- お役立ち記事
- Collaborative Demand Forecasting with Suppliers Using Digital Tools: Joint Planning and Inventory Optimization
Collaborative Demand Forecasting with Suppliers Using Digital Tools: Joint Planning and Inventory Optimization
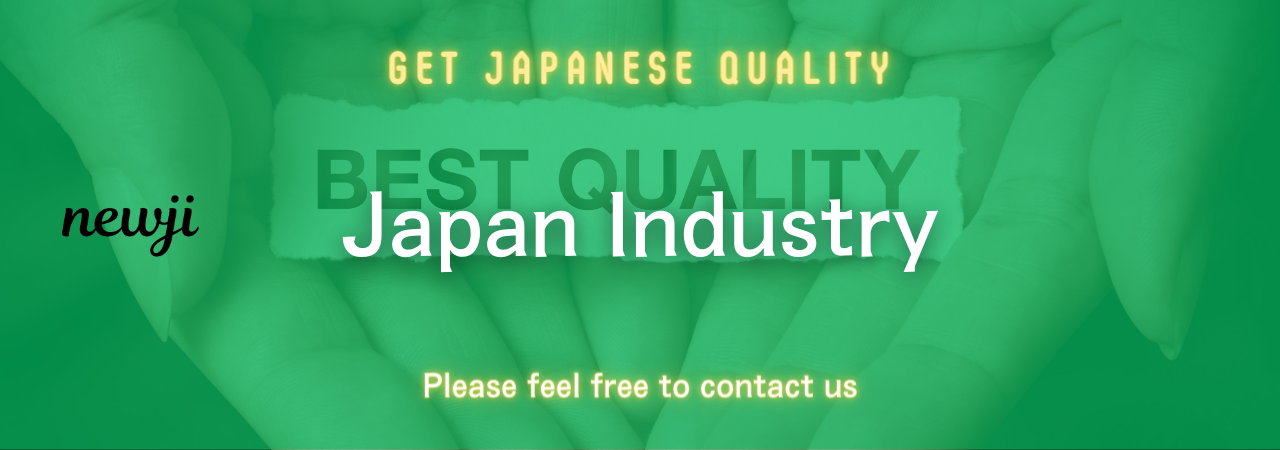
目次
Understanding Collaborative Demand Forecasting
Collaborative demand forecasting is a method where businesses and their suppliers work together to predict future customer demand.
By sharing information and using digital tools, both parties can create more accurate forecasts.
This leads to better planning and inventory management.
Benefits of Collaborative Demand Forecasting
When companies and suppliers collaborate on demand forecasting, both can enjoy several benefits.
Firstly, it improves the accuracy of demand predictions.
Better forecasts mean fewer stockouts and overstock situations.
Secondly, collaboration can lead to cost savings.
When supply chain partners work together, they can optimize inventory levels and reduce excess stock.
This helps free up capital and improves cash flow.
Better Planning and Coordination
Collaborative demand forecasting helps businesses and suppliers align their planning efforts.
When both parties have access to the same information, they can synchronize their production and delivery schedules.
This reduces the risk of delays and ensures that products are available when customers need them.
Good coordination also minimizes waste, as companies can better match supply with demand.
Enhanced Supplier Relationships
Working closely with suppliers to forecast demand can strengthen the relationship between both parties.
Collaboration fosters trust and opens up new opportunities for strategic partnerships.
Strong supplier relationships can lead to better negotiating terms, improved quality, and faster response times.
The Role of Digital Tools in Joint Planning
Digital tools are essential for effective collaborative demand forecasting.
These tools enable real-time data sharing, analysis, and communication between businesses and their suppliers.
Here are some key digital tools that can support joint planning:
Cloud-Based Platforms
Cloud-based platforms allow businesses and suppliers to share data and access forecasting tools from anywhere.
These platforms provide a centralized location for all relevant information, making it easy for both parties to collaborate.
Data Analytics Software
Data analytics software can analyze vast amounts of data to identify trends and patterns.
This helps businesses and suppliers create more accurate demand forecasts.
Advanced analytics can also provide valuable insights into customer behavior and market trends.
Supply Chain Management Systems
Supply chain management systems integrate various supply chain processes, such as procurement, production, and logistics.
These systems help businesses and suppliers coordinate their activities and ensure smooth operations.
By using supply chain management systems, both parties can optimize their inventories and reduce lead times.
Inventory Optimization through Joint Planning
Inventory optimization is a crucial aspect of collaborative demand forecasting.
When businesses and suppliers work together to forecast demand, they can better manage their inventories.
Here are some strategies for inventory optimization through joint planning:
Safety Stock Calculation
Safety stock is the extra inventory kept on hand to prevent stockouts.
By collaborating on demand forecasts, businesses and suppliers can calculate the optimal level of safety stock needed.
This ensures that there is always enough inventory to meet unexpected demand without overstocking.
Reorder Point Determination
The reorder point is the inventory level at which a new order should be placed.
Joint planning allows businesses and suppliers to determine the ideal reorder points based on accurate demand forecasts.
This helps prevent stockouts and ensures a steady supply of products.
Just-In-Time (JIT) Inventory
Just-In-Time (JIT) inventory is a strategy where products are produced and delivered just in time to meet customer demand.
Collaborative demand forecasting enables businesses and suppliers to implement JIT inventory effectively.
This reduces the need for large inventory holdings and minimizes storage costs.
Challenges and Solutions
While collaborative demand forecasting offers many benefits, it also comes with challenges.
Here are some common challenges and solutions to overcome them:
Data Sharing and Integration
One of the biggest challenges of collaborative demand forecasting is data sharing.
Businesses and suppliers need to share sensitive information, which can be difficult due to privacy concerns and data compatibility issues.
To overcome this, both parties should establish clear data-sharing protocols and use compatible digital tools.
Communication and Trust
Effective communication and trust are essential for successful collaboration.
Without these, misunderstandings and conflicts can arise.
Businesses and suppliers should invest in building strong relationships and ensure open and transparent communication.
Change Management
Implementing collaborative demand forecasting requires changes in processes and systems.
Employees may resist these changes due to unfamiliarity or fear of the unknown.
To address this, companies should provide adequate training and support to help employees adapt to new ways of working.
Conclusion
Collaborative demand forecasting with suppliers using digital tools is a powerful strategy for joint planning and inventory optimization.
By working together, businesses and suppliers can create more accurate demand forecasts, improve planning, and enhance inventory management.
Though challenges exist, they can be overcome with clear communication, trust, and the right digital tools.
Embracing collaborative demand forecasting can lead to a more efficient and responsive supply chain, benefiting both businesses and their customers.
資料ダウンロード
QCD調達購買管理クラウド「newji」は、調達購買部門で必要なQCD管理全てを備えた、現場特化型兼クラウド型の今世紀最高の購買管理システムとなります。
ユーザー登録
調達購買業務の効率化だけでなく、システムを導入することで、コスト削減や製品・資材のステータス可視化のほか、属人化していた購買情報の共有化による内部不正防止や統制にも役立ちます。
NEWJI DX
製造業に特化したデジタルトランスフォーメーション(DX)の実現を目指す請負開発型のコンサルティングサービスです。AI、iPaaS、および先端の技術を駆使して、製造プロセスの効率化、業務効率化、チームワーク強化、コスト削減、品質向上を実現します。このサービスは、製造業の課題を深く理解し、それに対する最適なデジタルソリューションを提供することで、企業が持続的な成長とイノベーションを達成できるようサポートします。
オンライン講座
製造業、主に購買・調達部門にお勤めの方々に向けた情報を配信しております。
新任の方やベテランの方、管理職を対象とした幅広いコンテンツをご用意しております。
お問い合わせ
コストダウンが利益に直結する術だと理解していても、なかなか前に進めることができない状況。そんな時は、newjiのコストダウン自動化機能で大きく利益貢献しよう!
(Β版非公開)