- お役立ち記事
- Cold Working Techniques to Enhance Mechanical Properties of Copper Products
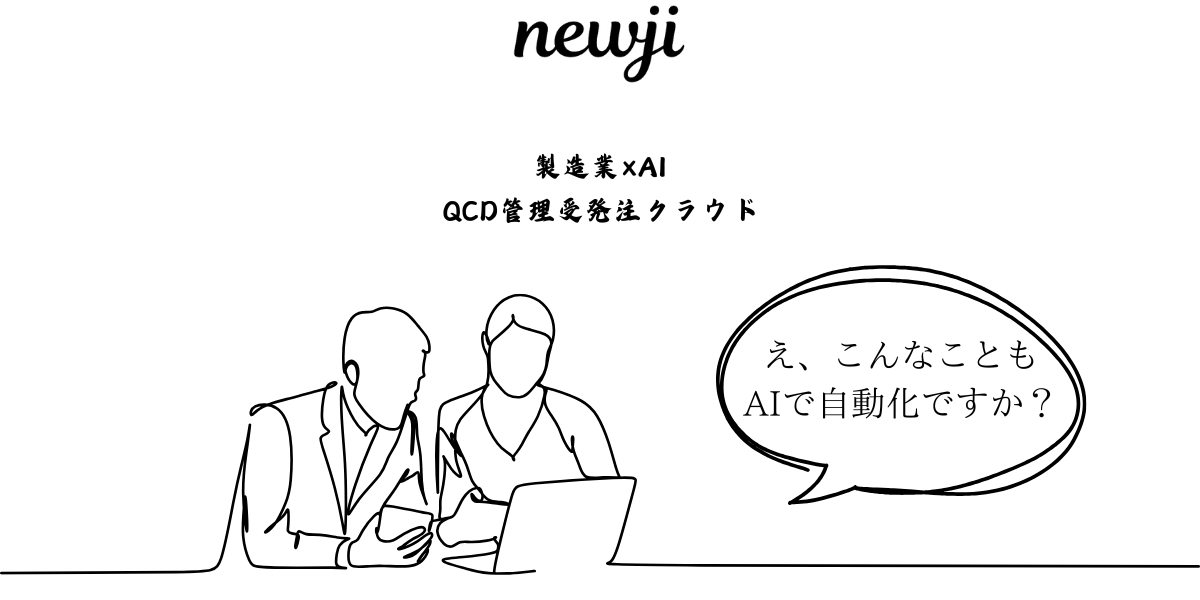
Cold Working Techniques to Enhance Mechanical Properties of Copper Products
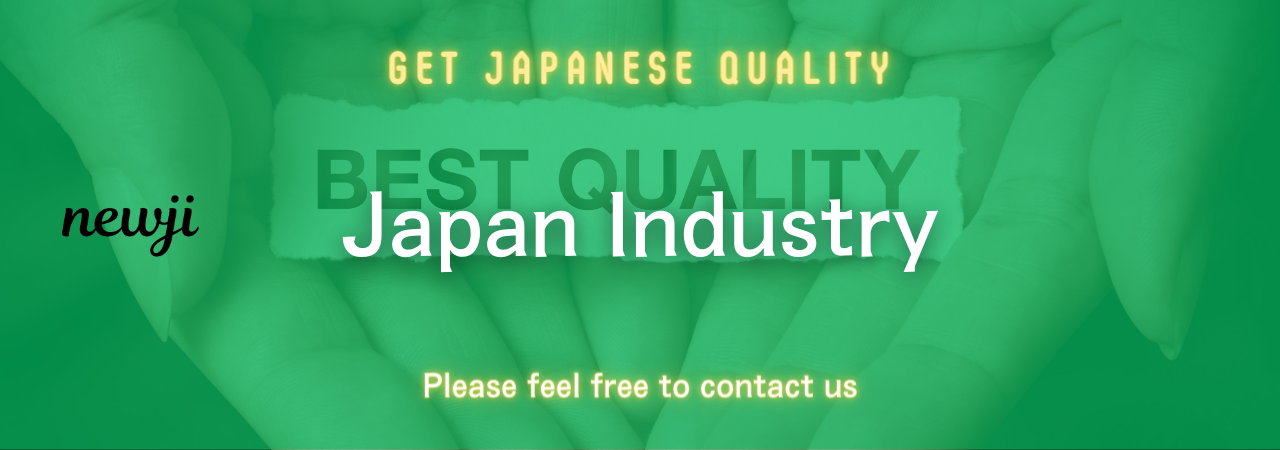
目次
Understanding Cold Working
Cold working, also known as work hardening, involves the deformation of metals below their recrystallization temperature to enhance mechanical properties such as strength, hardness, and toughness.
For copper products, cold working is a popular method because copper has excellent ductility and electrical conductivity, making it ideal for various applications in industries such as electronics and construction.
During cold working, the metal is typically subjected to processes like rolling, drawing, pressing, or forging, which changes the shape and mechanical properties without altering the material’s composition.
Benefits of Cold Working Copper Products
Enhancing the mechanical properties of copper through cold working offers several benefits.
Firstly, it significantly increases the strength and hardness of the material.
This is crucial for applications where durability and resistance to wear and tear are necessary.
Secondly, cold working improves the surface finish of copper products, providing a smoother and more aesthetically pleasing appearance.
Furthermore, it refines the grain structure, leading to enhanced material reliability and performance.
Common Cold Working Techniques
There are various cold working techniques used to improve the mechanical properties of copper products.
Below, we’ll explore some of the most common methods:
Rolling
Rolling is a process where copper is passed between two rotating rolls to reduce thickness and alter the cross-sectional area.
This technique is widely used for producing copper sheets and strips.
The rolling process increases the dislocation density, which in turn enhances the metal’s strength and hardness.
Drawing
Drawing involves pulling copper through a die to reduce its diameter and elongate the shape.
This method is typically used to produce copper wires and tubes.
Drawing can significantly improve tensile strength and hardness while simultaneously maintaining the material’s excellent ductility and conductivity.
Pressing
Pressing is a method that involves applying a high force to compress copper material into a desired shape.
It is often used to produce complex components with precise dimensions.
Pressing helps in increasing the material’s strength by altering the internal grain structure.
Forging
Forging involves shaping copper by applying compressive forces using a hammer or a press.
It is an excellent technique for producing high-strength components with superior mechanical properties.
Forging enhances the orientation of the metal grains, which contributes to improved toughness and fatigue resistance.
Impact of Cold Working on Copper Properties
The process of cold working can have significant impacts on the properties of copper, resulting in materials that perform better under different conditions.
For example, one of the primary results of cold working is the increased strength and hardness.
The process creates more dislocations within the metal’s crystal lattice, which resists deformation and contributes to the material’s enhanced characteristics.
Moreover, cold working reduces the ductility of copper.
While it remains one of the more ductile metals even after work hardening, the degree to which it can be deformed without breaking is somewhat reduced.
It’s essential to strike a balance between the desired mechanical properties and maintaining sufficient ductility for specific applications.
Another crucial effect of cold working is work hardening, where continued deformation leads to increased strength and hardening of the material.
Although this is beneficial for applications requiring strong components, it requires careful control as excessive work hardening can lead to brittleness and cracking.
Challenges and Considerations in Cold Working
While cold working offers numerous advantages for enhancing the mechanical properties of copper products, it also presents several challenges and considerations.
One significant challenge is the increased risk of residual stresses and defects such as cracks or warping due to uneven deformation.
It is essential to apply uniform forces and carefully control the deformation process to minimize these risks.
Moreover, cold working requires specialized equipment and tools, making it an investment-intensive process.
The tooling used must withstand the forces applied during deformation, ensuring the quality and consistency of the final product.
Additionally, it’s essential to consider the effects of cold working on the material’s electrical and thermal conductivity.
While copper remains conductive even after work hardening, excessive deformation can slightly impact these properties.
Striking the right balance between mechanical strength and conductivity is crucial for applications such as electrical wiring.
Applications of Cold Worked Copper
Cold worked copper products find their way into a variety of industries thanks to their enhanced mechanical properties.
In the electrical industry, cold worked copper wires are favored for their strength and excellent conductivity.
These attributes make them ideal for high-performance wiring, connectors, and other electrical components.
In plumbing, cold worked copper tubes and pipes are popular choices due to their durability, resistance to corrosion, and ease of installation.
Cold worked copper sheets and strips are also fundamental in architectural and decorative applications where both strength and a refined surface finish are desirable.
Conclusion
Cold working is a valuable technique for enhancing the mechanical properties of copper products.
By employing methods such as rolling, drawing, pressing, and forging, manufacturers can produce copper components with increased strength, hardness, and improved surface finish.
Despite the challenges involved, the benefits of cold working make it an indispensable part of producing high-quality copper products for a wide range of industrial applications.
Understanding the principles and effects of cold working allows for the optimization of copper products tailored to specific needs and performance requirements.
資料ダウンロード
QCD調達購買管理クラウド「newji」は、調達購買部門で必要なQCD管理全てを備えた、現場特化型兼クラウド型の今世紀最高の購買管理システムとなります。
ユーザー登録
調達購買業務の効率化だけでなく、システムを導入することで、コスト削減や製品・資材のステータス可視化のほか、属人化していた購買情報の共有化による内部不正防止や統制にも役立ちます。
NEWJI DX
製造業に特化したデジタルトランスフォーメーション(DX)の実現を目指す請負開発型のコンサルティングサービスです。AI、iPaaS、および先端の技術を駆使して、製造プロセスの効率化、業務効率化、チームワーク強化、コスト削減、品質向上を実現します。このサービスは、製造業の課題を深く理解し、それに対する最適なデジタルソリューションを提供することで、企業が持続的な成長とイノベーションを達成できるようサポートします。
オンライン講座
製造業、主に購買・調達部門にお勤めの方々に向けた情報を配信しております。
新任の方やベテランの方、管理職を対象とした幅広いコンテンツをご用意しております。
お問い合わせ
コストダウンが利益に直結する術だと理解していても、なかなか前に進めることができない状況。そんな時は、newjiのコストダウン自動化機能で大きく利益貢献しよう!
(Β版非公開)