- お役立ち記事
- Collaboration with suppliers to reduce inventory risk Points for purchasing departments to keep in mind
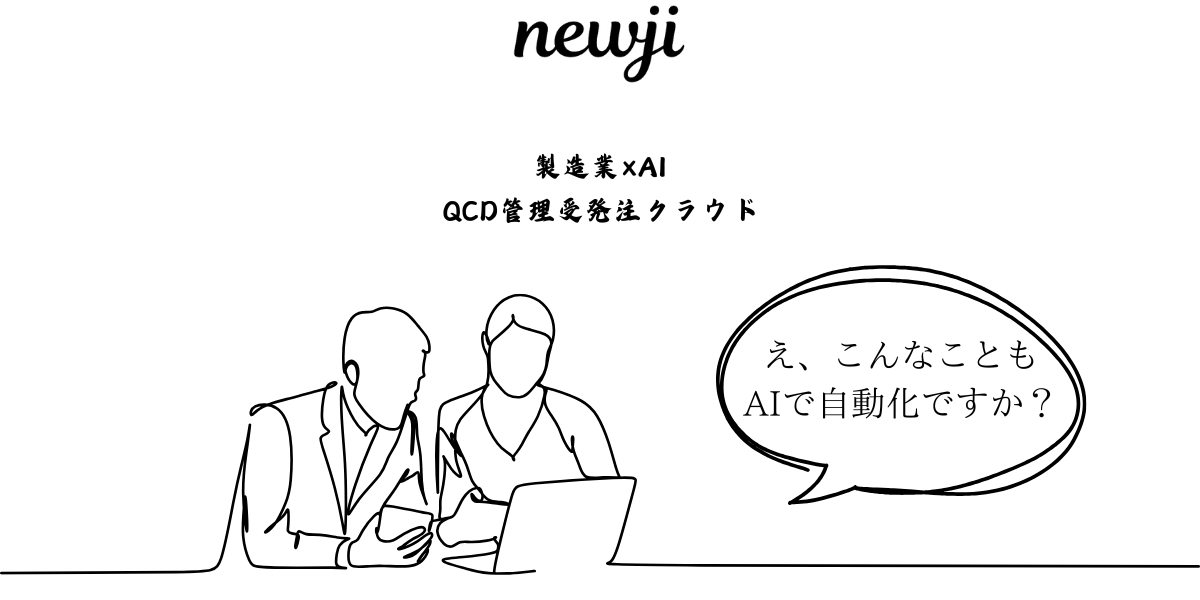
Collaboration with suppliers to reduce inventory risk Points for purchasing departments to keep in mind
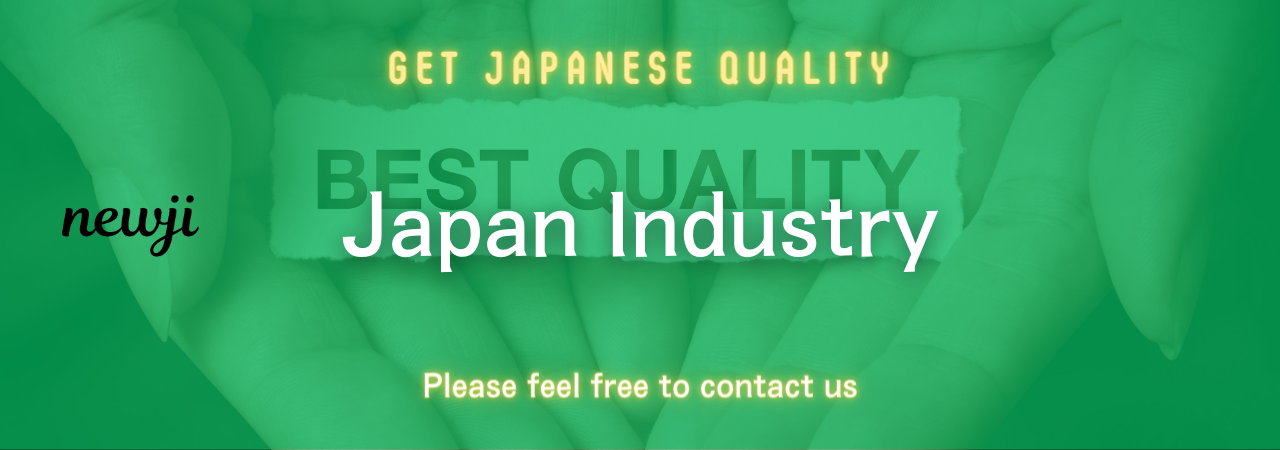
目次
Understanding Inventory Risk
Inventory risk is a significant concern for businesses, especially those involved in manufacturing, retail, and wholesale industries.
It arises from the possibility of holding excess or insufficient inventory, which can lead to financial losses.
Excess inventory ties up capital and increases holding costs, while insufficient stock can lead to missed sales opportunities and customer dissatisfaction.
A collaborative approach with suppliers can help mitigate these risks.
By working closely with suppliers, purchasing departments can better align supply with demand, reduce lead times, and optimize inventory levels.
This collaboration can result in more efficient operations and improved financial performance.
Benefits of Supplier Collaboration
Supplier collaboration offers several benefits that can significantly reduce inventory risk.
Firstly, it enhances communication and transparency between the purchasing department and suppliers.
This improved communication facilitates better forecasting and planning, reducing the likelihood of stockouts or overstock situations.
Secondly, collaboration allows for more flexible and responsive supply chains.
Suppliers can be more agile in adjusting production and delivery schedules to meet changing demand patterns.
This flexibility helps minimize the impact of unforeseen events like sudden spikes or drops in demand.
Another key benefit is the potential for cost savings.
By working closely with suppliers, companies can negotiate better terms, such as bulk purchasing discounts or more favorable payment terms.
These savings can be substantial and contribute to an overall increase in profitability.
Key Strategies for Effective Collaboration
To harness the benefits of supplier collaboration, purchasing departments need to implement key strategies.
Here are several points to consider:
1. Build Strong Relationships
Developing strong, trusting relationships with suppliers is crucial.
This involves open communication, regular meetings, and sharing relevant data.
Building such relationships encourages suppliers to prioritize your company and offer more personalized service and solutions.
2. Share Accurate Demand Forecasts
Accurate demand forecasting is essential for effective collaboration.
Purchasing departments should share forecasts with suppliers to help them anticipate needs and adjust capacity accordingly.
Using advanced analytics and historical sales data can improve the accuracy of these forecasts.
3. Implement Vendor-Managed Inventory (VMI)
Vendor-Managed Inventory programs can significantly reduce inventory risks.
In a VMI arrangement, the supplier is responsible for maintaining inventory levels based on agreed-upon parameters.
This approach can lead to better inventory turnover rates and reduced stockouts.
4. Utilize Technology and Data Analytics
Leveraging technology, such as inventory management software and data analytics tools, enhances collaboration with suppliers.
These tools provide real-time visibility into inventory levels and supply chain operations.
They enable more informed decision-making and quicker responses to changes in demand.
Collaborative Planning and Forecasting
Collaborative planning and forecasting are integral parts of reducing inventory risk.
The process involves the purchasing department and suppliers working together to develop joint business plans and forecasts.
This approach aligns expectations and ensures that both parties work towards common goals.
Regular joint planning sessions can help identify potential risks and areas for improvement.
For example, seasonal demand fluctuations can be addressed by adjusting production schedules or increasing safety stock levels during peak periods.
Agreements on resupply cycles, minimum order quantities, and lead times should be part of the collaborative planning effort.
These agreements foster a clearer understanding and mutual benefit for both parties involved.
Ensuring Continuous Improvement
Collaboration with suppliers should be an ongoing process, with a focus on continuous improvement.
Purchasing departments should regularly evaluate supplier performance and seek feedback to identify areas for enhancement.
Establishing key performance indicators (KPIs) can help measure the effectiveness of collaboration efforts.
Improvement initiatives might include reducing lead times, enhancing product quality, or cutting costs.
Each achievement not only strengthens the relationship with suppliers but also contributes to risk reduction and operational efficiency.
Challenges and Solutions
While collaboration offers numerous advantages, it also presents challenges.
For example, discrepancies in data, differences in organizational cultures, and power dynamics can hinder effective collaboration.
To overcome these challenges, companies must work towards establishing common goals and clear communication channels.
Training sessions or workshops can help align different teams and ensure everyone is on the same page.
A proactive approach to resolving conflicts and maintaining trust is essential.
Regular reviews and agreed-upon protocols for dispute resolution can prevent small issues from escalating.
Conclusion
Collaboration with suppliers plays a pivotal role in reducing inventory risk.
By implementing strategies like building strong relationships, sharing demand forecasts, and leveraging technology, purchasing departments can optimize inventory levels and enhance operational efficiency.
Continuously improving partnerships with suppliers will lead to better resource utilization, cost savings, and a competitive advantage in the market.
Reducing inventory risk through supplier collaboration not only improves the bottom line but also contributes to long-term business success.
資料ダウンロード
QCD調達購買管理クラウド「newji」は、調達購買部門で必要なQCD管理全てを備えた、現場特化型兼クラウド型の今世紀最高の購買管理システムとなります。
ユーザー登録
調達購買業務の効率化だけでなく、システムを導入することで、コスト削減や製品・資材のステータス可視化のほか、属人化していた購買情報の共有化による内部不正防止や統制にも役立ちます。
NEWJI DX
製造業に特化したデジタルトランスフォーメーション(DX)の実現を目指す請負開発型のコンサルティングサービスです。AI、iPaaS、および先端の技術を駆使して、製造プロセスの効率化、業務効率化、チームワーク強化、コスト削減、品質向上を実現します。このサービスは、製造業の課題を深く理解し、それに対する最適なデジタルソリューションを提供することで、企業が持続的な成長とイノベーションを達成できるようサポートします。
オンライン講座
製造業、主に購買・調達部門にお勤めの方々に向けた情報を配信しております。
新任の方やベテランの方、管理職を対象とした幅広いコンテンツをご用意しております。
お問い合わせ
コストダウンが利益に直結する術だと理解していても、なかなか前に進めることができない状況。そんな時は、newjiのコストダウン自動化機能で大きく利益貢献しよう!
(Β版非公開)