- お役立ち記事
- Collaborative robot safety improvement technology and usage examples at manufacturing sites
月間77,185名の
製造業ご担当者様が閲覧しています*
*2025年2月28日現在のGoogle Analyticsのデータより
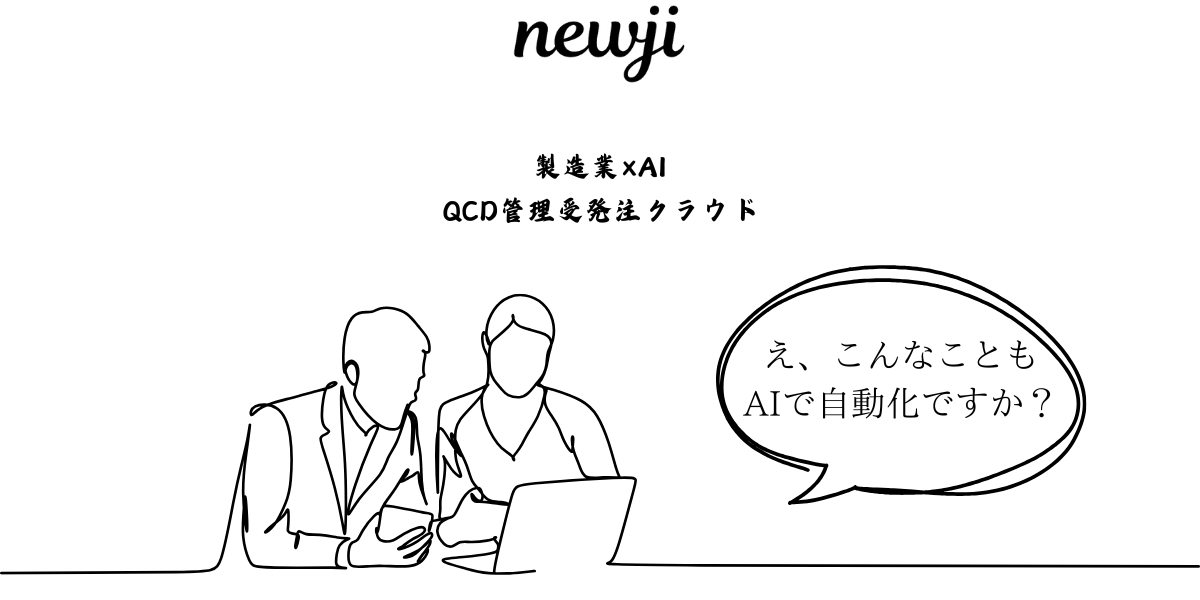
Collaborative robot safety improvement technology and usage examples at manufacturing sites
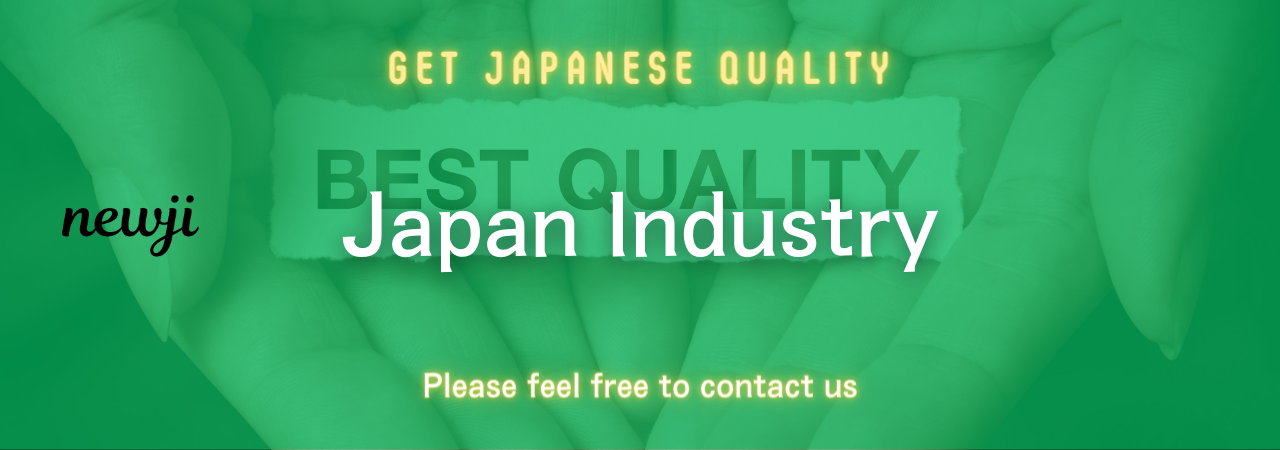
Collaborative robots, often referred to as cobots, are transforming the landscape of manufacturing by working alongside humans to streamline processes and increase productivity.
The significance of cobots is growing as they offer flexible automation solutions while maintaining safety standards.
In this article, we will explore the technology used to enhance the safety of collaborative robots and provide examples of their application in manufacturing settings.
目次
Understanding Collaborative Robots
Collaborative robots are designed to operate in conjunction with human workers.
Unlike traditional industrial robots, which are often enclosed in cages to separate them from human interaction, cobots are equipped with advanced sensors and safety features that allow them to work side by side with people.
These robots are built to be both small and flexible, allowing easy integration with existing workflows and environments.
The Importance of Safety in Cobots
Safety is paramount when integrating robots and humans in the workplace.
As cobots are designed to work closely with humans, ensuring that they operate safely and do not pose a risk to human workers is a primary concern.
The safety of cobots is driven by international standards such as ISO 10218 and ISO/TS 15066, which specifically outline requirements for robotic safety and collaborative operation.
Technology Used to Improve Cobot Safety
Several technological advancements contribute to the safety of collaborative robots.
These advancements ensure that cobots operate without endangering workers while still performing efficiently.
Advanced Sensors and Machine Vision
Cobots use an array of sensors, including proximity sensors, force sensors, and machine vision, to detect the presence of humans and other objects in their environment.
These sensors help the robot understand its surroundings and adjust its movements accordingly to avoid collisions.
Machine vision systems further enhance this capability by providing cobots with the ability to “see” and identify objects, allowing them to interact more safely and efficiently.
Force and Torque Limiting
One of the key safety features of cobots is the ability to limit the force and torque they apply.
In the event of a collision, the cobot is designed to reduce its force to prevent injury.
Force and torque sensors embedded in the robot’s joints allow it to respond dynamically to forces it encounters, ensuring that it stops or moves away when unexpected resistance is detected.
Speed and Separation Monitoring
Speed and separation monitoring is a strategy that allows cobots to adjust their speed based on their distance from human workers.
When a worker approaches, the cobot can slow down or stop, reducing the risk of injury.
This dynamic adjustment creates a safe work environment while maintaining operational efficiency.
End-Effectors with Safety Features
The end-effectors, or hands, of cobots are also designed with safety in mind.
Soft robotics, cushioned materials, and safety mechanisms help prevent pinching or bruising in the event of accidental contact with humans.
These features enable cobots to handle delicate tasks that require a gentle touch while ensuring worker safety.
Usage Examples of Collaborative Robots in Manufacturing
Collaborative robots are utilized in a variety of ways within manufacturing environments.
Their versatility and safety features make them ideal for numerous applications.
Material Handling and Packaging
Cobots are frequently used in material handling and packaging tasks.
They can efficiently lift and place products, load and unload pallets, and assist with packing products into boxes.
The precision and reliability of cobots make them perfect for repetitive material handling tasks, reducing physical strain on human workers.
Assembly and Quality Control
In assembly lines, cobots assist with assembling small parts and conducting quality control checks.
Their accuracy ensures that even the smallest components are assembled correctly, improving product quality.
Additionally, cobots equipped with sensors can inspect products for defects, identifying issues before they reach consumers.
Welding and Painting
In industries where welding and painting are required, cobots are increasingly preferred for their consistent performance.
Their ability to maintain uniform application, whether it be paint or weld beads, ensures high-quality results.
Furthermore, using cobots for these tasks protects human workers from hazardous fumes and extreme temperatures.
Machining and CNC Operations
Cobots also play a significant role in machining and CNC operations.
They can load raw materials, manage tools, and monitor equipment, enhancing productivity and precision.
Their capacity to work for extended periods without fatigue makes them a valuable asset in machining applications.
Benefits of Using Collaborative Robots
The integration of collaborative robots into manufacturing processes provides numerous benefits beyond just enhanced safety.
Increased Efficiency and Productivity
Cobots can work continuously without breaks, providing a constant level of productivity.
Their precision and reliability reduce errors and waste, contributing to higher efficiency.
Improved Worker Satisfaction
By taking over repetitive and physically demanding tasks, cobots allow human workers to focus on more complex and creative responsibilities.
This shift can lead to improved job satisfaction and reduce the likelihood of injuries associated with manual labor.
Easy Integration and Scalability
Collaborative robots are designed to be easily integrated into existing workflows.
Their flexibility allows them to be scaled up or down based on production demand, making them a cost-effective investment for manufacturers.
In conclusion, collaborative robots are revolutionizing the manufacturing industry by enhancing productivity while maintaining safety.
With advanced technologies to ensure their safe operation and numerous practical applications, cobots represent a sustainable solution for the future of manufacturing.
As technology continues to evolve, the role of cobots in collaborative environments is expected to expand, offering even more opportunities for innovation and efficiency in manufacturing.
資料ダウンロード
QCD管理受発注クラウド「newji」は、受発注部門で必要なQCD管理全てを備えた、現場特化型兼クラウド型の今世紀最高の受発注管理システムとなります。
ユーザー登録
受発注業務の効率化だけでなく、システムを導入することで、コスト削減や製品・資材のステータス可視化のほか、属人化していた受発注情報の共有化による内部不正防止や統制にも役立ちます。
NEWJI DX
製造業に特化したデジタルトランスフォーメーション(DX)の実現を目指す請負開発型のコンサルティングサービスです。AI、iPaaS、および先端の技術を駆使して、製造プロセスの効率化、業務効率化、チームワーク強化、コスト削減、品質向上を実現します。このサービスは、製造業の課題を深く理解し、それに対する最適なデジタルソリューションを提供することで、企業が持続的な成長とイノベーションを達成できるようサポートします。
製造業ニュース解説
製造業、主に購買・調達部門にお勤めの方々に向けた情報を配信しております。
新任の方やベテランの方、管理職を対象とした幅広いコンテンツをご用意しております。
お問い合わせ
コストダウンが利益に直結する術だと理解していても、なかなか前に進めることができない状況。そんな時は、newjiのコストダウン自動化機能で大きく利益貢献しよう!
(β版非公開)