecting materials that are resistant to these cleaning agents and designing shapes that do not trap particulates.
Compliance with Industry Standards
ISO 14644
The ISO 14644 standard is a globally recognized set of guidelines for cleanroom design and maintenance.
Ensuring that equipment design complies with these standards can help manufacturers meet the rigorous requirements of semiconductor production.
GMP Regulations
Good Manufacturing Practice (GMP) regulations provide additional guidelines for the design and operation of cleanroom-compatible equipment.
Adhering to GMP can further reduce the risk of contamination and improve product quality.
Technological Advancements in Cleanroom-Design
Advanced Filtration Systems
Incorporating advanced filtration systems into the design of semiconductor manufacturing equipment can further enhance cleanroom compatibility.
High-efficiency particulate air (HEPA) and ultra-low penetration air (ULPA) filters are commonly used to remove contaminants from the air.
Automation and Robotics
The use of automation and robotics in cleanroom environments can reduce the risk of human-induced contamination.
Automated systems are designed to operate in cleanroom conditions without generating particles, thus maintaining a high level of cleanliness.
Case Studies and Implementation Examples
Successful Implementation in the Industry
Numerous case studies highlight the successful implementation of cleanroom-compatible design methods.
For example, a leading semiconductor manufacturer achieved a significant reduction in contamination levels by redesigning their wafer handling equipment with smooth surfaces and advanced filtration.
Lessons Learned
Analyzing these successful implementations can provide valuable insights and lessons for other manufacturers.
Common factors include the importance of material selection, the benefits of minimizing moving parts, and the effectiveness of advanced filtration systems.
Conclusion
Cleanroom-compatible design methods are essential for maintaining the integrity of semiconductor manufacturing processes.
By selecting appropriate materials, minimizing particle generation, and facilitating maintenance, manufacturers can significantly reduce the risk of contamination.
Compliance with industry standards and the adoption of technological advancements further enhance the effectiveness of these design methods.
Ultimately, the implementation of cleanroom-compatible design principles can lead to higher product quality, increased yield, and improved operational efficiency.
資料ダウンロード
QCD管理受発注クラウド「newji」は、受発注部門で必要なQCD管理全てを備えた、現場特化型兼クラウド型の今世紀最高の受発注管理システムとなります。
ユーザー登録
受発注業務の効率化だけでなく、システムを導入することで、コスト削減や製品・資材のステータス可視化のほか、属人化していた受発注情報の共有化による内部不正防止や統制にも役立ちます。
NEWJI DX
製造業に特化したデジタルトランスフォーメーション(DX)の実現を目指す請負開発型のコンサルティングサービスです。AI、iPaaS、および先端の技術を駆使して、製造プロセスの効率化、業務効率化、チームワーク強化、コスト削減、品質向上を実現します。このサービスは、製造業の課題を深く理解し、それに対する最適なデジタルソリューションを提供することで、企業が持続的な成長とイノベーションを達成できるようサポートします。
製造業ニュース解説
製造業、主に購買・調達部門にお勤めの方々に向けた情報を配信しております。
新任の方やベテランの方、管理職を対象とした幅広いコンテンツをご用意しております。
お問い合わせ
コストダウンが利益に直結する術だと理解していても、なかなか前に進めることができない状況。そんな時は、newjiのコストダウン自動化機能で大きく利益貢献しよう!
(β版非公開)