- お役立ち記事
- Cold rolling technology for steel products and their strength improvement in the automobile market
月間77,185名の
製造業ご担当者様が閲覧しています*
*2025年2月28日現在のGoogle Analyticsのデータより
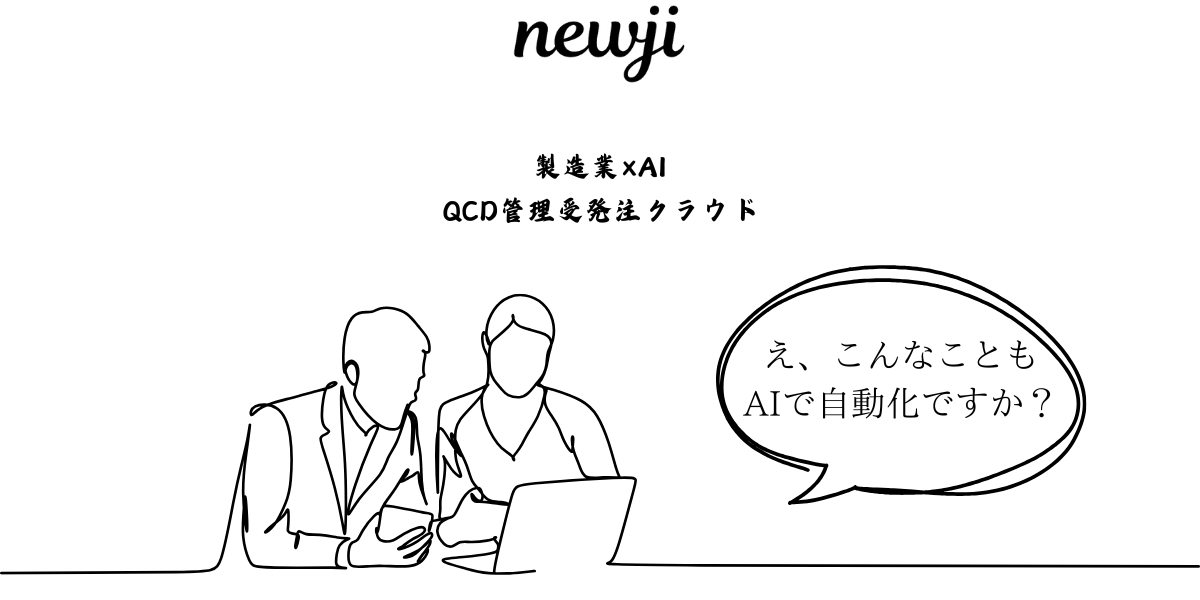
Cold rolling technology for steel products and their strength improvement in the automobile market
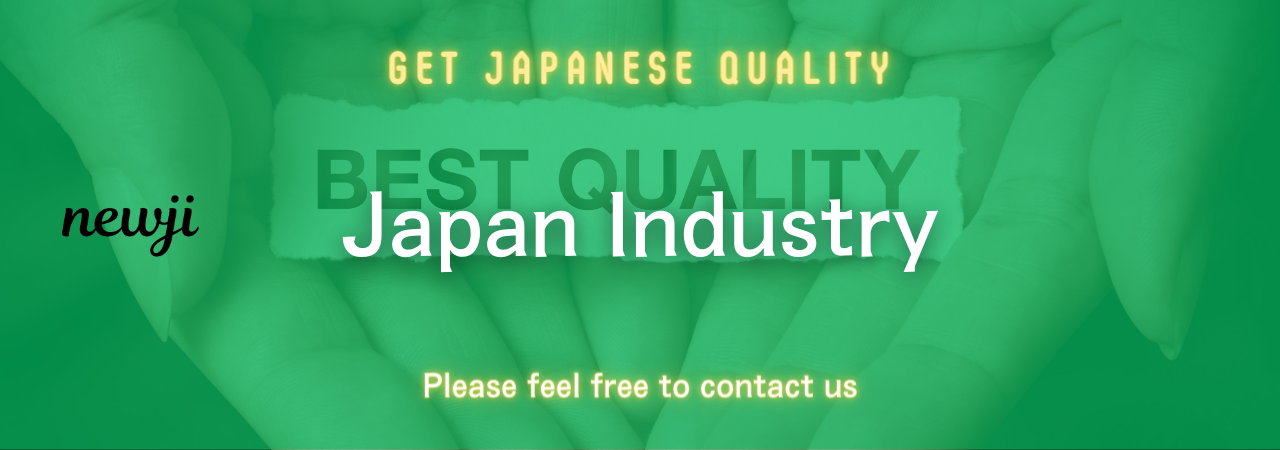
目次
Introduction to Cold Rolling Technology
Cold rolling technology is a critical process in the steel industry, essential for producing high-quality steel products used across a variety of applications, especially in the automotive market.
This process involves rolling steel at room temperature, below its recrystallization point, which enhances the metal’s strength and surface finish.
The technology impacts the production and performance of steel products, making it an indispensable part of modern manufacturing and engineering.
Understanding the Cold Rolling Process
The cold rolling process begins with a series of steps designed to reduce the thickness of steel, improve its surface quality, and enhance its mechanical properties.
The process starts with the pickling stage, where the steel is cleaned of any scale and impurities that could affect rolling.
Once cleaned, the steel is passed through a series of rollers that compress it to the desired thickness and shape.
This stage imparts a smoother surface and a more uniform thickness throughout the steel strip.
Following this, the material is subjected to annealing, where it is heated and then slowly cooled to relieve internal stresses introduced during rolling and to enhance ductility.
Finally, a skin pass, a light rolling of the steel, is conducted to achieve the desired surface finish.
The Benefits of Cold Rolling Steel
Cold rolling technology offers numerous benefits that make it preferable for specific applications, especially in the automotive sector.
One of the primary benefits is the increased strength of the final product.
The deformation process hardens the steel through work hardening, resulting in improved tensile strength.
Moreover, cold-rolled steel often has superior surface qualities, such as smoother and shinier surfaces, which are important for both cosmetic and functional reasons, particularly in vehicle manufacturing.
The enhanced surface finish also makes cold-rolled steel the material of choice in situations where aesthetics are important or where further processing, like painting or coating, is required.
This technology also facilitates extremely precise control over the thickness of the steel, allowing manufacturers to produce steel products with exact dimensions.
This precision is crucial for developing components that require a tight fit, such as those found in vehicles.
Strength Improvement in the Automotive Industry
In the automotive industry, strength is a critical factor, as it directly influences safety and performance.
Cold rolling technology helps improve the mechanical properties of steel, which enhances the structural integrity of automotive components.
The ability to produce high-strength, lightweight steel parts is integral to modern automotive design.
As automakers strive to meet increasingly stringent fuel economy standards, reducing vehicle weight without compromising safety or performance is pivotal.
High-strength, lightweight steel allows for the manufacture of components that contribute to the overall reduction in vehicle weight, leading to better fuel efficiency.
Furthermore, steel components made through cold rolling are more resistant to wear and impact, increasing the durability and lifespan of vehicles.
This durability is an essential factor in safety, as it ensures that critical components maintain their integrity throughout the vehicle’s life cycle.
Environmental and Economic Impacts
Cold rolling technology not only provides technical advantages but also has significant environmental and economic impacts.
Economically, producing high-quality steel that meets industry standards and customer demands can lead to reduced costs over the product lifecycle due to fewer defects and enhanced durability.
Additionally, the precision of cold rolling reduces material waste and inefficiencies, optimizing the resource usage in manufacturing.
Environmentally, improved steel durability and material efficiency contribute to sustainability by reducing the need for frequent replacement and minimizing resource extraction.
Moreover, using high-strength steel allows automakers to design lighter vehicles, which boosts fuel efficiency, subsequently decreasing emissions.
Challenges and Innovations
Despite its many advantages, cold rolling technology also presents challenges.
The process requires precise control and substantial energy consumption, which can be costly.
Maintaining quality control throughout the process is necessary to avoid defects that can compromise the product’s performance.
Recent innovations aim at addressing these challenges by introducing more energy-efficient equipment and adopting digital technologies for better process monitoring and control.
The integration of automation and advanced sensor technology allows for real-time quality assessment, reducing waste and increasing the consistency of the final product.
Additionally, research is directed at developing new alloy compositions that retain the strength benefits of cold rolling while further minimizing weight and enhancing other properties such as corrosion resistance.
Conclusion
Cold rolling technology is a cornerstone of steel production, particularly for high-performance applications like those in the automotive industry.
With its ability to enhance strength, improve surface finish, and offer precise control over dimensions, cold rolling plays a crucial role in meeting the demands for lightweight, durable, and energy-efficient vehicles.
While the process presents some challenges, ongoing innovations show a promising future for making it more efficient and environmentally friendly.
The advancements in cold rolling not only contribute to the evolution of the automotive industry but also embody a broader move towards sustainable and high-performance materials across different sectors.
資料ダウンロード
QCD管理受発注クラウド「newji」は、受発注部門で必要なQCD管理全てを備えた、現場特化型兼クラウド型の今世紀最高の受発注管理システムとなります。
ユーザー登録
受発注業務の効率化だけでなく、システムを導入することで、コスト削減や製品・資材のステータス可視化のほか、属人化していた受発注情報の共有化による内部不正防止や統制にも役立ちます。
NEWJI DX
製造業に特化したデジタルトランスフォーメーション(DX)の実現を目指す請負開発型のコンサルティングサービスです。AI、iPaaS、および先端の技術を駆使して、製造プロセスの効率化、業務効率化、チームワーク強化、コスト削減、品質向上を実現します。このサービスは、製造業の課題を深く理解し、それに対する最適なデジタルソリューションを提供することで、企業が持続的な成長とイノベーションを達成できるようサポートします。
製造業ニュース解説
製造業、主に購買・調達部門にお勤めの方々に向けた情報を配信しております。
新任の方やベテランの方、管理職を対象とした幅広いコンテンツをご用意しております。
お問い合わせ
コストダウンが利益に直結する術だと理解していても、なかなか前に進めることができない状況。そんな時は、newjiのコストダウン自動化機能で大きく利益貢献しよう!
(β版非公開)