- お役立ち記事
- Collaboration strategy between logistics and purchasing departments to improve transportation efficiency
Collaboration strategy between logistics and purchasing departments to improve transportation efficiency
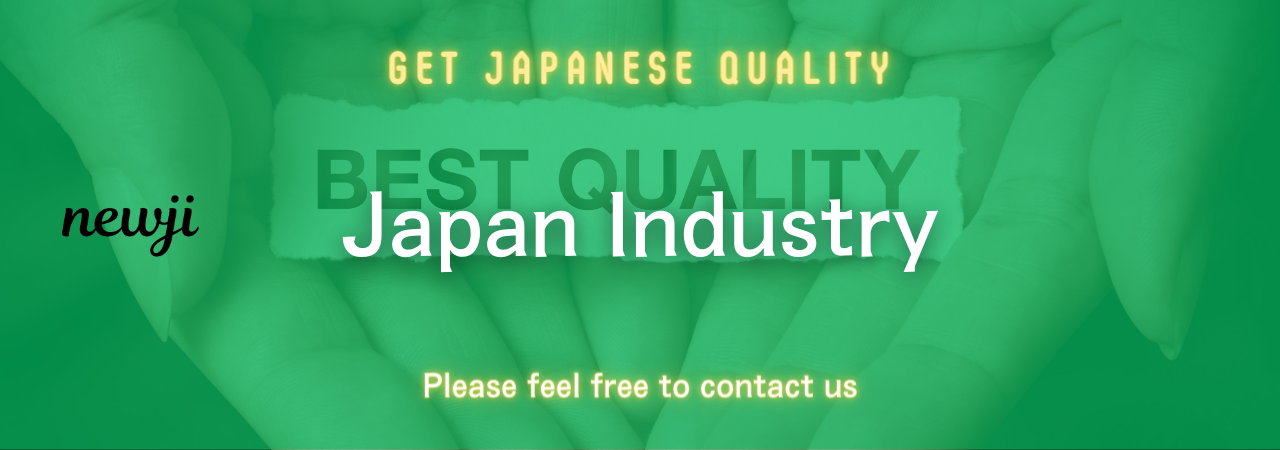
目次
Understanding the Importance of Collaboration
The logistics and purchasing departments play vital roles in any company that deals with the movement of goods.
While each department has its own unique responsibilities, collaboration between these two can significantly enhance a company’s transportation efficiency.
Understanding why this collaboration is important is the first step in implementing successful strategies.
Logistics handles the movement, storage, and flow of goods within a company and to its customers.
The purchasing department, on the other hand, is responsible for acquiring the needed materials and products from suppliers.
When these two departments work together, they can achieve more streamlined operations, reduce costs, and improve delivery times.
Goals of a Successful Collaboration
Successful collaboration between logistics and purchasing departments aims to optimize the transportation process.
This includes reducing transportation costs, ensuring timely deliveries, and maintaining high service levels.
One of the key goals is to align purchasing strategies with transportation capabilities.
For instance, if the logistics department is aware of upcoming large purchases, it can better prepare and optimize shipping routes.
This alignment helps in making transportation more efficient by reducing unnecessary trips, which in turn reduces fuel consumption and emissions.
Cost Reduction
A collaborative approach can significantly cut costs.
When logistics and purchasing departments share information and coordinate schedules, they can potentially negotiate better rates with suppliers and carriers.
Bulk purchasing often leads to discounts, and synchronized transportation scheduling can reduce expedited shipping costs.
Another cost-saving strategy involves joint decision-making on supplier selection, considering not only the cost of goods but also the transportation expenses.
Selecting suppliers closer to the company’s production facilities or distribution centers can lead to shorter distances to transport goods, thus lowering overall costs.
Improved Inventory Management
Collaboration aids in better inventory management.
When logistics and purchasing work in harmony, the purchasing team can avoid over-ordering, which might otherwise lead to excess inventory and increased storage costs.
Knowing exactly when shipments will arrive allows the logistics team to efficiently manage warehouse space, ensuring that inventory turnover is optimized.
An effective collaboration strategy might also involve implementing just-in-time (JIT) inventory systems.
This means receiving goods only as they are needed in the production process, which requires precise coordination between the two departments.
Implementing Effective Communication Channels
Effective communication is the backbone of collaboration.
Establishing robust communication channels between logistics and purchasing departments is crucial.
This might involve regular meetings, shared digital platforms, or integrated software systems that allow real-time data exchange.
Regular check-ins and coordination meetings help both teams stay informed about each other’s plans and challenges.
Using technology to provide real-time updates can drastically improve how quickly both departments react to changes, such as shipment delays or supplier issues.
Leveraging Technology
In today’s digital age, technology plays a crucial role in facilitating collaboration.
Integrated software solutions that provide data visibility to both logistics and purchasing teams are invaluable.
These systems can track shipments, manage inventory, and provide analytics on transportation costs.
For instance, an ERP (Enterprise Resource Planning) system centralizes all company data, allowing both departments to access relevant information seamlessly.
By using such tools, companies can automate many of the manual processes that currently cause delays and inefficiencies.
Shared Performance Metrics
To ensure that logistics and purchasing departments are working towards mutual goals, it’s helpful to establish shared performance metrics.
These metrics might include delivery times, shipping costs, and inventory levels.
Setting shared targets encourages teamwork and gives both departments clear objectives to strive for.
Regularly reviewing performance against these shared metrics keeps the collaboration on track and helps identify areas for improvement.
Overcoming Challenges
Despite the benefits, there are challenges to logistics and purchasing collaboration.
Departmental silos, lack of data transparency, and resistance to change are common hurdles.
To overcome these, it’s essential to foster a culture of teamwork and open communication across departments.
Management support and training can also play a key role in breaking down silos and encouraging collaboration.
Ensuring that both departments see the tangible benefits of collaboration is crucial.
Showcasing successful case studies or small wins can motivate teams to continue working together.
Developing a Collaborative Culture
For collaboration to be truly effective, it must be embedded in the company culture.
Encouraging cross-departmental initiatives and fostering an environment of trust and respect is vital.
Companies can organize cross-departmental workshops or team-building exercises to strengthen the relationship between logistics and purchasing teams.
This collaborative culture should be reinforced at every level of the organization, from top management to ground-level employees.
In conclusion, a solid collaboration strategy between logistics and purchasing departments can significantly enhance transportation efficiency.
Through effective communication, shared goals, and the use of technology, these departments can ensure that they work cohesively to meet business objectives.
By overcoming challenges and fostering a collaborative culture, companies can achieve improved outcomes, benefiting not only themselves but also their customers.
資料ダウンロード
QCD調達購買管理クラウド「newji」は、調達購買部門で必要なQCD管理全てを備えた、現場特化型兼クラウド型の今世紀最高の購買管理システムとなります。
ユーザー登録
調達購買業務の効率化だけでなく、システムを導入することで、コスト削減や製品・資材のステータス可視化のほか、属人化していた購買情報の共有化による内部不正防止や統制にも役立ちます。
NEWJI DX
製造業に特化したデジタルトランスフォーメーション(DX)の実現を目指す請負開発型のコンサルティングサービスです。AI、iPaaS、および先端の技術を駆使して、製造プロセスの効率化、業務効率化、チームワーク強化、コスト削減、品質向上を実現します。このサービスは、製造業の課題を深く理解し、それに対する最適なデジタルソリューションを提供することで、企業が持続的な成長とイノベーションを達成できるようサポートします。
オンライン講座
製造業、主に購買・調達部門にお勤めの方々に向けた情報を配信しております。
新任の方やベテランの方、管理職を対象とした幅広いコンテンツをご用意しております。
お問い合わせ
コストダウンが利益に直結する術だと理解していても、なかなか前に進めることができない状況。そんな時は、newjiのコストダウン自動化機能で大きく利益貢献しよう!
(Β版非公開)