- お役立ち記事
- Cold Forging Techniques to Enhance Dimensional Accuracy in Steel Products
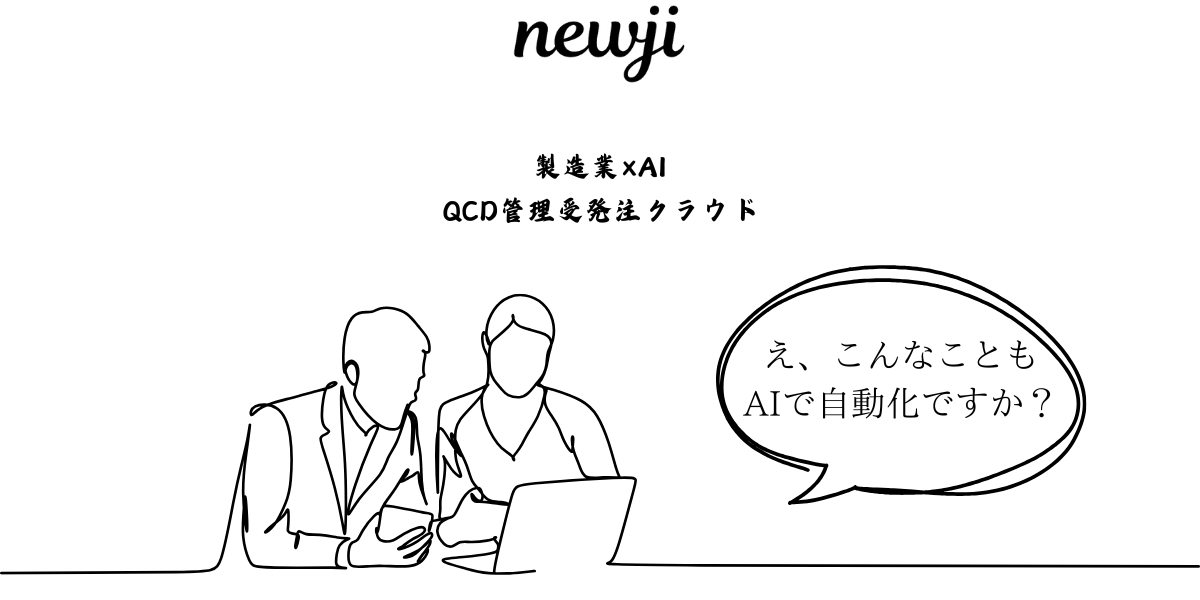
Cold Forging Techniques to Enhance Dimensional Accuracy in Steel Products
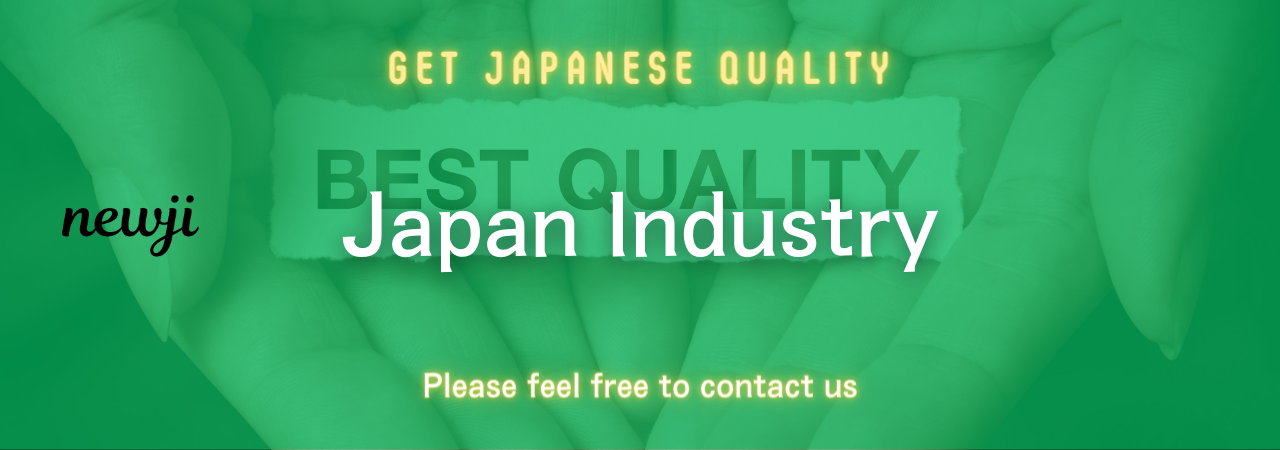
目次
Introduction to Cold Forging
Cold forging is a powerful manufacturing process that enhances the dimensional accuracy of steel products.
It involves shaping metal blanks into desired forms at room temperature, which helps retain the material’s properties and surface finish.
This method is preferred over hot forging when precision and surface quality are crucial.
Cold forging techniques have been refined over the years, making them essential for industries such as automotive, aerospace, and construction.
In this article, we will explore the advantages of cold forging and how it can significantly improve the dimensional accuracy of steel components.
Understanding Dimensional Accuracy
Dimensional accuracy refers to the extent to which the final product matches the specified dimensions and tolerances.
For steel components, achieving high dimensional accuracy is critical to ensure proper fit, function, and performance.
Inaccuracies can lead to issues such as reduced strength, misalignment, and increased wear and tear.
Cold forging techniques address these challenges by providing precise control over the shaping process.
By understanding the factors that contribute to dimensional accuracy, manufacturers can optimize their processes to produce high-quality steel products.
Factors Influencing Dimensional Accuracy
Several factors influence the dimensional accuracy of forged steel products.
These include the material properties, tooling design, process parameters, and equipment used.
Metal’s grain structure, ductility, and hardness play a crucial role in determining how it behaves during cold forging.
Tooling design, including dies and punches, must be carefully crafted to minimize deflection and ensure uniform material flow.
Process parameters such as deformation speed, force, and lubrication affect the final product’s dimensions.
Advanced machinery with precise controls is essential for achieving consistent and accurate results.
Advantages of Cold Forging
Cold forging offers numerous advantages over other manufacturing methods, making it ideal for producing steel components with precise dimensions.
One of the primary benefits is the enhanced surface finish achieved through cold working.
The process compresses the metal, resulting in a smooth and shiny surface without the need for additional finishing operations.
Additionally, cold forging increases the material’s strength and hardness through work hardening, improving the overall performance of the component.
Superior Material Utilization
Another advantage of cold forging is its high material utilization rate.
The process generates minimal scrap and reduces the need for extensive machining, saving both material and energy.
As a result, manufacturers can produce components with lower costs and reduced environmental impact.
This efficient use of resources is particularly important in industries with tight budget constraints or sustainability goals.
Enhanced Structural Integrity
Cold forging enhances the structural integrity of steel components by aligning the metal’s grain flow with the part’s geometry.
This alignment increases the component’s strength and resistance to fatigue and wear.
Unlike casting or machining processes, cold forging does not create weak spots or stress concentrations, resulting in a more robust final product.
As a result, cold-forged parts are ideal for critical applications requiring consistent performance and reliability.
Common Cold Forging Techniques
Several cold forging techniques can be employed to improve the dimensional accuracy of steel products.
Each method has its unique advantages and applications, depending on the desired product specifications and manufacturing requirements.
Upset Forging
Upset forging involves increasing the diameter of a metal workpiece by compressing its length.
This technique is widely used to produce components with flange-like features or increased cross-sections.
The process enhances dimensional accuracy by controlling the distribution of material across the workpiece.
Upset forging is typically applied in the production of bolts, nuts, and fasteners, where precise geometries are essential for optimal performance.
Forward and Backward Extrusion
In forward extrusion, the metal is forced through a die to elongate its shape, while backward extrusion involves forcing the die into the workpiece.
Both techniques offer precise control over the final dimensions, making them suitable for producing intricate components such as gear blanks, splines, and shafts.
Extrusion processes are highly efficient and can achieve tight tolerances, ensuring consistent dimensional accuracy across large production runs.
Coining
Coining is a precision stamping process that applies high pressure to a metal blank, creating detailed and accurate features.
This technique is optimal for producing components with complex geometries or fine surface details.
Coining enhances dimensional accuracy by compressing the material uniformly, resulting in minimal springback and distortion.
In addition to its application in steel products, coining is commonly used in the production of coins, medals, and decorative items.
Conclusion
Cold forging techniques are essential for enhancing the dimensional accuracy of steel products.
By understanding the factors that affect this precision and employing appropriate methods such as upset forging, extrusion, and coining, manufacturers can produce components with superior quality and performance.
The advantages of cold forging, including improved surface finish, material utilization, and structural integrity, make it a preferred choice for many industries.
As technology advances and new developments emerge, cold forging will continue to play a vital role in the production of dimensionally accurate steel components.
資料ダウンロード
QCD調達購買管理クラウド「newji」は、調達購買部門で必要なQCD管理全てを備えた、現場特化型兼クラウド型の今世紀最高の購買管理システムとなります。
ユーザー登録
調達購買業務の効率化だけでなく、システムを導入することで、コスト削減や製品・資材のステータス可視化のほか、属人化していた購買情報の共有化による内部不正防止や統制にも役立ちます。
NEWJI DX
製造業に特化したデジタルトランスフォーメーション(DX)の実現を目指す請負開発型のコンサルティングサービスです。AI、iPaaS、および先端の技術を駆使して、製造プロセスの効率化、業務効率化、チームワーク強化、コスト削減、品質向上を実現します。このサービスは、製造業の課題を深く理解し、それに対する最適なデジタルソリューションを提供することで、企業が持続的な成長とイノベーションを達成できるようサポートします。
オンライン講座
製造業、主に購買・調達部門にお勤めの方々に向けた情報を配信しております。
新任の方やベテランの方、管理職を対象とした幅広いコンテンツをご用意しております。
お問い合わせ
コストダウンが利益に直結する術だと理解していても、なかなか前に進めることができない状況。そんな時は、newjiのコストダウン自動化機能で大きく利益貢献しよう!
(Β版非公開)