- お役立ち記事
- Collaborative Robotics for Ensuring Worker Safety on Production Lines
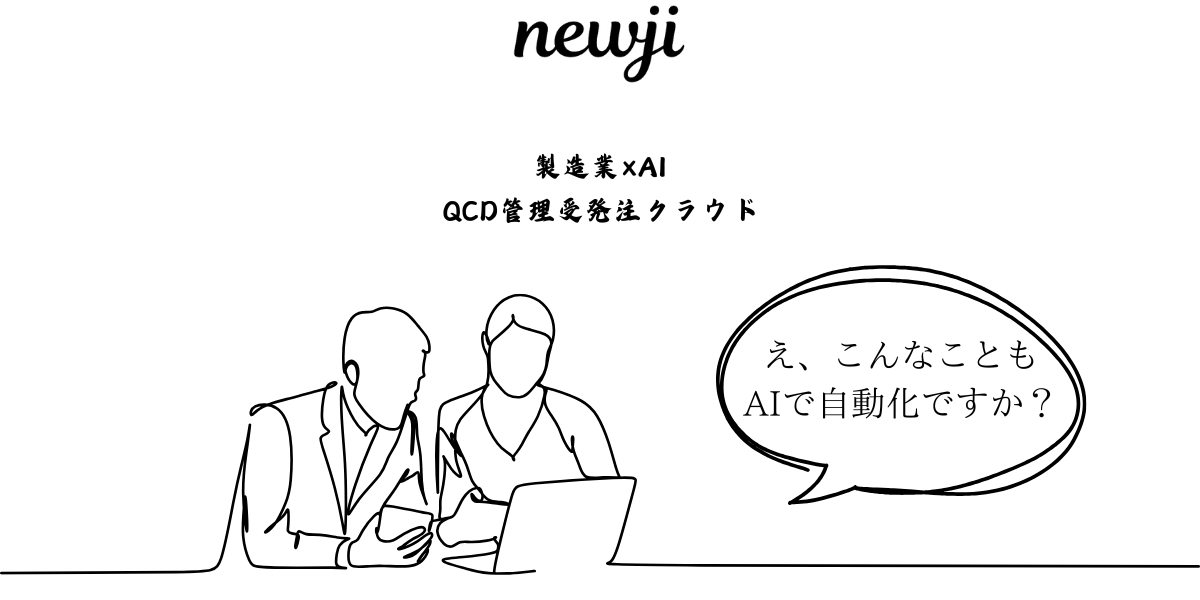
Collaborative Robotics for Ensuring Worker Safety on Production Lines
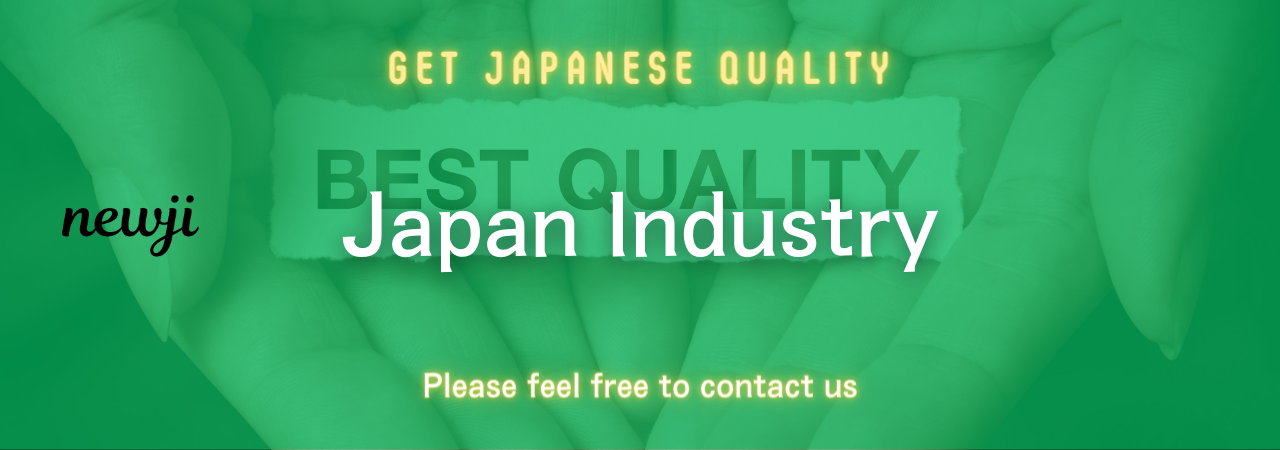
目次
Introduction to Collaborative Robotics
In today’s rapidly evolving industrial landscape, the integration of advanced technologies is essential for maintaining efficiency and safety on production lines.
One such technology that is revolutionizing the manufacturing sector is collaborative robotics or “cobots.”
These robots are designed to work alongside humans, enhancing productivity and ensuring greater safety in the workplace.
This article will explore how collaborative robotics contributes to worker safety on production lines, the technology behind cobots, and how companies can effectively implement these systems.
Understanding Collaborative Robotics
Collaborative robots are a class of robots specifically designed to assist human workers in manufacturing environments.
Unlike traditional industrial robots, which are often isolated from humans due to safety concerns, cobots are engineered to operate in close proximity to people.
They are equipped with sensors, cameras, and advanced software that allow them to perceive and respond to their surroundings.
This technology ensures that cobots can safely interact with human co-workers.
The Role of Cobots in Enhancing Worker Safety
One of the primary benefits of collaborative robotics is their ability to enhance worker safety on production lines.
Let’s delve into some ways cobots achieve this:
1. **Reduction of Workplace Injuries**: Cobots are designed to perform repetitive, hazardous, or physically demanding tasks, which reduces the risk of workplace injuries for human workers.
By taking on tasks such as heavy lifting, precise assembly, or operating in extreme environments, cobots allow humans to focus on more complex and less physically taxing duties.
2. **Safety Features**: Collaborative robots come equipped with numerous safety features such as force limitations, emergency stop functions, and advanced sensors that detect human presence.
These features enable cobots to immediately halt operations if they come too close to a human, preventing potential accidents.
3. **Improved Ergonomics**: By assuming tasks that require uncomfortable or strenuous postures, cobots help in improving workplace ergonomics.
This results in reduced musculoskeletal strain for human workers, leading to fewer injuries related to poor ergonomics.
Technological Advances in Collaborative Robotics
The success and safety of cobots on production lines largely depend on their underlying technologies.
Here are some advancements that have propelled collaborative robotics forward:
1. **Machine Learning and AI**: Integration of machine learning and artificial intelligence allows cobots to learn from human interactions and improve efficiency over time.
This adaptability is crucial in dynamic manufacturing environments, where cobots can adjust to new tasks or changes in production needs.
2. **Advanced Sensors**: Modern cobots are equipped with sophisticated sensors that enhance their ability to perceive and interact with their surroundings.
These sensors range from proximity sensors that detect human presence to force sensors that help cobots apply the right amount of pressure during tasks.
3. **Seamless Human-Robot Interaction**: The development of intuitive programming interfaces has made it easier for workers to interact with and program cobots without requiring extensive technical knowledge.
This has facilitated smoother integration of cobots into the workforce.
Implementing Collaborative Robotics on Production Lines
The introduction of cobots into an industrial setting requires careful planning and execution.
Here are steps to ensure a successful integration:
1. **Assessment of Tasks**: Identify which tasks are most suitable for cobots.
These typically include repetitive, hazardous, or precision-requiring tasks that can be automated without compromising quality or safety.
2. **Employee Training**: Proper training is crucial for employees to become familiar with cobot operation and programming.
Workers should understand the safety features and learn how to collaborate effectively with cobots.
3. **Infrastructure Adjustments**: Depending on the size and capabilities of the cobots, companies might need to adjust their existing infrastructure or facilities to accommodate these robots.
This includes ensuring enough space for safe human-robot interaction.
4. **Continuous Monitoring and Feedback**: Once deployed, continuous monitoring and regular feedback are essential to evaluate the performance of cobots.
This helps in identifying areas for improvement and adapting to any unforeseen challenges.
Case Studies and Success Stories
There are numerous examples of companies successfully integrating collaborative robotics into their production processes.
A notable case is of a large automotive manufacturer that implemented cobots to assist with assembling intricate engine components.
The cobots were able to perform tasks with greater precision and efficiency, leading to a reduction in assembly errors and improved employee safety.
Similarly, a food processing plant utilized cobots to perform repetitive packing and sorting tasks.
The deployment resulted in increased production speed and allowed human workers to focus on quality control and supervision, jobs that enhance job satisfaction and safety.
Future Prospects of Collaborative Robotics
The future of collaborative robotics looks promising, with ongoing research and development aimed at further enhancing their capabilities.
As technology continues to advance, we can expect cobots to become more intelligent, versatile, and seamless in their interaction with human workers.
In conclusion, collaborative robotics stands as a transformative force in ensuring worker safety and efficiency on production lines.
By intelligently integrating cobots into manufacturing processes, companies can create safer and more productive work environments while staying competitive in the ever-evolving industrial landscape.
資料ダウンロード
QCD調達購買管理クラウド「newji」は、調達購買部門で必要なQCD管理全てを備えた、現場特化型兼クラウド型の今世紀最高の購買管理システムとなります。
ユーザー登録
調達購買業務の効率化だけでなく、システムを導入することで、コスト削減や製品・資材のステータス可視化のほか、属人化していた購買情報の共有化による内部不正防止や統制にも役立ちます。
NEWJI DX
製造業に特化したデジタルトランスフォーメーション(DX)の実現を目指す請負開発型のコンサルティングサービスです。AI、iPaaS、および先端の技術を駆使して、製造プロセスの効率化、業務効率化、チームワーク強化、コスト削減、品質向上を実現します。このサービスは、製造業の課題を深く理解し、それに対する最適なデジタルソリューションを提供することで、企業が持続的な成長とイノベーションを達成できるようサポートします。
オンライン講座
製造業、主に購買・調達部門にお勤めの方々に向けた情報を配信しております。
新任の方やベテランの方、管理職を対象とした幅広いコンテンツをご用意しております。
お問い合わせ
コストダウンが利益に直結する術だと理解していても、なかなか前に進めることができない状況。そんな時は、newjiのコストダウン自動化機能で大きく利益貢献しよう!
(Β版非公開)