- お役立ち記事
- Cleanroom-Ready Design Methods for Semiconductor Manufacturing Equipment
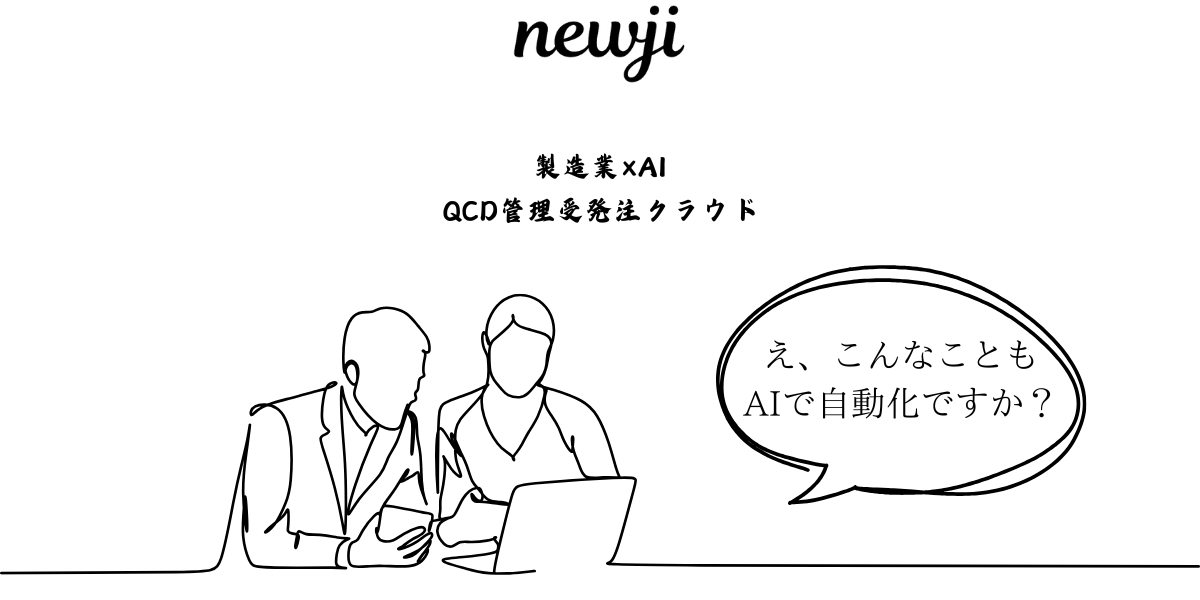
Cleanroom-Ready Design Methods for Semiconductor Manufacturing Equipment
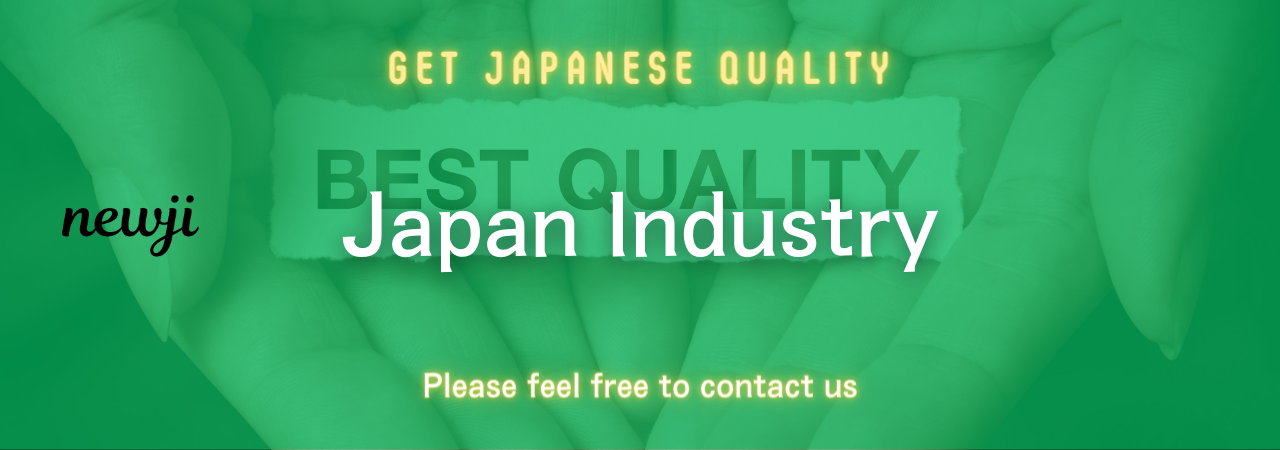
目次
Introduction to Cleanroom-Ready Design
Semiconductor manufacturing is a highly intricate process that demands precision and an uncontaminated environment.
This is why cleanroom-ready design methods for semiconductor manufacturing equipment are of paramount importance.
In this article, we will explore what cleanroom-ready design entails, its significance in semiconductor manufacturing, and how these methods are implemented to ensure the highest standards of quality.
Understanding Cleanrooms in Semiconductor Manufacturing
Semiconductor manufacturing requires a meticulously controlled environment to prevent contamination, ensure consistent performance, and maintain the integrity of the delicate components involved.
Cleanrooms are specialized environments where temperature, humidity, and airborne particles are strictly regulated.
In these spaces, even the slightest contamination can result in defects within the semiconductor products, leading to significant losses in manufacturing yield.
Why Cleanroom Design is Crucial
Cleanroom-ready design methods are essential because they help in minimizing potential contamination risks.
In the semiconductor industry, even microscopic particles can result in significant damage or defective products.
Therefore, equipment used in these environments must be designed to operate without introducing contaminants.
This ensures a high level of quality control and reduces the incidence of costly errors in semiconductor production.
Key Elements of Cleanroom-Ready Design
When designing equipment for cleanroom environments, several key elements must be considered to ensure that they are suitable for use in semiconductor manufacturing.
Material Selection
Materials used in the fabrication of cleanroom equipment must be chosen with care.
The selection of materials is crucial because they need to resist corrosion, do not shed particles, and can be easily cleaned.
Common choices include stainless steel and certain types of plastics that do not react with cleaning agents used to maintain the cleanliness of the environment.
Seamless Construction
Cleanroom equipment should be designed with seamless construction wherever possible.
Seams and crevices can harbor dust, particles, or microorganisms, which can contaminate the environment.
Smooth, seamless surfaces facilitate easy cleaning and ensure that contaminants do not accumulate in hard-to-reach areas.
Minimizing Airflow Disruption
Equipment design should aim to minimize disruption to the airflow patterns within the cleanroom.
Strategically designed shapes and surfaces can help ensure that air moves freely and without turbulence, which can carry particles around the cleanroom.
This helps maintain the integrity of critical airflow systems designed to remove particles from the environment.
Integration of Non-Shedding Components
All components of the equipment, including moving parts, should be non-shedding.
This involves the use of lubricants and materials that do not produce particulates as they wear.
Equipment should be designed in such a way that its operation does not introduce any new particles into the cleanroom atmosphere.
Implementing Cleanroom-Ready Design Methods
A successful implementation of cleanroom-ready design methods involves several systematic steps during the design and manufacturing process.
Collaboration with Experts
Designers and engineers must collaborate closely with cleanroom experts to understand the specific requirements and constraints of the environment.
Such collaboration ensures that the equipment design aligns with the regulatory standards and practical needs of semiconductor manufacturing facilities.
Rigorous Testing and Validation
Before new equipment is introduced into a cleanroom, it must undergo rigorous testing and validation.
This includes tests for particle emissions, compatibility with cleaning agents, and how well the equipment integrates into the overall cleanroom infrastructure.
These tests help ensure that the equipment functions as intended without compromising the cleanroom environment.
Regular Maintenance and Upgrades
Equipment maintenance is an integral part of cleanroom-ready design methods.
Regular checks and updates are necessary to ensure that all components continue to function at the highest standard.
This also involves updating or replacing parts as they wear out or as technological advancements are made in the industry.
Benefits of Cleanroom-Ready Design
Implementing cleanroom-ready design methods offers several benefits to semiconductor manufacturers.
Increased Yield
By reducing contamination risks, cleanroom-ready designs contribute to higher yields in semiconductor manufacturing.
Fewer defects mean more units meet quality standards, providing significant cost savings and increased profitability for manufacturers.
Enhanced Product Quality
Cleanroom-ready designs ensure that the highest levels of quality are maintained throughout the manufacturing process.
This not only prevents defects but also enhances the reliability and performance of semiconductor products in the market.
Regulatory Compliance
Many industries regulate the standards of cleanrooms tightly.
Designed equipment in accordance with these regulations ensures that companies remain compliant, avoiding potential legal issues and preserving their reputation in the industry.
Conclusion
The importance of cleanroom-ready design methods in semiconductor manufacturing cannot be overstated.
By understanding and implementing these methods, manufacturers can ensure high-quality production, reduce contamination risks, and maintain a competitive edge.
As technology continues to advance, maintaining the highest standards of cleanliness in manufacturing environments will remain a critical focus, emphasizing the need for ongoing innovation in cleanroom-ready design.
資料ダウンロード
QCD調達購買管理クラウド「newji」は、調達購買部門で必要なQCD管理全てを備えた、現場特化型兼クラウド型の今世紀最高の購買管理システムとなります。
ユーザー登録
調達購買業務の効率化だけでなく、システムを導入することで、コスト削減や製品・資材のステータス可視化のほか、属人化していた購買情報の共有化による内部不正防止や統制にも役立ちます。
NEWJI DX
製造業に特化したデジタルトランスフォーメーション(DX)の実現を目指す請負開発型のコンサルティングサービスです。AI、iPaaS、および先端の技術を駆使して、製造プロセスの効率化、業務効率化、チームワーク強化、コスト削減、品質向上を実現します。このサービスは、製造業の課題を深く理解し、それに対する最適なデジタルソリューションを提供することで、企業が持続的な成長とイノベーションを達成できるようサポートします。
オンライン講座
製造業、主に購買・調達部門にお勤めの方々に向けた情報を配信しております。
新任の方やベテランの方、管理職を対象とした幅広いコンテンツをご用意しております。
お問い合わせ
コストダウンが利益に直結する術だと理解していても、なかなか前に進めることができない状況。そんな時は、newjiのコストダウン自動化機能で大きく利益貢献しよう!
(Β版非公開)