- お役立ち記事
- Collaborative demand forecasting with suppliers using digital tools: collaborative planning and inventory optimization
Collaborative demand forecasting with suppliers using digital tools: collaborative planning and inventory optimization
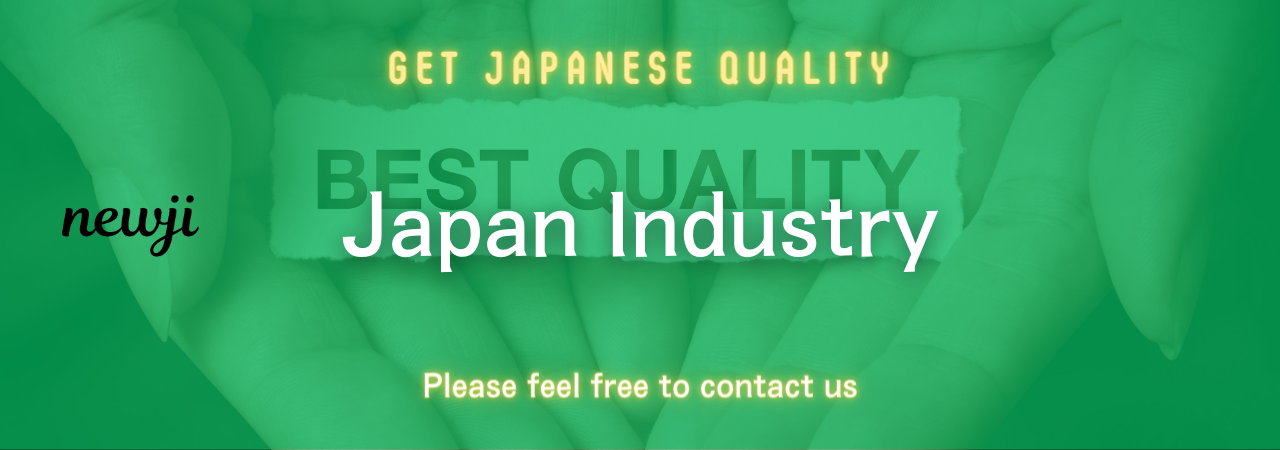
In today’s fast-paced business environment, staying competitive demands the effective management of inventory and supply chain processes. One essential strategy to achieve this is through collaborative demand forecasting with suppliers using digital tools. This approach, which encompasses collaborative planning and inventory optimization, aids companies in maintaining precision in inventory levels, improving supply chain efficiency, and ultimately enhancing customer satisfaction.
目次
The Importance of Demand Forecasting
Demand forecasting is the process of predicting future customer demand based on historical data, market trends, and various other factors. It allows businesses to make informed decisions regarding production, inventory management, and supply chain logistics. Accurate demand forecasting is crucial as it helps to balance supply with demand, minimizing the risks of overstocking or understocking.
Why Collaborate with Suppliers?
Collaboration with suppliers is a game-changer in demand forecasting. Suppliers play a crucial role in the supply chain, and their insights are invaluable. By working closely with suppliers, companies can share accurate demand forecasts, ensuring that suppliers can produce and deliver the right quantities of products on time. This collaborative approach leads to:
– Improved Accuracy:Collaboration reduces the uncertainties and variabilities in demand forecasting.
– Cost Efficiency:Optimized inventory levels reduce storage costs and minimize waste.
– Enhanced Relationships:Strong partnerships with suppliers foster better communication, trust, and reliability.
Leveraging Digital Tools for Collaborative Planning
Digital tools have revolutionized the way companies plan and manage their supply chain operations. Let’s delve into some of the essential digital tools that facilitate collaborative demand forecasting with suppliers.
1. Cloud-Based Platforms
Cloud-based platforms provide a centralized location for sharing information in real-time. These platforms enable companies and suppliers to access and update demand forecasts, inventory levels, and other critical data simultaneously. This transparency ensures that all parties are on the same page, reducing delays and enhancing overall efficiency.
2. Advanced Analytics and AI
Artificial Intelligence (AI) and advanced analytics play a significant role in demand forecasting. These technologies analyze vast amounts of data from various sources to identify patterns and trends. Machine learning algorithms can predict future demands with high accuracy, enabling companies to make proactive adjustments to their supply chain strategies.
3. ERP Systems
Enterprise Resource Planning (ERP) systems integrate various business processes, including inventory management, procurement, and sales. By consolidating data across departments, ERP systems provide a holistic view of the supply chain, aiding in better decision-making and more accurate demand forecasts.
4. Inventory Management Software
Inventory management software offers real-time visibility into stock levels and movements. With features like automated reordering and demand sensing, these tools help in maintaining optimal inventory levels, reducing the risk of stockouts or overstocks.
Collaborative Planning and Forecasting
Collaborative Planning, Forecasting, and Replenishment (CPFR) is a strategy where companies and their suppliers work together to fulfill customer demand. The process involves several steps:
1. Strategy and Planning:Both parties define the scope of collaboration, agree on key performance indicators (KPIs), and establish communication protocols.
2.Demand and Supply Management:Companies share their internal sales forecasts with suppliers. Suppliers, in turn, provide input based on their production capacities and lead times.
3.Execution: Orders are placed and fulfilled based on the collaboratively developed forecasts.
4.Analysis: Both parties review performance metrics and adjust strategies as needed.
Benefits of Collaborative Planning and Inventory Optimization
1. Increased Forecast Accuracy
When companies collaborate with their suppliers, they gain access to a broader dataset that enhances forecast accuracy. Suppliers’ insights regarding production constraints, lead times, and potential disruptions can refine the demand forecasts, reducing errors and improving reliability.
2. Reduced Inventory Costs
Collaborative planning helps maintain an optimal inventory level. By aligning production with actual demand, companies avoid the costs associated with excess inventory, such as storage, obsolescence, and capital investment.
3. Enhanced Customer Satisfaction
Accurate demand forecasting ensures that products are available when customers need them. This reliability enhances customer satisfaction and loyalty, driving repeat business and positive word-of-mouth.
4. Better Resource Utilization
With accurate demand forecasts and optimized inventory levels, companies can allocate resources more efficiently. Manufacturing processes can be streamlined, reducing downtime and improving overall productivity.
5. Risk Mitigation
Collaborative forecasting and planning help to identify potential risks early. Companies and suppliers can develop contingency plans to handle unforeseen disruptions, ensuring smoother operations even in challenging situations.
Implementing Collaborative Demand Forecasting: Best Practices
1. Foster Open Communication
Establishing a culture of open communication is essential for successful collaboration. Frequent and transparent communication ensures that all parties are aware of any changes or issues that may arise.
2. Invest in Technology
Utilizing the right digital tools is crucial. Invest in technology that supports real-time data sharing and analytics. Ensure that both your company and your suppliers are equipped with compatible systems to facilitate seamless collaboration.
3. Establish Clear KPIs
Define clear and measurable KPIs to track the success of collaborative demand forecasting efforts. Regularly review these metrics to identify areas for improvement.
4. Build Strong Relationships
Strong, trust-based relationships with suppliers are the foundation of effective collaboration. Engage in regular meetings, share relevant information, and work towards mutual goals.
5. Continuous Improvement
Collaboration is an ongoing process. Continuously seek feedback and look for ways to improve. Stay updated with the latest advancements in technology and best practices in supply chain management.
Collaborative demand forecasting with suppliers using digital tools is crucial for modern businesses striving to optimize their supply chain operations. By leveraging cloud-based platforms, advanced analytics, ERP systems, and inventory management software, companies can enhance forecast accuracy, reduce costs, and improve customer satisfaction. Implementing best practices in collaborative planning ensures sustained success and stronger relationships with suppliers. Embrace these strategies to navigate the complexities of the supply chain and stay ahead in the competitive market landscape.
資料ダウンロード
QCD調達購買管理クラウド「newji」は、調達購買部門で必要なQCD管理全てを備えた、現場特化型兼クラウド型の今世紀最高の購買管理システムとなります。
ユーザー登録
調達購買業務の効率化だけでなく、システムを導入することで、コスト削減や製品・資材のステータス可視化のほか、属人化していた購買情報の共有化による内部不正防止や統制にも役立ちます。
NEWJI DX
製造業に特化したデジタルトランスフォーメーション(DX)の実現を目指す請負開発型のコンサルティングサービスです。AI、iPaaS、および先端の技術を駆使して、製造プロセスの効率化、業務効率化、チームワーク強化、コスト削減、品質向上を実現します。このサービスは、製造業の課題を深く理解し、それに対する最適なデジタルソリューションを提供することで、企業が持続的な成長とイノベーションを達成できるようサポートします。
オンライン講座
製造業、主に購買・調達部門にお勤めの方々に向けた情報を配信しております。
新任の方やベテランの方、管理職を対象とした幅広いコンテンツをご用意しております。
お問い合わせ
コストダウンが利益に直結する術だと理解していても、なかなか前に進めることができない状況。そんな時は、newjiのコストダウン自動化機能で大きく利益貢献しよう!
(Β版非公開)