- お役立ち記事
- Collaborative Production Systems with Robots and Humans Utilizing Mechatronics Technology
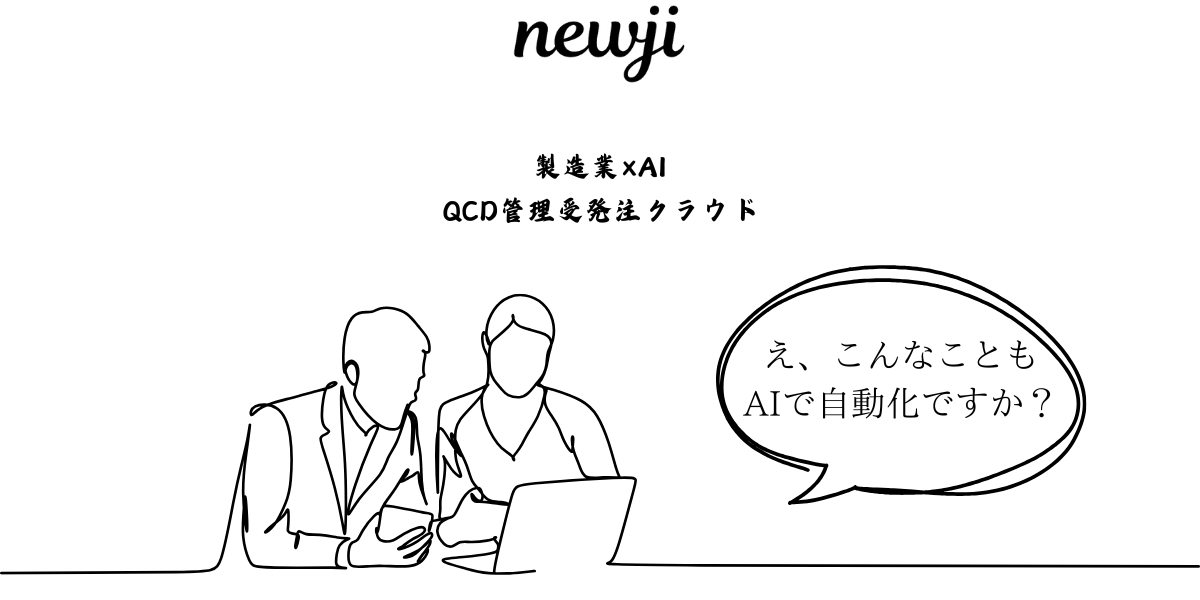
Collaborative Production Systems with Robots and Humans Utilizing Mechatronics Technology
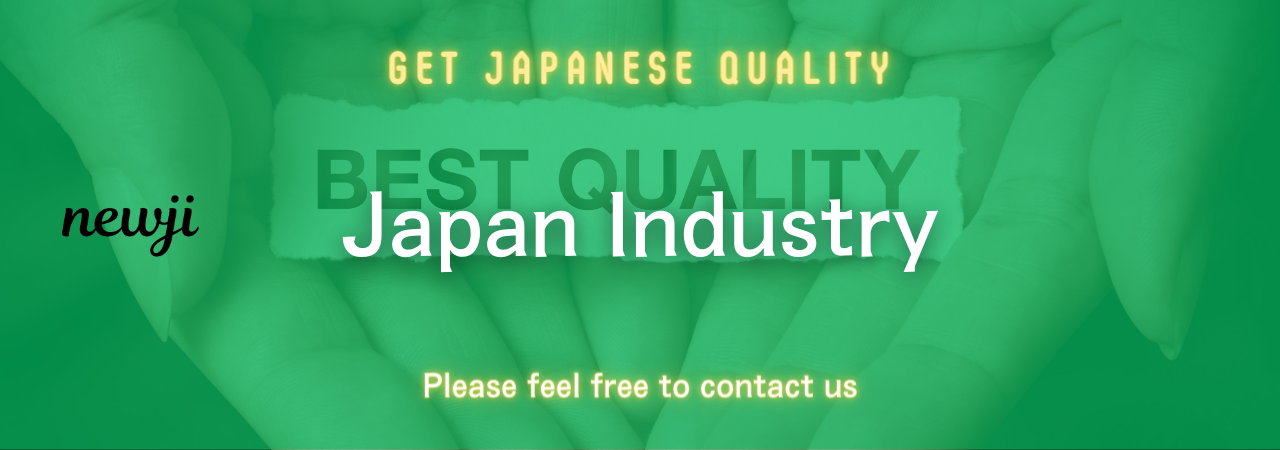
Understanding Collaborative Production Systems
Collaborative production systems are an innovative approach where robots and humans work together to optimize efficiency in various production environments.
This synergy of human intelligence and robotic precision is becoming increasingly popular across industries.
By utilizing mechatronics technology, these systems are designed to leverage the strengths of both human and machines, creating a harmonious work environment.
Mechatronics is an interdisciplinary field, blending mechanical engineering, electronics, computer science, and control engineering.
With advancements in this technology, production processes have seen significant improvements in terms of speed, accuracy, and flexibility.
The Rise of Mechatronics in Robotics
The integration of mechatronics in robotics has paved the way for more sophisticated and capable robots.
These robots are equipped with advanced sensors and control systems, enabling them to perform complex tasks with precision.
Artificial intelligence and machine learning algorithms also play a crucial role in enhancing the capabilities of these robots.
They can learn from human workers, adapt to changes, and make decisions on the fly, ensuring seamless collaboration with their human counterparts.
This fusion of technologies elevates the efficiency of production systems beyond traditional methods.
Benefits of Collaborative Production Systems
There are numerous advantages to utilizing collaborative production systems in manufacturing and other industries.
First, these systems can significantly enhance productivity.
Robots can handle repetitive and mundane tasks, freeing up human workers to focus on more creative and strategic roles.
This leads to a more balanced workload and allows companies to maximize the potential of their workforce.
Furthermore, the precision of robots reduces errors, improving the overall quality of products.
Another benefit is the flexibility that these systems offer.
Collaborative robots, or cobots, can be easily reprogrammed and reconfigured to adapt to different tasks and production lines.
This adaptability is crucial in today’s rapidly changing market, where companies must swiftly respond to new demands and consumer preferences.
Ensuring Safety in Human-Robot Collaboration
Safety is a paramount concern in environments where robots and humans work side by side.
Modern collaborative robots are engineered with safety features to protect human workers from harm.
These include sensors that detect human presence, allowing robots to halt operations or slow down if a person is nearby.
There are also special safety protocols and standards established to guide the operation of collaborative production systems.
Training employees to work effectively and safely with robots is essential.
When workers understand how to interact with these machines, it minimizes risks and optimizes cooperation.
Challenges and Considerations
Despite the many advantages, there are challenges to implementing collaborative production systems.
One concern is the initial cost involved in acquiring and setting up sophisticated robotic systems.
Although they provide long-term gains, the upfront investment can be significant.
Another consideration is the need for ongoing maintenance and updates to keep the technology functioning correctly.
As robots become more integrated into the workforce, companies must also address how this impact will affect employment.
Reskilling and retraining workers is an essential step in ensuring that they remain relevant in a tech-driven job market.
Companies should focus on integrating human skills with robotic capabilities, creating a team-oriented culture that values both contributions.
Future Prospects of Collaborative Production Systems
The future of collaborative production systems holds tremendous potential.
As technology continues to advance, these systems will become even more intelligent and agile, capable of handling a wider range of tasks.
Incorporating real-time data analytics, the Internet of Things (IoT), and cloud computing will enable even more sophisticated and interconnected production environments.
Industries such as healthcare, agriculture, and logistics will continue to benefit from these advancements.
In healthcare, for example, robots can assist with surgeries or care for patients alongside medical professionals.
In agriculture, they can automate harvesting and planting processes, improving efficiency and sustainability.
Conclusion
Collaborative production systems that utilize mechatronics technology represent a significant shift in how industries approach production challenges.
By harnessing the strengths of both humans and robots, these systems enhance productivity, precision, and flexibility.
While there are challenges to address, the ongoing development and implementation of these systems promise a more efficient and dynamic industrial landscape.
As we embrace this future, the collaboration between humans and machines will become an integral part of our working lives, transforming industries and driving innovation forward.
資料ダウンロード
QCD調達購買管理クラウド「newji」は、調達購買部門で必要なQCD管理全てを備えた、現場特化型兼クラウド型の今世紀最高の購買管理システムとなります。
ユーザー登録
調達購買業務の効率化だけでなく、システムを導入することで、コスト削減や製品・資材のステータス可視化のほか、属人化していた購買情報の共有化による内部不正防止や統制にも役立ちます。
NEWJI DX
製造業に特化したデジタルトランスフォーメーション(DX)の実現を目指す請負開発型のコンサルティングサービスです。AI、iPaaS、および先端の技術を駆使して、製造プロセスの効率化、業務効率化、チームワーク強化、コスト削減、品質向上を実現します。このサービスは、製造業の課題を深く理解し、それに対する最適なデジタルソリューションを提供することで、企業が持続的な成長とイノベーションを達成できるようサポートします。
オンライン講座
製造業、主に購買・調達部門にお勤めの方々に向けた情報を配信しております。
新任の方やベテランの方、管理職を対象とした幅広いコンテンツをご用意しております。
お問い合わせ
コストダウンが利益に直結する術だと理解していても、なかなか前に進めることができない状況。そんな時は、newjiのコストダウン自動化機能で大きく利益貢献しよう!
(Β版非公開)